William Shenberger – Field Application Engineer, Littelfuse, Inc.
Latest bulb designs require small footprint fuses that open safely for over-current protection
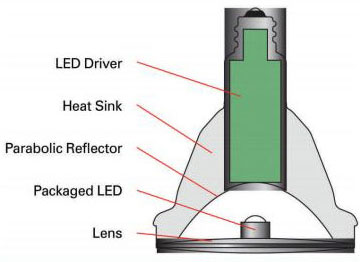
Since the earliest versions of indoor LED light bulbs were developed, their designers have faced a variety of technical challenges. These include AC-to-DC power conversion, thermal design/heatsinking, physical space constraints imposed by the current light bulb sizes, electrical transients — all in addition to the basic challenge of driving the LEDs that produce the light. One of the most significant of these challenges is providing protection from transients for both the LEDs and all the active and passive components upstream from them in the circuit. These transients are typically the result of lightninginduced surges on the AC input. These threats mean thatLED bulbs require both over-current and over-voltage protection. The growing demand for added functionality and higher light output has added to the number of components that must be placed on the LED board. The higher light output creates a demand for larger heat sinks to dissipate the heat produced by higher power LEDs. Because LED bulbs are intended to be form factor-compatible with current incandescent and CFL bulbs (such as the popular A19 bulbs typically used in household lamps), they include an AC/DC power supply circuit so they can operate from standard bulb sockets (Figure 1). Anything directly connected to an AC power source can be damaged by short circuit and overload conditions caused by component and/or circuit failures inside the bulb. In addition, lightning surges or load switching transients (originating outside the bulb) can create voltage spikes or ring waves that can stress and ultimately damage components inside the bulb.
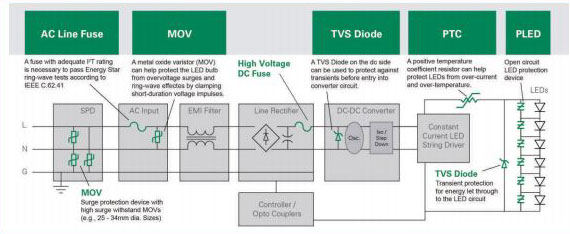
An LED-based light bulb includes the basic circuit blocks illustrated in Figure 2, (from right to left):
- Multiple, single-chip LEDs configured in series electrically, known as an LED string. Multiple strings are often connected in parallel and driven by a common power source.
- An LED string driver circuit, with corresponding controller circuitry for LED string protection, including a series positive temperature coefficient (PTC) resistor for over-current protection (OCP) and a parallel TVSdiode for over-voltage protection (OVP).
- A DC-DC converter circuit, which would include a parallel TVS diode on the input as secondary OVP for downstream components.
- A line rectifier circuit, which would include a series high voltage DC fuse on the output for secondary OCP for downstream components.
- EMI filter components.
An AC input circuit, which is made up of a line series AC fuse and a line-to-neutral parallel MOV. The AC input circuit AC fuse is the primary over-current protection device for the bulb. When properly selected for all of the required design parameters, this fuse will adequately protect all downstream components from Electrical Overstress (EOS) damage from induced transients and short circuit/overload conditions by safely disconnecting all circuitry from the AC line input. Given the tight space constraints associated with LED-based light bulb design, it’s critical to select an AC fuse for the AC input that is highly compact. A fuse’s function is to provide protection for components and complete circuits by reliably and predictably melting under current overload conditions. In other words, a fuse is intended to be the weak link in an electrical circuit. The AC fuse in series with the AC line input will provide protection against short circuit and overload conditions. Today, AC fuses are available in the smallest of form factors, with a wide choice of amperage ratings and voltage ratings. A range of additional key fuse parameters and surface mountable designs are also available to allow design engineers to choose a component that will satisfy all the requirements of the application.
An AC fuse with an adequate I2T rating is necessary to pass the Energy Star ring-wave tests according to IEEEC.62.41. The nominal melting I2T rating, measured in ampere squared seconds (A2sec), specifies the amount of energy required to melt the fusing element. Often, selecting a fuse base on the nominal melting I2t is meant for applications in which the fuse must endure large current pulses of short duration. Surge immunity testing forLED lighting applications requires complying with 8×20μs combination waveforms. Different fuse constructions may not react the same way to a surge, even if their nominal melting I2t rating exceeds that of the waveform energy. For example, electrical surge pulses produce thermal cycling that can fatigue the fuse mechanically and shorten its life. The primary over-voltage protection device for an LEDbased light bulb is an AC input circuit Metal Oxide Varistor (MOV). When properly selected for all of the required design parameters, it will protect all downstream components from Electrical Overstress (EOS) damage from induced transients and ring-wave effects by clamping short-duration voltage pulses. A MOV offers a costeffective way to minimize transient energy that could otherwise make its way into downstream components. Proper MOV selection is based upon a number of electrical parameters, including the voltage rating, peak pulse current, energy rating, disc size and lead configuration.
A designer of LED-based light bulbs needs to consider a variety of important issues in order to select an appropriate AC input circuit AC fuse:
- The first step is finding the answers to a number of technical questions about the application. In the past, understanding and answering these questions, then searching through component data sheets in order to select the right fuse for an application could be a very confusing and timeconsuming exercise. These questions include the bulb’s normal operating current, application voltage, ambient temperature, overload current level and length of time within which the fuse must open, maximum allowable fault current, and the pulses, surge currents, inrush currents, startup currents and circuit transients, etc.
