The Wireless HART (Highway Addressable Remote Transducer) is a communications protocol designed for the industrial automation & process control applications.
It is a wireless sensor networking technology based on the HART protocol. The Wireless HART was defined for the requirements of process field device networks and it is developed as a multi-supplier, interoperable wireless standard.
eInfochips, with strong experience in building comprehensive, critical, and connected solutions, brings together expertise on multiple tools and technologies to meet product design challenges.
This article provides introduction and design approach for field devices and network manager.
Wireless technology is developed gradually from the consumer market to industrial operations. Since the requirements for operation of wireless technology in industrial applications differ greatly from consumer applications, industrial wireless implementation has not been widely used until recently because there is no common standard has been developed. Typically, each wireless system installed today is proprietary. Different keys exist in parallel, which raises planning, maintenance and integration efforts. This has changed with the preface of Wireless HART. This is the first standard for industrial process automation. Wireless HART is an open wireless device-actuator network standard for industrial process monitoring and control that requires real-time data communication between sensor and actuator devices. Most important features of a Wireless HART network comprise centralized network management architecture, multi-channel TDMA- based wireless mesh networking technology operating in the 2.4 GHz ISM radio band, redundant routes, and evading of spatial reuse of channels for enhanced reliability and real-time performance. Wireless HART was officially released in September 2007 (as a part of the HART 7 Specification).
In this article, we have tried to give an introduction to the concept of Wireless HART and share our hands on experience in building hardware prototypes for this specification including top level architecture of typical wireless Hart, block diagrams of field device & network manager, challenges such as ultra low power hardware design for longer battery life, longer RF range, etc.
Concept of wireless HART architecture
The Wireless HART is a wireless sensor networking technology based on the Highway Addressable Remote Transducer Protocol (HART). Wireless HART was defined for the requirements of process field device networks.
Below figure is the top level architecture of Wireless HART network:
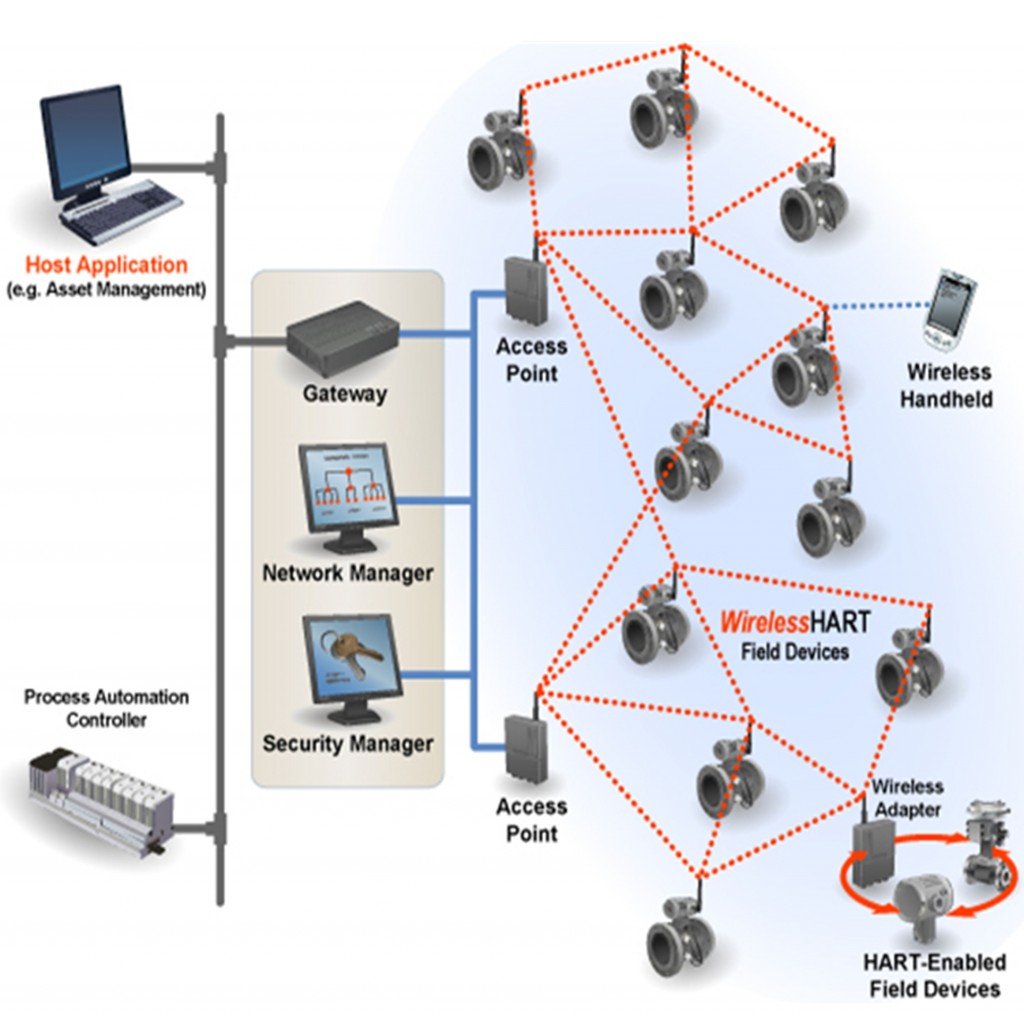
The Wireless HART has defined four communication concepts:
- Mesh Network
- Time Division Multiple access(TDMA)
- Frequency hopping
- Network Management
Mesh Network
