The author is the first to suggest using the term “distributed electrical power supply matrix systems“
Distributed electrical power supply systems consisting of a specified set of modules may be easily arranged on a drawing’s horizontal surface as a schematic image in order to analyse and optimize the system structure.
Recently, however, consumers designed for distributed electrical power supply system have appeared.
Their schematic images have a strongly expressed spatial matrix structure consisting of lines and columns with power supply modules located at their crossing points. Power supply systems for active phased array radars and those for supercomputers are typical examples of these rapidly developing structures.
(DEPSMS) to identify such systems. Our companies, united under the brand of AEPS-GROUP, deal exactly with such power supply systems.
The key element of the APAR DEPSMS is a transmitting-receiving module (TRM) which determines as much as 90% of the APAR price, weight and performance. Nowadays, the number of APAR TRM units in aircraft exceeds 2,000 and reaches 10,000 or more in ground equipment.
A typical modern TRM consists of UHF components (transmitter, receiver, phase shifter) and a controlling / signal conditioning microprocessor. An LF component ergonomically located in the TRM is also included. This is the bank of energy storage capacitors providing intermittent energization for the
UHF transmitter (pulsed power supply modes – duration of hundreds of nanoseconds to milliseconds, tens to 4-5 duty ratio).
It is extremely important to miniaturize the TRM as its width and height (the average length being 150 to 250 mm) together with the liquid and air cooling components (denoting the conventional side of the square formed with the TRM width and height as ΔL) may not exceed the emitted APAR half-wave length, i.e., Δ L .
Table 1 shows the typical values of Δ L accounting for the actual sizes of the cooling element for different APAR frequency ranges.
Nowadays, we have learned to accommodate UHF microcircuits in a 9-11 mm wide strip. Taking into account the necessity of a metal case to screen TRM UHF radiation from the adjacent TRMs (the EMC problem) with walls at least 0.5 mm thick (the heat removal problem), it can be affirmed that the UHF portion of the TRM with Δ L = 10…12 mm will be implemented soon.
One of the obstacles on the way towards miniaturization of the TRM (i.e., weight and APAA price reduction and EMC improvement) is the extremely difficult miniaturization of the power supply modules and their energy storage capacitors. Reducing the dimensions of transformers and throttles for power supply modules operating at frequency ranges 10,000 times less than those of the UHF portion is an extremely difficult task. For example, the best AEPS-GROUP DC/DC and AC/DC type modules for APAR have a ΔL exceeding 21.5 mm and 47 mm, respectively (Figs. 1, 2, 3, 4). This means that, as of yet, it is impossible to create a completely decentralized (which is desirable from the overall APAR reliability point of view) C and X range DEPSMS using AEPS-GROUP modules – time and expensive research are required.
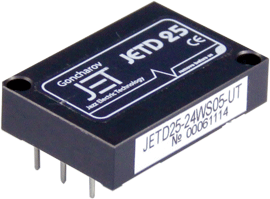
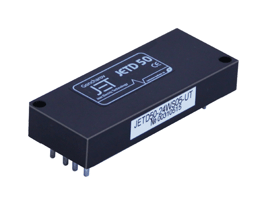
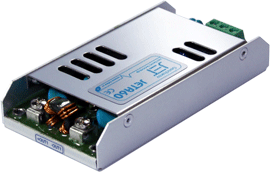
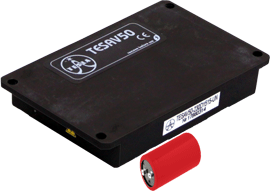
That is why only 4 to 6 GHz max. frequency decentralized APAR DEPSMSs based on single-channel TRMs are currently feasible.
Nowadays, proven technical solutions able to bypass the prohibition for APAR dimensions exceeding the emitted half-wave length can be used for APAR operating frequencies above 6 GHz. Specifically, these are multichannel TRMs. Their 2-channel or 4-channel TRM common case accommodates 2 power supply modules connected in series or in parallel providing for elementary (with all the following consequences) power supply module back-up.
In this case we obtain a decentralized DEPSMS with a reliability coefficient which is very close to 1, at the cost of having a complicated TRM and worse EMC.
Manufacturing large quantities of complicated and expensive multichannel type modules instead of single-type simple TRMs adapted for robotic production is hardly a promising business venture.
The cons also include the forced necessity of using AC/DC type centralized power supply sources for these systems, e.g., inverter-based with backed-up JETA2000 PFC (Fig. 5). The result is a two-staged inversion structure with low duty ratio efficiency.
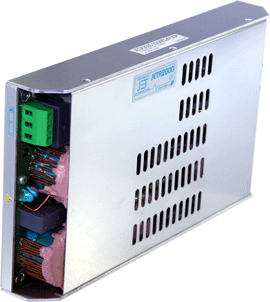
Data published in American magazines represents an excellent example of how difficulties of miniaturizing DEPSMSs consisting of more than 2,000 TRMs hamper 3D APAR implementation on the F22 RAPTOR fighter (Fig. 6).
