The Sustainable Journey
By Barley Li, DigiKey
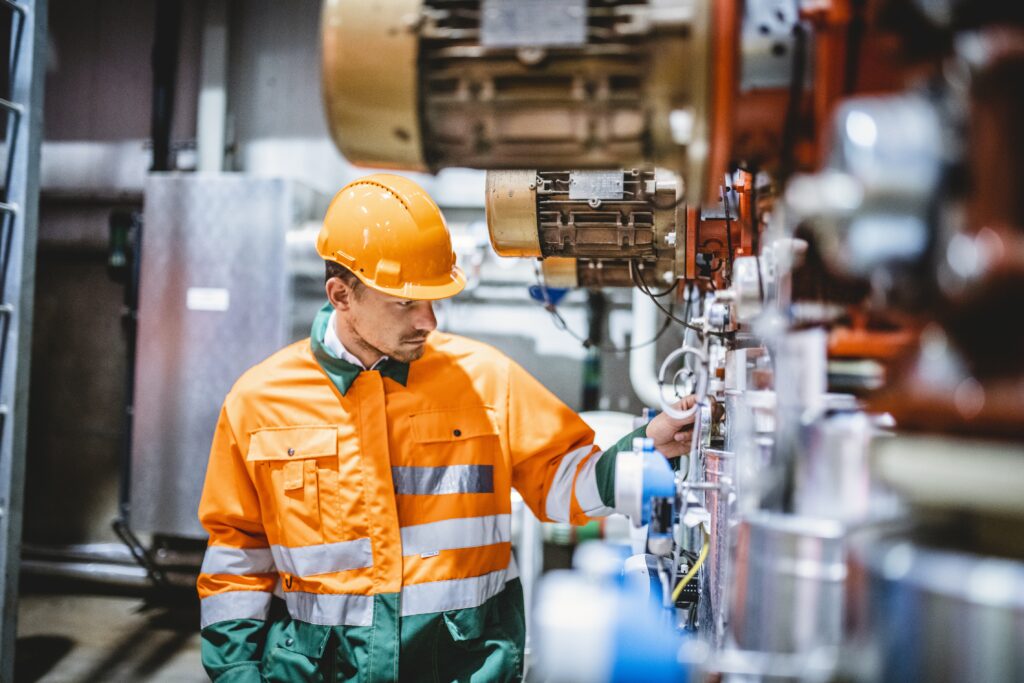
Connected sensors, robotics, adaptive drives – advanced automation concepts are key to energy-saving and resource-efficient production. To system integrators and plant operators, they provide a powerful lever for optimizing their infrastructure and processes in terms of sustainability.
The demand for energy, the use of raw materials, and – particularly in metropolitan areas – the size of the land required are the most critical factors of industrial production. On the one hand, they determine the economic efficiency of factories and plants; on the other, they are crucial for sustainable operation.
In many regions of the world, enormous efforts are being made towards limiting the use of conventional fossil fuels and replacing them by renewable alternatives. The successes to date are considerable thanks to the commitment of politics, industry, and the private sector. In Germany, for example, which aims to evolve renewables into the prevailing energy source within the framework of its energy revolution, their share of total energy consumption reached a value just above 48 percent last year [1]. According to the Federal Network Agency, the manufacturing industry accounts for more than a quarter of the energy consumption; its share of electricity demand is also comparable. Production and processing of chemicals and metals are the leading sectors [2].
These and many other manufacturing industries, including electrical and mechanical engineering as well as food production, are driven by the progress made in factory and process automation. In addition to optimizing productivity and costs, the focus is shifting more and more to parameters that result in improved sustainability of products and processes: In the context of digitalization and through the concept of Industry 4.0, they are increasingly targeting energy efficiency, the economic use of resources, waste avoidance, and the smallest possible carbon footprint.
