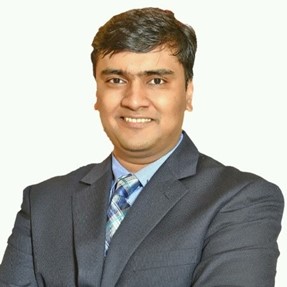
In this exclusive interview, Pramit Nandy, Product Marketing Manager for the MCU16/DSC Business Unit at Microchip Technology Inc., sheds light on the groundbreaking dsPIC33A series. Discover how this advanced Digital Signal Controller is set to revolutionize industries from automotive to AI by addressing energy efficiency, security, and software complexity in modern embedded systems.
1. What are the current complexity and high-performance requirements of embedded systems? Why is it necessary to upgrade DSC to the dsPIC33A series?
There are four key market trends in embedded systems that we see as driving the need for high-performance microcontrollers: increasing energy efficiency requirements, the need for multifunctionality in controllers, escalating requirements for security and safety as well as the growing complexity of software, driven by the adoption of more sophisticated ecosystems and a rising demand for model-based design approaches. These trends underscore the market’s call for microcontrollers with superior performance, a demand that has partly influenced the development of our new 32-bit dsPIC33A DSCs.
There are four market trends in embedded systems that we see are driving the need for high-performance microcontrollers. In some ways, these trends led us to upgrade our Digital Signal Controller (DSC) family to the new 32- bit dsPIC33A family of DSCs.
The first trend is increasing energy efficiency requirements. There is a universal push among our clients, regardless of their focus area—be it motor control, power supply or other systems—to enhance efficiency. This drive is motivated by the need to comply with industry standards and governmental regulations, prompting the use of superior hardware and complex algorithms to optimize system performance. Due to increased complexity in the system in terms of hardware as well as firmware, there is an increased demand for microcontrollers with higher performance capabilities.
Secondly, we have observed a trend towards multifunctionality in controllers or one controller performing multiple tasks. A notable example is within the automotive sector, specifically in thermal management systems where a single controller manages various components such as pumps, cooling fans, compressors and other actuators. This integration facilitates more sophisticated control loops and optimized system-level architectures, leading to demands for more integrated peripherals. The benefits include reduced board space and overall system cost savings, while also driving the need for higher performance and faster peripherals.
The third trend is the escalating requirement for security and safety across various sectors, including automotive, industrial, data center, consumer, aerospace and defense. To safeguard systems, there is a necessity for microcontrollers to incorporate dedicated security features, additional memory and enhanced performance. This is to accommodate the security libraries on top of the existing microcontroller functions, further increasing the demand for high-performance solutions.
Lastly, the growing complexity of software is driven by the adoption of more sophisticated ecosystems and a rising demand for model-based design approaches. These advancements assist our customers in streamlining and expediting their development processes. However, they also necessitate more complex systems which, in turn, push the boundaries of memory capacity and performance metrics.
In summary, these four trends collectively underscore the market’s call for microcontrollers with superior performance, a demand that has partly influenced the development of our new 32-bit dsPIC33A DSCs.
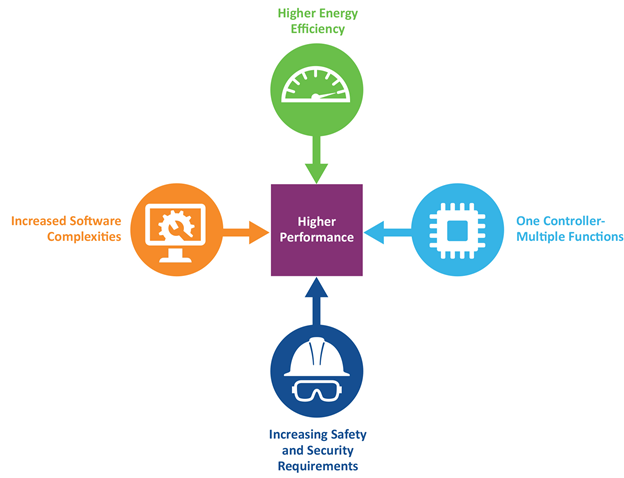
2. Could you provide a detailed analysis of the main features and advantages of the dsPIC33A series as compared to its predecessor and similar products?
