Viscom AG’s Technology Forum has a reputation for offering participants wide-ranging content with valuable practical relevance in a compact format. Looking at the big picture is a key aspect as well. Held at the beginning of October, the event on Viscom’s campus in Hanover, Germany, again offered extensive opportunities to experience cutting-edge inspection solutions for electronics manufacturing live and discuss important topics with fellow specialists, just as before the pandemic. Those unable to attend the Forum in person had the chance to participate in the interactive online program.
How much can our experience help us in a time when changes are happening faster than we were used to in the past? Why do we need a culture today in which it’s also okay to make mistakes? In his talk “Never get lost – the art of making difficult decisions,” well-known keynote speaker Peter Brandl discussed at this year’s Viscom Technology Forum how we can establish more clarity and direction in order to actually achieve the goals we have set for ourselves. Brandl noted that many projects take on an incredible dynamic of their own. Discussions center on problems and difficulties, and everything goes around in circles without moving forwards. Brandl is a consultant, pilot, author, and entrepreneur, and he highlighted various decision-making pitfalls to be avoided. Some examples include entrenched habits or the familiar bubble that happens online in particular, where we’re soon surrounded only by people who have opinions and attitudes similar to our own. Brandl urged his listeners to be more prepared to take risks and to build teams that bring together various strengths and affinities.
One hotly debated issue that requires clear decisions and rapid action in our current times is the question of which climate strategies are the right ones. Karsten Schischke from the Fraunhofer Institute for Reliability and Microintegration offered a fascinating insight into this issue at the Viscom Technology Forum. His talk focused on approaches that can be effectively put into action in companies today, from their own production through to the delivery chain. These considerations should take into account the company’s own vehicles, heating using fossil fuels, process emissions, electricity consumption, and upstream and downstream activities. At the same time, Schischke also specifically addressed PCB manufacturing and mentioned related influencing factors such as the number of layers in the product or the energy mix the company uses at its production site.
Both Brandl and Schischke as well as the speakers from Viscom presented their topics in the traditional way, live in front of an audience. In 2021, the Viscom Technology Forum had to be held completely online. It goes without saying that no one involved in the planning could be completely certain that COVID-19 wouldn’t put the in-person component of this year’s hybrid event at risk at the last minute. However, the provisions in place together with appropriate preventive measures made it possible to successfully link this event back to those held in the years prior to the pandemic, and Viscom was able to present a wide range of innovations in front of a large audience of interested attendees. “We showed our best side and can be proud of how we’ve moved forward. That’s something that becomes particularly clear at an event like this,” says Carsten Salewski, Head of Sales, Marketing, and International Business at Viscom. This year’s motto was “New Horizons in Electronics Production – an Innovative Approach to Automation with Smart Inspection, AI and Process Networking.” A corresponding English version of the two-day event was held online directly afterward.
The chosen motto intentionally brings to mind that quality control needs to always stay one step ahead of market requirements in the production of cutting-edge electronics, an area that never stands still. The Viscom Technology Forum responded by offering concrete solutions that open up new horizons. One example is a cleverly designed status monitoring solution for the inspection systems and associated peripheral equipment being used, such as offered by Viscom as part of its modular vConnect platform. This creates the conditions for forward-looking action in keeping with modern predictive maintenance. Central IT management and efficient handling of large quantities of data are other elements in this comprehensive toolbox which was examined from various perspectives during a presentation.
Artificial intelligence is one of many terms that comes up in connection with vConnect. The Viscom Technology Forum 2022 placed a separate focus on this topic. Customers had the chance to discover what AI is capable of on production lines today during one of the workshops on offer. Whether it’s verifying inspection results or segmenting voids – artificial intelligence can provide production staff with effective support in detecting errors and helps to make their work more flexible. Other topics covered in the wide range of talks, workshops, and meet-the-expert sessions included, for example, the use of ECAD data as the basis for creating inspection programs, 3D layer analyses and volumetric display in the area of manual and automated X-ray imaging, the right way to handle radiation loads in inline X-rays with the help of a special dosing server, ensuring the repeat accuracy of 3D AXI inspection results or rapidly transferring 3D AOI data via the open IPC CFX interface.
