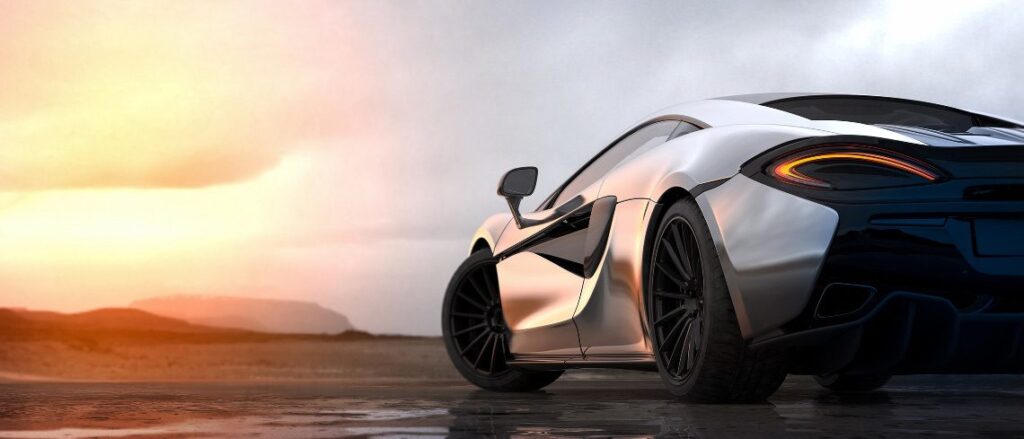
ST recently launched its Stellar P6 line of microcontrollers for light and heavy vehicles. Targeting platforms for domain-oriented applications, the device offers up to six Arm® Cortex®-R52+ cores. Built on a 28-nm FD-SOI process node, the Stellar P6 provides up to 2 x 16 MB of phase-change memory ready for over-the-air updates for greater performance and reliability in harsher conditions, such as high temperatures1. The Stellar P6 also includes IP that accelerates hypervisors. Developers can thus run multiple virtual machines to isolate functionalities, save resources, and pass stringent certifications. The feature also highlights the increasing importance of software integration. As software-defined vehicles (SDVs) transform the auto industry, what does it mean to build a car today?
The advent of software-defined vehicles and the transformations they have brought
How is the car changing?
In a feature article published in 2021 in IEEE Spectrum, Robert Charette explained: “how software is eating the car.” Gathering analyses from experts and industry leaders, the paper indicates that a car may contain more than 150 electronic control units (ECUs) running collectively hundreds of millions of lines of code. A few years ago, only high-end models displayed such complexity, but today even mainstream trims are software driven. The rise of software in cars follows the increasing number of ICs. Hence, the automotive industry is undergoing massive transformations that redefine what customers expect from a vehicle. Manufacturers must, therefore, adapt to the new trends and requests.
Consumers are familiar with many of the transformations currently shaping new vehicles. With the advent of more and better sensors, drivers started asking for innovative safety features that use software to recognize pedestrians or anticipate accidents. Consequently, makers developed code to predictively alert drivers of a potential collision or remind them of upcoming critical maintenance operations. Similarly, computer programs define new and more sustainable driving modes to extend a vehicle’s efficiency. Software-defined cars are also unique due to their connectivity to a cellular network and cloud platform that enables them to receive dynamic updates. Hence, for the first time, manufacturers can issue a patch instead of an expensive recall, vastly improving the consumer’s experience.
Value proposition for the consumers
Car makers also benefit from these new business models in unique ways. Thanks to over-the-air updates, manufacturers no longer have to release next year’s model to innovate. Moreover, they can port previously purchased functionalities or a customer’s settings to other physical models, thus increasing user retention. Subscription models generate new and recurring revenue streams by enabling makers to add services and tailor experiences. It is far simpler to customize software than a car’s frame. Consequently, companies now use software to build a more personal relationship with their customers while transcending a physical vehicle. It’s no longer about a machine but an ecosystem of applications. And now that OEMs treat cars as smart devices, they need development powerhouses.