The dsPIC33A series represents a significant advancement over its predecessors and similar products, featuring a 32-bit architecture operating at 200 MHz, which is a substantial upgrade from the previous 16-bit architecture. This enhancement, along with the Double Precision Floating Point Unit (DP-FPU) compliant with IEEE 754-2019, facilitates precise calculations, faster processing loops and seamless integration of third-party tools. Enhanced DSP and CPU performance is achieved through two 72-bit accumulators, 32-bit working registers and additional context switching registers, reducing latency and improving real-time application performance. Improved peripherals include ADCs with up to 40 MSPS conversion rates, 100 MHz GBW Op-Amps, faster comparators and a new BiSS interface for secure, high-speed serial communication. Security features such as secure boot, ECC for RAM and Flash, ICSP write inhibit and secure debug further enhance system reliability. Overall, the dsPIC33A series offers significant improvements in processing power, precision, peripheral performance, and security, making it a highly competitive option for high-performance and reliable applications.
The dsPIC33A series represents a significant advancement over its predecessors and similar products in several key areas:
- 32-bit Architecture: The dsPIC33A series features a 32-bit architecture operating at 200 MHz, which is a substantial upgrade from the previous 16-bit architecture. This enhancement is particularly beneficial for applications in digital power, robust design and motor control. The 32-bit architecture with Double Precision Floating Point Unit (DP-FPU) facilitates model-based designs and the seamless integration of third-party tools, which often favor a 32-bit architecture and double precision for their ability to minimize variable scaling, reduce error potential and expedite the development process.
- Double Precision Floating Point Unit (DP-FPU): The integration of a DP-FPU compliant with the IEEE 754-2019 standard allows for more precise calculations and faster processing loops, especially in control algorithms. This reduces the risk of software errors associated with variable scaling and enhances the overall reliability of the system.
- Enhanced DSP and CPU Performance: dsPIC33A DSCs now include two 72-bit accumulators which provide high resolution and accuracy, minimizing the risk of overflows or underflows. The 32-bit working registers which further enhance performance and resolution, reducing the need for variable scaling. Additional context switching registers reduce the overhead during interrupts, decreasing latency, which is crucial for real-time applications.
- Improved and New Peripherals: There is a significant improvement in peripherals for dsPIC33A DSCs compared to previous generations of DSCs or similar parts. The main improvements include:
- Analog-to-Digital Converters (ADCs): The ADCs can now do conversion at up to 40 MSPS, significantly reducing conversion latency and improving control loop performance.
- Operational Amplifiers (Op-Amps): A 100 MHz gain-bandwidth product (GBW) with low offset and user-adjustable calibration, enhances measurement precision. The previous generation’s GBW is 20 MHz.
- Comparators: The comparators have lower response time (5 ns) in dsPIC33A DSCs compared to previous generations due to the higher frequencies of clocking.
- Bidirectional Synchronous Serial Interface (BiSS): This new peripheral supports secure, high-speed serial communication between controller, encoder, sensor and actuator, accommodating up to 4 clients with 64-bit sensor data lengths and operating at speeds up to 10 MHz using RS485/422 interface.
- Security Features: The dsPIC33A series includes secure boot, Error-Correcting Code (ECC) for RAM and Flash memory, In-Circuit Serial Programming (ICSP) write inhibit, secure debug, Immutable Root of Trust and other security functions to help secure systems from various threats.
In summary, the dsPIC33A series offers significant improvements in processing power, precision, peripheral performance and security features, making it a highly competitive option for applications requiring high performance and reliability.
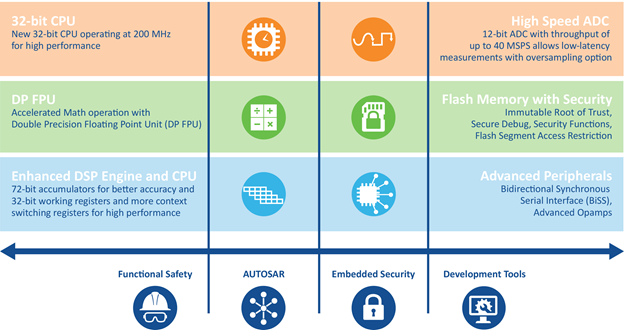
3. What are the benefits of using the dsPIC33A series in the motor control field? How does it enhance product performance? Could you share some case studies?