The Mesh Network is a concept where all wireless sensors in the field form a network, and a message can be communicated through this mesh network. The real sender of the message sends it to its nearest neighbor. This recipient forwards it to the next neighbor until the message reaches the final recipient.
The mesh network has two advantages:
- The covered area and range of network is larger
- There is always alternative path when link between two wireless field devices fails or data gets corrupted. This is called self healing network.
Time division multiple access (TDMA) and Frequency hopping
To avoid message collisions between the field devices in the mesh network Wireless HART uses combination of two concepts, TDMA and frequency hopping.
The TDMA of Wireless HART divides a second into 100 slots, 10ms each. The entire network is synchronized in these slots. This enables the wireless sensors to start the communication in a much defined time. If no communication is needed, field device go to a sleep mode to save battery power. This also allows other field devices to send data.
In Frequency Hopping all 15 defined channels of IEEE802.15.4 standard are used. During one slot, multiple wireless Field devices can transmit in one of the available channels in the 2.4GHZ ISM Band. So, 15 wireless sensors in a Wireless-HART network can send during the same time slot.
Network Management
The Network Manager configures the mesh network between the wireless field devices. Also, it organizes which field device is allowed to send a message on which channel. Organized in this way, the communication in the mesh network is best optimized.
The Network Manager manages and monitors the network continuously and reacts to deviations in the operation. The Network Manager is responsible to assure the best possible operation of the Wireless HART network.
The Solution
The solution architecture needs to capable to collect the information from WHART sensors and the massages can be routed to central network manager which should capable to manage and monitors the entire network and communicates with host application interfaces.
Solution Components
Each Wireless HART network contains three main device types:
Wireless field devices
These devices are connected to process or plant device. This device could be a device with Wireless HART built in or an existing installed HART-enabled device with a Wireless HART adapter attached to it. A wireless field device typically consists of two devices.
- Wireless sensor adopter: This device can access the data through sensors and converts into a digital form then pass it to wireless HART module via serial interfaces.
- Wireless HART module: This wireless module receives the data from WHART sensor adopter and transmits the data to gateways/network manager over wireless HART network.
