Power supplies for installation in control cabinets of automation plants are exposed to much greater stress than those used in offices and homes. In addition, such production plants are often running round the clock for many years. Unplanned production downtimes result in huge costs and loss of earning. It therefore comes as no surprise that the automation industry demands power supplies that come with an extended warranty while being still affordable.
If the power supply of a desktop computer fails after 3 or 4 years, we might not be particularly happy about it, but often just decide to upgrade to a newer model. The failure of a power supply in a control system of an industrial plant is however a much more serious issue. These devices need to be much more robust and reliable, while being exposed to much greater stress. They are normally neatly installed side by side with relays, contactors, distribution blocks and circuit breakers on a top hat rail in an air-tight control cabinet. These cabinets can however become quite warm, and the electronic components are more or less constantly exposed to voltage surges, current peaks and electromagnetic interference. All these factors must be taken into account by automation designers and operators. When sourcing DIN rail power supplies, their top concern is thus reliability.
Can reliability be quantified?
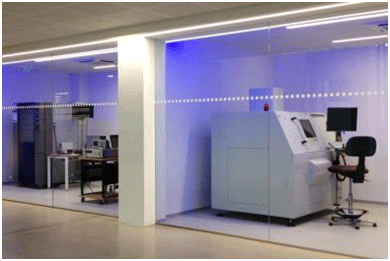
The answer is yes and no. Some technicians believe that MTBF, or mean time between failure, covers it all. This is however a theoretical value calculated on the basis of standard characteristics of the components used in the device. At best, MTBF is only a rough indicator of the quality of a device, predicting the time between inherent failures. Engineers designing systems would however rather prevent the first failure altogether.
A more practical indicator is the design lifetime determined by means of HALT tests (Highly Accelerated Life Tests). In HALT tests, devices are exposed to vibration, extreme humidity and fast temperature cycling, at levels that are significantly beyond those expected during normal operation. These tests are generally performed during the prototyping phase in order to identify and eliminate weaknesses in the design. By testing a limited number of serial products, it is possible to achieve fairly reliable figures as regards the average service life of a model. Such tests are however not yet common practice in the industry, and only a few manufacturer actually publish the results.
To enhance the design lifetime of its products, RECOM is operating its own environmental lab where new designs are tested and evaluated from the very first phase of development. Weaknesses detected in these tests can thus be eliminated long before a model enters serial production. For some LED drivers, the design lifetime is specified as 70,000 hours. The new DIN rail power supplies from RECOM to be launched at the electronica in Munich come with even longer design lifetimes. Reliable figures based on production device tests will be available in a few months’ time.
Enhancing reliability
The key factors determining the design lifetime of a power supply are actually few: they are the electrolytic capacitor, the ferrite cores of transformers and chokes, external voltage and electromagnetic fields. Capacitors and ferrite cores are susceptible to temperature fluctuations. Over time, electrolyte evaporates from the capacitors, and the higher the ambient temperature, the faster the evaporation rate. High temperatures have a similarly detrimental effect on ferrite material, as their performance deteriorates, resulting in further overheating, leading eventually to complete failure.
DIN rail power supplies are normally installed in control cabinets that are sealed to prevent damage to the components from dust or dirt. As such enclosed units are difficult to cool, the temperature inside a cabinet is generally quite high. Given that power supplies also generate some heat, the elevated ambient temperature plays a critical role and must be taken into account in the design of the component. How can the issue of reliability of power supplies be best tackled?
When designing the innovative REDIN series, the RECOM development team focussed primarily on implementing adequate safety margins. In a first step, the engineers determined the size of the housing, based on extensive thermal simulation tests. Small housings tend to cause serious problems as regards heat management. When assembling electronic components with small housings in the control cabinet, technicians need to ensure that the individual modules are not installed too close to each other and well away from other heat sources. Given the confined space and top rail mounting system, this is obviously not always possible. Small housings also prevent adequate heat transfer within the module, leading to temperature imbalance. Apart from developing the electronic design of the module, engineers therefore need to optimise the thermal design of the device. In reality, this is a Sisyphean challenge. Every extra millimetre between hot spots and to the capacitors has a negative effect on the efficiency of the component, or might result in an “aerial” picking up additional interference. In addition, there is the issue of electromagnetic compatibility, which can best be overcome with short distances between filters and switching transistors. To tackle these problems, engineers need an in-depth knowledge of analogue technology, as they must find a compromise considering all these factors.
No compromise when choosing components – RECOM follows the adage of “simply the best”! In products where electrolytic capacitors cannot be replaced with larger capacitors, we use the more expensive longlife model approved for ambient temperatures up to +105°C. The same applies to ferrite cores in transformers and chokes where we have opted for high temperature grade material designed for even higher temperature ranges.
Top grades across the board
With a development time of over twelve months, RECOM has invested more time in its new DIN rail series than in any other of its products. And the results are impressive. The new range of power supplies achieves top grades in virtually all areas.
The new models will initially be available for 45W (REDIN45) and 60W (REDIN60) with outputs of 12 or 24VDC. We believe that these two models will cover around 50% of the most common applications. Additional models are in currently in the pipeline.
With a width of 41mm, the modules are quite compact. As they can be installed side by side without the need for gaps, they are optimised for installation in control cabinets where space is at a premium. This is made possible by first-class thermal management inside the module housing and the excellent efficiency of the units of up to 87%. In control cabinets of limited depth, the modules can be installed at an angle. While not a requirement for industrial applications, the no-load power is <500mW and thus conforms to the EU Ecodesign Directive. The modules can be upgraded at any time with voltage-free relay contacts for a “Power Good” signal. This signal can be used to control an operating panel on the control cabinet door or sent to a PLC for error signalling. It is also possible to connect the contacts of several modules in series in order to generate general “OK/NOK” signals. For more information, see text box “Technical data”.
7-year “Fit & Forget” warranty
The models of the new REDIN range of power supplies will not be among the cheapest – but definitely among the best. Their design lifetime will be well above 10 years. It is therefore only logical that they come with a comprehensive 7-year manufacturer warranty. We call it “Fit & Forget”, as that is what we want our customers to do! The new modules will be launched at the electronica in Munich at our stand in hall B2/311. They are now available from DigiKey and other reputable suppliers.