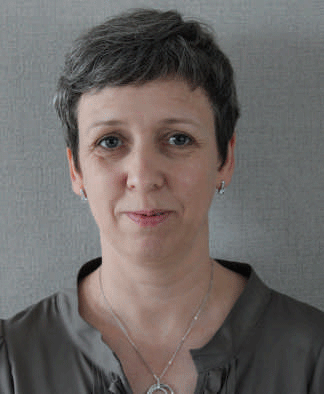
Interview with Hilde Goossens, Technical Service Engineer, Henkel Electronic Materials.
-
Please introduce Henkel product range in conformal coating products.
Henkel offers a range of conformal coating materials based on different chemistry platforms, including acrylics, urethanes, silicones and hybrid systems (urethane-acrylate). While many conformal coating products aresolvent-based, Henkel is always conscious of the environment and has moved toward more sustainable formulations which are solvent-free, low-VOC materials. The Loctite® portfolio of conformal coatings – including to solvent-free formulas – are also offered in fast-cure systems, enabling process efficiency and environmental friendliness.
-
What are the solutions offered by Henkel for Automotive applications
There are several products developed by Henkel that are well-suited for automotive applications, with material selection based on the end use and its environment – the car interior, under-the hood or exterior. For interior applications such as air bag sensors and car multimedia devices, where high temperature, harsh environment protection is not required, Loctite Stycast PC62 (acrylic) and Loctite Stycast PC18M (urethane) are frequently used. Technomelt® low pressure molding materials are also used successfully for in-cabin electronics that require environmental protection.
For under-the-hood applications such as engine management control boards, the most recommended productsare generally silicone-based conformal coating materials like Loctite Stycast 5293. This material has a temperature range of -40°C to 200°C, cures quickly with UV to allow fast handling of devices, and a moisture cure mechanism to ensure shadowed areas also cure completely. .When automotive electronics will be subjected to high temperatures; Henkel potting materials provide good protection against temperature extremes and exposure to automotive fluids.
-
In your views how important is conformal coating while talking about automotive applications
Reliability is a ‘must have’ for today’s electronic devices within automotive applications, as many electronic systems are critical to auto performance and safety. Examples include air bag sensors, tire pressure sensors, blind spot/lane change detection sensors, anti-lock braking systems, engine control units and driver assistance systems, among others. These electronics need to be protected from environmental influences andconformal coatings are one method of safeguarding electronics to ensure long term reliability.
-
What are the challenges of modern automotive systems can be met by conformal coating and how Henkel products are working in these fields.
The industry’s move to smaller components and finer-pitch devices dictates better insulation between components on the PCB. Because conformal coatings are applied in extremely thin layers, there is very low weight contribution to the device, yet the materials still deliver robust protection and insulation. If manufacturers don’t want to coat the entire assembly, conformal coating materials can be selectively applied to only the areas that require protection. In fact, Henkel has just developed a novel masking solution, using Technomelt® AS 8998 that further facilitates the process of selective conformal coating on highly miniaturized devices. Henkel’s advanced conformal coating materials protect PCBs from thermal shock, moisture, corrosive materials, and a variety of other adverse conditions to ensure long product lifecycles in harsh automotive electronics applications.
-
What are the key considerations while a selecting a coating material for given applications specifications.
The main requirement for selecting a conformal coating material is the required operating temperature, as this will decide the type of chemistry to be used. Only silicone-based systems can be used when operating temperatures will be above 140°C. If temperature resistance is less critical, the environmental exposure, application and processing requirements will determine if acrylics or urethanes can be used.