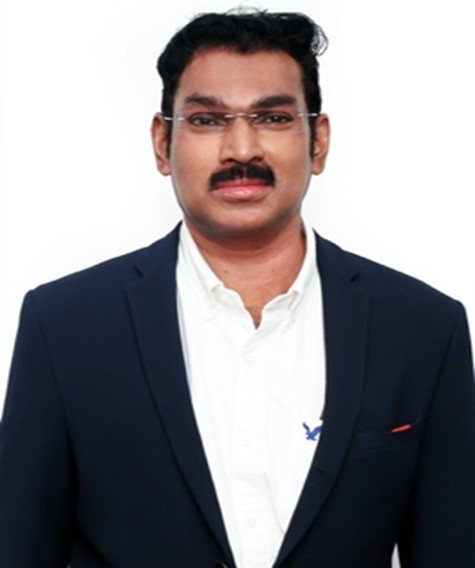
The scope of Industry 4.0 is so broad that in order to succeed, electronics manufacturers must concentrate on areas of expertise rather than master all new technologies. Sekaran Letchumanan, Vice President, Operations at Flex India, in an exclusive conversation with Electronics Maker shed light on Industry 4.0 technology in Industry automation and how it will ensure effective collaboration with the partners.
1. What role do you see 5G playing in the development of Industry 4.0 in India, and how can manufacturers leverage this technology to stay competitive?
The advent of 5G technology is set to play a pivotal role in the development of Industry 4.0(I4.0) in India. The integration of 5G technology into I4.0 holds great promise for the future of manufacturing.
Leveraging 5G in Industry 4.0 can help manufacturers compete by enabling real-time data processing and analytics for faster, informed decisions. Automation and robotics in production processes can increase efficiency and reduce costs. 5G can enable remote work, training, and maintenance using AR/VR tools, reducing travel, and improving safety. Embracing 5G and digital technologies can give manufacturers a competitive advantage, transforming the industry with increased automation, flexibility, and efficiency.
2. What are some of the biggest challenges you face when integrating automation and robotics into a manufacturing process, and how do you overcome them?
Integrating automation and robotics into manufacturing processes can bring several benefits, such as increased efficiency, reduced costs, and improved safety. However, there are various obstacles that one must overcome. Challenges like the high upfront investment required can be a significant barrier for smaller manufacturers; integrating new automation and robotics with legacy manufacturing processes and equipment can be challenging and require significant retooling and reconfiguration. Also, creating a technology framework that integrates hardware and software to monitor key machines’ status and regular maintenance and repairs of automation and robotics systems can be time-consuming and expensive.
One of the primary challenges to automation in manufacturing is the resistance to change among employees who may feel uncertain about new technologies and methods. To overcome this, manufacturers should ensure that they are well-informed about the benefits of new technologies and train existing employees to use the new technologies. Reskilling and upskilling programs can greatly benefit organizations. Initiatives such as the All-India Council for Technical Education (AICTE), Atal Innovation Mission (AIM) and lastly, Recognition of Prior Learning (RPL) a skill certification introduced by the Government of India helps bridge the skills gap in the industry and move towards upskilling the workforce.
At Flex India, we have developed an Education Assistance Program (EAP) for all employees designed to foster professional growth. Through this local initiative, eligible employees benefit from technical training or financial assistance for professional development through partnerships with engineering colleges.
3. How can manufacturers ensure the security of their data when using cloud computing in smart manufacturing?
To ensure the security of data in smart manufacturing, manufacturers should use encryption and access control, choose a trusted cloud service provider and lastly, monitor systems regularly for security breaches. Automation of manufacturing execution system (MES) features can also optimize production plans, increase productivity, and reduce the risk of errors or delays. Additionally, employees should be trained to adopt best practices for data security, such as implementing strong password policies and limiting access to sensitive data.