The dsPIC33A series of Digital Signal Controllers (DSCs) is widely used in motor control applications due to its high-performance digital signal processing capabilities and microcontroller features. Key benefits include high-performance processing with a 32-bit architecture and DSP engine for complex algorithms like field-oriented control (FOC), enhanced by a Double Precision Floating Point Unit (DP-FPU) for accuracy and control loop performance. Integrated peripherals such as high-resolution PWM modules, high-speed ADCs and Quadrature Encoder Interfaces (QEIs) are essential for precise motor control. Real-time control capabilities ensure precise motor speed, torque and position management, which are crucial for robotics, industrial automation and electric vehicles. The series offers scalability in memory, processing power and peripherals allowing designers to tailor solutions to their specific needs. Extensive software libraries and development tools from Microchip reduce development time and time-to-market, while the ability to implement various control algorithms on the same hardware platform provides design flexibility. Additionally, integrating multiple functions into a single chip makes the dsPIC33A series cost-effective compared to using separate microcontrollers and DSPs.
The dsPIC33A series of Digital Signal Controllers (DSCs) are widely used in motor control applications due to the combination of high-performance digital signal processing capabilities and microcontroller features.
Here are some key benefits and ways it enhances product performance:
- High-Performance Processing: The dsPIC33A series, featuring a 32-bit architecture and high-speed DSP engine, efficiently executes complex motor control algorithms like field-oriented control (FOC). The Double Precision Floating Point Unit (DP-FPU) enhances accuracy, control loop performance and handling of nonlinearities. Additionally, it supports model-based designs and seamless integration of third-party tools, accelerating development.
- Integrated Peripherals: These controllers come with specialized peripherals such as high-resolution Pulse Width Modulation (PWM) modules, high speed Analog-to-Digital Converters (ADCs) and Quadrature Encoder Interfaces (QEIs), and now the BiSS interface which are essential for precise motor control.
- Real-Time Control: The real-time control capabilities of the dsPIC33A series allow for precise and responsive control of motor speed, torque and position, which is critical in applications like robotics, industrial automation and electric vehicles.
- Scalability: The dsPIC33A series provides a range of options in terms of memory, processing power and peripheral sets, allowing designers to scale their solutions according to specific application requirements.
- Flexibility and Reduced Development Time: With extensive software libraries and development tools provided by Microchip, engineers can quickly develop and deploy motor control solutions and reduce their time-to-market. The ability to implement various control algorithms (e.g., Field-Oriented Control, Sensorless Control) on the same hardware platform provides flexibility in design and application.
- Cost-Effectiveness: By integrating multiple functions into a single chip, the dsPIC33A series can reduce the overall system cost compared to using separate microcontrollers and DSPs.
4. I’ve noticed many outdoor power supplies still use MCU and DSP chips with a main frequency of around 100 MHz. Will higher-frequency DSCs become a trend in the digital power sector? How do they contribute to digital power conversion in applications such as AI servers and automotive chargers?
For several power supply applications, DSCs operating up to 100 MHz, such as the dsPIC33CK (single-core) and dsPIC33CH (dual-core), suffice for current requirements. However, advanced applications like AI servers and automotive chargers demand more efficient and precise power management, driving the need for higher performance DSCs. The dsPIC33A DSC, with its higher clock speed, addresses these needs by offering enhanced performance and efficiency, crucial for sophisticated algorithms and rapid response times. It supports advanced control algorithms, improved monitoring and diagnostics and increased security through cryptographic measures. Thus, the dsPIC33A DSC significantly advances digital power conversion, meeting the evolving demands of AI and automotive sectors.
Many power supply applications, such as those for data centers, can fulfill current requirements with DSCs operating up to 100 MHz. For customers who do not require enhanced performance, our 4th generation DSC family, including the dsPIC33CK (single-core) and dsPIC33CH (dual-core), will continue to meet their needs.