Optimize for sustainability
Automation technology offers a range of approaches that system integrators in mechanical and plant engineering, as well as manufacturing companies, can utilize to leverage the optimization of their infrastructure, plants, and processes in terms of sustainability. The comprehensive use of sensors and their integration into the Industrial Internet of Things (IIoT) opens up a wide range of possibilities here by means of continuously monitoring energy consumption, environmental parameters, or inventories. With the help of connected sensors, manufacturing companies can, for example, track the transport of goods in real time, monitor filling levels or record condition data of machines and tools in production lines (Figure 1).
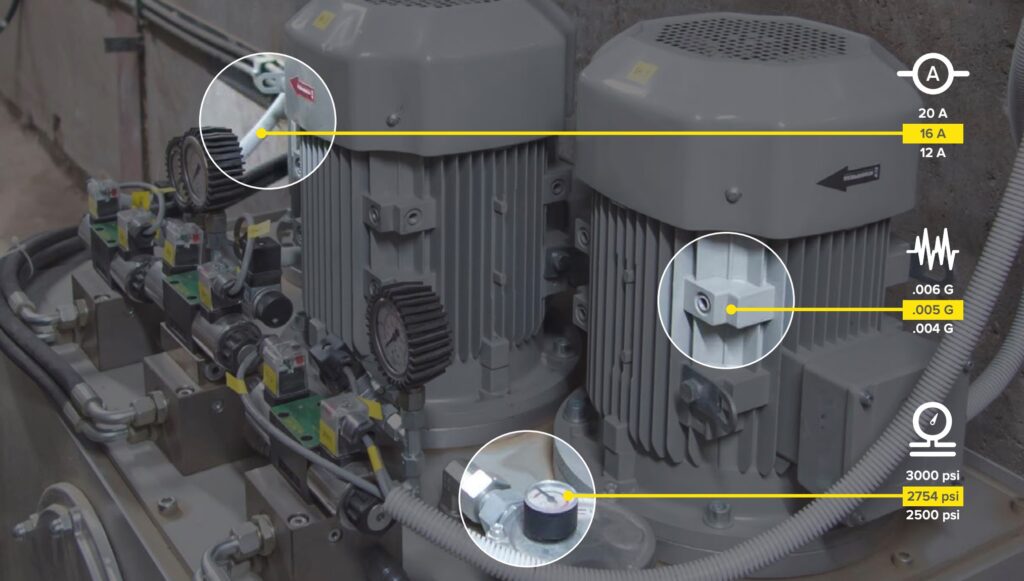
An excellent example of sensor product families that holistically support the IIoT approach to production is the Snap Signal portfolio from US supplier Banner Engineering. In general, the users’ challenge is to first identify relevant data and, in the next step, to extract it from existing equipment. If the need is identified to integrate additional sensor technology for measuring further variables, such as vibration and temperature at a drive, this should not require any changes to the existing control architecture. It is also important to standardize communication and convert all sensor and control data to a common protocol. For this purpose, the Snap Signal product line (Figure 2) offers smart sensors, signal converters, controllers, signal adapters, and wireless communication modules, as well as wired connectivity technology that enables automation engineers to plug-and-play to resolve these tasks [3].
