In this exclusive conversation with Rashmi Gopala Rao, Principal, Automotive Industry and Vijayalayan R, Senior Manager, Application Engineering – Automotive Industry, MathWorks India talks about the electrification trends and discusses how MathWorks accelerates the pace of simulation for EV development.
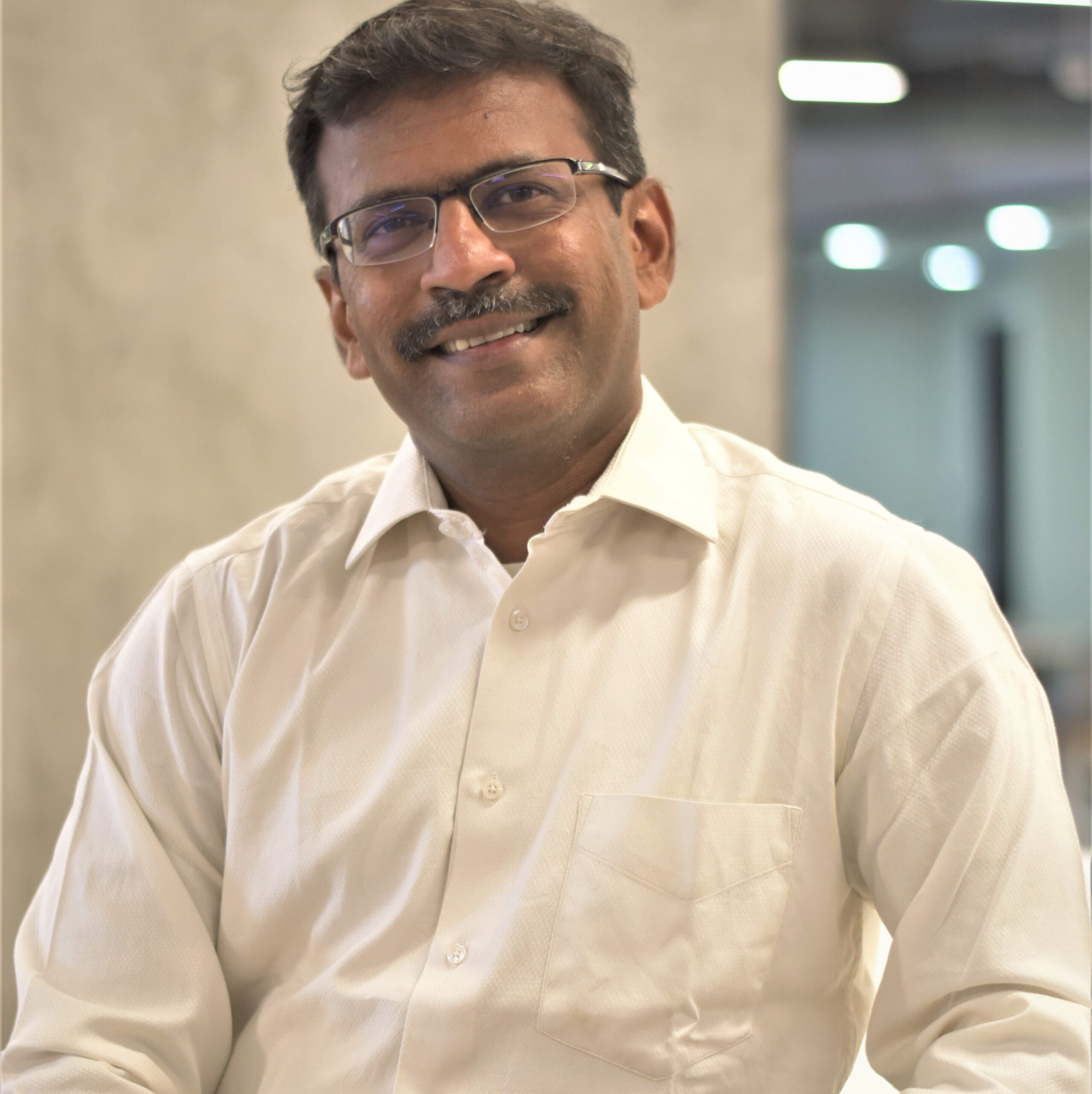
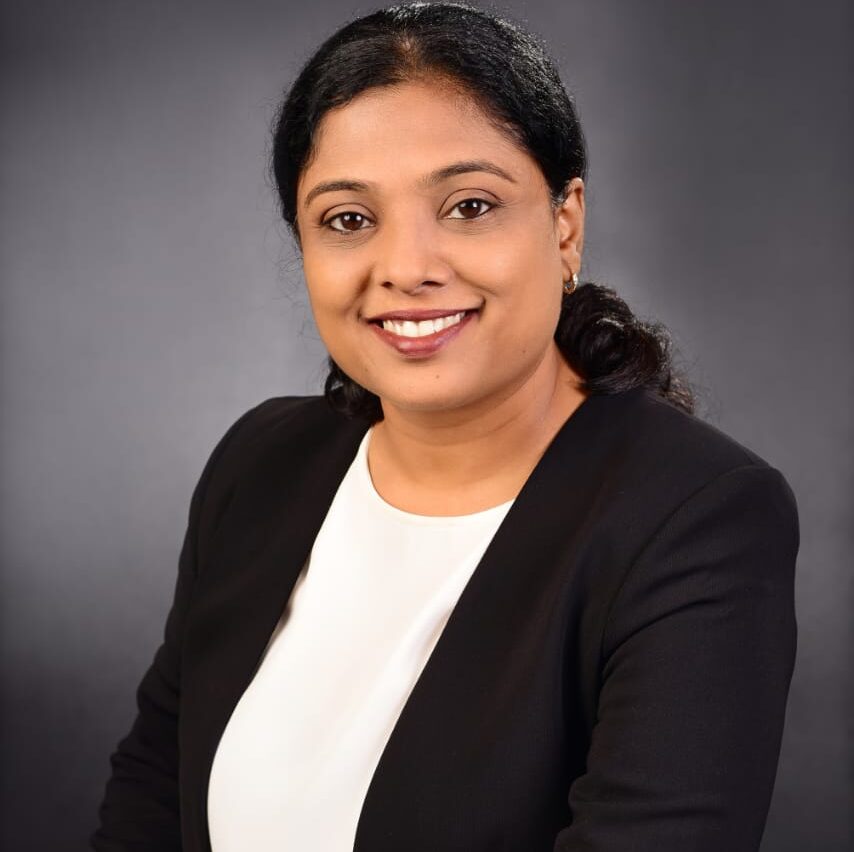
Q1. What are some upcoming electrification trends, and what have been your expectations with the rise of the EV market?
As India and other governments set deadlines for carbon net neutrality, the automotive sector is also adopting increased electrification to meet stringent emission targets. In this background, we observe several key trends in the industry:
OEMs redefining the powertrain mix: Many OEMs in the passenger car segment have announced roadmaps to introduce EVs or completely electrify their fleets. They are setting up manufacturing, selecting vendors, and establishing toolchains and processes to electrify their drivetrain. While complete electrification is on the horizon, we know that traditional internal combustion engines (ICE) will also be in the market for the foreseeable future. Today, OEMs define their desired powertrain mix so they can invest in EVs while hedging with ICE and hybrids. The commercial vehicle segment is exploring fuel cell or hydrogen engines. The two-wheel segment is experiencing a transition to battery-powered motors. No matter which segments we look at, automotive OEMs are gearing up for a change.
Battery Technology: The battery pack is the heart of the EV and contributes significantly to the performance and cost of EVs. There is significant work involved in reducing battery costs and increasing efficiency.
Building up the charging infrastructure: Along with OEMs and Tier-1s we are also seeing infrastructure providers and grid companies prepare for this change.
