The LED revolution is on! LED technology, now over 50 years in the making, enables the “Digitization of Light”. This “Analog-to-Digital Transformation” of light sources, from traditional light sources such as incandescent, fluorescent and HID, to LED, enables a whole new range of applications and markets, from Displays, to Automotive and General Lighting, and emerging markets such as Indoor Vertical Farming and Horticulture, IOT and Visible Light Communications. Our ability to rapidly engineer applications-specific new product designs, coupled with appropriate LED light sources and driver and control electronics, is resulting in rapid adoption of this platform.
The LED General Lighting segment, in particular, is growing at the fastest rate, with unit volumes of LED retrofit lamps, luminaires and tubes forecast to grow by 50% in 2016, over 2015. This is driven by rapid technological advances, simultaneous cost reductions and scale of manufacturing in LED package technologies as well as systems integration technologies. The key issues that need to be addressed by the LED lighting supply chain include:
- Efficiency, Brightness and Light Quality Improvement (Lumens per Watt)
- Higher efficiency of electrical power to light and lumen output per package reduces energy consumption.
- High heat dissipation
- Good light extraction and directionality
- Reliability and Lifetime Improvement(Lumen Maintenance over Life)
- Reliability of the package and the system determines lifetime of the package and system, and lowers maintenance costs.
- Vibration and high temperature thermal cycling performance
- Cost/Lumen Over the Lifetime($/Lumen and Lumens/$)
- Increased efficiency and brightness, and increased reliability and lifetime reduce the cost per lumen over life.
- New Form Factors
- Greater Integration and Design Freedom
- Greater Integration and Design Freedom
Role of Interconnects in LED Lighting and Where High Reliability Interconnects Fit
One important class of applications in the General Lighting segment is high power outdoor lighting such as street lighting. Customers such as municipalities and building owners expect very high reliability of such LED based street lights, since major value propositions include energy savings as well as lumen maintenance over a long lifetime. For such applications, a B50, L70 lifetime of 35,000 hours is needed. For these high reliability and lifetime requirements, it is critical to have excellent assembly interconnect reliability (i.e. LED Package to Insulated Metal Substrate attach).
The role of interconnects in LED assembly is fundamentally to:
- Convey power and information efficiently and reliably over the rated life.
- Get the heat out faster and reliably over the rated life.
- Enable more light output, consistently, for longer time for the same package and system footprint.
New super-high and ultra-high power LED package designs provide high lumen density that can enable significant system cost reductions through fewer LEDs, smaller PCBs, and smallerheat sink size requirements. This, however, puts significant performance demands on the interconnects (solder joints in particular), due to the nature of the materials stack in the assembly, and the high operating temperature inherent in such systems.
In the case of a super-high or ultra-high power LED assembly on aluminum MCPCB, the ΔCTE between the LED and the MCPCB is 18-20, which is quite high, as shown schematically in Figure 1. During thermal cycling experienced by the LED assembly in applications such as outdoor lighting or automotive, the high ΔCTE causes significant strain energy build-up in the solder joint between the LED submount and the MCPCB, during the thermal cycling experienced in use. This is shown schematically in Figure 2. This strain energy buildup causes micro-cracking, and eventually, failure of the joint.
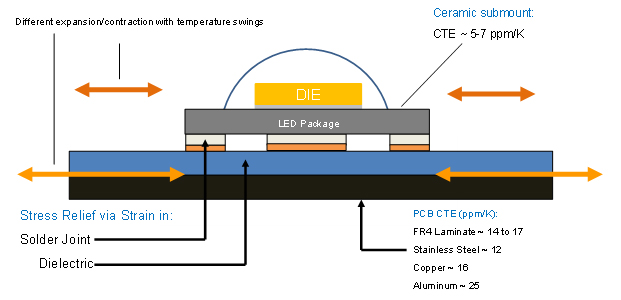
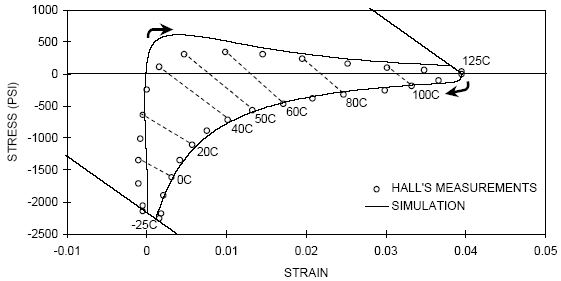
Thus, for a given LED package structure and board material used, it is beneficial to use solder joints with improved mechanical and thermal fatigue/creep and vibration resistance. A new class of creep-resistant and vibration resistant alloys has been developed, that can provide this capability, via a micro-structural control approach. These advanced alloys have been developed with special additives for improved thermal stability for high temperature operation and higher thermal fatigue and vibration resistance. These alloys have been commercially implemented for high power LED assembly.
Figure 3 shows and example of component shear data for a high power ceramic based LED assembled on a Metal Core PCB using such a creep resistant solder alloy-based solder (Maxrel™), compared with SAC305 and a low silver alloy (SACX0807), over 1000 thermal cycles from -40C to 125C. It is clear that the creep resistant alloy maintains excellent shear strength even after 1000 thermal cycles under high CTE mismatch conditions.
Such creep resistant alloys can provide significant benefits, in addition to maintaining solder joint integrity over a long time. In particular, improved creep resistance limits the amount of strain energy build-up in the solder joints, and can thus reduce the resistance increase and forward voltage increase that could result from such a strain energy build-up. This can provide a direct benefit to limit power draw to maintain current input to the LED, and maintain lumen output over a longer period of time. For LED circuits connected in series, this becomes an especially important feature.
Parting Thoughts
LEDs are enabling the “Digitization of Light” and therefore, an “Analog-to-Digital Transformation” in any application that uses light. Our ability to engineer the light wavelength spectrum, gives us unprecedented control over light generation and allows us to tailor the light being produced, to the specific application at hand. Our ability to rapidly engineer applications-specific new product designs, coupled with appropriate LED light sources and driver and control electronics, is resulting in rapid adoption of this platform. This adoption is only accelerating, due to dramatic performance improvements, coupled with economies of scale and systems cost declines. This combination of capabilities and favorable economics is enabling a whole new range of applications and markets, including obvious markets such as Displays, Automotive and General Lighting, and emerging markets such as Indoor Vertical Farming, IOT and Visible Light Communications.
In the General Lighting space in particular, which is the biggest emerging space using LEDs, significant LED systems cost reductions are being enabled through the availability of super and ultra-high power LED packages, for applications such as street lighting. Implementation of such packages in reliable, long lifetime systems calls for higher reliability, high operating temperature capable interconnects. Creep resistance of the solder alloys used is a significant determinant of solder joint reliability in high CTE mismatch assembly stacks under thermal cycling conditions. Solder joints with improved mechanical and thermal fatigue/creep and vibration resistance and bond line uniformity, are possible by using micro-structural control approach. Such alloys are being deployed now in commercial use.