By Tony Armstrong and Steve Knoth, Analog Devices, Inc.
In today’s world of constant connectivity, it is commonplace for many electronic systems to be always operational—regardless of their external environment or operating conditions. Said another way, any glitch in a system’s power supply, whether momentary, seconds, or even minutes, must be taken into account during its design process. The most common way of dealing with such circumstances is to use uninterruptible power supplies (UPSs) to cover these brief downtimes, thus ensuring high reliability, continuous operation of the system. Similarly, many of today’s emergency and standby systems are used to provide backup power for building systems to provide assurance that safety systems and critical equipment can maintain their operation during a power outage—whatever the root cause.
Obvious examples can be readily found in the ubiquitous handheld electronic devices used in our everyday lives. Because dependability is paramount, handhelds are carefully engineered with lightweight power sources for reliable use under normal conditions. But no amount of careful engineering can prevent the mistreatment they will undergo at the hands of people. For example, what happens when a factory worker drops a handheld portable scanning device, causing its battery to detach? Such events are electronically unpredictable and important data stored in volatile memory would be lost without some form of safety net—namely some sort of short-term power holdup system that stores sufficient energy to supply standby power until the battery can be replaced or the data can be stored in permanent memory.
This example clearly demonstrates the need for an alternative form of power source to be available in electronic systems, just in case there is an interruption in their primary power source.
In automotive electronic systems there are many applications that require continuous power even when a car is parked (engine not running), such as remote keyless entry, security, and even personal infotainment systems.
These systems usually incorporate navigation, GPS location, and eCall functionality. It is easy to understand why these systems have to remain on even when the car is not moving, since the GPS aspect of these systems must be always-on for emergency and security purposes. This is a necessary requirement so that rudimentary control can be activated by an external operator when necessitated.
Consider an eCall system (take General Motor’s OnStar® system in the USA as a prime example), which is becoming more pervasive in newer automobiles across the globe, with many manufacturers having already rolled them out across their ranges. In fact, these systems became mandatory in Europe in all new cars and light trucks sold after March 31st, 2018. It’s a pretty simple bit of technology: in the event of a collision in which a car’s airbags are deployed, the eCall system automatically contacts emergency services. It uses GPS to relay the time, your location, what type of car you’re in, and what kind of fuel it uses to the authorities, while a microphone in the car allows you to speak directly to call handlers when the system is activated. These eCall system can share what direction you were travelling in when the incident occurred, allowing authorities to know which side of the freeway they need to head to in the event of a collision. All this allows ambulance, police, and fire crews to reach you as quickly as they can following an accident, armed with as much information as possible. An individual can also activate eCall by pressing a button, so if someone becomes ill (or has been injured in a collision in which the airbags haven’t deployed), help can still be easily summoned.
Storage Mediums
Having acknowledged the need for backup power in a wide array of systems, the question then arises: what are the options for storage mediums for this type of backup power? Traditionally, the choices have been capacitors and batteries.
It is fair to say that capacitor technology has played a major role in power transmission and delivery applications for multiple decades. For example, traditional thin film and oil-based capacitor designs performed a variety of functions, such as power factor correction and voltage balancing. However, in the past decade there was substantial research and development that has led to significant advances in capacitor design and capabilities. These advanced capacitors have been called supercapacitors (also known as ultracapacitors) and they are ideal for use in battery energy storage and backup power systems. Supercapacitors may be limited in terms of their total energy storage; nevertheless, they are energy dense. Furthermore, they possess the ability to discharge high levels of energy quickly and recharge rapidly.
Supercapacitors are not only compact, but they are robust and reliable, and they can support the requirements of a backup system for short-term power-loss events such as the ones already outlined herein. Furthermore, they can easily be paralleled or stacked in series or even a combination of both to deliver the necessary voltage and current demand by the end application. Nevertheless, a supercapacitor is more than just a capacitor with a very high level of capacitance. Compared to standard ceramic, tantalum, or electrolytic capacitors, supercapacitors offer higher energy density and higher capacitance in a similar form factor and weight. And, although supercapacitors require some special care, they are augmenting or even replacing batteries in data storage applications requiring high current/short duration backup power.
