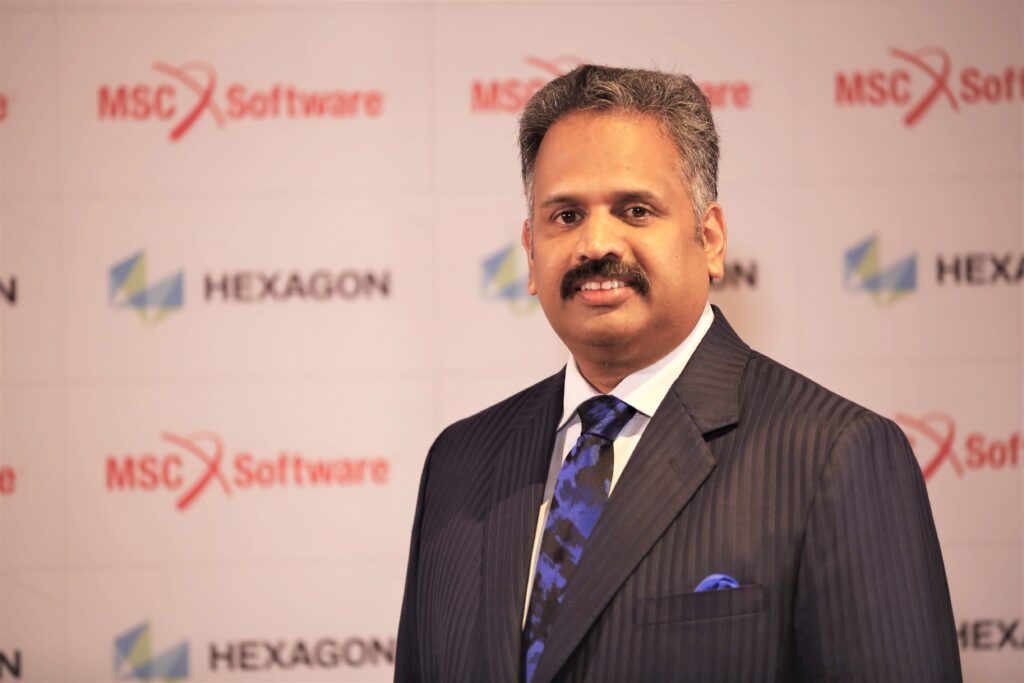
There is no denying that the future of manufacturing is in Industry 4.0 solutions and digitalisation of the shopfloor Hexagon is a global leader in sensor, software and autonomous solutions. Hexagon’s Manufacturing Intelligence division provides solutions that utilise data from design and engineering, production and metrology to make manufacturing smarter.
Mr. Sridhar Dharmarajan, EVP & MD, Hexagon & MSC Software spoke to Electronics Maker about manufacturing transformation and shares insights on smart manufacturing trends, automotive industry future and company’s intelligent solutions for the industry.
How is Hexagon leading digital transformation in manufacturing?
At Hexagon, we often say that data is in our DNA. Hexagon Manufacturing Intelligence division utilises data in all aspects ranging from design to engineering, production and metrology. We believe that data utilisation is the most innovative way to make manufacturing smarter and drive digital transformation in manufacturing. Hexagon strives to bring the most cutting-edge and high-quality technology solutions to the industry.
Hexagon’s Manufacturing Intelligence division form a digital matrix that creates solutions throughout the entire manufacturing process. This enables a conceptual, productive, and holistic view of the factory as a whole, enhancing quality assurance, productivity and lean processes with machine speed and confidence to achieve the desired outcome. The data allows the formation of interconnected links in the manufacturing ecosystem by capturing quality data for measurement, positioning and inspection.
Hence, data is the nodal point between the real and virtual worlds, transitioning real-world data into the digital domain. Our measurement-assisted production technology is best-in-class, and we continue to innovate towards more real-time feedback loop applications. This allows us to create a future where data is autonomously employed to drive sustainability and productivity.
Our software solutions, including simulation software, facilitate the exploration of prototypes without physical elements, which can be a drain in resources. For example, our computer-aided engineering (CAE) software allows for optimisation that drives innovation, product quality and efficiency throughout the manufacturing process, while our Coordinate Measuring Machines (CMMs) and systems integrate metrology hardware and software capabilities that allow for automation of cross-sectional measurement, quality assurance, inspection capacity, and productivity.
