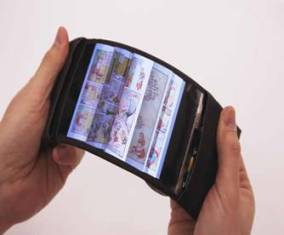
By Dr.S.S.Verma, Department of Physics, S.L.I.E.T., Longowal, Distt.-Sangrur-148 106, Punjab
In the electronic age when countless every-day electronic devices like computers, televisions, phones etc. have become an integral part of life, their body rigidity and size constraints are creating problems in their further development. Then the thoughts come to mind are what if embedding of integrated circuits and thus creating transistors were as easy as printing of a paper. In that world, abundant, cheap and flexible electronics could be embedded in objects thus making them more users friendly and leading towards the development of flexible electronics termed as “Rolltronics” or
“Roll-to-Roll” or “R2R”. Present electronic industry, which is basically a semiconductor industry; still focus its R&D primarily on making faster,denser microchips on silicon. Presently electronics chipmakers can squeeze tens of billions of transistors onto each wafer. But the economies of scale that come from such batch processing disappear with low-density applications such as the drive electronics for liquid-crystal displays, where only one transistor is needed for each widely-spaced pixel. The chip making is just essentially jostling around a pie that’s getting smaller and smaller. Instead there is a need to go out to find the game-changing new paradigm that’s what Rolltronics represents. It will cost the same amount to make this one transistor as it would to make thousands using Rolltronics. Electronic companies recently demonstrated the world’s first working silicon transistor made using this radical new manufacturing technique. In this process, a continuous sheet of flexible polymer is unrolled from one spool, covered with circuit-board-like patterns of silicon, and collected on another spool. That’s exactly what Silicon electronics giants are working for.
Rolltronics
For most semiconductors today, it is necessary to deposit the film and then pattern it with conventional lithography (in which a pattern is defined by photographic processing of a polymer masking layer that serves as a mask while the exposed areas are chemically etched into the desired pattern). These processes, which are routinely used to make integrated circuits on silicon wafers or glass plates, can all be adapted to polymer webs. The result is a much less expensive process, and products that are light, thin, rugged, and flexible (characteristics not shared by their silicon or glass counterparts). To do this, however, requires major innovations in machine design, process recipes, and system integration. Rolltronics’ core competency will be the development of processes for creating precision electronic components on thin films. Rolltronics’ technology exploits an economic opening left by today’s chip fabrication plants. In these facilities, integrated circuits and memory chips are burned onto crystalline silicon one wafer at a time.
In Rolltronics system, amorphous (non-crystalline) silicon transistors are deposited in precise patterns onto a continuously unwinding ribbon of plastic as it rolls through a vacuum chamber. Roll-to-roll/R2R processing, as the phrase implies, involves creating devices on a roll, or web, of flexible material (usually plastic, but possibly metal foil), that runs through the process machine using rollers to define its path and maintain proper tension and position. The simplest vacuum-based process is metal deposition (mainly used for capacitors and food packaging); the metal is evaporated onto the web. The typical web is a few meters wide and up to 50 km long and, for many products and processes, can run at several meters per second. Wet coating processes also form the basis for huge industries such as printing and photographic film. In order to make electronic devices, the films must be patterned. In some cases this can be done just like newspapers: by printing the material in the desired pattern.
Recently, there has been a surge of interest and activities in developing plastic substrate-based display devices to enable thin, lightweight, flexible and durable displays. A flexible plastic substrate also has significant potential in providing economic benefits in display manufacturing. Using web processing for the manufacturing of plastic display backplanes promises not only much less capital investment, but also substantially reduced manufacturing cost. As the development of emerging display technologies such as OLED, PLED, EP and Flex LCD advances, plastic substrate-based display devices have become possible and the motivation to implement a roll-to-roll manufacturing process has become very attractive.
