New Simulation and Analysis tools in 0D and 1D can achieve large-scale design space exploration
Serdar Ucku, CEO and founder of CyDesign Labs
Imagine generating 1,000 design alternatives for a new rocket engine and analyzing the performance and behavior of these designs in parallel, using virtually unlimited computing resources in the cloud. This is the promise of design space exploration.
Simulating and analyzing a vast space allows designers to:
- Isolate and eliminate inferior designs;
- search for and identify promising optimal designs;
- verify designs with respect to system requirements;
- identify design tradeoffs to maximize performance; and
- move to detailed designs with proven system models.
Today’s simulation and analysis (S&A) tools allow engineers to study and verify system properties and visualize the thermal, structural, electromagnetic and other physical properties without having to build a physical prototype. We can crash simulated cars into walls, perform stage separation in simulated rockets, and fly virtual aircraft with remarkable precision and accuracy. But for the most part, engineers only run a handful of designs through the S&A process because of the tool costs and the time it takes to create models. Furthermore, verification and certification of system designs is often done using actual hardware–a rather costly and time-consuming endeavor.
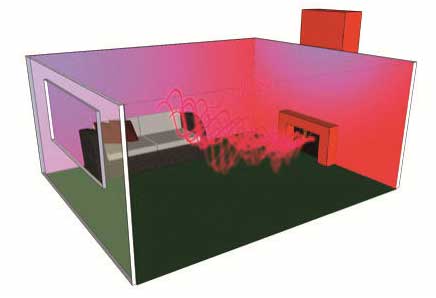
It doesn’t have to be that way. In the semiconductor industry, new chip designs are routinely optimized and verified using computer models and simulations, using a process known as “correct by construction” design (Sangiovanni-Vincentelli 2003). Achievement of a similar capability has been the Holy Grail of complex cyber-electromechanical systems design for the last couple of decades.
Arguably, it is much harder to do correct-by-construction design for systems that directly interact with an uncertain external world. On the other hand, computing power is ever-increasing. In theory, simulation capabilities should become more affordable and readily available.
And with that, a compelling vision emerges: Could true design space exploration finally take place without having to create physical prototypes?
Achieving Design Space Exploration
The reality is that sophisticated S&A tools are only available to a privileged few. The majority of model-based engineering analyses use complex methods such as computational fluid dynamics (CFD), finite element analysis (FEA), and multi-body dynamics (MBD). These tools require a 2D or 3D design configuration as the starting point for grid generation.
Imagine what’s required to generate one 3D design for a passenger car, and multiply it by 1,000 design alternatives. Even if we were to only use conceptual CAD models, it would require extraordinary computing power and data storage–not to mention simulation and design expertise.
And so, even with the movement to bring more cloud-based S&A tools to market, 3D thinking will still result in very few designs being extensively explored, thanks to their complexity.
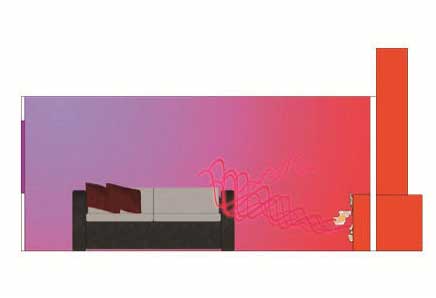
So, what is the alternative? The key is to free ourselves from the constraints and commitments imposed by precise 3D configurations. Detailed low-dimensional models of system behavior can provide valuable insights into system performance and function. And once an appropriate high-fidelity, low-dimensional model has been found to perform well, it can easily be augmented with appropriate 3D details.
Breaking Down the Walls
Let’s look at this in the context of a familiar example: heating a living room. Imagine a fireplace on one side of the room, an open window on the other side, and a cold winter day outside.
A 3D CFD model would be the most detailed model of the thermal characteristics of the room. We could use such a model to study heating irregularities within the room, or to better understand thermal flux. A typical CFD model of the room would divide the space into a 3D mesh, and then use a set of partial differential equations (PDE) to evolve the temperature (and possibly humidity, airflow and other factors) in each segment of the mesh as a function of time. To produce meaningful results, the CFD model would require knowledge of the precise geometry of the room, including furniture placement, other impediments to heat flow (such as columns), and the thermal characteristics of the objects in the room.
A 2D model of the room would follow the same principles as a 3D model. To simplify modeling and simulation, we could use a 2D grid that divides a 2D cutaway of the room into individual cells, and a set of PDE models to define the heat transfer between the cells. We might ignore the width of the room and simply model heat transfer along the length (fireplace to window) and height (floor to ceiling) axes. By eliminating one dimension, one could achieve significant computational speedup in exchange for some loss in precision.
Properties of 0D, 1D and 3D Models |
|||
OD |
1D |
3D |
|
Behavior |
System dynamics as a function of time | System dynamics as a function of time and one dimension | System dynamics as a function of time and space |
Type of model |
Lumped parameter ordinarydifferential equations or differential-algebraic equations | Ordinary differential equations or differential-algebraic equations | Partial differential equations |
Inputs |
Component-connectivity model;component behavior models; context | Component-connectivity model;component behavior models; context | 3D CAD configuration; materialproperties; context |
Critical expertise |
Model abstraction | Model abstraction | Grid generation |
Typical use |
Component sizing; design space exploration; preliminary verification of performance and function | Component sizing; design space exploration; preliminary verification of performance and function | Detailed analysis and verification of performance, risks, and failure modes |
Common tools |
MATLAB/Simulink, Modelica, C, Java, Excel | MATLAB/Simulink, Modelica, C, Java, Excel | Various open and proprietary CFD and FEA solvers |
Both 2D and 3D models are based on PDEs, which are difficult to solve. By contrast, 0D and 1D models could be based on ordinary differential equations (ODEs) or differential-algebraic equations (DAEs) that are easier to solve. A 1D model of the same room would define heat transfer along the length axis of the room (from fireplace to window), while a 0D model would assume that the temperature is uniform across the entire room (commonly referred to as a lumped parameter model) at any given time.
A significant advantage of 0D/1D modeling is that one does not need precise 3D geometry to develop lower-dimensional models. While lower-dimensional models do not provide the same level of precision as detailed spatial models, they can be used during earlier stages of design (prior to conceptual or detailed CAD) for the purpose of design space exploration.
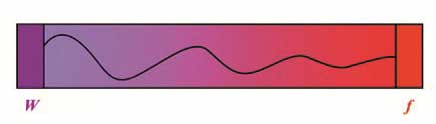
A vast space of system configurations may be generated rapidly by using a component model library and by composing end-to-end system models from these components. For instance, we could easily generate and analyze 1,000 alternatives by choosing from 10 window sizes, 10 fireplace models and 10 different-sized rooms. In this particular case, a 1D model of heat transfer could be used quite effectively to determine the proper fireplace size to meet certain room-heating requirements. Once the sizing study is completed using a 1D model, the designer can incorporate the appropriate fireplace into the 3D design of the room.
In other applications, the insights gained from 1D analysis may help constrain the 3D configuration options. For instance, performance analysis of an electric powertrain might place constraints on the size of the vehicle under consideration.
A Final Word about Model Fidelity
It’s true that 1D models do not have the same level of fidelity as 3D models, and it’s often not be possible to study all pertinent behavior using a 1D model alone. However, the goal of space exploration design is to eliminate inferior designs from consideration so that detailed S&A efforts may be spent on the most promising designs. By using high-fidelity surrogate models in less than three dimensions, we achieve substantial performance gains in the overall design process without sacrificing final product quality. Simply put, three dimensions are sometimes just too many.