Encryption and access control can protect sensitive data by scrambling it into an unreadable format and limiting who can access data and how they can access it. A trusted cloud service provider with robust security measures in place, such as firewalls, intrusion detection and prevention systems, and regular security audits, is also important. Regular monitoring of systems for security breaches, vulnerability scans, penetration testing and security incident and event management systems are also crucial to ensure data security.
Finally, manufacturers should adopt best practices for data security and train their employees to be aware of the risks and how to mitigate them, such as regular security awareness training, strong password policies, and limiting access to sensitive data only to those who need it. These measures can ensure the security of data when using cloud computing in smart manufacturing and leverage the many benefits that this technology offers.
4. How can predictive maintenance help electronics manufacturers reduce downtime and improve the reliability of their equipment?
Industry 4.0 (I4.0) is being used to decrease downtime through predictive maintenance. Predictive maintenance is a method that analyzes operational data from machines to identify irregularities in operation and potential equipment faults, thereby preventing any unexpected failures.
By analyzing data from sensors, manufacturers can identify potential issues and proactively schedule maintenance, preventing costly breakdowns and downtime. This approach can also optimize maintenance schedules by focusing efforts on equipment that is showing signs of wear or impending failure, reducing the frequency of checks for equipment that is operating efficiently.
By leveraging predictive maintenance, electronics manufacturers can increase operational efficiency and profitability by minimizing downtime, improving equipment reliability, reducing maintenance costs, and optimizing inventory management. This will give manufacturers an added edge due to the ability to be more agile in the face of market changes.
5. How do you ensure efficient collaboration with suppliers and partners using Industry 4.0 technologies?
In smart factories, digitization and other industry 4.0 (I4.0) technologies enables the connection of machines and systems to exchange information and perform coordinated actions with one another. I4.0 technologies offer the additional benefit of fostering collaboration using cloud-based platforms that enables suppliers and partners to share data and information. This can help suppliers and partners have a better understanding of the production process, from the availability of raw materials to the status of finished products. Such collaboration aids in simplifying communication, shortening lead times, and enhancing overall supply chain efficiency.
Flex sites around the world leverage I4.0 technologies to not only deliver better business outcomes for our customers but also advance sustainable manufacturing and production throughout various manufacturing processes. For e.g., by recognizing the manufacturing industry’s role in tackling e-waste challenges, our zero-waste certified Sorocaba, Brazil site developed a circular economy ecosystem using I4.0 technologies to transform e-waste and reintroduce repurposed materials into the product lifecycle by repairing, recycling, and refurbishing.
This has resulted in a 94% reduction of material waste and a 38% reduction of plastic material costs. This decade-long journey has earned Sorocaba its designation as the first Sustainability Lighthouse in Brazil by the World Economic Forum.
6. How do you see virtual reality evolving in the manufacturing industry in the next few years?
Over the past decade, Industry 4.0 (14.0)technologies have promised new levels of efficiency, quality, and sustainability in manufacturing. However, the pandemic has solidified that advanced shop floor technologies, like simulation and automation, will play a fundamental role in the future of manufacturing.
For example, in early 2020, when travel restrictions were a significant concern, simulation enabled us to collaborate with customers closely (yet safely). The technology helped us create a virtual realm or digital twin of factories, line layouts, staff, equipment etc., to simulate and improve real-world processes.
Not only did this help us increase efficiencies in throughput, bolster production, and optimize processes, but it also allowed us to test scenarios and have upfront conversations with customers without having to travel or move equipment and material, saving time and money. Beyond simulation, leading-edge innovations in automation, AI, digitization, and other disruptive technologies, coupled with the years of experience and critical thinking of employees, are unlocking a new era of manufacturing.
This era will allow organizations to capture and transform all the data on the shop floor and generate never-before-seen insights that enable optimization and spark further innovation.
At Flex, we’ve invested in a focused portfolio of I4.0 technologies that deliver value to our customers. Recently, we have been recognized by the Manufacturing Leadership Awards and the World Economic Forum’s Global Lighthouse Network (GLN) for manufacturing excellence.