Add Value, Reduce Costs and Eliminate Risk on the Shop Floor
By adopting a true paperless environment, and not just displaying PDFs, a factory can increase yields, quality and traceability while reducing costs and eliminating many of the risks associated with incorrect or badly controlled documentation. This paper seeks to discuss the benefits of embracing a paperless system to all of the stakeholders in the processes affected and in the business. The paper also discusses methods and processes used to move towards a paperless environment where files can be interrogated, updated and commented on rather than merely viewed.
People’s perception of what constitutes the paperless shop floor may vary from individual to individual and indeed from company to company, but if you are looking to get all the benefits from going ‘paperless’ it needs to be much more than just another way of displaying documents that were formerly printed and held on the shop floor.
Deploying a system that merely replaces paper with pdf or images of paper documents will most times result in failure to gain the full benefits of being paperless. Delivering work instructions to a screen rather than via a folder full of forms and drawings may provide some benefit to operators and line managers, but does not really get to the core of the far more comprehensive solution that being paperless offers.
This is all about the delivery of information, or data, and in a paperless environment that is delivered digitally. But we need to consider more than just the method of delivery, we need to envision the type of data, the interactivity of that data, its revision control and its adaptability.
When a truly paperless system is put in place that addresses all of these issues the benefits can be substantial. When documents are merely replaced with a digital version, the benefits are much more limited.

activities and track product movement while ensuring the
correct documents are presented at the correct locations.
Take for example cost. Top of the agenda for many companies, particularly those that find themselves in the competitive space that is the EMS (Electronics Manufacturing Services) industry, where quarterly calls for cost reduction from OEMs (Original Equipment Manufacturers) are commonplace. In a paperless environment customer audits, quality audits and regulatory audits can all be done via a digital terminal and via a single system, with all revision control and document management visible. This could even be done remotely in some cases further reducing costs. This is potentially a cost saving for the vendor but also for the customer, something that they will doubtlessly appreciate and remember.
Another cost benefit comes in the form of reduced, or even eliminated personnel costs associated with the maintenance of documents like standard practice manuals, preventative maintenance manuals, user manuals and work instructions, all of which can be managed centrally rather than being disbursed all over the shop floor.
And finally the obvious cost saving of any paperless system is paper and the costs associated with printing and distributing that paper around the shop floor. It’s not like the work instructions are static, they change constantly and in a paper driven world that means reprinting numerous versions, distributing them around the shop floor, making sure everyone has seen them and doesn’t use old instructions. This is time consuming and risky.
And risk reduction is the second benefit worth highlighting in the paperless environment. The potential presence of down-revision documents on the shop floor is eliminated in a well-ordered paperless system; audits become risk free and operators are not in danger of building to the wrong document, resulting in costly rework and/or scrapped assemblies.
Beyond reduction of cost and risk, there are the improvements in performance and quality to consider. Optimizing the performance of an operator is about having them spend as much time as possible making, testing and shipping product, not searching for or through documents to find an instruction or procedure. In a CAD (Computer Aided Design) driven paperless environment, test and diagnostic data can accelerate the resolution of quality issues or the data required to expedite a repair function.
A paperless system also allows the operator to become part of the process improvement feedback loop. Feedback systems allow for fast and effective improvements in the documentation and more importantly in the process and multiple operators on multiple lines and/or shifts can impact upon any improvement initiative.
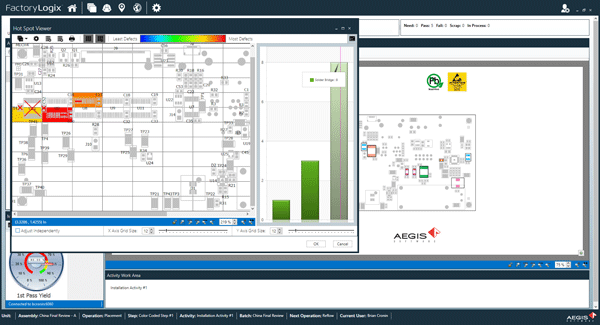
accurate quality issue resolution and robust analytics
Paperless processes also provide interactive visual data that can guarantee the current and proper parts list and CAD information is available improving quality, increasing inspections reliability as well as raising the accuracy of diagnosis and repair.
The route to paperless success
The route to paperless success requires a holistic approach that fully embraces many factors. As mentioned before digital delivery is fundamental and this needs to be available to each operator on his or her own terminal.
The type of data must also be considered. The shop floor portals should be capable of presenting interactive operator visuals, CAD and BOM (Bill of Materials) information, revision control data, analytics regarding processes, as well as supporting secondary, less regularly used documents like preventative maintenance or user manuals or standard practice manuals.
All of these documents need to be more than just flat representations. They need to be interactive allowing data to be visually queried by the operator via a simple user interface that allows for a deeper dive into data by simply clicking or touching the item in question. Visual documents that are grounded in both the CAD and the BOM and that are interactive can be queried for rich, always current data that refers back to the central manufacturing database. The final part of the interactivity puzzle is the ability of the operator to redline and provide improvement feedback that can be assessed and when appropriate implemented by the engineering team.
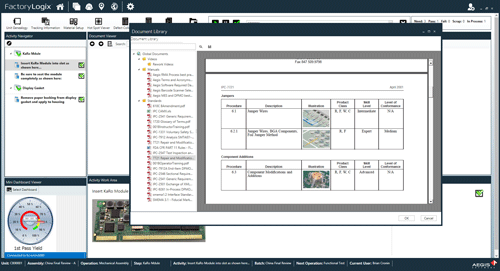
the use of large binders and cabinets of seldom-used
documents.