Changing value chains: The traditional gasoline or diesel engines were complex, and there was an established hierarchy of OEM -Tier1 – Tier2 and so on in the Auto Industry. However, the EV powertrain is much simpler – just the Battery, Inverter, and Motor. This is lowering the barrier for OEMs, and they aspire for more in-house development. This is also an opportunity for Tier 2 and semiconductor players to rise in the value chains.
Skilling and Reskilling: As organizations are investing in manufacturing and supply chains they also must invest in people. We are seeing a need for skilling and reskilling driven by OEMs to let them take on the challenges of designing, implementing, validating, and producing EVs. We are seeing partnerships between Industry and Academia emerge so fresh engineers can have reduced ramp-up time. We are also seeing reskilling of ICE engineers so they can move to EV development of future models and a need for domain and tools skills in this area.
Increased software features to differentiate: OEMs are also planning software platforms and features where they can differentiate their offering. This includes infotainment and connectivity features. They are looking at recurring revenues from subscription and on-demand features. Like a cell phone, the vehicle can now be updated even after it has left the shop floor.
As MathWorks, we work with all players in the ecosystem: OEM, Tier-1, Tier-2, Semiconductors, Utility companies, and Infrastructure companies. Being in the business for 40 years, our investments in system simulation put us in a strong position to support engineers and scientists in this megatrend of electrification.
These are exciting times, and we are looking forward to partner to accelerate the pace of electrification.
Q2. How are Semiconductors enabling the Electric Vehicle Revolution?
Semiconductors are playing a critical role in enabling the electric vehicle revolution. Here are some ways in which they are contributing:
- Power Electronics: Semiconductors are used extensively in the power electronics systems of electric vehicles, such as motor inverters, and voltage step-up and step-down converters.
2. Battery Management Systems (BMS): Semiconductors are also critical components in battery management systems, which monitor and control the charging and discharging of the battery. BMSs use a combination of sensors, microcontrollers, and power electronics to optimize the performance and lifespan of the battery. As electric vehicle batteries become more complex, the demand for advanced BMSs is increasing, driving demand for semiconductors.
3. Motor Control Unit (MCU): Electric motors in electric vehicles require sophisticated control systems to ensure efficient operation and maximum performance. Semiconductors are used in motor control systems to manage the flow of current and voltage to the motor, allowing for precise control of speed and torque. This helps to optimize the performance of the motor and extend the range of the vehicle.
MathWorks enables customers by supporting the modelling and simulation of analog electronic components and digital control algorithms in the same simulation environment. Closed-loop simulation of the power stage and the controller lets our customers evaluate and verify design choices before implementing the controller.
As automotive industry moves to software defined vehicles, where the perceived value of the car will mainly come through software; semiconductor players are developing controllers, processors, and system on chips for increased compute that will be demanded from this trend. Semiconductor companies are collaborating closer with OEMs for design of chips and in some cases even providing software development environments on the cloud that is tailored to their HW offerings to enable development for Over the Air updates of software.
MathWorks is evolving with the Auto Industry to support emerging needs for development of a software defined vehicle such as newer architectures, cloud-based development workflows, solutions for digital twins that use cloud connectivity combined with AI and support for increased virtualization so that customers can frontload the development of their software defined vehicles.
Overall, semiconductors are enabling the electric vehicle revolution by providing the electronics and control systems necessary for efficient, high-performance electric vehicles. As electric vehicle technology continues to evolve and improve, the demand for semiconductors is likely to grow even further.
Q3. What is MathWorks’s projection for electrification adoption overall for India?
There are many aspects that will decide the adoption of EV such as government policy, infrastructure build-up, sources of energy to name a few. While it hard to predict an exact number, we have learnt through our work with OEM’s and Tier-1’s what are some of the drivers and challenges for EV adoption.
Interestingly some of the drivers for an EV are the quick pickup, the smooth drive and the total cost of ownership which is less than an ICE vehicle. The early adopters mainly run in the city with lower kms driven per day – so range anxiety is also lesser. Subsidies are also driving sales, especially in the 2W segment. Also, many of the new EV come with connected and infotainment features which is attractive to the younger demography of India.
