The cobot market with an annual 50% growth is now the fastest growing segment of industrial robotics, forecast to hit $3B in global revenue in 2020.
Collaborative robots (also called co-bots) are robots designed to assist humans in the performance of their tasks – i.e., to work jointly on a project. Because co-bots are almost plug and play – and very low-cost – SMEs are buying and the segment is quickly growing.
There are many reasons for the emergence of collaborative robots: to handle ergonomically challenging tasks, using them alongside humans in small-spaced electronics assembly lines, using them because they are affordable, using them because they are plug and play and easily trainable, using them for their flexibility to handle short runs, and using them to offload repetitive and boring jobs.
Co-bots are also emerging because sensors and computer power have become so cheap that they are driving down the cost of robots and making them more available to businesses of all sizes. Most professional service robots are collaborative by design, hence co-bots aren’t just for SMEs or for manufacturing use. Offices, homes, labs, warehouses, farms, distribution centers, hospitals and healthcare facilities are all enabling service robots to help them do their jobs better. The market is open-ended but current uses for co-bots include machine tending, material handling, assembly tasks and packaging. They also pick and place, count and inspect. As more co-bots are deployed, more uses will be discovered.
Understanding Cobots
Cobotics stands for human-robot collaboration in professional contexts – in other words: direct interaction between people and robots in the same working environment.
A new kind of technology, Cobotics marries the advantages offered by human actions with the very latest robotics technology.
Ultimately, this makes it possible for Cobotics to create completely new production and automation processes – within the current realms of robotics, but also beyond. (> Cobotisation)
Superior sensitivity, bionic motions and on-the-fly switches between autonomous and supervised work – these are the hallmark of Cobots. Many Cobots are have their own inbuilt interaction systems and learning functionality (teaching by demonstration).
This is highly useful for mobile service systems, human-robot collaboration in manufacturing or surgical assistance. These lightweight robots are extremely adaptable and mobile, making them perfectly suited to a variety of application scenarios.
Market Potential
At present, sales of collaborative robots represent 5% of the overall robot market but with strong growth expectations for the future. In fact, the market acceptance of collaborative robots and also drones are expected to be significant drivers in non-industrial robotic growth.
The collaborative robotics sector is expected to increase roughly tenfold between 2015 and 2020, reaching over $1 billion from approximately $95M in 2014. Insiders suggest more rapid growth: that collaborative lightweight robots will become the top seller in the industry in about 2 years, selling hundreds of thousands and with prices falling to the $15,000-$20,000 level. TechNavio, a British market research firm, in their September, 2015, $2,500 report, forecasts the global collaborative robots market to grow at a compounded annual growth rate (CAGR) of 50.88% to 2019.
In response to growing demand for collaborative applications that pair machines and humans for a single purpose, suppliers of collaborative robots are addressing the regulatory, technical and business challenges facing this new asset class. Manufacturers of traditional industrial robots, meanwhile, are responding with new collaborative capabilities of their own.
The pioneers and early adopters
The automotive industry first pioneered this human-machine collaboration. A couple of years ago, BMW started to deploy cobots on car door assembly lines. In 2013, Volkswagen introduced cobots to install glow plugs in its engines. Last year, Audi introduced 1.40 m tall, two-arm cobots on its Ingolstadt, Germany assembly lines.
Cobots are now entering the aerospace industry. Boeing and Airbus are increasingly interested in using collaborative robots for the assembly of entire wing sections. Boeing already deployed two cobots on its 777 assembly line in Seattle. Airbus recently launched the Futurassy project in its factory in Puerto Reale, Spain. Nextage, a semi-humanoid, two-arm cobot designed by the Japanese firm Kawada, is being used to assemble A380 elements.
So far, four suppliers of these robots have emerged:
- Rethink Robotics, Boston, is a seven-year-old company that put collaborative robots on the map with its Baxter series of two-armed robots, each arm with seven axes. Baxter has 360° sonar and a front-facing vision system to detect human presence and perform its tasks. Its “servo-elastic” control halts motion if an arm meets resistance of less than 1 lb. Its anthropomorphic “face” is an LCD screen with two eyes and a range of expressions that indicate the robot’s “state of mind” and direction of motion.
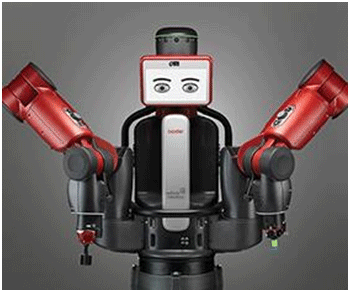
Last year, Rethink commercialized Sawyer, a one-armed cousin of Baxter that has longer reach, higher payload capacity, and a more sophisticated vision sensor on the seven-axis arm.
- Universal Robots is a Danish company with a U.S. office in E. Setauket, N.Y. Introduced in 2014, its UR5 and UR10 have one six-axis, articulated arm with true absolute encoders and eight adjustable safety-related functions, as well as 32 built-in I/Os. With a working radius of 33.5 in. (850 mm) and payload capacity of 11 lb (5 kg), the UR5 arm weighs in at about 40 lb. The larger UR10 has a working radius of just over 51 in. and payload capacity of 22 lb. The smaller UR3 model was launched last year.
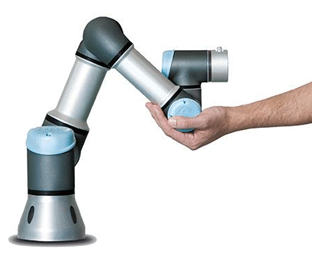
- Kuka Robotics, Shelby Township, Mich., is the U.S. arm of a German supplier of articulated robots. It introduced the collaborative IIWA (Intelligent Industrial Work Assistant) series with the LWR 5 (Lightweight Robot) in 2013. These robots made their first splash in plastics at the Fakuma 2015 show in Germany last fall, where they appeared as part of the Arburg and Boy Machines exhibits.
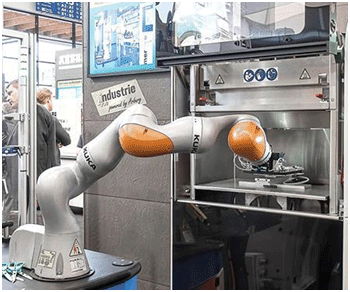
- Fanuc America, Rochester Hills, Mich., just introduced its first collaborative robots in November. The CR-35iA Collaborative Robot is a six-axis arm described as “the industry’s first 35-kg (77-lb) payload, force-limited collaborative robot designed to work alongside humans without the need for safety fences.” It has a soft outer cover to minimize impact force and is said to stop safely when it touches a human operator or other obstruction. It can integrate Fanuc’s iRVision so it can see what it is picking up.
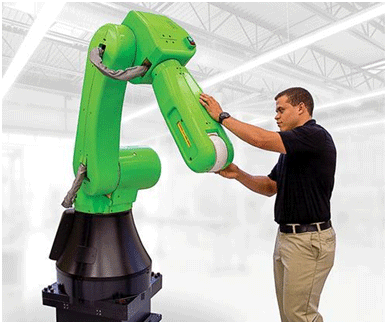