As temperatures increase, the performance of electronic components can deteriorate. So, it is critical to the function of automotive electronics that heat is efficiently drawn away from its source by thermally conductive materials. As temperatures rise, the choice of materials often narrows to high-temperature-rated epoxies or silicones for effective thermal management.
Many electronics industries operate reliably in harsh environments and extremely high temperatures. In High-Temperature electronics applications the operating temperature is a function of the underground depth of the well. Worldwide, the typical geothermal gradient is 25°C/km depth, but in some areas, it is greater.
High Power Electronics in Automotive
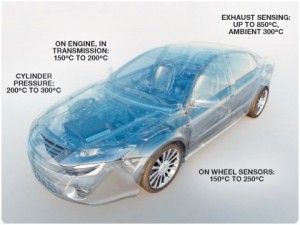
Electrified powertrains, systems, and components bring new performance capabilities, such as greater responsiveness, higher low-speed torque, weight-out, and significantly improved fuel efficiency. But often these new capabilities pose challenges. One of the biggest challenges confronting electric (EV) and hybrid-electric vehicle (HEV) designers today is how to manage the high temperatures stemming from the electrical losses associated with high-power electronics.
Narrow Material Choices
As temperatures increase, performance can deteriorate. This can result in slower or even incorrect CPU processing and almost always reduces component life expectancy. Such reduced performance can occur within two categories: function and fit.
Both function and fit require careful consideration of the different material pathways leading to effective thermal management and thermal stability. But while each poses its own unique set of engineering issues, they can both often be resolved with one material technology.
A look at function
Function is typically the first consideration. In essence it asks, “Will the part continue to work the way it was designed?” Following closely is the question of durability. That is, “How long will the part continue to work to specification?”
Function is seeing new challenges as emerging applications call for the use of higher-temperature chips fabricated on advanced semiconductors like silicone carbide (SiC). But, in all mobility electronics, it is critical to function that heat is efficiently drawn away from its source. This typically requires the use of thermally conductive materials to interface between heat sources and heat spreaders, such as metal fins, pins, fans, or other structures that dissipate heat as quickly as possible into the air.
Thermal interface materials have greatly proliferated in recent years into a dizzying array of physical forms, such as greases, adhesives, gap fillers, encapsulants, and thermal pads. Each of these forms may be served by a broad range of material types, including silicones, epoxies, urethanes, and others.
Each has its own performance profile that must be considered, which includes elements such as coefficient of thermal expansion (CTE), modulus, elongation, strength, and adhesion. Handling characteristics that range from dispensing requirements and assembly time to cure time and clamping also come into play.
As if this were not enough, material selection must also factor in functional performance metrics. These can range from thermal and electrical conductivity, thermal resistance and dielectric properties, as well as joint movement capabilities, stress stability when exposed to high temperatures, vibration, chemical resistance against fluid splash, and other environmental characteristics.
By no means is any of this an exhaustive list. The point is that with so many choices, it can be very difficult to narrow down the best material options for a given module design, especially when design modifications can narrow or widen the choices.
As temperatures rise, however, the list of materials candidates quickly begins to shrink. When temperatures push above 125°C (257°F) in electric brakes or other very high power systems, for example, the choice often narrows to high-temperature-rated epoxies or silicones for effective thermal management.
Both can handle prolonged high-temperature exposure, and both can deliver excellent heat flow characteristics via formulation with highly conductive fillers. Given the availability of these equally thermally conductive products, the choice is frequently determined by thermal joint design and durability under simulated accelerated environmental aging.
Epoxies have the advantage of providing structural strength and rigidity. Interfaces that require bonding strength without fasteners, for example, will generally be better served with a conductive epoxy.
Likewise, the high modulus and hard durometer of epoxies can benefit joints designed to allow very little movement from thermal cycling, vibration, or other application stresses. The potential drawback of these characteristics is the tremendous stress that can be produced during any induced movement. During thermal cycling, CTE mismatch coupled with very high modulus can easily break wires, ball grid arrays, or components. This is the point at which epoxies reach their physical limits.
Silicones are available in a wider variety of forms than epoxies to meet designers’ ever-broadening design requirements for maintaining reliably functional electronics. These advanced materials, in many ways, occupy the other end of the mechanical property spectrum. They may not share the structural strength of epoxies. But they are softer and highly flexible. Also, despite their comparatively larger CTE, the very low modulus of silicones compensates during thermal cycling to result in much lower stress. In fact, they often behave as effective buffers against system stress.
Thermally conductive silicone gap fillers, encapsulants, and pads all may generate some stress during thermal cycling, for example. But silicone adhesives, which are by nature a harder form, still offer very low modulus in comparison with epoxies. Silicone greases, which are essentially very thick liquids, provide the least movement stress since they readily deform.
Very soft silicone gels deliver expansion pressure that is an order of magnitude lower than epoxies by some measurements.
Fit as fit can be
Fit concerns how well materials not necessarily in the heat flow pathway tolerate the high temperatures common in and around advanced electronics, such as emerging power electronics based on SiC. The focus here is on the thermal stability of materials during the manufacture and application life of electronic components, boards, housings, and environmental protection products. As in the case of function, there is an array of materials and material forms for each of these applications.
Protective materials for mobility electronics, for example, commonly take the form of conformal coatings, gels, encapsulants, and/or housing sealings. There are a variety of material choices for each of these protection strategies. But again, as temperatures rise the options narrow, and once more epoxies and silicones are typically viewed as the best candidates.
As discussed previously, the low CTE but very high modulus of epoxies make them suitable as adhesives and encapsulants in certain applications. But within certain upper-temperature limitations, high CTE yet extremely low-modulus silicones often can provide equal and even superior performance compared to epoxies. This is especially true in applications demanding significant joint movement, or where more stress-sensitive components or other important features exist.
Thin silicone conformal coatings offer particularly cost-effective protection against liquid splash or humidity. In these applications, the strength of epoxies can actually be a significant detriment if rework or repairs are needed, or during part failure analysis.
Epoxies and silicones are both commonly used for thermal management and environmental protection when high application temperatures threaten durability and performance of mobility electronics. Both can be formulated to achieve similar thermal conductivity and both have high thermal stability.
Epoxies are very strong and tough, but the stress they generate from CTE mismatch during thermal cycling can be excessively high and even catastrophic. Silicones may have higher CTEs, but they are very soft and offer low modulus—yielding substantially lower thermal stress on bonds, wires, and components.
In addition, silicones are available in many more product forms to offer wider design latitudes when designing high-power electronic devices. This makes them especially valuable when designing electronic components and systems for the harsh operating environments of hybrid-electric, as well as all-electric vehicles.