Revision control is a cornerstone of any system, be it with or without paper. The system must control and be fully aware of process version, design version and the stations where documents are to be deployed. The paperless system should be capable of automatically ensuring that the right documents and analytics are presented to an operator in a single scan with zero risk of displaying the wrong revision of any data.
No system can work without a degree of built-in flexibility or adaptability. The system will need to allow engineers to ‘cut in’ an emergency engineering change or a process change if it is required on the shop floor. This will need to occur digitally, simply and seamlessly, with the proper documentation and recording procedure supporting it.
The results speak for themselves
The results of such an endeavor speak for themselves and can be seen from the experiences of all those vested in the process.
From the operators point of view they can bring up the correct revision assembly instructions, dynamic video assistance, CAD images, BOM information and all associated documentation and work instructions with a single scan of the unit in production. This can be done immediately and at any point in the manufacturing process. The operator also enjoys the ability to interrogate the data provided, rotating or zooming into CAD data or digging deeper into a BOM to query a particular part. First article assembly and inspection become simpler as the operator can receive adapted and dynamic information. And finally the operator can close the feedback loop by sending suggestions to the engineering team from their own terminal instantly, supporting their value and the continuous improvement of the product and process. There is plenty of evidence supporting the tenet that operator satisfaction is much higher when the data provided to do their job is unambiguous and when their voice is heard. All lean manufacturing principles completely support the concept of operator involvement and the paperless environment simplifies this process.
Let’s explore how the process engineer benefits from the paperless experience. Where engineers are allowed to develop all visual instructions via a single digital system, first product launches and subsequent engineering changes are expedited much more efficiently. Revision control is no longer a slow, manual and risky process, but a fully automated simple procedure that can be assured throughout the shop floor. When the vast majority of supporting documentation such as user manuals, maintenance specifications, corporate procedures and standard practices are maintained digitally there is no need for the shop floor management of such documents. Revisions can be done once and the engineer can relax in the knowledge that all copies of that document are updated on all the relevant workstations and that the revision control and changes made are duly recorded.
Engineering changes are inevitable. These can be carried out quickly and can be digitally ‘cut in’ to production where required without the need for chasing legacy documents on the shop floor and without costly hold-ups in production. And most importantly the engineer can get the front line feedback from the operator digitally, before processing suggestions and incorporating them when necessary in the next revision. This creates a better dynamic between the operator and the engineer and a clearer understanding of each other’s challenges.
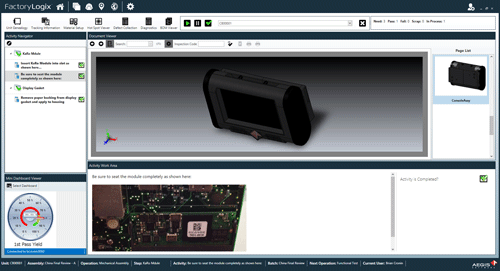
notices can be conveyed to the factory floor in real-time.
The Operation Director can also enjoy the benefits of being paperless. First of all they are ensured that down revision documents cannot be lost and re-emerge later on the shop floor. Secondly, there is no risk of operators building to the wrong revision. Thirdly, the audit path is hugely simplified for customers and regulatory agencies and that audit is wholly visible, so no unexpected surprises await the Operation Director on audit day. The whole audit process can be conducted quickly and efficiently with no shop floor disruption.
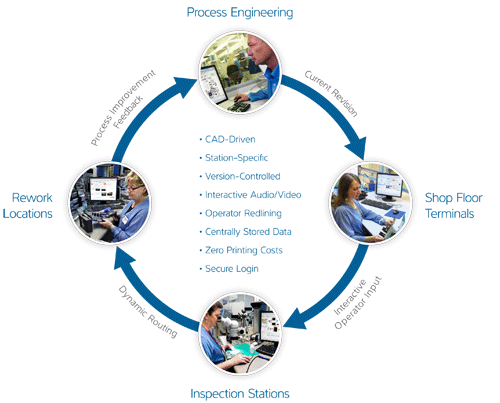
delivering increased speed, control and visibility to your manufacturing operations.
New product introduction becomes faster, simpler and more reliable with a paperless system. Digital review and approval procedures, using electronic signatures, are simplified and are more reliable, ensuring that improper data never reaches the shop floor, and traceability is absolute in all product documentation and data. And lastly the Operations Director can take the majority of the cost of printing and paper out of his operating costs.
Perhaps the most important person in any value chain is the customer and the demonstration of an in-control documentation system is certainly valuable to them. Risk reduction is hugely valuable as customers see the risk of product being manufactured with an outdated or incorrect specification being eradicated. Customers’ costs related to on-site audits are also reduced as this process is simplified. Customers like faster new product introduction (NPI), they like to be able to make changes quickly and reliably and they like to be able to gain full traceability quickly and seamlessly when they need it. All of this adds up to improved levels of customer satisfaction and better customer retention.
In conclusion
In short the true paperless factory is a much larger issue than merely digitizing work instructions and presenting them to an operator. Managing the entire digital thread from design data, through revision control and work instructions and bill of materials to final dispatch, along with control of revisions and engineering changes, is the real path to paperless enlightenment. A path that leads to improvements in manufacturing excellence, reduced engineering and management overhead and a more reliably repeatable method of manufacturing.
Only a holistic approach to the question of documentation, including version and change management will provide all the benefits available from a paperless manufacturing environment.