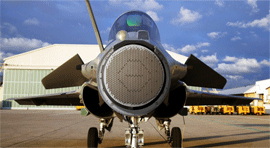
With the volume/weight of all side-looking airborne radars being 565 dm3/553 kg and with the MSDNE
AFAS 16 total power being 530W, the volume/weight of MSDNE represents 40/45 %. It should be noted here that a virtually centralized DEPSMS is used in this example. It possesses critically low reliability and has a high share in the weight of the TRM feeder-type power supply system, but it is lighter than the decentralized system.
The following are examples of some typical ground and airborne APAR DEPSMS implementations, and how the transistor technology used for the TRM UHF part impacts the key energy indicators of a decentralised MSDNE.
Design 1 (Fig. 7) was developed on the basis of GaAs UHF transistors with their typical 10 V power voltage and 0.2 efficiency. An energy storage capacitor of 3.14 nominal units volume is available (differential power voltage and efficiency are considered when comparing Designs 1 and 2).
Design 2 (Fig. 8) was developed on the basis of transistors with 28 V power voltage and 0.5 efficiency typical for GaN technology. An energy storage capacitor of 1 nominal unit volume is available.
The following parameters are common for both designs: radiated pulse power of each TRM = 10 W, max. frequency = 6 GHz, power supply module efficiency = 0.88, TRM number = 2,000, pulse duty ratio = 5.
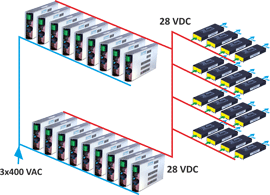
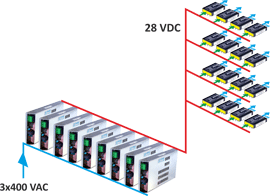
The total volume of GaAs-based DEPSMS is 10,280 nominal units or approximately 56 dm3, and together with the centralized backed-up inverter including 18 JETA2000 type modules w/ PFC connected in parallel (each having a volume of 1,200 nominal units) we have 21,600 + 10,280 = 31,880 nominal units or approximately 174 dm3.
The total volume of GaN-based DEPSMS is 4,000 nominal units or approximately 21.7 dm3, and together with 9 centralized inverter JETA2000 type modules w/ PFC connected in parallel we have 10,800 + 4,000 = 14,800 nominal units or approximately 80.4 dm3.
Conclusions
- The results show that using GaN technology instead of GaAs technology can allow for a reduction in APAR power consumption of up to 2.5 times, a reduction in thermal power dispersion of more than 8 times and a reduction in the volume and weight of all components of more than 2 times.
- Even today, in 2015-2016, the industry would be able to manufacture APARs based on singlechannel
GaN TRM operating in S, C and partially in X ranges, with 20,000 W total output UHFpower.
- JETD25, JETD50, JETA2000 modules produced in series by AEPS-GROUP could be used as prototypes of power supply modules for APAR and supercomputers.
- AEPS-GROUP TESAV50 modules without/with PFC and JETA60 modules with PFC are rather promising for supercomputers and compact APAR systems – direct operation from 220 V or 3х380 V generators without a centralized inverter becomes possible, dramatically improving dimensional and weight parameters and considerably reducing thermal power dispersion.
The author will be grateful for questions and remarks on this material. Communication should be carried out via www.goncharov-jet.com. All the data in this article have been taken from freely accessible online sources.
New products by AEPS-GROUP
9 kW AC/DC Electrical Power Supply Unit for use with diesel generators
- Input voltage: 304…456 VAC 3-phase
- Output power: up to 9,000 W
- Output current: up to 316 A
- Parallel operation function
- Current overload, short circuit, output overvoltage, thermal protection
- Remote start/shutdown
- Output voltage adjustment
- Built-in aluminium heatsink
- Built-in cooling fans
- Built-in outlet isolation diodes
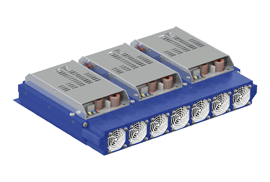
3.6 kW AC/DC Electrical Power Supply Unit
- Input voltage: 100…242 V
- Output power: up to 3,600 W
- Output current: up to 133.2 A
- Parallel operation function
- Power factor correction. Current overload, short circuit, output overvoltage, thermal protection
- Remote shutdown
- Output voltage adjustment by means of external voltage control
- Possibility of operation from an accu battery in float mode
- Built-in aluminium heatsink
- Built-in cooling fans
- Built-in outlet isolation diodes
EVA – JETA Demonstration Devices
The EVA-JETA device is a demonstration set consisting of JETA series power supply modules connected in parallel and designated for developing, under your specific conditions, technical solutions for creating powerful power supply systems based on air cooled AC/DC inverters connected in parallel (with fan cooling as an option).
The EVA-JETA is equipped with the relevant cooling system, indication, monitoring and alarm devices, it enables the development of both 2+1 backed-up power supply systems (with the possibility of hot swapping one of its modules) and power boost systems consisting of several modules connected in parallel.
The EVA-JETA demonstration set is a completely finished product and it can be used not only for developing parallel module connection, but also as a separate power supply system for your projects.
The set is protected against overheating, overload and short-circuit.