Technological advances
A plastic demo unit square bearing one of flexible transistors, attached via alligator clips to a small, gray box has been developed. The box sends a periodic charge to the transistor’s “gate” layer, allowing current to flow from one of the transistor’s terminals to the other. When this current returns to the box, it’s amplified and used to turn a red light-emitting diode on and off. Bell Labs has developed a system for printing multi-layered plastic transistors on small sheets of flexible polymer using a finely patterned rubber stamp. Another company has fused printed transistors with sheets of electronic ink to demonstrate a working electronic paper prototype. As a display of computational power, it isn’t exactly stunning, but it does prove that Rolltronics’ transistor can—like all transistors—act as a switch, clearing the way for the manufacture of more complicated silicon-on-plastic structures. The first of the developed products will likely include backplanes for organic light-emitting displays and electronic paper systems. Putting transistors on organic substrates [like plastic] is another step in the electronics revolution that puts more functions into the daily life of the consumer. Another key advantage: the roll-to-roll process is more environmentally friendly than conventional semiconductor production technology as it uses fewer toxic solvents and cleaners and can be carried out with many recyclable materials.
Applications
Rollotronics is something that could be very beneficial to people. The applications for Rolltronics technology are widespread and varied. These transformative roll to roll processes will lead to an entirely new R2R electronics industry, with the creation of many new companies, products, and markets. Though, there are a lot of applications, like cell phone or PDA that need transistors that can be spread over a large surface area, and that is what it can be cost-effectively. The advances in Rolltronics could speed implementation of devices such as cheaper desktop displays and flexible electronic paper. These industries are planning to incorporate flexible, roll-to-roll electronics into radio-frequency ID tags, digital X-ray detector panels, biometric sensors and backplanes, the layers of electronics that control the pixels in active-matrix displays. The great advantage of roll-to-roll processing can be realized through lamination and exposure in minimizing yield losses due to debris. Various applications of Rolltronics that could be a multi-billion-dollar market in future are discussed below.
Nanoscale Memory: By combining state-of-the-art web lithography with the roll-to-roll deposition of amorphous silicon, R2R solid-state molecular memory technology can store gigabytes or even terabytes of information in a small form factor leading towards thin, flexible, inexpensive, high density, durable memory arrays. This non-volatile, random access memory (which consists of an organic solid layered between crossed microelectrodes, a thin film light source, and drive electronics) will have a lightning-fast access time.
Thin Film Transistor (TFT) Integrated Circuits: Chipmakers can squeeze tens of billions of transistors onto each wafer. But the economies of scale that come from such batch processing disappear with low-density applications such as the drive electronics for liquid-crystal displays, where only one transistor is needed for each widely-spaced pixel. Cost advantages will come with TFT based chips, using inkjet printers or roll-to-roll production. Cost per MB will here become so low that true disposable memory chips can be envisaged. Rolltronics nanoscale memory is capable of storing data at a density approaching molecular. The technology could be used to produce a PC Card module that can hold up to 64GB (billion bytes) of data. This is 100 times more data storage than PC Cards based on current flash memory technology. A larger USB memory module would be capable of storing up to 5TB (trillion bytes) of data in the same space as a standard 3.5inch hard disk. Roll-to-Roll industries will manufacture ultra-high density solid-state nanoscale memory in thin sheet format. The roll-to-roll process will make memory arrays less expensive than flash memory, and price competitive with standard hard disk drives. In addition to mainstream memory solutions these technologies sees major opportunities for applications of this nanoscale memory in the developing world.
Display components: The Internet boom and the “convergence” vision are creating an insatiable need for economical and portable displays. Rolltronics will produce the backplanes and drive electronics for OLED and bistable display panels built on flexible substrates. The goal of the program is to make displays rugged and inexpensive. One path to making displays inexpensive is to use roll-to-roll processing. One of the projects currently is to develop the processes required to build reflective liquid crystal displays on flexible substrates using roll-to-roll processing. Two of the important steps are the ability to directly etch the transparent conductor, eliminating costly and slow photolithography steps, and to assemble the display into a finished module. While the flat panel display market is currently estimated at about $38B, the printing market is well over $1T. Many companies involved in developing electronic paper-like products are projecting rapid expansion in many parts of this huge space due to the dramatic manufacturing cost savings of Rolltronics display electronics compared to current glass-based devices.
RFIDs: The radio frequency ID tag market represents an enormous opportunity for Rolltronics. It will be easier to manufacture and fabricate functional RFID devices with the advantage of greater flexibility, smaller size, thinness, lower cost, and greater adaptation to various form factors using R2R technology.
