The design of high-voltage transmission lines involves optimization under a complex series of economic, electrical, mechanical, and environmental constraints. Using simulation, POWER Engineers, Inc. analyzed transmission line corona performance prior to
device manufacturing and high-voltage testing, saving both time and money.
Leveraging highly accurate simulation technology and knowledge gained from decades of analyzing in-service equipment, today’s engineers are able to investigate, model, and neutralize subtle effects that were impossible to assess without expensive and rigorous testing even just a few years ago. One area in which simulation is successfully being applied is in the analysis of the adverse effects of corona discharge in bulk power transmission lines and their associated equipment.
While analyses of this sort are usually conducted through testing in high-voltage labs or by evaluating in-service equipment, POWER Engineers, Inc. (POWER), a global consulting engineering firm, found that finite element simulation software was an effective tool for analyzing the corona performance of transmission lines. As an example, under contract to a Midwestern utility company, POWER performed detailed studies of corona performance for special 345-kilovolt transmission line equipment proposed to mitigate mechanical stress due to wind and ice loads. These studies provided a better understanding of the device’s electrical performance prior to high-voltage testing in the laboratory.
Calculating Electric Fields for Complex Geometries
Transmission structures designed to support significant lateral forces from conductor tension are called dead-end structures. Insulator assemblies mounted on these structures provide an electrically isolated connection between the structure and the energized conductor (see Figure 1). Electric fields near the surface of these high-voltage conductors and dead-end assemblies can ionize the surrounding air molecules, resulting in corona discharge. The effects of this phenomenon include energy losses, electromagnetic (AM radio) interference, audible noise, visible light, and possible erosion of materials.
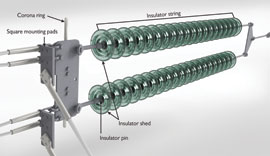
Images courtesy of Danny Frederick and Charlie Koenig, POWER Engineers, Inc.
“If you’ve ever stood near a transmission line, you’ve probably heard the buzzing noise it makes,” says Jon Leman, Senior Project Engineer at POWER. “Above a certain voltage, the electric field ionizes air molecules and creates corona discharge. Usually that’s what causes the noise you hear. Minimizing this noise and other negative effects requires reducing corona discharge.” A certain level of corona activity and associated effects are tolerable for transmission line conductors, but attachment hardware is typically supposed to be free of noticeable corona activity. Leman used COMSOL Multiphysics® to determine the electric field strength near the surface of the energized hardware and to estimate the probability of corona discharge at locations with high electric fields.
“In order to set up a lean simulation, we modeled the insulator assembly for one of the three transmission line phases and only included the first unit of the insulator string,” says Leman. POWER then used a 2-D axisymmetric model of the complete insulator string to determine the floating potential on the last insulator unit’s cap (see Figure 2). Knowing this boundary voltage allowed POWER to build a reasonably accurate 3-D model without having to include the repetitive geometric complexity and computational burden of the whole insulator string.
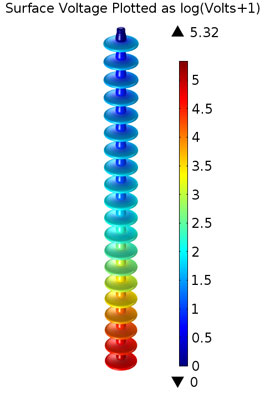
Predicting Device Corona Performance
Corona discharge is a complex physical phenomenon affected by a combination of electric field strength, device geometry, atmospheric conditions, and the surface condition of the conductor. Leman performed custom postprocessing of the electric field results by entering empirical, space-dependent equations into COMSOL to estimate the net number of air ionizations near regions with high electric fields. This allowed him to estimate the probability of corona activity. Results showed that there were two areas with electric fields strong enough to result in corona discharge: The energized pins of the insulator units and the corner of the upper square mounting pads (shown as red areas in Figure 3).
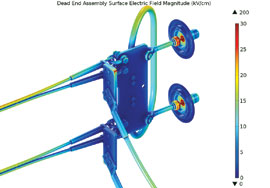
“Our results demonstrated that the outside corners of the square mounting pads are likely susceptible to corona discharge, but only marginally so,” explains Leman. “The insulator pins, however, may experience significant corona discharge.” Detailed views of the electric fields present at the insulator pins are shown in Figure 4.
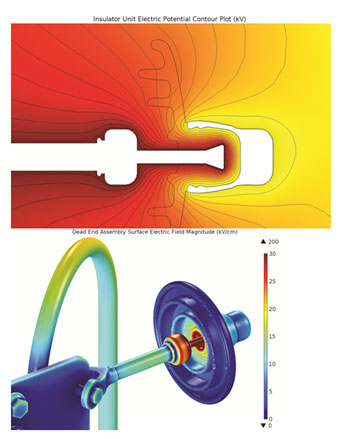
In addition to audible noise and radio interference, severe corona discharge can deteriorate the insulator unit over time, possibly resulting in loss of strength and insulating capability. “Now that we have identified where the issues are likely to occur on the hardware, it will provide an opportunity to modify the design prior to testing,” says Leman. Rob Schaerer, a project engineer at PO
WER who also participated in the project, coordinates procedures and witnesses high-voltage corona testing for clients. He says, “Laboratory testing is an important part of new hardware design, but there are costs that can be saved by up-front analysis, particularly if retesting is required. Scheduling time in high-voltage labs can be difficult on short notice, so by having a reasonably vetted design prior to testing, a project is less likely to be impacted by a design that’s found to be insufficient in the first round of testing.”
Accurate Simulations Drive Real-World Results
Simulation can be used to provide information about how a device will perform prior to its construction. When combined with results from empirical testing, engineers can arrive at a reasonable prediction of how a new device design will perform. “I have great respect for the engineers who built the electric grid without the use of modern computing. It’s important that we combine that ingenuity with the use of advanced tools to efficiently design tomorrow’s grid,” says Leman. “The COMSOL software combines the tools necessary for us to provide our customers with an accurate analysis of how the proposed transmission hardware will perform, allowing opportunities to reduce design iterations that would otherwise take place after high-voltage testing.” Examples such as this show how simulation can change the process by which devices are designed in order to reduce costs and more quickly optimize solutions.