Moreover, they are also finding use in a variety of high peak power and portable applications in need of high current bursts or momentary battery backup, such as UPS systems. Compared to batteries, supercapacitors provide higher peak power bursts in smaller form factors and feature a longer charge cycle life over a wider operating temperature range.
Supercapacitor lifetime can be maximized by reducing the capacitor’s top-off voltage and avoiding high temperatures (>50°C).
Batteries, on the other hand, can store a lot of energy, but are limited in terms of power density and delivery. Due to the chemical reactions that occur within a battery, they have limited life with regard to cycling. As a result, they are most effective when delivering modest amounts of power over a long period of time, since pulling many amps out of them very quickly severely limits their useful operating life. Table 1 shows a summary of the pros and cons among supercapacitors, capacitors, and batteries.
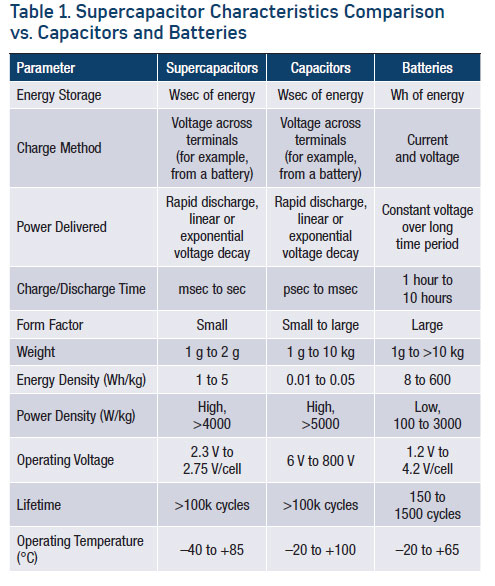
New Backup Manager Power Solutions
Now that we have established that either supercapacitors, batteries, and/or a combination of both are candidates for use as a backup power sources in almost any electronic system, what are some of the solutions available?
First of all, any IC solution would need to be a complete lithium ion battery backup power management system with the capability to keep 3.5 V to 5 V supply rails active during a main power failure event. Since batteries provide considerably more energy than supercapacitors, they are superior for applications that require backup for extended periods of time.
Accordingly, any IC solution would need to have an on-chip bidirectional synchronous converter to provide high efficiency charging of the backup battery, as well as be able to deliver high current backup power to the downstream load should an interruption on the main power rail occur.
Thus, when external power is available, the device would operate as a step-down battery charger for single-cell Li-ion or LiFePO4 batteries while giving preference to the system load. However, if the input supply was to suddenly drop below the adjustable power-fail input (PFI) threshold the IC would need to operate as a step-up regulator, capable of delivering multiple amps to the system output from the backup battery. Accordingly, if a power failure were to occur, then the IC would need power path control to provide reverse blocking and a seamless switchover between input power and the backup power source. Typical applications for such an IC would include fleet and asset tracking, automotive GPS data loggers, automotive telematics systems, toll collection systems, security systems, communications systems, industrial backup, and USB-powered devices. Figure 1 shows a typical application schematic for this purpose using Analog Devices’ Power by Linear™ LTC4040 lithium ion battery backup manager.
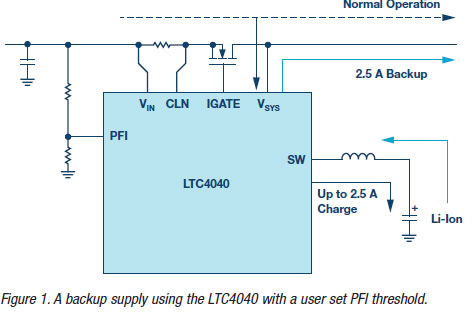
The LTC4040 also includes optional overvoltage protection (OVP) that protects the IC from input voltages greater than 60 V with an external FET. Its adjustable input current limit function enables operation from a current limited source while prioritizing system load current over battery charge current. An external disconnect switch isolates the primary input supply from the system during backup. The LTC4040’s 2.5 A battery charger provides eight selectable charge voltages optimized for Li-ion and LiFePO4 batteries. The device also includes input current monitoring, an input power loss indicator, and a system power loss indicator.
Analogous to batteries are supercapacitors. However, instead of supporting long time intervals of power loss, they are an excellent choice for systems that need high power, short duration backup power. Accordingly, any IC that supports this type of application would typically require the capability to support 2.9 V to 5.5 V supply rails during a main power interruption.
