By Mark Patrick, Mouser Electronics
Recent automobile industry research indicatesa rise in the uptake of electric vehicles.Automobile sales stalled during the pandemic, but it appears that many people used this time to consider their options before making their next vehicle purchase. For increasing numbers of consumers, an EV has become a practical option, but their wider acceptance is limited by worries about travel range and charging times. Despite this, the availability of Government grants and manufacturer discounts mean that the rate of sales growth is predicted to increase in the future.
From the point of view of automobile manufacturers, there remains several technical challenges to be overcome. The early approach used to encourage the adoption of EVs was to widen the choice of brands and models available on the market. However, maintaining and then building on this growth will also require the development of new vehicle technologies.
Battery development, design and construction is one area that is evolving. While many of these innovations are relatively new, they are already showing potential. The provision of an easy-to-use and readily accessible EV charging infrastructure also requires substantial investment. Apart from price, range and the length of time it takes to recharge a vehicle are still the most important issues and vehicle weight impacts on all of these.
Today’s EVs today still include a 12 V battery to provide power to functions such as windscreen wipers, seat comfort controls, and infotainment system. However, in newer models, some manufacturers are beginning to use a 48V battery.
12V Battery Power
Almost every new vehicle now includes an extensive range of electronics-based functions. Sophisticated touch-controlled infotainment systems now typically feature radio, media players, a navigation system, smartphone connectivity and interfaces that provide information about vehicle status and show systems configuration menus. Occupants can stream music from their smartphone, a multimedia storage drive, or a cloud-based service. Advanced driver assistance systems (ADAS) use a combination of RADAR, LiDAR, and machine learning-based computer vision to enable safety features such as adaptive cruise control (ACC), blind-spot detection, and emergency braking. While these are based on advanced technology, they are all powered by the legacy 12 V battery.
In EVs with a 400 V or 800 V battery pack, adding an extra battery with power management electronics, simply to power infotainment and ADAS systems, would add unnecessary cost. Figure 1 shows the higher levels of complexity in hybrid and full EV power architectures compared to the internal combustion engine powered vehicles.
Automotive manufacturers traditionally packaged each system function in a dedicated electronic control unit (ECU)powered from a 12 V supply rail. This distributed approach to power conversion and management increases the BOM. Aside from BOM, it is important to remember that a 12 V battery (typically 20kg) and associated components add significant weight to an EV.
The power train in an EV requires more than 50 kW of power management and conversion, substantially more than the 3 kW (max) for a vehicle powered by an internal combustion engine. This makes light, small, reliable and efficient power conversion critical. The power architecture of an EV must meet the requirements of the legacy systems, onboard and infrastructure charging, and the drivetrain.
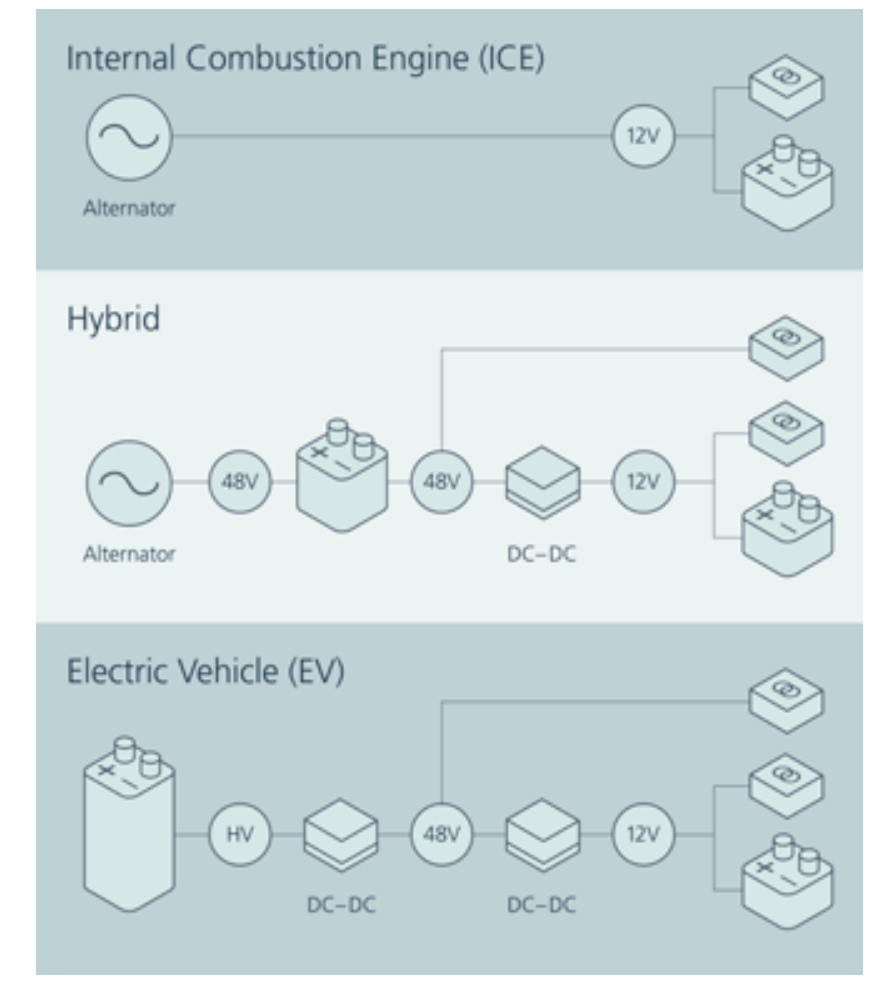
Innovative Automotive Power Deliver Architecture
Vicor propose an alternative approach to power delivery that can help manufacturers to meet these challenges. This method uses some of the power in the 400V/800V battery pack to perform the functions ofa ‘virtual’ 12 /24/ 48V battery, as shown in Figure 2. In this way, manufacturers can save weight and reduce engineering, supply chain and stocking costs.
