Dr. Boris Golubovic, Vice President, Marketing & Strategy, Littelfuse
Designers need to consider a range of circuit protection solutions to ensure customer satisfaction.
To ensure a positive user experience and high customer satisfaction, modern appliances that include the latest electronic functions must also incorporate appropriate circuit protection solutions.
Even though appliances are more complex, consumers continue to expect that major appliances will provide a lifespan of seven to ten years or longer. Because of the growing number of electronic components in refrigerators, appliance design engineers must consider carefully how to continue to meet consumers’ reliability and longevity expectations. Although fridge designers have long have taken considerations like power efficiency and sensor monitoring into account, ensuring adequate circuit protection has become more important than ever as the number of features grows.
Built-in wireless connectivity modules are becoming more widely available to address consumers’ interest in remote monitoring and control of their appliances. The Internet of Things (IoT) is making it possible to make IoT appliances part of the smart home concept.
The newest refrigerator designs offer a wide choice of “smart” features ranging from speed chilling, variable speed compressors that help limit internal temperature swings to reduce energy usage, and separate compartments that can adjust refrigeration conditions based on what’s stored in them to high-efficiency LED lighting, see-through doors, touchscreen communications, and internal cameras for remote viewing. In many ways, today’s refrigerators have more in common with consumer electronics like smartphones and tablets than they do with the home appliances of a few decades ago. However, the relatively high price tag for today’s refrigerators means that buyers feel they have the right to expect a far longer lifespan than the three to five years that consumer electronics buyers would accept.
Today’s communications, processing, and user-interface electronics require more comprehensive consideration of ESD, power surges and other electrical disturbances. That means designers need to consider an ever wider array of circuit protection solutions to ensure customer satisfaction.
The Evolution of the Fridge
Earlier generations of refrigerators and freezers relied on the use of mechanical switches to indicate open doors and compartments, but newer models employ various electronic and magnetic sensors. Although these sensor systems generally allow for more durable, aesthetically pleasing, and easier-to-clean designs, some technology choices can also be more vulnerable to damage from electrical transients.
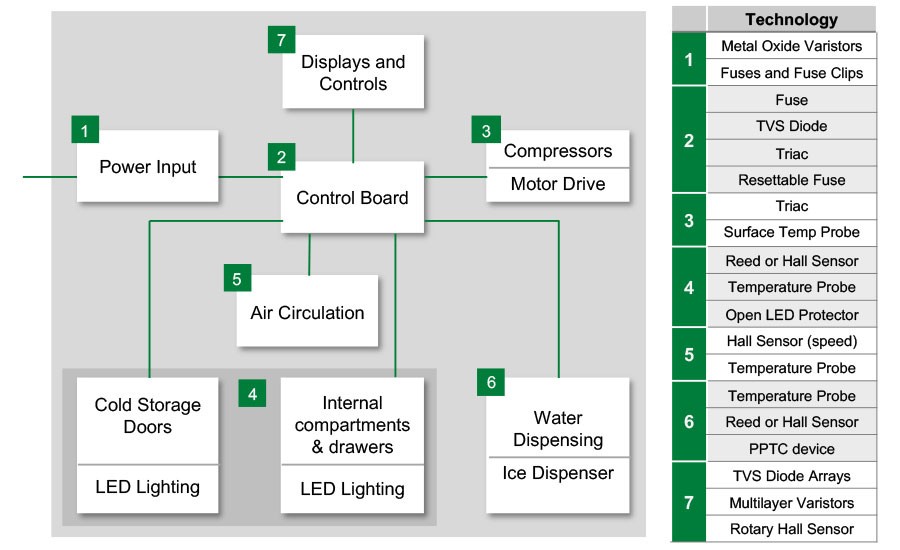
To reduce energy consumption and support all the advanced features that consumers are looking for, modern refrigerators and freezers incorporate more control circuitry and a growing array of temperature, humidity and digital sensors distributed throughout the unit in the various drawers and compartments. However, adding more electronics increases the potential for more electrical failures, potential warranty expenses, and dissatisfied customers.