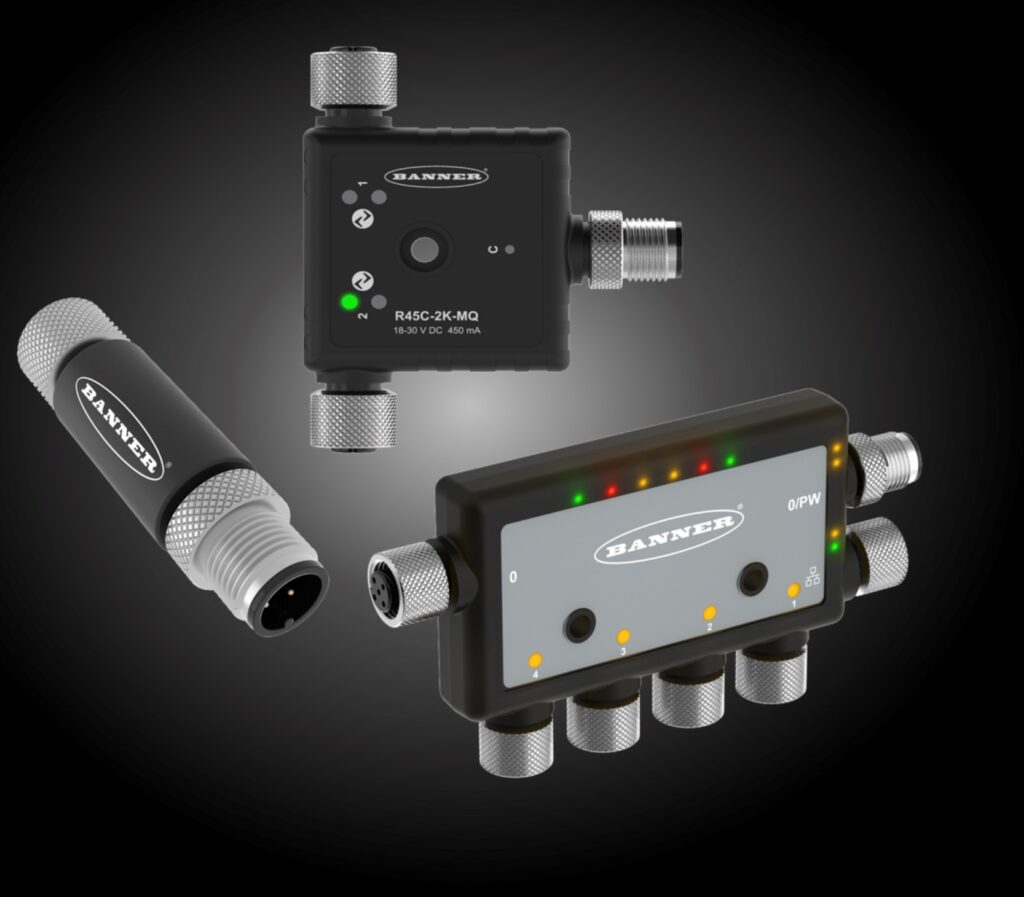
The processing and analysis of such sensor data – performed either centralized in a cloud or directly in the field – then allows conclusions to be drawn regarding error and optimization potential in the processes or the need for maintenance. In this way, energy losses can be reduced and the use of resources minimized. On the other hand, predictive maintenance makes it possible to plan service work in advance and thus reduce downtime, which in turn helps avoid additional expenditure on energy and materials.
Smarter control
In the quest for a more sustainable use of energy and industrial resources, optimizing control technology is an inevitable part of the equation. When it comes to collecting, processing, and analyzing production data in automated plants, state-of-the-art edge controllers play a key role today. Compact, scalable and connected via Industrial Ethernet, these devices can be used to implement both cloud-based and local solutions. Dedicated functions for diagnostics and energy management help automation engineers analyze manufacturing processes, identify bottlenecks, and initiate optimization measures based on industrial controllers such as theSimatic S7-1200. Advanced control algorithms as well as integrated communication and safety functions make a decisive contribution to precise process execution.
