Courtesy: Littelfuse
1 Test Geartooth Sensing using 55075 device
The best ferrous targets are made of cold-rolled low carbon steel. Sintered-metal targets are also usable, although care must be taken to ensure uniform material composition and density,
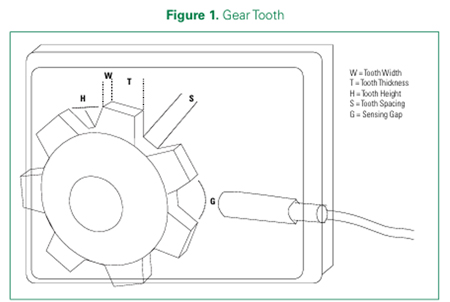
The Littelfuse device is a self-adjusting digital output geartooth speed sensor. The sensing distance between the sensor and a geartooth is influenced many factors including the gear teeth dimensions, the grade of ferrous metal of the gear and alignment of sensor to gear. Typically, larger teeth and slots allow a larger sensing air gap. For best performance, the sensor should be located as close as possible to the target. Optimally this gap should be less than 1 mm. The sensor may sense up to 2mm depending on your gear geometry.
General gear guideline should consider the following as an example:
W = 4mm S = 5mm
T = 6mm G = 1.5mm typical
H = 4mm
For gears with smaller tooth dimensions the sensing gap would be typically 0.5 to 1.0mm. It is best to evaluate a sensor against your specific gear prior to final selection.
The teeth or slots of the target should be cut with a slight angle so as to minimise the abruptness of transition from metal to air as the target passes by the sensor. Typical air gaps for Littelfuse geartooth Sensors are between 1-1.5 mm. Littelfuse 55075 includes an internal pull up resistor for the sinking output.
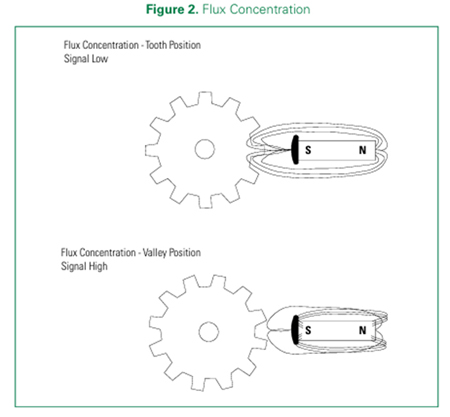
The need to sense speed and position of ferrous gears occurs in many industries. The ability to convert the repetitive passing teeth to an electrical impulse has been sought for many decades. Purely mechanical systems have been used with the attendant issue of wear and failure limiting its use to low speed and low duty cycle applications. Hall effect geartooth sensing makes use of the Hall element to sense the variation in flux found in the air gap between a magnet and passing ferrous geartooth. By digitally processing the Hall signal, several advantages are obtained. Peak detection, peak hold, and level comparison are all done digitally. The maximum and minimum Hall signal that corresponds to the last geartooth and valley is then remembered indefinitely without the drift associated with analog techniques. The level comparison then adapts to the last peak. This creates true zero speed adaptive speed sensor. It is immune to orientation requirements and can follow the gear speed down to the cessation of motion. It will detect the first edge of the next tooth immediately after power on. The digital signal processing does introduce an uncertainty from quantization that is greater at larger speeds. Extremely demanding timing requirements like those found in crank position sensors may suffer from the loss of accuracy at high speeds.
In order to detect the passing gear teeth with a Hall effect sensor, it is necessary to provide a source of magnetic energy. One simple way to do this is to arrange a permanent magnet such that the axis of magnetization is pointing toward the surface of the gear teeth. As a tooth moves across the surface of the magnet the flux will become attracted to the lower reluctance path provided by the ferrous steel structure.
When this occurs the flux density measured by the Hall element between the face of the sensor and the geartooth increases. Many schemes have been developed and some patented that use the various attributes of the vector flux field and its changing nature to create zero speed Hall effect geartooth sensors. Geartooth Specifications:
2 3-Wire Hall Sensors: 55100, 55140
These sensors utilize CMOS technology and consist of a Hall plate, active stabilization circuitry, a comparator, and an open drain output.
