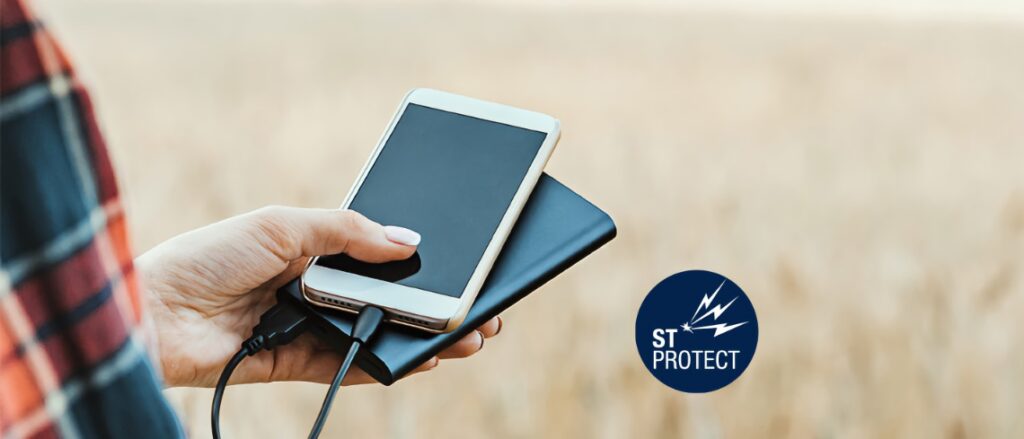
The TCPP02-M18 protects USB Type-C ports in source mode against over-current on the VBUS pin and against over-voltages of up to 24 V on the communication channel (CC lines). It is a companion chip to USB-C platforms running on STM32 MCUs that includes a current sensing mechanism accessible by the microcontroller for greater application control. The TCPP02-M18, is a Type-C Port Protection (TCPP) for devices that send a charge (source), unlike the TCPP01-M12, which protects USB-C ports in sink mode (charging). And while both have similarities, like system-level ESD protection rated at ±8 kV IEC61000-4-2 Level 4 on CC1 and CC2 pins, they tackle significantly different challenges.
Why Does the TCPP02-M18 Matter Today?
The New Challenges from Harmonization
The European Commission has been pushing for charging devices to use USB-C connectors, thus creating new challenges. In fact, the European Parliament announced a new directive last week mandating a common USB-C charging port on all mobile phones by autumn 2024. Previously, many companies would design and ship a specific charger for their product. Designers even used rare barrel jacks to ensure consumers would only use the charger they conceived. The European initiative will suddenly mean that one charger will work with a wide range of devices. As a result, engineers must account for more edge cases, faulty sink systems, etc. The environmental benefits of such a measure are essential. However, the electrical challenges it represents are significant.
Amongst the many issues engineers must solve, there are three main concerns: power optimizations, form factor, and cost. Consumers are demanding smarter chargers. Designers must thus create applications that optimize power consumption, especially when pushing the charger to its limits. Additionally, despite all this, consumers still want cheaper and smaller chargers. After all, the whole spirit behind the EU’s initiative is to reduce electronic waste. Hence, solving all three issues is particularly difficult.
The Ability to Do More With an STM32 and the TCPP02-M18
Traditionally, engineers rely on a port controller. The problem is that they don’t house an entire Cortex-M core and their memory capabilities remain small. They thus represent an added cost to the bill of materials (BoM). Engineers can’t use them for anything else except the USB-C port and adding essential features like current sensing often means integrating even more components onto the motherboard. Consequently, shrinking the PCB while adding all this becomes a serious issue that requires much work and can delay a release to market. Moreover, a controller and a protection device also require external PMOS transistors, increasing the BoM.
Engineers, however, have solutions to sidestep all these landmines. For instance, using an STM32 microcontroller with built-in USB-C PD controllers allows for far greater computational throughput. Engineers can optimize their power management system thanks to more advanced controls and even run their entire firmware alongside their USB-C application, simplifying overall developments. For instance, it’s possible to connect the TCPP02-M18 to the ADC pin of an STM32 to benefit from instant current sensing measurement very easily. Put simply; engineers can build far more feature-rich applications in a more straightforward process.
