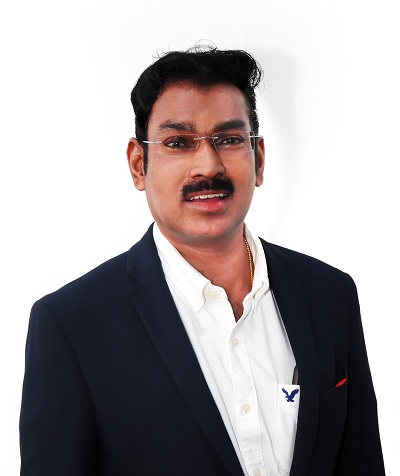
Sekaran Letchumanan, Vice President, Operations at Flex India, in an exclusive conversation with Electronics Maker shed light on latest technology trends in electronics manufacturing, Flex sustainable business model to drive circular economy. He also spoke about Digital Twin technology and its benefits in manufacturing process.
How does Industry 4.0 improve supply chain management?
Industry 4.0 has revolutionized the way the manufacturing industry functions. Advanced technologies such as Automation, Virtual Reality, Cloud, Big Data, and Cybersecurity now help bridge multiple gaps that were previously existent in the manufacturing process. Enhanced connectivity and machine intelligence are Industry 4.0’s hallmarks. Manufacturers are harnessing the benefits of cyber-physical systems and the Internet of Things (IoT) in factories, delivering improved efficiency, quality, and sustainability to customers.
Smart Automation, Machine-to-Machine communications, Cloud Computing, and Real-Time Analytics made it easier to predict potential disruptions and identifies abnormalities to provide smooth operations. In an increasingly complex and uncertain global scenario, our strong partnerships and supply chain management tools mean Flex is well-equipped to deploy Industry 4.0’s wide range of benefits.
Share your thoughts on the importance of a circular economy in electronics manufacturing.
The circular economy re-evaluates and disrupts the traditional linear supply chain model that gets products into the market. When implemented correctly, a circular economy model helps lengthen product lifespan, reduces waste, and most importantly, creates a more sustainable world.
In today’s context, sustainability is arguably the most important benefit derived from circular economies. Flex’s solutions are based on four key aspects – Sustainability Analytics, Design for circularity, Product as a Service, and Product lifecycle Management. We also partner with customers to focus on aftermarket and end-of-life services with the goal of minimizing environmental effects.
Sustainability is at the core of our vision, especially in a world where companies are being held to higher standards in terms of product sourcing and disposal. We believe that emphasizing on sustainable manufacturing is critical to earning and retaining the trust of our customers, suppliers, and employees.
How are Digital Twin simulations advancing digital transformation in manufacturing?
We think of Digital Twins as a bridge between the digital and physical worlds. Since a Digital Twin is an exact replication of physical models or systems, it allows us to simulate processes and scenarios before they occur in real time. This eliminates the need for physical trial and error that costs manufacturers valuable time and resources. This leads to enhanced cycle time, improved quality, and reduced costs. The data integrated into digital twins can encompass environmental factors such as temperature and humidity as well as physical attributes such as weight, dimensions etc.
Some of the benefits manufacturers can derive from digital twins are:
More Flexibility in Planning of Production – The traditional trial-and-error process typically does not allow manufacturers to pivot between desired outcomes quickly. By Leveraging digital twins, manufacturers can determine optimal output, from quantity optimization to revenue maximization.
Increased Agility in Operations – This is exemplified by Flex’s partnership with a medical device client in the launch of a new Class II Diabetes product. Digital twins allow our customers to run numerous trials quickly, enabling product refinement, and cutting time-to-market from months to just weeks. In fact, production figures can even surpass quarterly estimates by a significant margin.
Integrated collaboration between automation and humans – Humans continue to form an integral component of the manufacturing process and exercise crucial decision-making in factors such as time-to-market consideration and cost. Flex recommends a gradual adoption system known as “autonomation,” Which introduces automation into specific, necessary steps. This supports human employees and streamlines the entire process while enabling smoother workforce development.