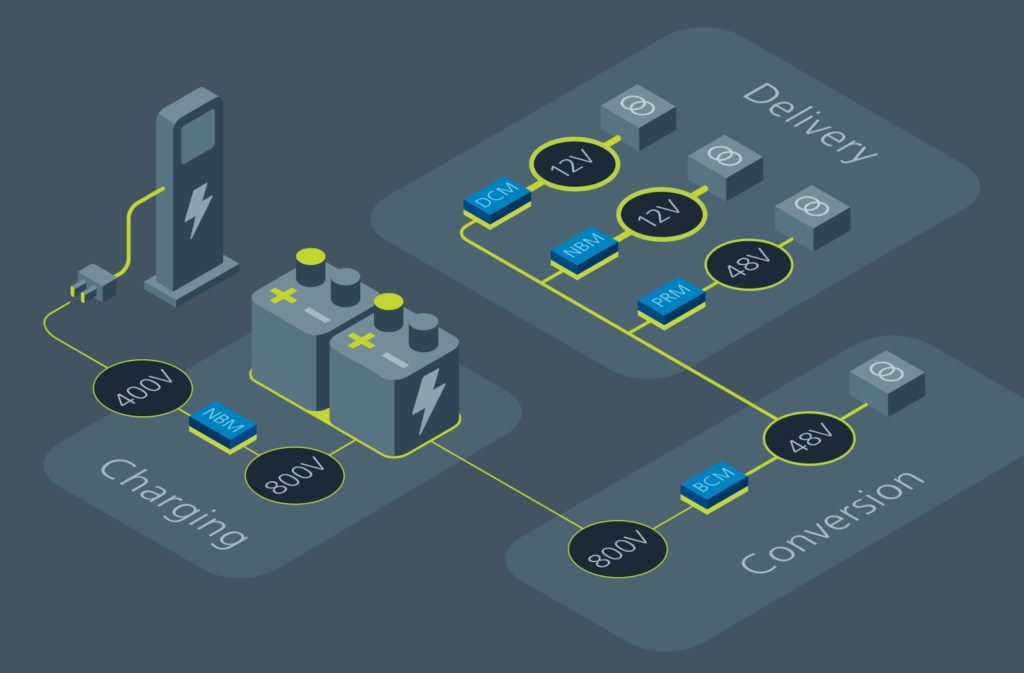
Vicor also incorporate highly integrated step-downconverters modules into existing sub-systems, to help further reduce size and BoM.This architecture addresses three aspects of the power network as shown in Figure 2 – charging, conversion, and delivery.
Charging: While many EV manufacturers are moving towards an 800 V battery pack operating voltage,much of the existing EV charging infrastructure is based on the original 400 V standard. This means that new EVs must be able to operate using both voltage levels. Bi-directional converter modules provide a flexible, highly efficient, and highly integrated way to provide this dual voltage compatibility.
Conversion:Manufacturers can save weight and space by using high-density automotive-qualified DC/DC modules to down-convert the high battery voltage, then using the virtual 48V battery to provide intermediate energy storage where required.
Delivery: Drive, steer and brake-by-wire are examples of 48V applications now being included in newer vehicles. Vicor provide small and light modules to meet the power delivery requirements of these and legacy systems.
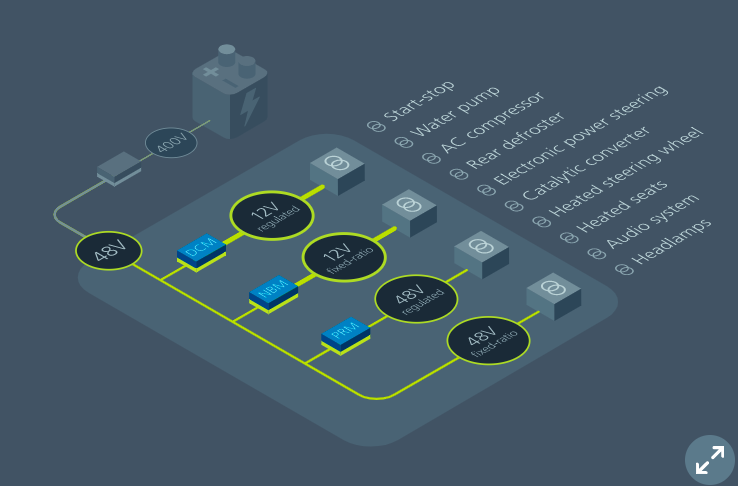
Rethinking Power Delivery in EVs
EVs have proved to be the most viable option for automotive OEMs to reduce emissions and their focus is now turned to improving vehicle performance.Part of this challenge is to minimize vehicle weight to allow them to travel for longer distances before recharging. Redesigning the power delivery architecture in an EV can help to achieve this goal, while also helping to lower costs.
Mouser Electronics
Authorised Distributor
www.mouser.com