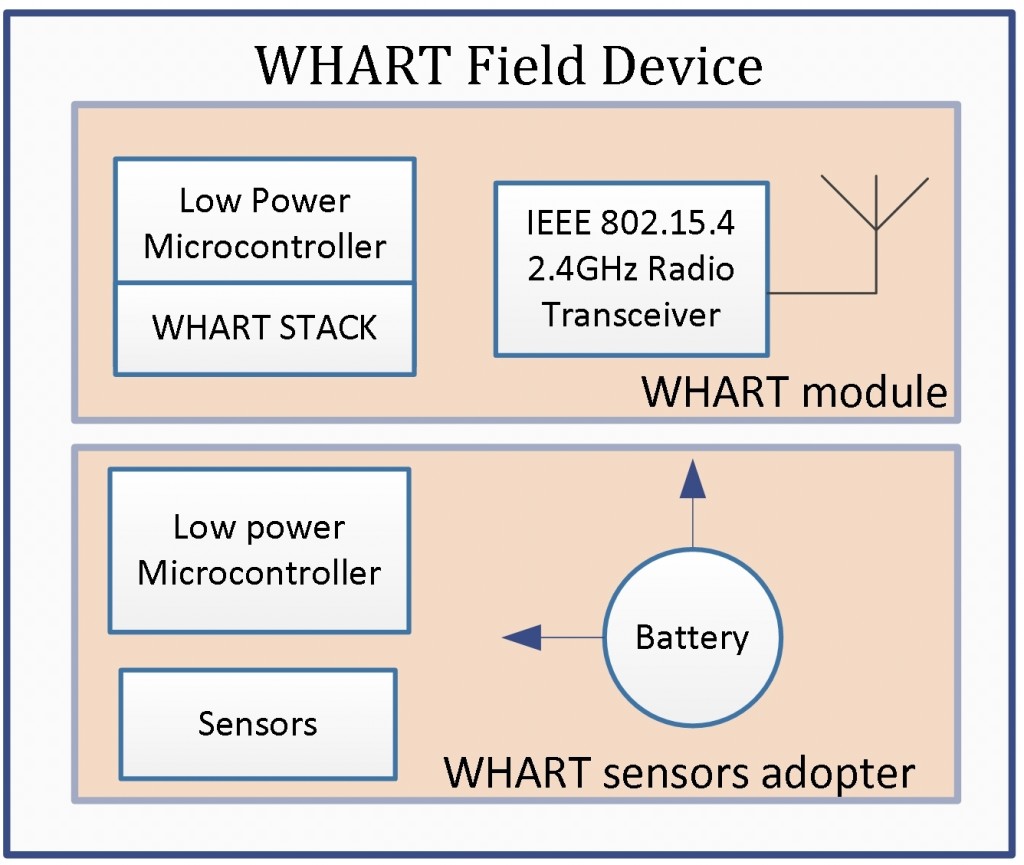
Gateways
Gateways enable communication between field devices and host applications connected to a high-speed LAN or existing plant communications network.
A Network Manager
Network manager is responsible for constructing the wireless mesh network, handling communications between field devices, managing message routes, and monitoring network health.The Network Manager can be combined into the gateway hardware.
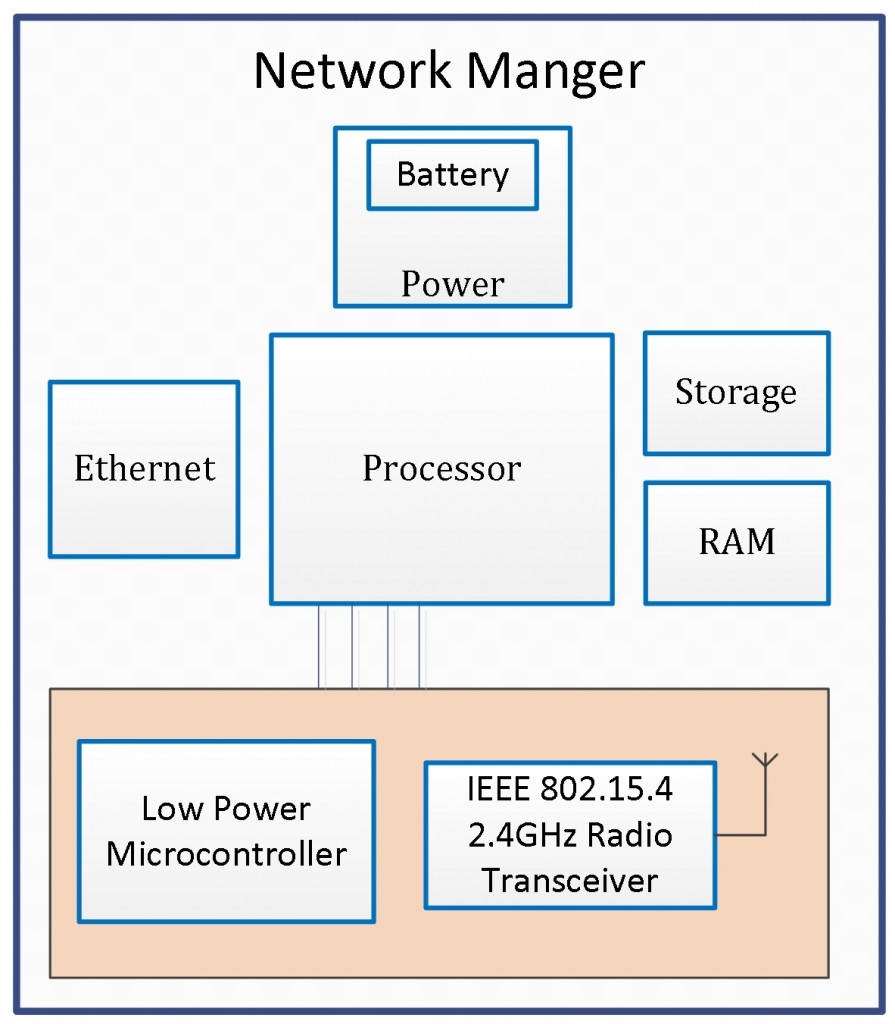
Derived benefits
- The reliability of communication path between the wireless field devices has been improved through the alternative communication paths.
- The network range area which can be covered wirelessly is increased by implementing mesh topology.
- The throughput of the network is increased by using 15 channels 100 times per second
- Due to low power IEEE 802.15.4 complaint radios for implementing wireless HART network field devices higher battery life time can be possible.
Hardware Design Challenges
Here are certain challenges product design teams are likely to face in building the architecture for a wireless HART based network.
Battery life
To derive the battery life time of wireless HART field device the designer needs to examine the following things
- First thing that needs to analyze the current consumptions of each component in the wireless HART field devices such as low power microcontroller, radio, sensors and other circuits etc.
- Due to various process of the WHART protocol consumes energy. These can be divided into two groups. The first group defines processes for network management such as joining, synchronization, advertising and routing and the second group derives the processes that are used for real data transmission.
- Derive the current consumption of each individual process defined in WHART protocol by the help of defined hardware architecture.