Now, let us look at what are some of the challenges in EV adoption. While price continues to be a deterrent the major challenge today is not price but the range anxiety. There are also concerns about safety. Customers also are looking at charging availability. They are asking questions such as “How long will my battery last?”, “How does an EV depreciate?” to name a few.
Let us take the case of Range. MathWorks is working with OEMs and Tier-1’s in alleviating the challenge of range anxiety. Our customers can get full EV simulation with motors, invertors , and energy storage components using pre-built reference examples . They can perform analyses such as architecture trade off, motor and battery sizing, and control parameter optimizations. Simulations with our tools can also help to optimize the energy flow so OEMs can offer a better range without changing the hardware components. We are also investing in simulating the entire vehicle – called virtual vehicle that can combine engineering of powertrain, vehicle dynamics, environment, and driver behavior so OEMs and Tier-1 can simulate not just drivetrain but the entire vehicle and make optimizations.
Many of challenges perceived today can be alleviated through engineering. Simulation and modelling can be the backbone for that engineering – to make early decisions and effective designs.
Q4. What are the key steps needed to get charging infrastructure ready in places where EV take-up could be high and charging capacity could act as a constraint to sales?
Several steps need to be taken to ensure charging infrastructure is ready and charging capacity should not act as a constraint to sales. Some areas are in establishing the DC fast charging infrastructure, ensuring that the charging infrastructure is compatible with the charging standards used by different EV manufacturers, upgrading of grids to handle demand surges, identification of suitable locations for charging setup to name a few.
However, there are challenges to develop and test many of the above aspects. Let us take the communication protocol as an example; there are challenges here as the protocol is not uniform between vehicles and charging infrastructure- an area where MathWorks is working with OEMs. MathWorks is investing in simulating the digital communication, charging states, connection & disconnection, system faults, authentication modes, start-up/shutdown to frontload the development in this area.
Another area being explored is to understand whether the energy storage is sufficient for optimal charging? Or is there any specific software needed for optimal charging? Here again our tools are being used for concept evaluations such as where should the charging hubs in a city be, what kind of renewal sources are needed, upcoming concepts like vehicle to grid – to name a few.
For EV adoption to accelerate, OEMs and infrastructure companies must design and collaborate closely. MathWorks is uniquely positioned as we understand the challenges of both these industries and can provide a common platform capable of simulating communications, control, power electronics, and power systems to support the design, development, and validation of these interconnected systems.
Q5. Is India’s relatively hot climate not suited for batteries in electric vehicles (EVs) running on roads?
Battery fires occur due a condition called Thermal Runway. Batteries can experience thermal runaway where the chemical reactions accelerate as temperature rises, leading to an exponential increase in temperature and an explosion.
Thermal runaway can occur due to Overcharging from incompatibility between cell and charger, or poorly designed battery management system, multiple discharges followed by charge, external short circuit or poor cell assembly.
The need is to have a thermal management system with an effective control software so these thermal runaways can be avoided. However, there are several challenges to designing an efficient thermal management system.
This is an area where MathWorks is adding significant value by offering an environment that enables engineers to analyze the entire system at just the right level of fidelity and develop safety critical control software.
Our solutions can:
- Refine requirements for the cooling system, such as heat dissipation and power consumption.
- Explore cooling system architectures by drawing schematics to place pipes, valves, heat exchanger, and tanks.
- Model systems that use various working fluids, including gases, liquids, and refrigerants that change phase.
- Develop software for battery management systems that are ISO26262 compliant
- Reduce costs by performing less expensive, time-consuming hardware tests using modelling and simulation.
We need the right engineering design and validation to build robust EVs. Poor cell design, inadequate cooling systems, poor control software and insufficient validation can all be reasons for failures in safety – which cannot be compromised. Engaging with partners such as MathWorks can give organizations access to best-in-class tools and solutions so that safety is not a tradeoff.
Q6. How do you see the Battery management system market growth and key drivers?
As discussed in the previous question, maintaining the battery at an optimal temperature is a crucial engineering requirement for an electric vehicle. Keeping this in mind, the BMS market should see significant growth as EV adoption rises.