The challenges behind this new transformation and how OEMs are dealing with it
The challenges to software development
Users want software-driven vehicles, and car makers aim to deliver. However, the last 60 years of computer science testify that a software ecosystem is only as effective as the hardware platform it runs on and the tools that take advantage of it. The history of ecosystems is filled with promising projects that failed because they were too hard to work on or couldn’t bring the performance and features promised. Software-defined vehicles thus demand a robust silicon architecture and development environments that will hasten software engineering while ensuring optimal security, safety, and performance. The problem is that creating an optimal software paradigm for cars can be challenging.
In a guest commentary published in the journal ATZelectronics worldwide2, Jörg Ohlsen explains that some in the industry are struggling to find the “skills [or] resources […] on the industrial scales [needed] to be competitive.” While some have cracked the code and are profiting from the new paradigm established by software-defined vehicles, Ohlsen posits that some are feeling “overwhelmed” because their core business is so different from software development. Some car makers expressed a similar sentiment and delegated software creation to OEMs as a solution.
The challenges to software-driven vehicles
Besides grappling with software development, companies must deal with the specific challenges of a software-defined vehicle. For instance, nodes, domains, and zone controllers run in parallel, sometimes interacting with one another or independently, and must not interfere with one another. The head-up display (HUD) on a windshield must work with the cruise control or lane-change detection to display information and warning. Similarly, the airbag deployment system can’t be affected by the data transmitted through the entertainment unit. Moreover, with the advent of software-defined vehicles, car makers must deal with more data and a different type of connectivity, such as cellular networks that deliver over-the-air updates.
The wide variety of software solutions combined with the need to resort to a greater range of providers and OEMs can create a perfect storm. Consequently, OEMs are rethinking how they manage operating systems, software stacks, and development operations. They are creating new partnerships and adopting platforms like Stellar products to broaden their capabilities and meet the new demands of software-defined vehicles. Similarly, car makers must ensure that ECUs work together and that all modules follow strict safety, security, and reliability standards. Even if they rely on OEMs, manufacturers must understand how to build an ecosystem, which also explains why many require Stellar products.
The Stellar solution to software-driven vehicles
Why Stellar P, Stellar G, and Stellar E series?
The launch of the Stellar P6 is symbolic because it comes at a time when the industry is clamoring for a hardware solution to the challenges inherent to software-defined vehicles. Stellar is a platform featuring 32-bit microcontrollers by ST for the automotive industry. There are two main categories of devices: Stellar Actuation and Stellar Integration MCUs. The former includes the Stellar E series, which is fast enough to drive silicon carbide or gallium nitride transistors. It provides fast analog-to-digital conversion, precise pulse-width modulation, and more, thanks to advanced timers and a CORDIC accelerator, among other things. As a result, it offers the necessary actuation for the drivetrains and power conversion operations found in electric vehicles.
The second category of Stellar devices, the Stellar Integration, comprises Stellar G and Stellar P. The first is for zone controllers, gateways, and body integration. It acts as a power, data, and I/O hub, among many others, or works as an aggregator for modules in a specific vehicle zone. Finally, the Stellar P helps engineers simplify designs by facilitating the integration of drivetrains and domain-oriented applications. All Stellar Integration MCU have real-time and deterministic performances to help run the various modules efficiently. Hence, the Stellar family of devices is broad enough to handle the ecosystems that consumers rely on in their software-driven vehicles.
How to answer security, safety, and communication challenges?
As developers also look to take advantage of the new software paradigm to improve overall security, ST provides support for over-the-air updates on all Stellar MCUs to ensure carmakers patch issues rapidly. The update mechanism also helps save up to 50% of memory usage. As a result, engineers can use fewer memory modules for a lower bill of materials. Additionally, all devices include a hardware security module and a cryptographic hardware accelerator. Developers can thus adopt best practices to protect keys or encrypt and decrypt data without hindering performance.
ST also prioritized communication interfaces to provide a software-driven platform suited for various car applications. Designers will find the traditional modular controller area network (MCAN) supporting CAN-FD and compatibility with LIN interfaces. Moreover, the Stellar Integration MCUs feature CAN-XL interfaces, which support far greater payloads and can help future-proof a platform. Stellar P and Stellar G also offer an ethernet controller for high-speed communications. Finally, Stellar Integration devices support hardware and software hypervisors to help with safety requirements. Systems can run multiple applications concomitantly or add new programs without risking existing installations.
Click Link- https://blog.st.com/stellar-p6-software-defined-vehicle-sdv/