The industry itself wasn’t the only source of interest in the Viscom Technology Forum. The field of politics was also represented by well-known figures from Germany’s Social Democratic Party, with member of the Bundestag and party head Lars Klingbeil, member of the Bundestag Adis Ahmetovic, deputy chairman of the parliamentary group in the state parliament of Lower Saxony Stefan Politze, and president of the Hanover region Steffen Krach making a visit to the event. An intensive discussion focused on various aspects, including where policymakers can provide effective support to companies like Viscom. In addition, a short tour provided a vivid look at Viscom’s way of working and the special features of the inspection systems produced by its employees.
Those at the Viscom Technology Forum who were interested in taking a detailed look behind the scenes of the company had the chance to go on an extensive tour that offered an exclusive insight into production and logistics. Items on the agenda included, for example, a visit to the competence center for microfocus X-ray tubes, where a wide range of closely interlinked tasks have been located since June 2019, ranging from development, to production and final approval, and all the way to custom adaptations of the tubes. The center is home to three radiation shielding rooms for conducting fatigue and stress tests on the products. Meanwhile, tailored tours focusing on innovation at Viscom provided a compact look at the current highlights of the 3D SPI, 3D AOI, 3D AXI, 3D MXI, 3D Bond, and CCI inspection technologies. Key information was provided directly at each of the inspection systems in the form of a quick overview.
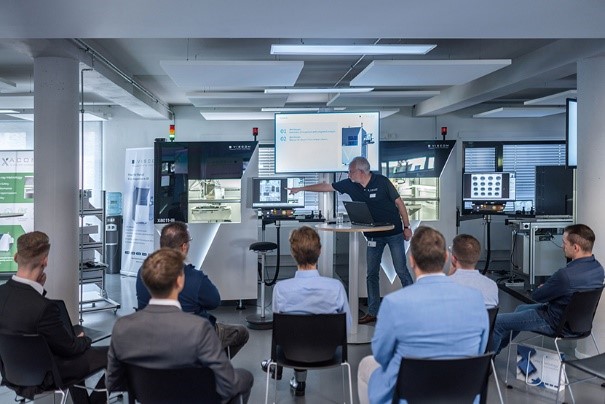
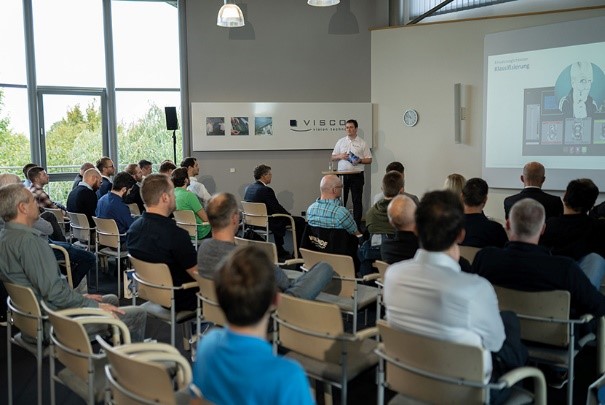
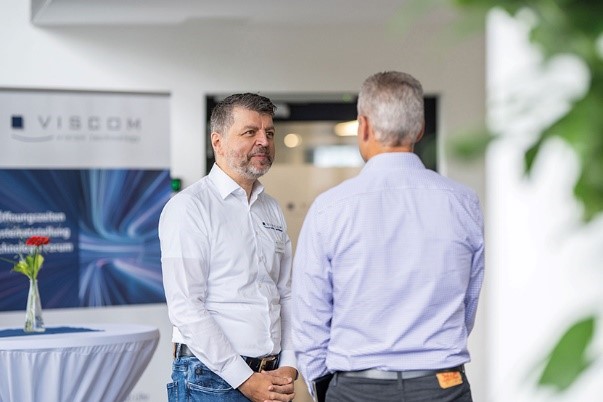