By Rafik Mitry for Mouser Electronics
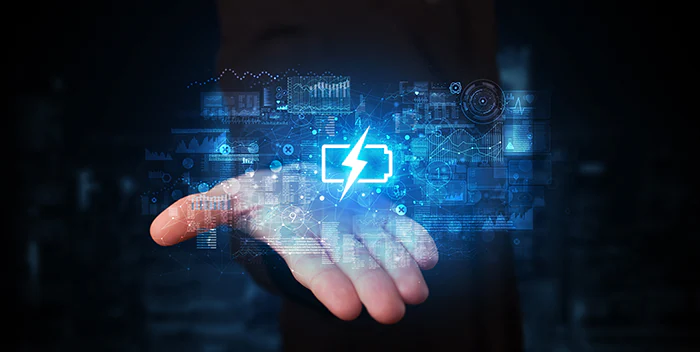
Wireless sensor nodes are being used increasingly more in our daily lives because they are suitable for use in diverse and inaccessible environments. They do not require a power supply because they are usually connected to a battery. However, batteries have a limited lifetime, after which they must be replaced. Replacing them takes time and effort and can incur considerable costs. Extending battery life would avoid this and mean that a standalone sensor node could also be used for long-life applications. This can be achieved with the help of energy harvesting. Energy harvesters can scavenge available energy from the environment, such as mechanical, thermal, or photovoltaic energy, and convert it into electrical energy. The following will show the different energy harvesting technologies and the circuits needed to store the harvested energy efficiently.
Energy Harvesting Technologies
Wireless sensor nodes (WSN) can sense, process, and transmit specific parameters. They are of great importance for environmental and structural monitoring and are also applied in the medical field to monitor the human body’s health. They are typically battery-powered and often used for long periods, which means battery life is critical.
Sensor nodes are often used in inaccessible places, so charging or replacing the batteries at the end of their lives is all the more costly and uneconomical. Several approaches exist to reduce the energy consumption of WSNs and maximize battery life. Among them are the regulation of power consumption within the WSN and programming its operation based on duty cycles. Here, the sensor node is continuously in low power mode (deep sleep) and is activated for a short time for data acquisition, calculations, measurements, and communication.
Because many emerging applications require network lifetimes of several decades, batteries are reaching their limits. If a long-term application is needed, which exceeds a battery’s lifetime, then the battery life can be extended by an energy harvester. This guarantees that the wireless sensor node becomes self-powered and will reach the required lifetime. Figure 1 shows how the lifetime of a WSN could be extended with energy harvesting.
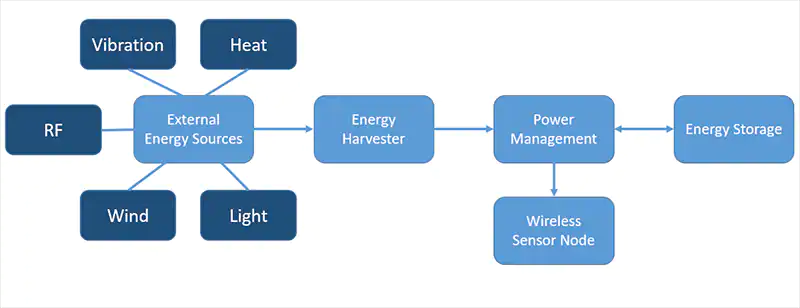
For energy harvesters to supply power to a WSN, it is first necessary to investigate sources of available ambient energy. Some primary sources of ambient energy are light, heat, mechanical vibration, radio frequency (RF), and wind. These energy sources need a transducer to convert the harvested energy to electrical energy, such as photovoltaic cells for indoor lighting, piezoelectric element for vibrations, and thermoelectric generator (TEG) for temperature differentials. A power-management circuit is then needed to store the harvested energy in a battery or a supercapacitor.
Power Management
The power-management circuit aims to connect the energy harvester to the sensor node while maximizing the harvested energy. The first aspect to consider in the power-management circuit is the harvester’s output voltage, as the output voltage varies with the type of energy harvester. For example, a thermoelectric generator’s output is a DC voltage in the millivolt range. On the other hand, a piezoelectric generator’s output is an AC voltage, which can be in the one- or two-digit volt range. In this case, the power-management circuit must rectify the energy harvester’s output and convert it into the range between 1.8V and 3.6V. This corresponds to the standard operating voltage of sensor nodes. Additionally, the power-management circuit must match its internal impedance with that of the piezoelectric generator (typically kilo- or mega-ohm) to maximize energy transfer.
Rectification
Energy harvesters that generate AC voltage are electromagnetic (radio frequency), electromagnetic (mechanical), electrostatic, and piezoelectric. To be useful in powering a WSN, the AC voltage generated by the energy harvester must be rectified. Rectification is the first component needed for the power-management circuit. Figure 2 shows a full-wave bridge rectifier circuit connected to a piezoelectric element.
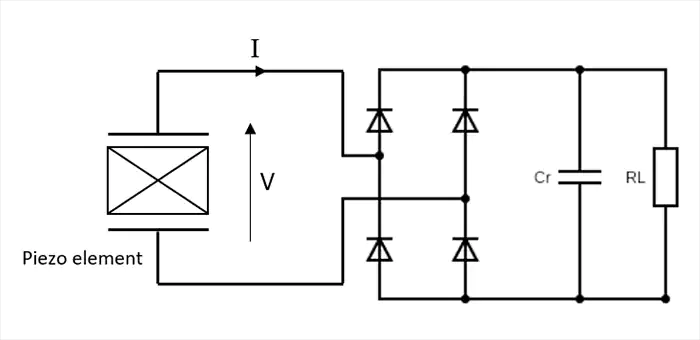
A bridge rectifier is preferred over a single diode as it provides full-wave rectification, converting the alternating voltage into a pulsating DC voltage. With real diodes, a forward voltage must be taken into consideration. This corresponds to 0.7V for silicon diodes, while for germanium diodes, it corresponds to 0.3V and drops to 0.1V for Schottky diodes. The capacitance Cr (Figure 3) serves as a smoothing capacitor. In this case, the rectified voltage is stored in the capacitor as electrical energy and supplies the load RL.