Medical and Security Devices (X-ray Detector Panels): Medical radiology is rapidly evolving away from wet-processed film, toward digital detection and display, where images are available instantly, can be transferred via networks, and are cheaper and easier to store. The cost and fragility of the current glass-based digital imaging plates limits their use in ambulances, on sports fields, or on the battlefield. Rolltronics flexible x-ray plates would eliminate the problem of fragility, while significantly reducing costs. There are also excellent prospects for flexible x-ray panels in security markets for package and bomb inspection by the military, police and airports, as well as industrial inspection.
Sensors: These include Environmental, Biometric (e.g., fingerprint), Biotech, Chemical and Industrial Sensors. The development of such sensors will fulfill the market demand for low-cost moderate-speed flexible logic circuits.
Thin film batteries: Using roll-in-roll processing to develop rechargeable lithium and lithium-ion batteries that are flat and very thin, resembling a piece of paper. These flexible batteries will be much thinner, lighter, safer, and less expensive and have higher energy density than current lithium batteries. These solid-state batteries are a perfect solution for portable computing and telephony devices, for storing electricity produced by photovoltaic solar panels, and eventually as batteries for electric cars and other machinery.
Flat-Panel Displays Slim Down with Plastic: Display manufacturers are particularly interested in the potential to manufacture large displays inexpensively, particularly with a roll-to-roll continuous manufacturing technique much like the roll-to-roll printing process. In this scenario, the plastic would roll through processing stations similar to those of a printing press, and finished displays would be cut to size. Plastic solar cells have significant advantages over the traditional silicon ones, as they offer mechanical flexibility and can be produced at a lower cost. The processing of foil into flexible solar cells can be realized by means of a continuous roll to roll process, whereas for the glass analogue batch processes are the general rule. This implies that for the flexible nc-DSC a higher throughput can be realized. Also, special applications requiring some flexibility of the solar cell, such as smart cards, come into play. Roll-to-roll adaptable techniques are needed in the processing of these devices for numerous applications ranging from lighting and signage, to low information content displays. It demonstrates the use of screen-printing in the processing of ultra thin organic layers for OLEDs fabrication.
Rolltronics and sustainability
Nearly two-thirds of our fellow global citizens currently have no access to the information or the economic benefits that the Internet and technologies have bestowed on us in developed societies. At one hand, R2R products, processes and technologies will help to bridge the economic, digital and technology divide of societies. Another key advantage of the roll-to-roll process is its more environmentally friendly nature than conventional semiconductor production technology. These developments will meet customer needs with electronics technologies that are, throughout their life cycle, substantially less harmful to the environment than existing semiconductor products. Technologies allow us to produce products that are fabricated at significantly lower temperatures, eliminate the need for lead solder connections, and allow cost-effective recycling, since all the electronics are built, to the maximum extent possible, with less use of toxic solvents and cleaners on recyclable materials.
Advances toward sustainability won’t happen by themselves. There is a need to actively pursue research and development activities that eliminate environmental impacts from products and processes. Over time, R2R processes will create additional advantages that will require effort and effective partnerships to realize. These will include significantly reduced energy and materials consumption in electronics supply chains, because whole electronic devices will be fabricated close to their point of use, from design instructions created and transmitted electronically instead of being assembled from discrete components. Significantly reduced use of hazardous materials and production of hazardous waste, as depositional processes will replace the etch and strip processes used in conventional semiconductor manufacturing. Recycling systems designed from the start to capture the entire stream of electronic waste from products at the end of their useful life will play a great role in sustainable development.
Conclusion
There is a need to design products and enabling technologies specifically to help meet the needs of the 50-75% of the world’s population not served by the electronics industry at present. Products should improve people’s lives by enabling significant improvements in communication, education, health care, and other fundamental needs. In the last few years, there has been a dramatic increase in interest in roll-to-roll (R2R) manufacturing, and a growing awareness of the advantages of R2R especially for the production of semiconductor devices. Some even call it the second semiconductor revolution, a technology that will have as much impact as the transistor. New flexible transistor technologies could bring payoffs for the whole industry. All this looks like it has a very high probability of success and if it does succeed, it could have a very big effect on making transistor arrays more available to people, for things like displays. Though, experts contends that because flexible transistors are themselves made of plastic thus will never be capable of reaching the switching speeds of silicon. These silicon-on-plastic circuits are the only viable approach for making integrated e-paper devices where the display, the backplane, and high-speed drive electronics—such as analog-to-digital converters and row- and column-drivers—are all flexible.