To enhance the user experience by providing higher brightness and greater color accuracy, modern fridge lighting is rapidly switching from incandescent lighting elements to LED-based illumination systems. However, just like many other semiconductor devices, LED drivers and lighting elements themselves may need protection against electrostatic discharge (ESD) voltages and electrical transients. It is worth noting that ESD surges are often the result of normal user interactions; surges in excess of 10 kV can be a result of a person touching the unit after simply walking across a carpeted floor.
The newest appliance designs also incorporate increasing numbers of small motors and actuators, such as those in water dispensers, ice machines, fans, etc. For each of these motors, designers must consider what’s needed to ensure protection against overcurrent and overheating conditions.
Designers who incorporate wireless communication capabilities and touchscreen user interfaces into appliances need to consider the best design practices employed to protect mobile electronic devices (tablets, phones, notebooks). However, given the choice, more conservative design practices are warranted because many mobile consumer devices come with significantly shorter life expectancies than appliance buyers demand.
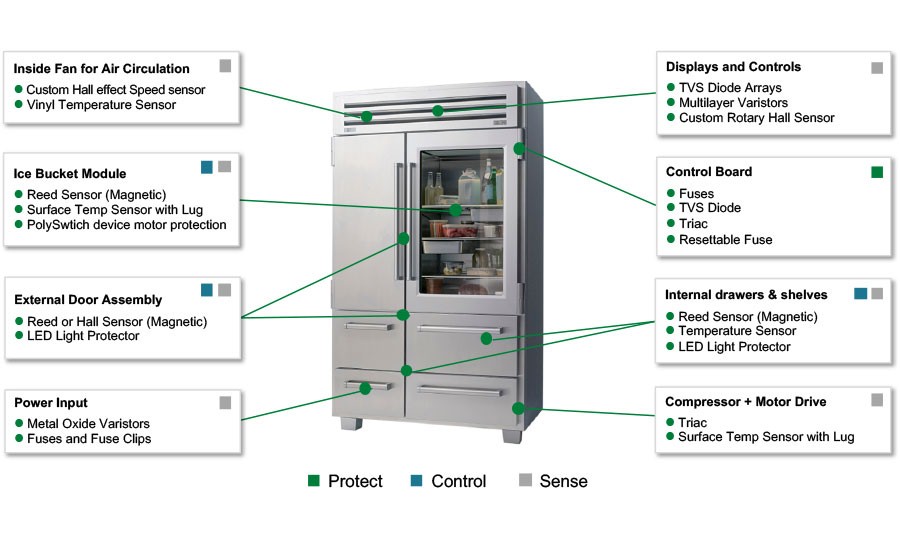
Identifying Vulnerabilities
A wide range of refrigerator and freezer components are vulnerable to electrical threats and can benefit from the right type of circuit protection. The specific protection technology needed will depend on the specific electrical threat present and the component being protected. These include:
- Sensors (e.g., proximity, temperature, humidity)
- Motors and actuators (e.g., ice machine, doors, fans)
- User interface (e.g., touchscreen and displays)
- Cameras
- LED lighting
- AC power input
Specific Electrical Threats and Solutions
Sensor Protection
Temperature sensors are typically very robust devices, but today’s refrigeration systems have many more of them than those of the past. Some modern designs can have eight or more temperature sensors to monitor the various compartments. This increases the complexity of the circuit protection design because of the addition of long signal lines and the need for computer control.
Other sensor types, such as switch sensors and pressure sensors, are also typically located far from the control board, requiring signal lines that may be up to a meter long.
It’s essential to maintain signal integrity over these longer distances. Long signal lines can act as antennae, which can inadvertently add excess electrical noise to the signal. This, in turn, can result in false sensor or control readings. This is the first design consideration; therefore, one must ensure the signal remains high enough and surges stay below the damage threshold of signal processing components.
The second design consideration is induced voltage surges, another vulnerability that can be amplified by long signal lines.