DC/DC Converter
The other main function of the power-management circuit is regulating the generated voltage from the energy harvester. If the voltage is too low, it must be increased. On the other hand, if the voltage is too high, it must be decreased. For a WSN to operate, the operating voltage must be regulated between 1.8V and 3.6V. This should be done most efficiently so that energy losses are minimized. The power-management circuit is also responsible for recharging the WSN batteries. To ease the design process, multiple products are available to handle the power-management for a WSN powered by an energy harvester.
The e-peas AEM10941 is an energy harvesting power-management integrated circuit that can extract DC power from up to 7-cell solar panels. It includes an ultra-low-power boost converter that can recharge a lithium-ion (Li-ion) battery, a thin-film battery, or a supercapacitor. The AEM10941 features an ultra-low-power cold start-up and can start to operate with input voltages as low as 380mV and input power of just 3µW. It has two supply voltages:
- LVOUT (low-voltage) with 1.2V or 1.8V for supplying a microcontroller with power.
- HVOUT (high-voltage), which can supply a radio transceiver with a configurable voltage between 1.8V and 4.1V.
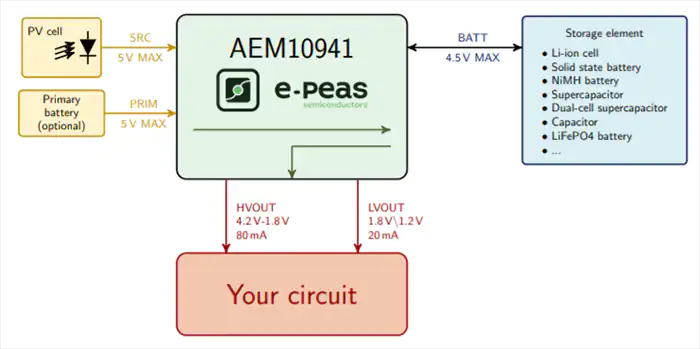
Both supply voltages are driven by a high-efficient Low-Dropout (LDO) regulator, ensuring low noise and high stability. Figure 3 shows a schematic of a typical application for the AEM10941.
Analog Devices LTC3331 is another all-in-one power-management IC circuit. The LTC3331 can be connected to an energy harvester from sources such as piezoelectric, solar, or magnetic. It features an integrated full-wave bridge rectifier and combines a buck-switching regulator and a buck-boost switching regulator. An on-chip prioritizer selects the appropriate converter to use based on the harvested energy or the battery’s available power. The LTC3331 can handle energy harvesting input voltages between 3V and 19V. It also includes a low quiescent current shunt battery charger that can charge a Li-Ion battery with the harvested energy. Figure 4 shows a circuit schematic of a typical application for the LTC3331.
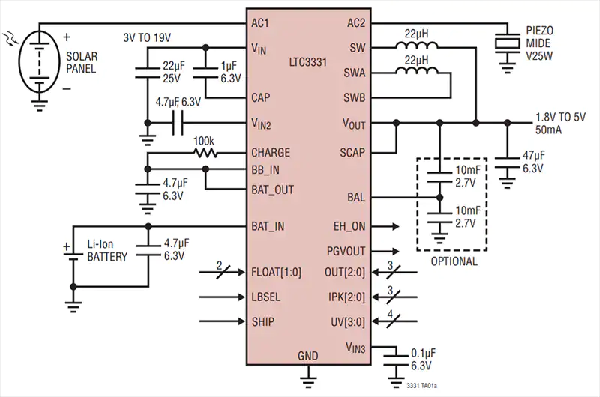
Storage
Rechargeable batteries and supercapacitors are two alternatives for energy storage that occur most frequently. Supercapacitors are similar to conventional capacitors, but they offer a very high capacity at a smaller size. They offer several advantages over rechargeable batteries. Supercapacitors can be:
- Charged and discharged as often as desired, whereas an electrochemical battery’s typical life is less than 1,000 cycles.
- Recharged quickly with simple charging circuits, reducing system complexity and not requiring full-charge or deep-discharge protection circuits.
Leakage current and self-discharge are phenomena that affect both batteries and supercapacitors. The advantage with batteries is that self-discharge is much lower than for supercapacitors because batteries have higher specific energy and can hold the charge for longer periods.
Conclusion
Now, the question to ask: Is energy harvesting worth it? This depends on how long you want to run your application. Energy harvesting has proven that it can extend the lifetime of batteries to support WSN for a more extended period, but this is only viable if the harvested energy can cover the WSN power consumption.
Author Bio
Rafik Mitry joined Mouser Electronics in 2019 after finishing his Master’s degree in Electrical Engineering at the Technical University of Munich where he also worked in research in the field of energy harvesting for three years. As a Technical Marketing Engineer at Mouser, Rafik creates unique technical content that reflects current and future technology trends in the electronics industry. Besides keeping up with the latest in technology trends, Rafik is an avid lover of aviation and tennis.
Source: Mouser Electronics