Advanced applications like AI servers and automotive chargers demand more efficient and precise power management and have ever evolving security and functional safety requirements. These factors are driving the need for higher performance DSCs, which translates to DSCs with more powerful a CPU operating at higher clock speeds. Some of the key factors driving the need for higher performance MCUs are as follows.
- Performance and Efficiency: Higher-frequency DSCs like the dsPIC33A can process more instructions per second, allowing for more sophisticated algorithms and faster response times. This is crucial for applications requiring precise control and rapid adjustments, such as AI servers that need to manage fluctuating power demands efficiently and run complex algorithms for power factor correction, resonant converters and synchronous rectification, vital for data center efficiency.
- Advanced Control Algorithms: With higher processing power, DSCs can implement more complex control algorithms, such as predictive control and adaptive filtering. These algorithms can improve the efficiency and stability of power conversion, leading to better performance in dynamic environments.
- Improved Monitoring, Diagnostics: Enhanced processing capabilities enable better monitoring and diagnostic features, which are essential for maintaining reliability and efficiency in critical applications like AI servers and automotive chargers.
- Increasing Security: Securing data center and automotive power supply against spoofing and tampering is more critical now than ever before. By implementing firmware attestation and device authentication using cryptographic algorithms like asymmetric key pairs and hashes can help achieve security goals. However, these requirements will continue to drive the memory and performance requirements for DSCs and MCUs controlling these power supplies.
The dsPIC33A DSC will contribute significantly to the advancement of digital power conversion by providing better performance, efficiency and flexibility, which are essential for modern applications in AI and automotive sectors.
5. In terms of development tools, what design convenience does the dsPIC33A series bring to engineers?
At Microchip, we streamline the adoption of our solutions from evaluation to final design, accelerating development and mitigating early-stage design risks with expert support. Our ecosystem includes evaluation boards for the dsPIC33A series, an optimized MPLAB® XC-DSC C compiler, demo codes for various applications, future support for model-based design and advanced algorithms for motor control, digital power conversion as well as other real-time control applications such as sensor interfacing applications. We also plan to offer comprehensive functional safety and security support for dsPIC33A, including documentation, diagnostic software libraries and reports. For more details, visit www.microchip.com/dsPIC33A.
At Microchip, we streamline the adoption of our solutions from evaluation to final design. Our ecosystem accelerates development and mitigates early-stage design risks with support from our expert engineers. The ecosystem includes:
- Evaluation Boards: Supports dsPIC33A series with development boards for general purpose, motor control and digital power conversion, along with matching dual inline modules with the dsPIC33A DSC.
- Software Tools: The MPLAB® XC-DSC C compiler optimizes ANSI C programs into DSC assembly language.
- Application Firmware: Demo codes for development boards in general purpose, motor control and digital power conversion. Future support will include model-based design with MATLAB® and enhanced Motor Control and DSP algorithms.
- Ecosystem: We are also preparing to offer comprehensive support for functional safety and security for dsPIC33A just like our previous generation dsPIC33C DSCs and will be supporting customers with a functional safety package comprising of documentation, diagnostic software libraries and associated reports.

6. With industrial control MCUs now reaching frequencies of 600 MHz+, and Microchip recently launching a 64-bit MPU, the performance of MCUs in applications such as industrial, digital power and sensor systems is continuously improving. Could you outline the future development path for DSC products?
MCU performance requirements for industrial automation, digital power conversion, sensor interfacing and automotive applications are continuously increasing. Over the past couple of decades, we have evolved the dsPIC33 DSC family to meet these needs. The dsPIC33A DSCs, our fifth generation, showcase significant advancements.
From the first generation dsPIC30F with a 30 MHz CPU to the fourth generation dsPIC33C with a 100 MHz CPU, we have consistently improved. We have added functional safety features and expanded flash memory up to one megabyte, even in our smallest 4×4 package devices.
The fifth generation dsPIC33A DSCs feature a 32-bit CPU operating at 200 MHz, a double-precision floating-point unit, and enhanced analog peripherals and security features. We will continue to evolve this product family with higher memory options, advanced application-specific peripherals, and enhanced security and functional safety features to meet evolving requirements.