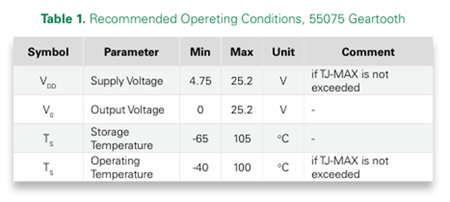
Outputs are active low sinking- an external pull-up resistor is needed for most applications. The supply voltage and pull-up voltage need not be the same voltage. Any pull-up voltage from 0V to 24V nominal may be used. The pull-up resistor value is limited only by the maximum output leakage current over temperature of 10uA and the maximum recommended output current of 20mA.
The polarity of the magnet is very important for Hall sensors. “Switch Type” Hall sensors are activated by the South Pole. The proper magnet pole should be presented to the activation face of the sensor (see the sensor Datasheet for Activation Detail).
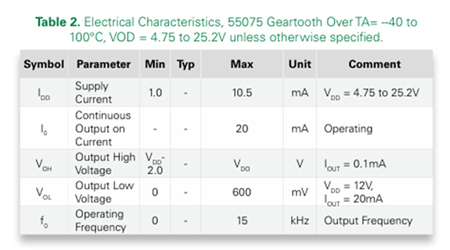
This family of sensors utilizes chopper stabilization. This feature provides nearly constant magnetic characteristics over variations in supply voltage, temperature, and mechanical stress. In order to implement this technology, an internal oscillator switches amplifier circuitry between sampling a reference and sampling the active magnetic sensor. The period of the oscillation is called TOSC and is a few microseconds (see specification). The sensor’s digital output may be delayed by up to this amount. This very small delay is inconsequential in most applications and is far outweighed by the stability provided by the chopper circuitry.
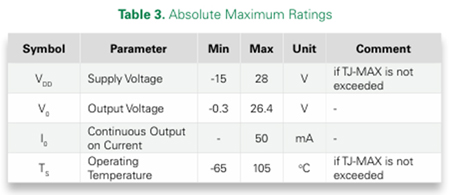
Electrical Characteristics, 55100 3-wire, 55140 3-wire (Note 2) Over TA = -40 to 90°C, VDD = 3.8 to 24.0V unless otherwise specified
3 Analog Hall Sensor: 55100-AP, 55140-AP
Analog Hall sensors are semiconductor devices that use the Hall effect to measure magnetic fields. They are often implemented using CMOS technology, which allows for programmability and customization of various sensor parameters. Some key features and characteristics of these sensors are as follows:
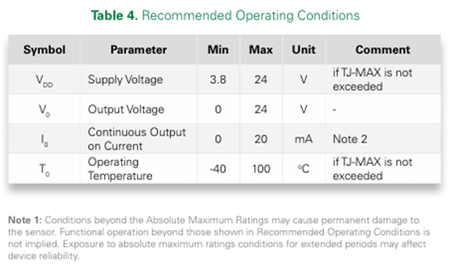
1) Customer Preset: Analog Hall sensors can be preset to a specific output voltage corresponding to a particular magnetic field strength (measured in gauss). This allows the sensor to be tailored to the specific requirements of the application.
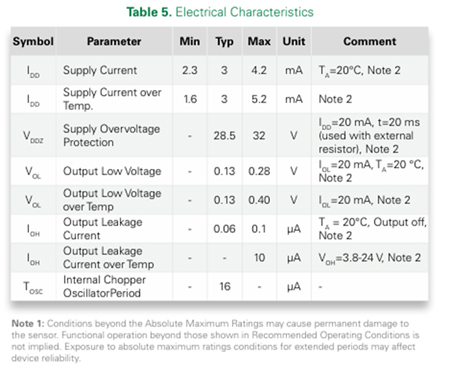
2) Programmability: The sensor electronics are programmable, enabling customization of different parameters, such as magnetic field range, sensitivity, output voltage range, and temperature coefficients. This flexibility makes the sensors suitable for a wide range of applications.
3) Ratiometric Output: The output voltage of the sensor is referenced to the supply voltage. This means that the output value is proportional to the magnetic field strength relative to the supply voltage. Ratiometric outputs provide a stable and accurate measurement even when the supply voltage fluctuates.
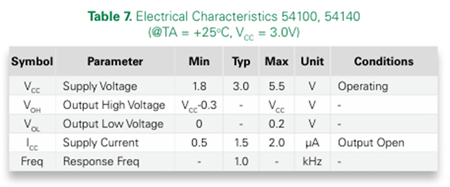
4) Fault Tolerance: The sensor is designed to handle different fault conditions, such as power supply open-circuit, ground open-circuit, or power supply over/undervoltage to ground or supply voltage. This ensures reliable operation even in challenging scenarios.
