Industries such as fuel retailing, water/waste management, agriculture and recycling often need to store large quantities of liquids in tanks or containers that may be distributed over a large geographical area. Monitoring the levels of liquids in tanks has traditionally been a manual process that suffers from several drawbacks. Visiting remote sites can be time consuming, and taking measurements can be unpleasant or dangerous, particularly in bad weather. Some workers may forget or neglect to take regular readings.
In any case, taking measurements manually always carries the risk of human error, which can cause incorrect data to be recorded: If a tank is holding sales stock, such as fuel or diesel exhaust fluid at a filling station, the tank may then run empty before being refilled, or excessive new stock may be ordered that cannot be stored. On the other hand, if the tank is storing waste liquid for disposal or recycling, accurate level information can allow the tank to be emptied on demand thus avoiding the expense of regular visits to collect small quantities.
Taking advantage of Industrial Internet of Things (IIoT) technologies promises a convenient and cost-effective means of eliminating these drawbacks and achieving improvements such as saving unnecessary mileage, raising operational efficiency, improving customer service, and enhancing worker safety.
Non-contact fluid-level measurement
Sight glasses and float/level indicators are long established methods for verifying fluid levels inside industrial tanks. Sight glasses can be expensive to implement and seal, and float/level sensors can be vulnerable to failures caused by corrosion, jamming, or puncturing of the float. Ultrasonic sensors can eliminate the complex sealing needed with a sight glass, and exceed the reliability of float/level sensors since there are no moving parts.
Ultrasonic level sensors like the TE Connectivity Ultrasonic Sentio™ LL-01 are threshold sensors that generate a signal by detecting the presence of fluid in the probe’s sensing gap. The ultrasonic signal is transmitted across the gap, and fluid detection relies on the difference in attenuation, which is much lower when the gap is filled with fluid. When the detector receives a valid signal, the sensor generates an output indicating liquid is present. This type of sensor is suitable for applications such as pump protection, oil-film detection, or cutoff systems.
A different ultrasonic monitoring principle is needed to measure the exact level or volume of fluid in a tank. The SSI Technologies Digital Fluid-Trac™ DFT-110, which is designed to be fitted in the lid of a standard 55 gallon drum, generates an ultrasonic sound wave that is reflected from the surface of the fluid below (Figure 1). By measuring the time for the echo to arrive, the distance from the sensor to the liquid can be calculated based on the speed of sound. The sensor then calculates the volume of liquid, using the known dimensions of the drum as specified in the industry standard (ANSI MH2-2004), and shows the result on an integral display panel that comprises a digital LCD and red LED low-volume warning light. The liquid volume can be measured with resolution of 1.0 liter.
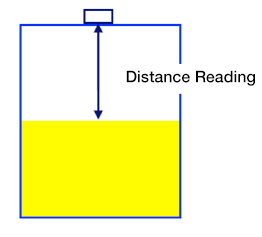
Large-scale remote fluid-level measurement
With the development of the Industrial Internet of Things (IIoT), it is possible to envisage a remote fluid-level sensing solution that sends ultrasonically monitored fluid-level data into The Cloud and makes detailed information readily available via a web browser on a desktop or mobile device. The information may be as simple as threshold alerts or real-time fluid-level readings, or predictive information generated by a Cloud-based analytical application.
Digi International has created a family of turnkey fluid-level sensors that use the same ultrasonic measurement principle as SSI’s DFT-110 mentioned earlier, and also integrate a cellular connection and optional GPS receiver. Among these devices, the Digi Connect® Tank CTANK-A611 has a short-range ultrasonic detector, an international 2G/3G UMTS cellular connection, and incorporates a GPS receiver that allows the sensor to send location data as well as fluid-level information. Using the cellular connection enables tanks to be monitored even in remote locations where other network infrastructure may not be available. The sensor also contains a temperature detector to compensate for the known change in the speed of sound with temperature, and has a non-rechargeable battery that can last up to two years performing two reads and two transmits per day.
The sensor sends the fluid level and location data via the cellular network to the Digi Device CloudSM. Device Cloud account holders can use this service to monitor sensed values and sensor status via a web browser, and can also take care of configurations and firmware updates. Information calculated by the Digi Device Cloud service can be imported to an application such as an enterprise supply-chain management program to coordinate the necessary response, such as purchasing extra liquid and arranging delivery to the site, or instructing a recycling collection to visit and empty the tank. Figure 2 shows how the Digi Connect Tank and Device Cloud can be used as a turnkey monitoring solution for coordinating the supply of Diesel Exhaust Fluid (DEF) to a filling station (DEF is injected into the exhaust of a diesel engine to reduce soot and harmful NOx emissions).
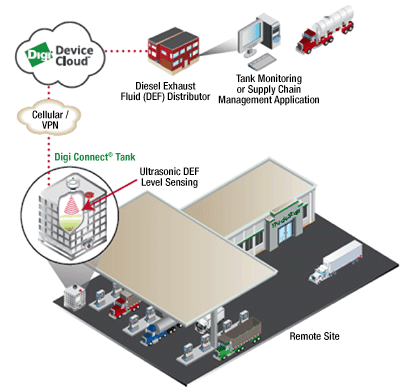
The Digi Connect® Sensor cellular gateway is also available, and provides a means of connecting a wide variety of sensors to the Digi Device Cloud (Figure 3). The module has four analog I/Os that can be configured as 1-10 VDC or 4-20 mA current inputs giving flexibility to connect numerous types of analog industrial sensors. A digital I/O is also available, which can be configured to count pulses or wake the device from sleep on detection of a rising or falling edge. Each connection also contains an adjustable voltage output that can be configured to power almost any sensor. Also available is the Digi Connect Wizard mobile app, which can connect directly to the sensor gateway via Bluetooth® to display data locally, thereby saving any need for dedicated instrumentation. This mobile app can also connect to the Device Cloud service to verify configurations and monitor status.
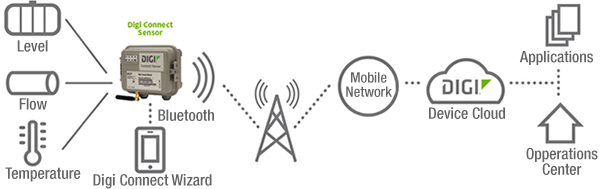
Conclusion
Ultrasonic fluid-level sensing is safe, convenient and reliable. Sensors that calculate the distance travelled by ultrasonic waves provide accurate measurements of fluid levels, and can be used in a variety of scenarios for local or remote monitoring. For remote monitoring, a turnkey solution like Digi Connect Tank with built-in cellular connectivity integrates everything needed to configure the sensor and gather the data in The Cloud for analysis and monitoring. The sensor and Device Cloud service are part of a wider IIoT ecosystem that enables a large variety of industrial sensors to be easily connected to The Cloud.
Contributed By Digi-Key’s European Editors