- Calculate the average current for single field device and mesh network routing current by analyzing current consumptions of each activity in the WHART protocol. Typically WHART protocol divides second into 100 slots 10ms each. Practically in real payload transmission and network activities the field device consumes peak currents (>35mA) and If no communication is there they go into deep sleep mode (µA range) to save the battery energy.
- The WHART mesh network can be divided into hopes structure. Hopes current of field device in the mesh network delivers the battery life time of wireless HART field device. This is the reason wireless HART field devices consumes ultra low power consumption and it leads to higher battery power consumption.
Form Factor
Considering the complexity and flexibility envisaged in the architecture and design of the solution, our teams recommend certain approaches that would overcome the challenges mentioned above.
- Use ultra low power microcontrollers within built RF transceivers, thereby reducing the PCB size and BOM cost.
- Use on board inverted antennas, thereby reducing the PCB size and costs.
Regulatory Requirements / Certification
In order to certify the product the following regulatory requirements needs to be done for the respective countries.
For USA
- EMC standard for FCC as per the FCC part 15 subpart B
- Wireless standard for FCC as per the FCC part 15 subpart C
For European countries
- EMC standard for ETSI as per the EN 301489-1,EN301489-17
- Wireless standard for ETSI as per the ETSI EN 300328
Summary
Wireless HART network provides very good benefits and are listed below:
- Elimination of cabling and installation costs of existing wired plants.
- Ensures improvement of production quality and safety in plants.
- Greater flexibility and efficient maintenance.
- Low cost solution and easy to operate.