It is well known that supercapacitors have higher power density than batteries, making them an ideal choice for systems whose applications require high peak power backup for brief time intervals. By way of example, the LTC4041 from Analog Devices’ Power by Linear product line uses an on-chip bidirectional synchronous converter to provide high efficiency step-down supercapacitor charging, as well as high current, high efficiency boost backup power. When external power is available, the device operates as a step-down battery charger for one or two supercapacitor cells while giving preference to the system load. When the input supply drops below the adjustable PFI threshold, the LTC4041 switches to stepup mode operation and can deliver up to 2.5 A to the system load from the supercapacitor(s). During a power fail event, the device’s PowerPath™ control provides reverse blocking and a seamless switchover from input power to backup power. Typical applications for the LTC4041 include ridethrough “dying gasp” supplies, high current ride-through 3 V to 5 V UPSs, power meters, industrial alarms, servers, and solid-state drives. Figure 2 shows a typical LTC4041 application schematic.
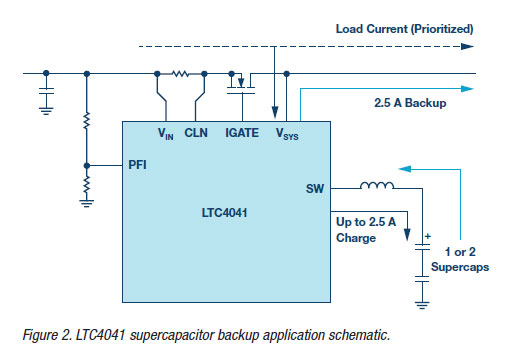
The LTC4041 includes an optional OVP function using an external FET that can protect the IC from input voltages greater than 60 V. An internal supercapacitor balancing circuit maintains equal voltages across each supercapacitor and limits the maximum voltage of each supercapacitor to a predetermined value. Its adjustable input current limit function enables operation from a current limited source while prioritizing system load current over battery charge current. An external disconnect switch isolates the primary input supply from the system during backup. The device also includes input current monitoring, an input power fail indicator, and a system power fail indicator.
Conclusion
Whenever a system must have constant availability, even if the primary power source should fail or is briefly interrupted, it is always a wise choice to have a backup power source available. Fortunately, there are many IC options for designers to consider for their specific needs, including the LTC4040/LTC4041 backup managers. These types of ICs allow an easy method to have backup power available if the main power is interrupted or lost, regardless of whether their storage medium is a supercapacitor, an electrolytic capacitor, or even a battery. The LTC4040 and/or LTC4041 have the functionality to provide an end system with backup power, whether it be a momentary burst or for extended periods of time. So, make sure that your system has the right backup when it is needed. Got it?
About the Authors
Tony Armstrong is the product marketing director for Analog Devices’ Power by Linear product group. He is responsible for all aspects of power conversion and management products, from their introduction through obsolescence. Prior to joining ADI, Tony held various positions in marketing, sales, and operations at Linear Technology (now part of ADI), Siliconix Inc., Semtech Corp., Fairchild Semiconductors, and Intel. He attained a B.S. (honors) in applied mathematics from the University of Manchester, England. He can be reached at anthony.armstrong@analog.com.
Steve Knoth is a senior product marketing engineer in Analog Devices’ Power by Linear Group. He is responsible for all power management integrated circuit (PMIC) products, low dropout regulators (LDOs), battery chargers, charge pumps, charge pump-based LED drivers, supercapacitor chargers, low voltage monolithic switching regulators, and ideal diode devices. Prior to joining Linear Technology (now ADI) in 2004, Steve held various marketing and product engineering positions since 1990 at Micro Power Systems, Analog Devices, and Micrel Semiconductor. He earned his bachelor’s degree in electrical engineering in 1988 and a master’s degree in physics in 1995, both from San Jose State University. Steve also received an M.B.A. in technology management from the University of Phoenix in 2000. In addition to enjoying time with his kids, Steve can be found tinkering with pinball/arcade games or muscle cars, and buying, selling, and collecting vintage toys and movie/sports/automotive memorabilia. He can be reached at steve.knoth@analog.com.