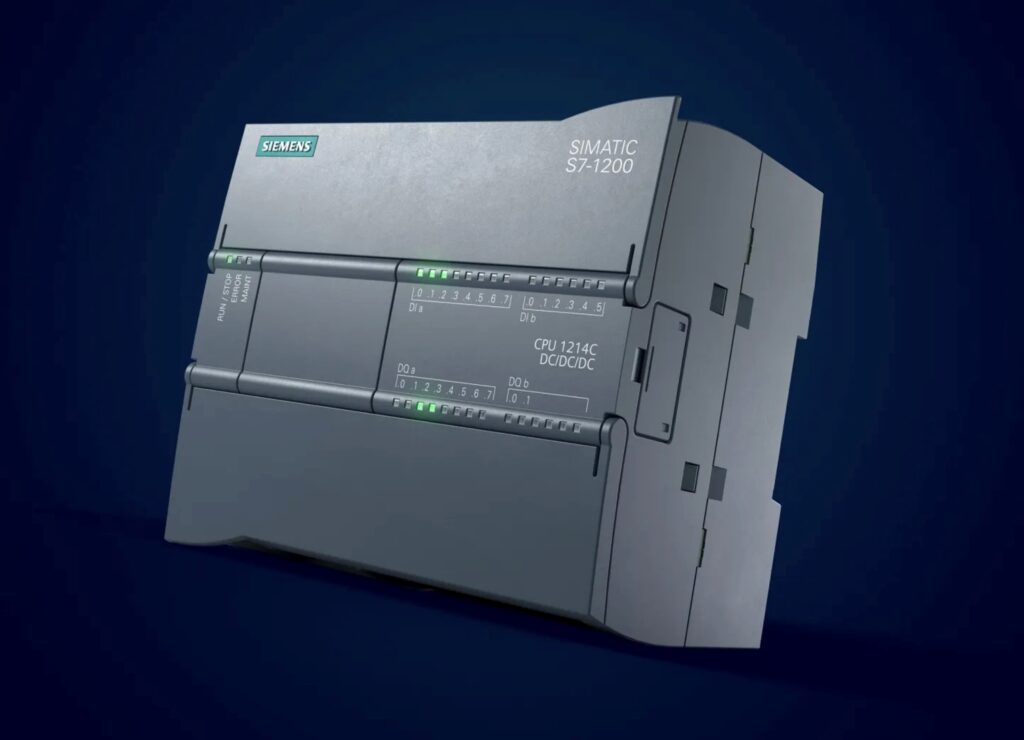
Efficient by precision
Small, agile and extremely versatile, with their compact, lightweight design and intelligent control technology, robots have a significant impact on the sustainable use of production resources. The robust and highly adaptable devices of German manufacturer Kuka’s Agilus family are an outstanding example of this (Figure 5). They come with an integrated energy supply and in several variants, some are offered as cleanroom robots, others for hygiene-critical applications or potentially explosive environments. Designed for human-robot collaboration, the robots enable highly efficient processes thanks to their very precise and repetitively accurate motion control. For example, they are ideal for minimizing the need for rework in machining processes as well as the level of rejects.
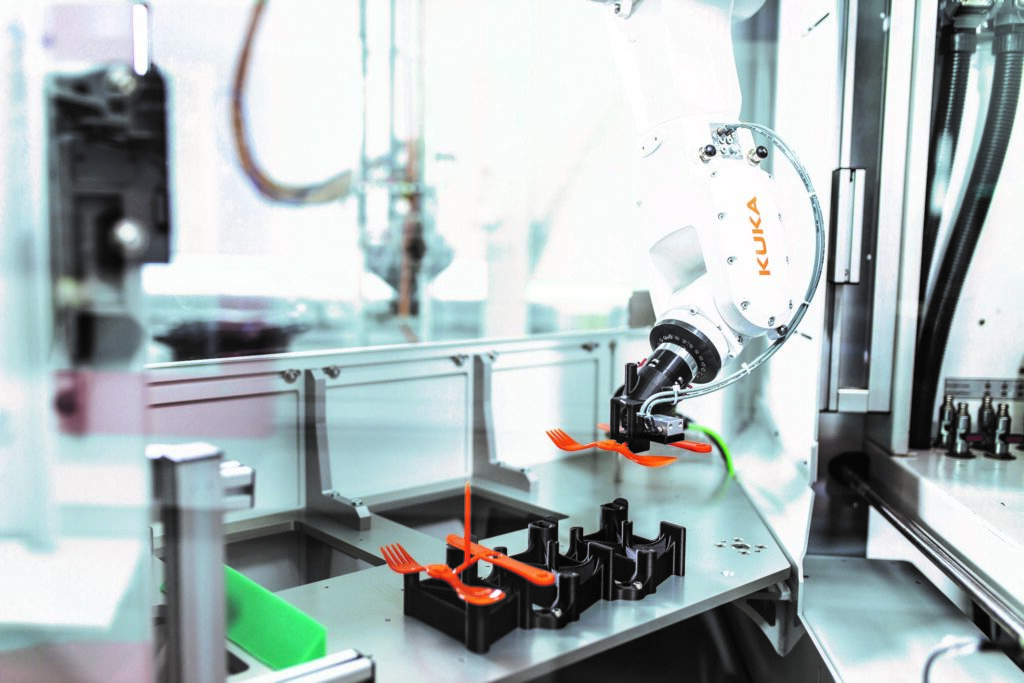
The use of such compact and variable assistants also makes sense for small and medium-sized companies as the manufacturer documents in various success stories [4]. These include a university project in which students at the University of Reutlingen/Germany are researching reusable alternatives to disposable plastic cutlery. They are supported by German injection molding expert Gindele as well as by Kuka and their system partner Robomotion. All handling around injection molding is covered by a highly flexible robotic cell, the core of which is an Agiluscompact robot equipped with a 3D-printed gripper [5].
