Deposit Materials During Precision Manufacturing Processes
Uniform film coating changes surface characteristics of the substrate
The PD Series for plasma deposition uses a gas vapor or heated liquid monomer vapor delivery system to deposit coatings that can reduce, and in certain cases eliminate, tackiness, provide a tie layer, make surfaces more slippery or resistant to corrosion, act as a drug enhancement or inhibition agent in life sciences applications, and change desired surfaces from hydrophobic to hydrophilic or vice versa. Polymers can be directly attached to a desired surface while the chains are growing, which reduces the steps necessary for other coating processes such as grafting. This is very useful for pinhole-free coatings of 100 picometers to 1 micrometer thickness with solvent insoluble polymers.
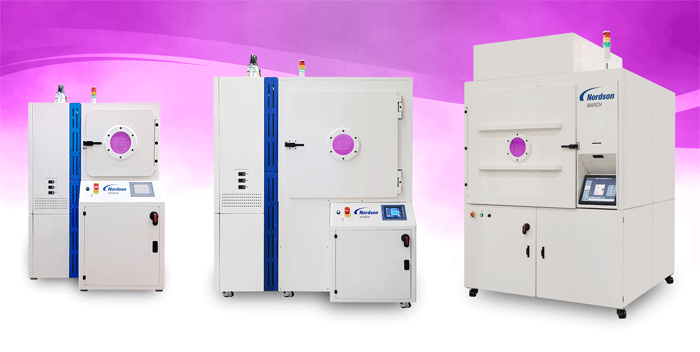
- Low temperature processing because plasma energy is the catalyst for film growth.
- Plasma deposition is uniform and applies coatings evenly over curved or varied-level surfaces.
- Precise control of film thickness.
- Eliminates wet chemistry. Because polymers are deposited directly from the monomer, there are no waste streams due to wet chemical synthesis or solvents.
- Exhibits similar properties to those created via standard chemical polymerization techniques.
- Can be used in multiple steps during device manufacture: pre-treat the surface, deposit material, and apply functionalized polymer films.
Three models are available to meet a broad spectrum of manufacturing requirements. The PD-1000 and PD-1500 are ideal for batch prototype, pilot, or production processing of substrates. The PD-Pro has a large plasma processing cavity to treat big substrates or multiple smaller substrates.
For more information contact Nordson MARCH at info@nordsonmarch.com, call +1.925.827.1240, or visit our website at www.nordsonmarch.com.