5) Total Error: The sensor’s total error, which includes all sources of inaccuracies, is specified to be less than 2% over the entire operating voltage and temperature range. This level of accuracy makes the sensor suitable for precise measurement applications.
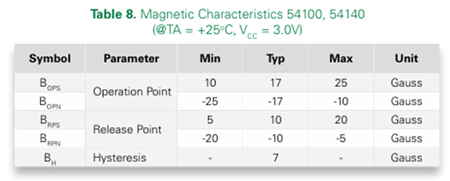
Overall, analog Hall sensors utilizing CMOS technology offer a versatile and reliable solution for measuring magnetic fields across various industries and applications, including automotive, industrial, and consumer electronics.
The standard programming of the AP series Analog Hall Sensor has a preset voltage output of 2.5 Vdc and declines to approximately 0 Vdc as the magnetic field strength increases (magnet pole approaches the senor face). Customization is accomplished using a Programming Interface and Dedicated Programming Software.
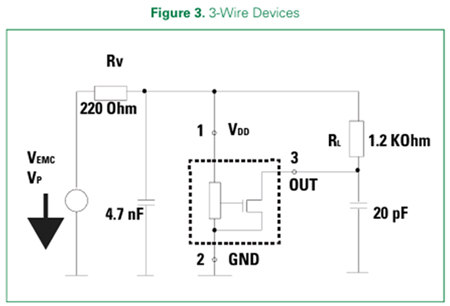
4 3-Wire TMR Sensors 54100, 54140
These TMR (Tunneling Magneto Resistance) sensors utilize CMOS technology which consist of a TMR sensing element, band gap regulator, a comparator and a Push/Pull output.
Outputs are active low sinking and active high sourcing. The maximum recommended output current is 6 mA.
The Omnipolar sensors require either a North or a South magnetic pole to operate. The sensor is activated (output sinking to ground) by the either pole once the BOP threshold is exceeded and deactivated (output sourcing to Vcc) when the BRP threshold is crossed. The magnet pole should be presented to the side of the sensor opposite the wired side.
5 Custom Design Sensors
Littelfuse specializes in meeting our customers specific requirements. Littelfuse offers full service Engineering capability in-house.
6 EMC and ESD
For applications with disturbances on the supply line or radiated disturbances, a series resistor and a capacitor are recommended. The series resistor and the capacitor should be placed as closely as possible to the sensor. Applications with this arrangement passed the EMC tests according to the product standards DIN 40839.
7 Overvoltage Protection except 55075
Absolute maximum rating for a continuous supply is 24 V. If the supply voltage exceeds the Zener voltage of 28 V, the current consumption of the devices increases. Voltages above the Zener voltage can be tolerated only for short time. In order to protect the Hall sensor against overvoltage, an external series resistor is required. The voltage drop at this series resistor increases with increasing supply current. A Zener diode in combination with a (external) series resistor acts as clamping device, limiting the supply voltage of the device to the Zener voltage.
8 Reverse Voltage Protection except 55075
The maximum reverse voltage is -15 V. As an example, if the device is used with an automobile 12 V supply, it may be connected incorrectly without damage. As with overvoltage protection, with external components this value can be increased. Please consult Littelfuse for details.
9 Temperature, Voltage and Power
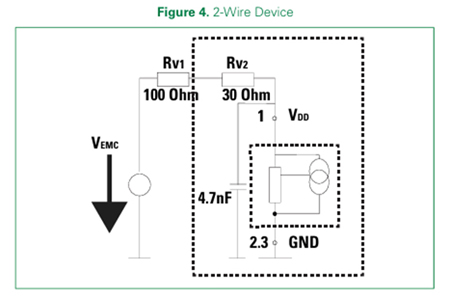
Like all solid-state semiconductor devices, Hall and TMR sensors have a maximum operating junction temperature. The operating junction temperature is determined by the power (voltage times current) that the sensor is dissipating, the thermal resistance of the package, any heat-sinking effects resulting from mounting configuration, any air movement, and ambient (air) temperature. Because of the internal power dissipation and self-heating, the maximum operating temperature may need to be reduced at higher supply voltages in order to limit the junction temperature to an acceptable value.
10 ESD Precautions
Littelfuse semiconductor products are sensitive to Electro Static Discharge (ESD). Always follow ESD control procedures whenever handling our Hall Effect Sensors