- A comprehensive list of these questions and guidance in finding the answers is available in the free Fuseology Selection Guide: Fuse Characteristics, Terms, and Consideration Factors from Littelfuse.
- Littelfuse also offers the iDesign Fuse Selection Tool, a robust, web-based tool, based on the Fuseology Selection Guide. It is designed to help circuit designers identify the optimal electronic fuses for their projects. The iDesign tool offers a fast, intuitive way to identify the best component for an application, find parts documentation, and order part samples for prototyping. It walks designers through a fuse selection process that quickly narrows the available options based on the inputs provided.
- It’s crucial to know early in the design process in which market or markets the bulb will be sold. Depending on whether the bulb is intended for use in the United States, elsewhere in North America, Europe, Asia, or somewhere else, different standards will govern design and testing requirements. See “Can Your LED Bulb Live Up to the Standards?” for guidance on determining the agency approvals and certifications required for the bulb based on geography.
- Determine the size limitations that might affect the fuse that can be used. Fuses can be packaged using a variety of methods, but surface mount designs are the most common form factor for LED lighting applications. Fortunately for circuit designers, smaller footprint fuses are now available to protect the AC input, some just half the size of the smallest fuses previously available.
- The fuse temperature generated by the current passing through the fuse increases or decreases with ambient temperature change. Be aware that the “ambient temperature” of the fuse is not, as the name might suggest, the same as the “room temperature.” Instead, ambient temperature is the temperature of the air immediately surrounding the fuse, which is often much higher than the room temperature because the fuse might be enclosed (such as in a fuseholder) or mounted near heat-producing components on the LED board. For ambient temperatures around 25oC, it’s generally recommended that fuses be operated at no more than 75% of their nominal current rating. Fuses are essentially temperature-sensitive devices, so even small variations in temperature can greatly affect the predicted life of a fuse when CIRCUIT PROTECTION it is loaded to its nominal value, usually expressed as 100% of rating.
- Determine the application’s required breaking capacity. This may also be referred to as the interrupting rating or short circuit rating (I2t value). This is the maximum approved current that the fuse can safely interrupt at rated voltage. During a fault or short circuit condition, a fuse may receive an instantaneous overload current many times greater than its normal operating current. Safe operation requires that the fuse remains intact (no explosion or body rupture) and clear the circuit.
- Be sure to allow sufficient time for thorough application testing and verification before production. If the initial design fails any of these tests, make sure there’s enough leeway in the schedule to modify the design and retest.
- Finally, the designer must coordinate the fuse with the downstream OVP and the LED string driver circuit. Transient suppression must be considered at the beginning of the LED light bulb design process. The selected fuse must withstand the energy of the transient at the specified level so that the LED string driver circuit capabilities are not adversely affected. The AC input circuit fuse and MOV, when properly coordinated, provide a transient protection solution that allows the needed over-voltage clamping capability to occur without the fuse opening and yet safely protect the downstream circuitry and result in minimal disruption to the LED string driver circuit, including the LED string itself.
- However, there will be instances when specific LED light bulb operational circuitry is just not able to survive the required transient event levels. In these cases, adding a secondary TVS diode for over-voltage protection, as noted previously in the section on the DC-DC converter block, is a proven solution that further clamps the “let-through” energy from the MOV. For the most extreme cases, there is even an additional OCP device (the high voltage DC fuse in the line rectifier block output, shown in the center of Figure 2) and LED string OCP device (a PTC in series with the LED string), OVP (TVS diode in parallel to the LED string) and open circuit LED protection (individual LEDs with a parallel PLED) in order to provide the even more robust circuit protection.
- Coordination of the fuse with the over-voltage protection and the LED driver
- Transient voltage suppression must be part of the initial design process; the device chosen must dissipate the impulse energy of the transient at a sufficiently low voltage so that driver circuit capabilities are not affected.
- TVS diodes are among the most commonly used type of suppression device. A TVS diode is specifically designed to protect electronic circuits against transient over voltage events. Being a silicon avalanche device, it is available in both uni-directional and bi-directional configurations. In the unidirectional version, the specified clamping characteristic is only apparent in one direction, with the other direction exhibiting a forward voltage (VF) characteristic similar to a conventional rectifier diode. LED lighting power supplies (drivers) typically need TVS diodes at one or more locations in their circuits.
- The destructive potential of transients is defined by their peak voltage, the follow-on current, and the time duration of the current flow. The time required for a transient suppressor to begin functioning is extremely important when it is used to protect sensitive components like driver ICs and LEDs. If the suppressor is slow acting and a fast-rise transient spike appears on the system, the voltage across the protected load can rise to damaging levels before suppression begins.
When selecting a TVS diode, several important parameters must be considered:
- Reverse Standoff Voltage (VR).
- The most important of these is VR, which should be equal to, or greater than, the peak operating level of the circuit (or the part of the circuit) to be protected. This will ensure that the TVS does not clip the circuit drive voltage.
- Peak Pulse Current (IPP). IPP is the maximum current the TVS can withstand without damage and is usually stated in reference to an exponential waveform such as 10×1000μs. The required IPP can only be determined by dividing the peak transient voltage by the source impedance.
- Maximum Clamping Voltage (VC). VC is the peak voltage that will appear across the TVS device when subjected to the Peak Pulse Current (IPP), based on the referenced exponential waveform.
- The failure mechanism in a TVS diode is a short circuit. Therefore, if the TVS diode fails due to a transient, the circuit it’s in will still be protected.