At Hexagon, we also work to increase awareness and promote education on digital transformation through webinars, workshops, engagement events and many more for our industry partners, customers and users.
Could you please explore your innovations and intelligent solutions?
Hexagon Manufacturing Intelligence creates smart solutions leveraging data-driven smart technologies. All our products employ data to arrive at sustainable and innovative solutions – this includes real-time data assessment, continuous learning cycles and connecting departments to ensure intelligent ecosystems where quality drives output.
Hexagon’s Metrology solution portfolio division is of industrial capacity to ensure accurate dimensional measurements. As the largest software developer in the metrology industry, Hexagon Manufacturing Intelligence offers customisable and innovative metrology solutions for seamless data acquisition, analysis and management.
SFx Solutions is the latest from Hexagon Manufacturing Intelligence, which connects ecosystems and enhances enterprise intelligence. It is geared towards ensuring seamless autonomous and smart environments.
Hexagon also offers Production Software as well as Design and Engineering Software. Production Software utilises simulation technologies to provide solutions for production methods, and Design and Engineering Software simulates component behaviour to allow the design of quality into products.
What is your vision about an autonomous future?
In the automotive and manufacturing industry, there are two keywords that are sometimes used interchangeably: autonomy and automation. However, while both processes are meritorious in their ability to drive manufacturing innovation, autonomy is the game-changing future which we must secure.
Our vision of an autonomous future is where solutions utilising smart sensing, machine cognition, machine learning or artificial intelligence work to increase productivity and efficiency, reduce risks, improve employee safety and enhance revenues by improving order fulfillment rates, delivery speed, and customer satisfaction.
For Hexagon, to put the ‘smart’ in smart manufacturing is to enable manufacturers to maximise the use of data generated during manufacturing processes. After all, autonomy is the ultimate form of putting data to work, and to drive innovation across the shopfloor.
One example is our work in the automotive industry– specifically, with regards to autonomous vehicles (AVs).
While tech companies are racing to put AVs on the road, accidents still occur. There is no way to generate every unexpected occurrence even though AVs are tested on the road for millions of driverless miles, you cannot train the ‘artificial driver’ to react to every situation. Like many machine-learning technologies, AV perception systems can also be ‘biased for success’. They are often trained in artificially perfect conditions, leading them to fail when confronted with real-world imperfections. Machine learning cannot accurately replicate the full range of instinctive human analysis and response to novel and unpredictable situations.
So when you read that autonomous vehicle technology has exceeded X-million driverless miles – on the road, or virtually – this is by no means a metric for safety. When deciding that a car is safe and roadworthy, what matters is not how many miles it has traversed, but how many ‘smart miles’ it has covered and how many scenarios it was exposed to in those miles.
This is where Hexagon comes in.
Virtual Test Drive (VTD) software, which is used to test Advanced Driver Assistance Systems (ADAS) and autonomous driving systems, can cover as many as 13 million kilometres a day. It can simulate maximum possible driving conditions, including ‘black swan events’ or outlier scenarios such as total system faults and storms, faulty street light poles and potholes – including traffic and terrain undulations in 3D.
Hexagon’s system is well-organised in its collection of data, to extract all simulations to compute meaningful performance indexes – such as average time to collision, sensor failure or misbehavior such as mud sputters covering a component and more.
What are the major trends you are witnessing in the automotive domain with regards to manufacturing? How are you addressing these trends?
A major trend we’re witnessing in the automotive domain is with regards to first, the advancement of AVs, and second, the push for sustainability and true ‘green’-ness of EVs.
There has been a lot of debate about how green EVs really are, compared to traditional internal combustion engines (ICEs). In addition, there is a lot of debate surrounding sustainable sourcing, production and disposal of EV batteries and the rare earth materials used in these batteries.
We believe that sustainable, scalable and innovative technology is the answer to the questions. At Hexagon, our technologies and solutions are all about being scalable and sustainable – we believe that this is the true future of humanity. Digital innovation is driving emergent technologies, which are being harnessed to provide scalable and sustainable solutions and services. These are core tenets of business-centred strategies and policies, setting the stage for any organisation’s digital transformation initiative.
Global consumer trends are indicative of change in consumer behaviour that is predicated on sustainable technologies. The global pandemic is a point in which businesses had to pivot and innovate to survive. Hexagon was able to rise to the challenge by facilitating the manufacturing industry to adapt swiftly to global disruption.