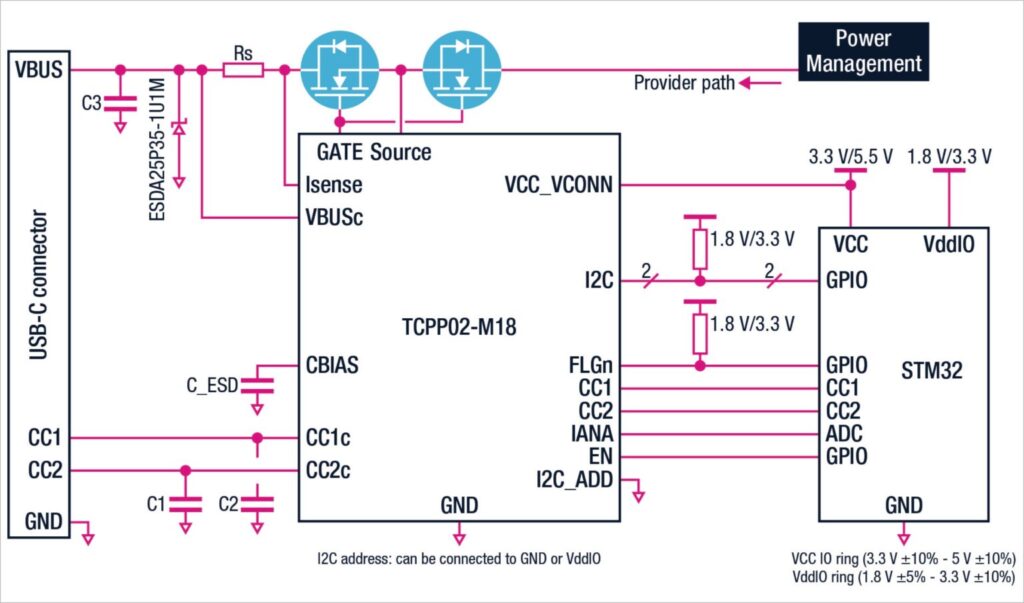
Size and Cost
Another consequence of using an STM32 and a TCPP02-M18, or any TCPP devices for that matter, is reducing components on the PCB. It becomes possible to create a robust system without adding complex ad hoc controllers or a myriad of external components. As a result, shrinking a design becomes far more straightforward. Engineers also get better reliability assurances. Indeed, fewer devices mean fewer fail points. Moreover, STM32 microcontrollers have a 10-year support warranty, while the TCPP family directly benefits from our BIPOLAR-CMOS-DMOS (BCD) technology, recently recognized as an IEEE Milestone. As chargers must now handle a wide range of use-cases, it is essential to meet new reliability requirements.
A more straightforward and reliable design also means a more cost-effective BoM and life cycle. If engineers use an STM32 that doesn’t integrate a USB-C PD controller, they can still use a TCPP02-M18 to design 5 V / 3 A legacy applications. And those STM32 with a USB-C PD controller can manage up to 20 V and 5 V for up to 100 W. In both cases, an STM32 and TCPP02-M18 help drive costs down. Additionally, the TCPP02-M18 companion chip includes a charge pump that drives more cost-effective NMOS transistors instead of PMOS devices.
What Makes Source Protection Special?
VBUS Protection
The USB Implementers Forum (USB-IF) defined unique responsibilities for a USB-C port in source mode. For instance, the product charging another system must monitor and control the electrical current. Hence, the TCPP02-M18 has over-current protection with an integrated gate driver on the VBUS. Comparatively, the TCPP01-M12 for sink devices has over-voltage protection since products receiving a charge must negotiate the voltage and protect themselves against defective chargers or cables. Additionally, USB-IF defined the source port as a cold connector. In a nutshell, it means that there can be no current flowing after disconnecting a cable. As a result, the TCCP02-M18 has a discharge path redirecting current to the ground after a disconnection.
CC and VCONN Protection
USB-C is a reversible connector, meaning that a cable will plug into the port regardless of which side is up. This is possible because the connectors use two communication channels, one at the top (CC1) and one at the bottom (CC2). Since USB-C cables only have one CC wire, the port detects which channel the cable connects to, thus determining the orientation. Protecting the CC lines is therefore essential. TCPP02-M18 provides over-voltage protection of up to 6 V on the CC lines against a short to the VBUS. The protection device also guarantees high ESD protection on the communication channels.
After plugging a USB-C cable, the unused CC line serves as an optional power line for cables, if needed, and for small accessories. For instance, the line called VCONN may power electronically marked cables (EMCA). The latter include ICs that can shape the signal to extend cable length, among other things. The challenge is that the USB-IF sets the power on the VCONN at 0.1 W. Hence, the TCPP02-M18 includes over-current protection of up to 50 mA and over-voltage protection of up to 6 V to guard against a short-to-VBUS.
How to Get Started?
The quickest way to start designing a USB-C source product is to take inspiration from our two development kits: the STEVAL-2STPD01 and the X-NUCLEO-SRC1M1. The first is a dual port reference design that uses two TCPP02-M18, one STM32G0 housing two USB-C PD controllers, and a power-sharing feature. Indeed, the STPD01 can share 120 W. Hence, theoretically, if one port is only charging a legacy device at 15 W, the other port could deliver the rest of the 120 W envelope. The STEVAL-2STPD01, however, limits each port to 60 W (20 V at 3 A). Engineers get a schematic and a software package, the STSW-2STPD01, to get started toward customization.
The X-NUCLEO-SRC1M1 is a more traditional daughterboard featuring one USB-C port, a TCPP02-M18, and everything needed to support power profiles of up to 100 W, thanks in part to its ST715 high-voltage regulator.. Engineers can use it on Nucleo boards with an MCU that includes a USB PD controller, such as the NUCLEO-G071RB, NUCLEO-G474RE, and NUCLEO-G0B1RE. It makes an application design much more straightforward, especially after using the X-CUBE-TCPP drivers and middleware. Using the X-NUCLEO-SRC1M1 without an MCU embedding a USB PD controller is also possible, with the NUCLEO-F446RE serving as an example. However, developers will simply benefit from a 5 V solution in that configuration.
Click link: https://blog.st.com/tcpp02-m18/