In order to remain competitive in the global economy, companies must introduce better and better products to the market at shorter and shorter intervals. Putting this into effect is to a great extent the responsibility of the participating R&D departments. Tricky steps in the product development process must be monitored, analyzed and optimized early and highly precisely. The thermal imager testo 890 is the ideal tool for this. It allows the heat allocation of individual components or whole assemblies to be measured without contact and non-intrusively. The heating and cooling actions of product components can be remarkably presented as a time progression thanks to the image sequence capturing. This makes it possible for the thermal imager testo 890 to ensure product quality as well as the efficiency of production cycles.
The challenge
The main task in R&D is to increase speed of the development times of new products without making compromises regarding quality and safety. For this purpose, important process steps must be precisely monitored and analyzed in order to be able to constantly optimize them. However, potential sources of error are not always easy to identify, so that a detailed analysis of the product or certain components is inevitable. Thermal processes are especially relevant. These can be presented as thermal images. Static thermal images can provide an insight into the heat distribution, but it is only an observation of temperature developments as a time progression which really allows all anomalies to be detected.
This is relevant in electronic development and other areas. In this field, components such as transistors are becoming ever smaller and are positioned closer and closer to each other. For this reason, overheating is difficult to identify, but can have serious consequences. The developers must therefore always keep an eye on even the smallest details, and test them for susceptibility to malfunction. A further difficulty is the lack of clarity as to when a problem occurs, and where. In R&D, it is crucial to know exactly where and when to look, in order to detect an anomaly. If, for example, temperature-sensitive components are installed adjacent to ones with develop heat, there is a latent danger of heat transfer – the desired function of an individual component or the complete product would be endangered.
The objective of R&D in the plastics processing industry is to improve cycle times and simultaneously to ensure optimum product quality. It is important here that the right mould release temperature is reached, and the moulds have a temperature at which a heat distribution is present in the mould which is suitable for avoiding flow lines or incomplete casting when injecting. The temperatures must also be monitored during the cooling phase of the moulded object after mould release, in order to test it for distortion or stretching. In addition to this, very fine faults in the plastic, such as moulding lines, must be identified precisely.
And finally, detailed observations of temperature developments usually generate very large quantities of data, of which often only a fraction is relevant. Despite this, all data have to be examined conscientiously, in order to be able to detect all anomalies. A great deal of time is lost searching – time which could certainly be be better spent elsewhere.
The solution
With its numerous innovations and intuitive functions, the thermal imager testo 890 is the optimum tool for visualizing all thermal processes in R&D, thus accelerating the product development process.
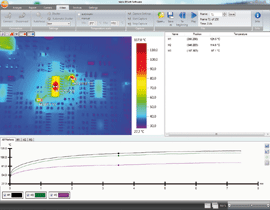
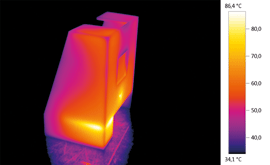
Identify even the smallest faults
Thermography of microelectronics and other measurement objects with very fine structures requires a high geometric resolution. This is the only way the smallest structures can be measured reliably. A detector size of 640 x 480 pixels is indispensable for this purpose. The testo 890 provides this – and with it, 307200 individual measurement values. In combination with a 42° lens, the thermal imager thus allows a focus distance of only 10 cm. This makes the resolution of tiny structures of only 113 μm possible. If the camera is being used in hand-held operation, the SuperResolution technology can additionally be applied. This patent-pending innovation from Testo records several images one after the other in the shortest possible time, and slightly offset to each other. Using an algorithm, these are then calculated into a single thermal image with four times the number of measurement values. Even higher-resolution images than usual – up to 70 μm – are then available when subsequently viewing the data in the professional analysis software IRSoft.
If you would like to learn more about Testo SuperResolution technology, simply order the brochure.
Analyze heat development as a time progression
If the developments of temperatures need to be observed over time, the testo 890 is able to record a sequence from a series of images. You obtain radiometric image sequences which allow you to evaluate the temperature in the thermal image for every point in the time progression and at every position of the measurement object. This avoids time-consuming searches.
The recording is made at individually configurable intervals, and can be started manually or after a timer countdown. After finishing the measurement, you can examine the recorded sequences conveniently at a PC in the professional analysis software IRSoft. If your workplace provides space for a more extensive experimental set-up with your thermal imager, you can connect the testo 890 to a PC via USB interface, and use the fully radiometric video streaming in the IRSoft function “fully radiometric video measurement”. Here you benefit among other things from a higher recording speed of up to 25 Hz.
In order to evaluate temperature developments as a time progression, you can present measurement points and profile lines as a temperature-time diagram, which you can then export as a graph or Excel® file.
Work only with relevant data
If you need to be able to record thermal images only above a certain thermal limit value, you can benefit from testo 890’s automatic, limit value-based trigger. This triggers the thermal imager only when a limit value defined by you has been reached. This function has the further advantage that you only record data which are really relevant for the development of your product. The viewing of unnecessary measurement data can be dispensed with, resulting in further time savings.
With the Testo thermal imager, you can:
- Record image sequences directly in the imager, thus visualizing thermal processes in high resolution
- Work more efficiently with an automatic,limit value-based trigger
- Transfer the measured data to temperature-time diagrams and Excel®
To know more, write to us at info@testoindia.com or visit www.testo.in