Our agility and focus on innovation ensured that our business transformation was dynamic and fluid, delivering value to all our customers in a global time of need. Data-driven technologies and intelligent software have enabled us to create a future with long-term growth initiatives. For Hexagon, that means an accelerated pace of sustainability centred on the rise of smart connected cities, autonomous Internet of Things and Artificial Intelligence. The future will consist of autonomous vehicles, smart manufacturing and connected cities.
All of Hexagon’s solutions are developed with this as the guiding principle, underscored with continuity and best business practices. We adopt a holistic view and practice by driving sustainability throughout the entire value chain. We strive to ensure unparalleled productivity, lean processes and uncompromised efficiency which can only be enabled with smart solutions and simulation technologies.
Which are the major bottlenecks in today’s manufacturing industry?
To be sure, the Covid-19 pandemic has had a considerable impact on manpower on shopfloor. In addition, helping bring manufacturers, whether big or small, into the realm of Industry 4.0 is a huge challenge, especially with the issue of legacy systems and cost concerns. The major bottleneck now is resolving the issues of manpower efficiency and helping all manufacturers, both big and small, enter into Industry 4.0.
What is your outlook for new technology emergence in today’s connected world? What’s your take on Industry 4.0 and digitalisation of manufacturing?
There is no denying that the future of manufacturing is in Industry 4.0 solutions and digitalisation of the shopfloor. However, securing an Industry 4.0 future means going beyond automation. While automation has been a game changer for many decades now, autonomy is the next level that will secure the future of the industry.
We know the impetus to drive manufacturing intelligence solutions, and to usher in Industry 4.0, is compelling: A 2019 Deloitte study found that smart factory initiatives have given companies 12 per cent labour productivity gains in the past three years, and that productivity gains could ‘grow at a compound annual rate of 2.3% during 2025-2030’.
Hexagon focuses on smart and connected systems. We are focused on embedding quality into product design and engineering (D&E). Our software solutions, including simulation software, facilitate the exploration of prototypes without the need for physical manifestations that can be a drain in resources.
All our solutions ensure that quality assurance is maintained in component manufacturing and productivity, including factoring in a huge number of variables that can affect downstream manufacturing processes. Our computer-aided engineering (CAE) software allows for optimisation that drives innovation, product quality and efficiency throughout the manufacturing process.
Hexagon smart manufacturing technologies unlock and enhance the potential of Coordinate Measuring Machines (CMMs) and systems, which is at the core of all smart factories. CMMs integrate metrology hardware and software capabilities that allow for automation of cross-sectional measurement, quality assurance, inspection capacity, and productivity.
Digitalisation allows for real-time data and intuitive navigation via Hexagon’s HxGN SFx Asset Management System; fully automating measurement jobs with Hexagon’s TEMPO and EYE-D; and even monitoring environmental variations with Hexagon’s Pulse Wireless device.
What is your outlook for India’s manufacturing industry and what are your activities to push India’s smart manufacturing industry to the next level?
India is the next hub for Smart Manufacturing and there is immeasurable potential in manufacturing industry. McKinsey report identifies several sectors that could generate about $320 billion more in gross value added (GVA) than they do now within the next seven years. These sectors include chemical products and petrochemicals, agriculture and food processing, electronics and semiconductors, capital goods and machine tools, iron ore and steel, and automotive components and vehicles– all sectors which would benefit greatly from a push towards smart manufacturing that truly lives up to its ‘smart’ moniker.
Our technology is helping manufacturers pioneer mechanisms to inform design and engineering processes and provide feedback to the production process. The seamless automation and digitalisation of routine tasks will increase efficiency and make manufacturing smarter by driving both profitability and sustainability. India has the potential for long-term competitiveness and sustainability, which will solidify its position as a global manufacturing hub. This is a viable future for India with Hexagon’s innovative solutions that enhance productivity, efficiency, and performance via smart technologies.
Any comments for future manufacturing scenarios?
We see enormous gains from adopting smart manufacturing solutions in the industry, but we do not wish to see labour redundancy happen. Instead, we would say that the manufacturing industry must embrace technology without sacrificing humanity. Job loss must be kept to a minimum, with reskilling and upskilling opportunities presented to all employees to move them up the skills and values chain. In this way, manufacturers will be able to increase worker productivity, reduce the risks of dangerous manual jobs (by leaving that up to smart automated machines) and improve worker value and knowledge.