According to the data sheet [6], the KukaAgilus KR6 R900-2six-axis robot features a maximum reach of 901 mm and a payload of 6.7 kg and it achieves a pose repeatability of ±0.02 mm in accordance with ISO 9283. Possible usage ranges from handling in conjunction with other machines, through test and measurement technology, and the application of adhesives or sealants, to assembly, pick-and-place, packaging, and commissioning. The robot occupies a footprint of 208 mm x 208 mm, weighs approximately 54 kg, is IP56/67 and ESD-protected (Electrostatic Discharge), as well as suitable for floor, ceiling, wall, and angle mounting.
Digital models, materials, and more
Beyond the approaches shown here, engineers can leverage further optimization potential by applying sustainable materials, circular economy techniques and the latest developments in the field of digitalization. The aim of circular economy is to avoid waste and residual materials and to recycle and reuse as many raw materials, components, and packaging materials as possible. Its principles can make a decisive contribution to automated plants operating more sustainably.
The concepts of the digital twin and the digital shadow are promising approaches towards identifying optimization potential without testing on real machines or plants with a high expenditure of resources. Thanks to the comprehensive digital representation of real products, plants or processes – and of their life cycles – maintenance measures can be initiated or correlations established between development, production and all other stages of the value chain. Engineers can thus simulate the behavior, functionality and quality of real objects or processes in detail – and improve their sustainability, for example by eliminating the need for physical prototypes.
Summary
Automation holds major advantages for process and production engineering in terms of productivity and costs. It is thus a crucial economic factor. Beyond this, however, advanced automation concepts and products are also key to improving the sustainability of industrial processes. From predictive maintenance to the modular factory and human-robot collaboration – this article, along with selected examples, gives an impression of the manifold possibilities.
References
1 Bundesnetzagentur: Bundesnetzagentur veröffentlicht Daten zum Strommarkt 2022, https://www.bundesnetzagentur.de/SharedDocs/Downloads/DE/Allgemeines/Presse/Pressemitteilungen/2023/20230104_smard.pdf?__blob=publicationFile&v=3, visited June 03, 2023
2 Statistisches Bundesamt (Destatis): Bedeutung der energieintensiven Industriezweige in Deutschland, https://www.destatis.de/DE/Themen/Branchen-Unternehmen/Industrie-Verarbeitendes-Gewerbe/produktionsindex-energieintensive-branchen.html, visited June 03, 2023
3https://info.bannerengineering.com/cs/groups/public/documents/literature/b_51158769.pdf, visited June 03, 2023
4 Sandra Hirsch: Success stories: How small and medium-sized enterprises benefit from their automation solutions, https://www.kuka.com/en-de/company/iimagazine/2023/05/kmu-erfolgsgeschichten, visited June 03, 2023
5 Case study: Kuka robot automates handling at injection molding machine, https://www.kuka.com/en-de/industries/solutions-database/2019/09/robomotion, visited June 03, 2023
6 Kuka Deutschland: Data sheet KR 6 R900-2, https://www.kuka.com/-/media/kuka-downloads/imported/8350ff3ca11642998dbdc81dcc2ed44c/0000290001_de.pdf?rev=dd54a65d87d644b5a7b7ff989e63ca8a&hash=CA85FC604FD471310D3017E9B4FB41FA, visited June 03, 2023