Let us understand what a BMS is and how it helps. The battery management system (BMS) is responsible for safe operation, performance, and battery life under diverse charge-discharge and environmental conditions. When designing a BMS, engineers develop feedback and supervisory control that does the main tasks:
Monitors cell voltage and temperature.
- Estimates state-of-charge and state-of-health of a battery.
- Limits power input and output for thermal and overcharge protection
- Controls the charging profile.
- Balances the state-of-charge of individual cells
- Isolates the battery pack from the load when necessary.
We are seeing an uptick in requirements from the Indian market on several fronts. Startups or teams beginning their software journey want to work with us to establish the right processes for EV powertrain and hence BMS development. We provide the proper modelling and tools and engage through our consulting teams to establish the correct process to meet standards such as ISO26262. We ship several examples with our tools which lowers the barrier to start BMS design for engineers.
On the other end of the spectrum, we are working with engineering teams who are looking at advanced concepts such as Digital Twins for batteries. A digital twin reflects the current asset condition and includes relevant historical data about the asset so a digital twin of the battery can predict the State of Charge and State of health of the battery based on the actual operating conditions of the battery. Modelling a digital twin can employ not just physical models but also data driven techniques using AI.
We are observing a range of engineers at different stages of maturity to meet the EV demand. As EV adoption grows, we expect BMS to be in higher demand especially in the passenger car and commercial vehicle segments. The need will be to develop and validate BMS in a robust, time bound and cost-effective way. MathWorks looks forward to partner with engineers by providing the right tools and consulting services to achieve this demand.
Q7. What are the challenges involved in the development of BMS, and how do you tackle them with your solutions?
MathWorks observations on some of the challenges engineers face in BMS development are as follows:
1.Frontloading software development when hardware is unavailable: Typically, in the life cycle of vehicle development, engineers must develop software much before the hardware is ready. Model-Based Design allows engineers to develop and validate their algorithms on desktops without waiting for Hardware and Vehicle prototypes. Such an approach helps to detect software issues faster – significantly reducing cost and time.
2.Verification and validation with actual batteries: Especially in the case of BMS, verification and validation take a lot of work with actual batteries. Consider a case where an engineer needs to validate the battery algorithm for a specific battery SOC – this will involve charging / discharging cycles that are tedious, unsafe, and difficult to test fault conditions with a real battery. This is where MathWorks battery modeling solutions can come into play. MathWorks recently released Simscape Battery, which allows auto engineers to interactively evaluate different battery pack architectures and automatically create models of the desired pack topology. Engineers can quickly simulate other SOC, SOH, and Fault battery conditions to validate their algorithms’ behavior.
3.Developing for Certifications and Standards: Today, AUTOSAR standards are pervasive in the automotive industry, allowing OEM and other stakeholders to integrate SW and collaborate faster. MathWorks AUTOSAR offerings allow engineers to import AUTOSAR components into our environment, develop the algorithms and generate code for this implementation. There is also a demand for safety-based certifications such as ISO26262, as BMS is a safety-critical component. MathWorks tools are certified by TUV SUD as qualified tools according to ISO 26262 for ASIL A-D. Many teams doing these tasks manually seek MathWorks support to automate the process, thereby reducing the resources needed for certification.
4. Integration of multidomain systems for design and validation: Engineers today need an electromechanical simulation to develop and validate the BMS comprehensively. This requires the integration of electrical, thermal, mechanical, and software systems within a single environment. MathWorks provides workflows to integrate multidomain tools giving engineers the best environment for their use case.
5. Automation for Efficiency: Given the rise of software complexity, engineers today seek tools that can help them automate their tasks and support an increase in productivity. Again, they leverage Model-Based Design to automate several development steps, such as automatic code generation, our Verification and validation solutions that automate testing at model, code, and Hardware-in-the-loop levels. As the industry is moving from prototyping to production, MathWorks investments in Model-Based Design support engineers’ component reuse, reduce manual coding, improve communication with the ecosystem, and deliver a higher-quality BMS.