How are emerging technologies helping to eliminate waste and promote sustainable practices? What are the enabling factors?
Emerging technologies play a vital role in driving manufacturers’ sustainability efforts by maximizing resource utilization and promoting sustainable practices. An area of concern where these technologies excel is carbon emission reduction. Advanced analytics and the Internet of Things (IoT) enable manufacturers to monitor energy usage and emissions data to identify areas for improvement, optimization, and ultimately reduce their carbon footprint.
Industry 4.0 solutions also enable manufacturers to optimize waste management, track resource utilization and improve efficiency. Simulation tools such as digital twins can help boost production by providing a line of sight into the transition from design to production, efficiently minimizing raw material consumption.
Meanwhile, 3D printing offers precise and localized production, reducing transportation emissions, and can be used to design parts for refurbished products, further enabling circular practices.
How is Flex helping the electronics industry achieve a sustainable business model?
In 2021, we announced our commitment to cut our operational emissions in half by 2030 through implementing and purchasing renewable energy and optimizing site infrastructure. We doubled down in 2022, announcing our commitment to reach net-zero greenhouse gas emissions by 2040, taking an ecosystem approach including investing in site and system efficiencies, procuring and deploying renewable energy, and continuing collaboration with our ecosystem of customers and suppliers.
Our circular economy philosophy acknowledges that sustainable changes do not occur instantly or via isolated “off-the-shelf” solutions. Recycling solutions alone cannot singlehandedly enable circular value chains to deliver a positive environmental impact. Instead, we craft a set of solutions (comprising repair, refurbishment, and recycling) that are tailored to align with our customer’s organizational targets.
Our collaborative approach employs a fleet of services such as the homegrown Flex ECO2 tool that analyze information and help customers quantify both long-term and short-term effects. Digitalization also a critical role, helping manufacturers reduce their environmental footprint by providing live insights and real-time data.
Flex’s commitment to achieving a sustainable business model is visible in our sites across the globe. Take our smart factory at Althofen in Austria, for example, which is part of the World Economic Forum’s Global Lighthouse Network. Powered by 100% renewable resources, it is carbon neutral and includes real-time data monitoring that alerts us to high energy consumption or leakages.
Meanwhile, our zero-waste-certified site in Sorocaba, Brazil, uses these technologies to repair, recycle, and transform e-waste into repurposed resources. Waste tracking and cloud-based logistics systems drive waste collection at Flex Sorocaba, resulting in a 94% reduction in waste and a 38% decrease in plastic material expenditure. The facility also implements automated management systems and CO2 dashboards to pronounced effect, saving resources equivalent to 44,000 carbon credits.
How does Flex optimize products throughout their entire lifecycle?
We put a great deal of effort into crafting services and solutions that can cater to the diverse needs of different business models. But we also believe that our solutions must be adaptable according to each customer’s unique requirements.
Today’s markets are dynamic, which has placed added emphasis on agile, omnichannel fulfilment strategies on a global scale, and after-sales services. Manufacturers now look to collaborate with partners who operate around the world and bring cross-industry knowledge to the table.
The ideal solution is one that:
- Pays attention to every detail of the customer experience.
- Establishes a circular product chain – from innovative design and manufacturing to afterlife services such as returns, repair, and recycling.
- Strikes the right balance between maximizing economic value and minimizing environmental impact.
Flex has been empowering customers to achieve specific goals by seamlessly configuring and optimizing paths and channels to the market, for decades.
What are the latest trends in the Indian manufacturing industry for global competitiveness?
Few trends that that are increasingly used globally are:
• Robotics and automation in production processes –Plays an important part in optimizing production by fulfilling strenuous, repetitive tasks.
• Digitalization of manufacturing sites and supply chains – helps make predictive, well-informed decisions on timeframes, resource utilization, and operations.
• Digital twins – this concept allows manufacturers to simulate specific processes, thereby eliminating the traditional trial-and-error approach that is bogged down by a waste of resources and inefficient time management.