- Threat: Induced surge. Consider a signal line that runs close to the compressor or power line, which could cause an induced surge on the line that damages either the devices on the control board or those on the sensor. Some sensor solutions are more robust than others; for example, magnetic sensors based on reed technology tend to stand up better in appliance applications than some solid-state options; similarly, for temperature sensors, negative temperature coefficient (NTC) thermistors or polymeric positive temperature coefficient (PPTC) devices may be more robust than some semiconductor alternatives.
- Technology solution: Designers often employ either a multilayer varistor (MLV) or a transient voltage suppression (TVS) diode for circuit protection.
- Location in the circuit: Protection devices can be located either on the control unit’s printed circuit board or nearby, or at the sensor end of the line. Typically, the components on the control board are more sensitive than the sensor, so add protection devices on the control board at a minimum.
Motor Protection
- Threat: Overheating. For example, an ice machine could stall, overheating the motor and causing it to fail. Protection of this nature is commonly used on seat motors in vehicles, window lift motors, or similar applications.
- Technology solution: The simplest solution is adding a PPTC device. These self-resettable fuse-like devices will open quickly at elevated temperatures. A temperature sensor is an alternative solution, but that requires intelligent control.
- Selection consideration: The protection device should be chosen based on the motor’s operating current and placed at the motor where the heat is generated.
User Interface Protection
Touchscreens, cameras, touch panels and controls also require careful consideration as to the needed level of circuit protection; portable electronic device engineering practices are a good starting point.
- Threat: ESD. Wi-Fi, Bluetooth, and ZigBee systems are all susceptible to ESD exposure. ESD is a greater risk than many designers realize. As mentioned previously, just walking on a carpeted floor can generate 10 kV or more. Consequently, ESD protection may not be adequately specified by the design engineer. It’s never safe to assume that the touchscreen module specified includes sufficient ESD protection.
- Technology solutions: Polymer ESD suppressors and solid-state ESD protection devices are optimal choices to suppress energy before it can reach sensitive chipsets.
- Selection consideration: This choice requires weighing some engineering tradeoffs: for example, for an antenna, a polymer ESD suppressor will have less capacitance, which could otherwise clip the signals. A diode array, however, might be preferable when the space available is extremely limited and multiple devices are needed.
Proper mechanical design can significantly reduce the risk of ESD, allowing designers to forego an ESD protection device in some circumstances. These devices include specialized components that protect circuits from ESD and thus from malfunction. On the other hand, making some mechanical changes (such as to a gasket) could be more expensive than adding an ESD protection device.
When testing the user interface, test to the industry standards applicable to consumer electronics like smartphones and tablets. Relevant standards for units equipped with wireless communication capabilities include:
- IEC 60335 series – General Safety of Household Appliances
- IEC 60730 series – Automatic Electrical Controls
- IEC 60950 series – Information Technology Equipment (ITE)
- IEC 62368 series – ITE, A/V, and Communication Equipment
LED Protection
- Threat: Voltage surges (overvoltage).
- Technology Solution: A TVS diode on the LED driver. An LED lighting element with basic surge protection on the driver circuit is generally sufficient to provide protection in normal residential environments. The LED driver, on the other hand, is a more sensitive electronic device that can be damaged by voltage surges caused by induction. A TVS diode is usually applied on the board upstream of the driver device to provide surge protection
AC Power Line Input Protection
- Threat: Overcurrent and overvoltage.
- Technology Solution: This is the most “classic” protection point generally addressed with overcurrent protection though fuses and overvoltage protection through metal oxide varistor (MOV) devices. At this design point, it is critical to check for compliance with applicable national and international safety regulations (such as UL or IEC) every time
Summary
As the complexity and feature sets of today’s refrigerators and freezers have grown, so too has the need for effective circuit protection. Once they’ve gained an understanding of the electrical threats and their associated technological solutions, appliance designers can do much to enhance the robustness of their designs and ensure they provide a long-term positive customer experience.