– Rapid prototyping solution in response to eyewear designers’ need for a more efficient process, offering a unique combination of stiffness and flexibility, essential for eyewear makers’ prototyping requirements
– Addition of Agilus30 rubber-like material and Digital ABS Plus engineering-grade material increases versatility of the Stratasys J750 full-color, multi-material 3D printing solution
HONG KONG, Sept. 28, 2017 /PRNewswire/ — From initial design concept to display on the store shelf, a new eyeglass-frame design takes about 18 months, using traditional development techniques, according to Stratasys eyewear customers. Large eyewear manufacturers may create up to 150 new frame designs weekly (or thousands of new frames per year). Imagine cutting up to 15 months from the development and production cycle of every frame and shrinking time-to-market to eight weeks or less.
That’s what’s possible, say pioneering companies that tested a new eyewear rapid prototyping solution introduced from Stratasys (Nasdaq:SSYS), a global leader in applied additive technology solutions. Stratasys developed the VeroFlex Rapid Prototyping Eyewear Solution to help manufacturers dramatically improve time-to-market and cost-efficiency.
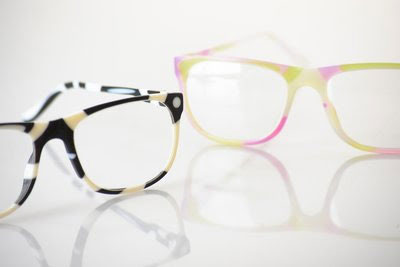
The Stratasys VeroFlex Rapid Prototyping Eyewear Solution
The new solution combines Stratasys’ unique J750 Multi-color, Multi-material 3D Printer with, VeroFlex, a new specially formulated 3D printing material for eyewear rapid prototyping needs. VeroFlex offers a unique combination of stiffness and flexibility, essential for a wide range of prototyping requirements. From initial concept iterations to complex multi-color and advanced texture models, to precise functional models for performance testing, VeroFlex offers a more durable and flexible material for demanding internal tests prior to tooling and production. This provides eyewear manufacturers the ability to deliver products over a year faster and lead with the latest market trends, while improving salability of its products.
“The eyewear market continues to expand, driven by new technologies, demand for customization and growing addressable markets,” says Mike Vasquez, founder and CEO at the digital manufacturing consultancy, 3Degrees. “As the industry seeks to maximize its opportunity, Stratasys’ prototyping solutions for frames and eyewear accessories — which can cut time-to-market by upwards of 80 percent — will be an attractive solution that is able to deliver immediate value for users looking to make parts with a high degree of mechanical function and appearance.”
For functional performance testing, the Stratasys VeroFlex material stands up to key eyewear-maker evaluation, including drop tests, lens-mounting, stress tests and wearability tests. When used for design verification, the Stratasys VeroFlex material offers ultimate realism enabled by combining six new VeroFlex materials (Cyan, Magenta, Yellow, White, Black, and Clear), and the ability to create and mix solid, opaque, transparent and color shades in addition to simulating true-to-life textures such as wood grains, leather, stitching, bone, carbon-fiber, and photo-realistic images.
For more information, visit the Stratasys VeroFlex Rapid Prototyping Eyewear Solution webpage.