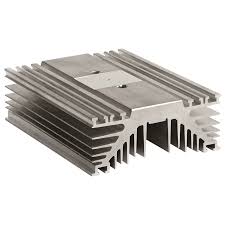
Heat Sinks are most components for thermal management in technology, natural systems, and machinery. Heat sinks are always overlooked by the technicians as well because they are ever present. In this article we will cover the basics of a heat sink, and pros and cons of a large heat sink
What is a heat sink?
An aluminum heat sink is used to direct heat flow away from the device. In other words, it acts as a heat exchanger and is engineered to have a large surface area with a cooling agent: air. Smooth working of the heat sink is determined by the engineering of the component, surface treatment, physical features such as protrusion design, and air velocity. Other factors that can greatly affect the working of a heat sink are width, thermal resistance, air flow, volumetric resistance.
Two types of heat sinks
- Passive Heat Sinks: These heat sinks do not use any fans to cool off and they do not have any sort of moving parts and are considered as more reliable.
- Active Heat sinks: These heat sinks use a cooling fan to cool off. They have an effective performance, but they require high maintenance due to the moving parts
How Does a Heat Sink Work?
Heat sinks works in a four-step process
- Heat Generation: Heat is generated by a source; this source can be any machinery or technological device which requires the heat to be removed for working properly.
- Diverting the heat: Heat moves away from the source and sinks into the heat sink via natural conduction. The thermal conductivity of the material used to make heat sink directly affects the performance. Therefore, it is suggested by the techs to use copper and aluminum for the making of the heat sink
- Distribution of heat:Heat naturally will move throughout the heat sink via conduction. Heat will move across the thermal bank away from the high temperature environment towards the low temperature environment. Heat sink, because of the distribution of the heat, will be hotter on the side of the heart source
- Heat moves away from the heat sink:This process depends on the temperature gradient and the heat sink’s fluid: air or sometimes non-electrically conductive fluid. The fluid passes on the surface of the heat sink and absorbs the heat from the sink using thermal diffusion process to remove heat from the surface and into the more ambient environment. If the ambient environment is not cooler, then no heat removal of any sort will occur.
Aluminum Heat Sinks
Reconstruction of aluminum extrusions has offered new way to produce a higher ratio air cooled heat sink. An experienced heat sink manufacturer always makes good use of the aluminum extrusions to create a large heat sink.
At its finest, aluminum extrusion is a process of forcing aluminum into a shape by forcing it to pass through a die. Extruded aluminum comes out as the shape of the die. Reconstruction of aluminum takes the form of improvements in the process of the extrusion by enhancing the speed or by beautifying the finish. The new process of extrusions is mainly beneficial for lighting and electronic industries.
Extruded heat sinks are widely used thermal management technology for cooling, power electronic modules.
There are two categories of extruded heat sinks:
- Fin Ratio: The height of the fin in comparison with the width in between the fin. The most common ratio is 6;1 which is not the required ratio by the most power electronics. The ratio which is required nowadays is 12:1 exceeding to 19:1. Fin ratio is directly proportional to the surface area of heat sink, the greater the fin ration the greater the surface area. And the greater surface area can help effectively in the removal of heat
- Higher ratios: Extrusion of higher ratio requires experience and technology; it is very challenging to extrude higher ratios and it is almost impossible to find 24 in heat sinks.
Methods to creating large heat sinks
Epoxy Bonding
When higher fin ratios are required bonded fin heat sinks are used because they have a higher fin ratio. Bonded fin heat sinks involve the use of epoxy method to j-bond aluminum extrusions to a coil of aluminum.
Friction Stir Welding
Friction stir welding is a bonding method for aluminum welding. It joins the metal surfaces by rotating a mechanical tool and produces high strength homogenous joints which will not downgrade over time. The process begins with extruded base and fin which are held together by clamping the friction stir welding process ensures a maximum of 20 in heat sink
The benefit of extruded heat sinks is that it is a solid plate of the thermal material it does not have any insulators which is why it can help effectively in the heat removal.
Test results
The comparison between epoxy bonding and FSW modular heat sink was carried out in a wind tunnel with different airflows. Several metrics like pressure drop, temperature distribution, and thermal resistance were noted and compared with the benchmark as being the extruded heat sink. The heat source used was power resistors. The results obtained were phenomenal. The FSW showed 8% increase in thermal performance over epoxy binding.
The 8% increase provided two benefits. One was the size of the heat sink wasn’t compromised with the increase amount of power an electronic device generates. The second was to decrease the size of the FSW heat sink by 8% without affecting the thermal performance.
What are the Pros and Cons of a Large Heat sink?
A large heat sink will provide a greater surface area which help in effective absorption of heat. A large heat sink is engineered in a way that it has more contact with heated surface to allow more effective heat transfer. It also allows a greater surface for cooling area, allowing heat to travel across heat sink and getting transferred to a more ambient environment. This is beneficial for people who over work their computers by using different things at one time. It also helps the CPU to work more effectively and efficiently.
However, it must be noted that. A large heat sink will have greater surface area and therefore it will take a lot of space inside the computer. This will create a hurdle in installation of other important components. It will also create a barrier to reach ports and plugs inside a motherboard. A large heat sink can be very loud.
Wrapping Up
Heat sinks applications are now widely used in many electronic devices and its ability to dissipate energy outwards is what makes this product stands out. Careful designing and manufacturing need to be carried out to produce an energy-efficient heat sink. And as technology is advancing exponentially, choosing the right and most effective material is also a necessary.