By Mark Patrick, Mouser Electronics
One of the most useful real-world parameters to measure is movement. Sensors that detect motion and vibration can provide valuable insights, giving rise to a new era in condition monitoring and preventative maintenance. This article explores the sensors being used to enable those insights.
The world relies on industrialised manufacturing and the automation of mechanical tasks. It is hard to think of any vertical that doesn’t require some level of automation. The mechanisation and, more recently,digitalisation of control systems underpins industrial automation. It takes automation into new levels of reliable repeatability, with which comes efficiency. That digitalisation is in turn enabled by advanced sensors.
Data generated by sensors can be used to improve processes, and one of the most critical elements of an automated industry is asset maintenance. Knowing if and when a piece of machinery will fail can avoid much longer and costlier downtimes if the failure escalates. This predictive maintenance is entirely reliant on good data, some of which may come from operators but, increasingly, it is coming from networks of sensors.
Adopting predictive maintenance is a strategic decision, one that touches almost all electrical and mechanical elements of a process. They must be designed to interoperate systemically to deliver the data needed. One key element in these systems is the effect vibration can have on electromechanical systems. The vibration may be inherent in the operation, as many machines demonstrate. Secondary vibration may be caused by wear in the primary systems, and this, too, needs to be monitored.
Vibration is characterised by movement, typically oscillation. Each cycle will have a definite pattern, with a signature that can be described through acceleration. Monitoring acceleration and deceleration are now easily achieved using sensors specifically designed for this paradigm, the accelerometer. As technology improves, accelerometers have also evolved; they are now smaller, lighter, and more accurate, which means they are no longer restricted to being located on large moving parts. They can easily be applied to smaller masses, such as spinning wheels, moving platforms, and even covers and flaps.
Anything that moves can now be monitored. Itsmovement contributes to the data set that, holistically, can accurately depict the status of practically any process. This is how predictive maintenance is evolving, but it also illustrates how important it is to select the right type of sensor in any specific application.
Understanding vibration sensor selection
One of themain technologies used in vibration sensors to measure acceleration is the piezoelectric effect. Sensors based on the piezoelectric principle are typically constructed using Lead Zirconate Titanate Ceramics, or PZT. Polarisation aligns the dipoles in the material to make the crystal structure act as a piezoelectric material. Their construction makes them ideal for use in industrial applications where the temperature range can vary significantly.
Piezoelectric (PE) accelerometers are triggered when the material is stressed. In practice, this is often achieved through a known mass, either compressing the sensor or applying shear stress on the PE material. The compression type is known to have a higher thermal drift than the shear-style and suffer more from the base strain. The PE element in a shear design sensor is isolated from the base and is also affected less by thermal changes. Of the two, the relative benefits of the shear mode sensor mean it is often favoured in condition monitoring and preventative maintenance applications.
The alternative to PE is variably capacitance (VC). Two plates form one part of the capacitance, with the load mounted in between. This is the main technique used in the construction of MEMS (micro-electromechanical systems) sensors. Any vibration causes the load to move, resulting in a change in capacitance. Unlike the PE sensor, the output of a VC sensor needs to be interpreted by an analogue frontend (AFE) or an equivalent circuit. This conversion process introduces additional noise into the system and, as the signal generated by the change in capacitance is small, the signal to noise ratio can be a limiting factor.
Assessing the sensors
A study conducted by TE Connectivity looked at both types of sensors to see how they measured up against one another. Both of the sensors selected for the test had a full-scale operating range of ±50g.
For the assessment, a high-frequency shaker designed for calibration purposes was used, and tests were conducted across a vibration frequency range of 5 kHz to 20 kHz, with a ±1 dB variation in amplitude. The test measured the output of the sensors across the frequency range selected, and the results indicated the working bandwidth of each sensor. The VC MEMS sensor demonstrated bandwidth of around 3 kHz, while the PE sensor demonstrated a useful working bandwidth of over 10 kHz.
To achieve laboratory conditions, the tests were conducted in an isolated noise chamber at the same time to remove the possibility of any outside influences affecting the results. The test equipment used included measurement devices able to capture vibrations with micro-g resolution. A total of four sets of tests were carried out across four bandwidth ranges, the results of which are shown in Figure 1. The results also show the residual noise that was measured in each of the four runs.
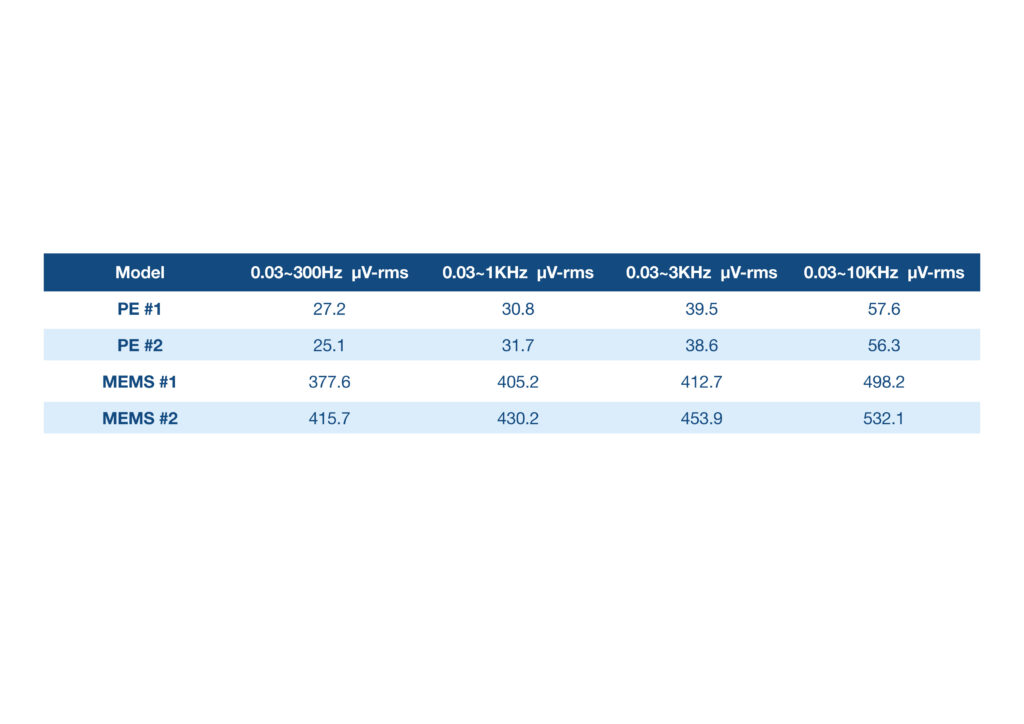
Figure 2 shows a comparison of the resolution achieved with each sensor. This was calculated using a bandwidth of around 10 kHz (0.03 kHz to 10.00 kHz). The study made by TE Connectivity shows that the resolution of the PE sensor was around 9 times higher than the resolution of the VC sensor. What this means in practice is a much better dynamic range, allowing smaller anomalies to be detected sooner. In a preventative maintenance application, this could leadto potential defects being detected sooner.
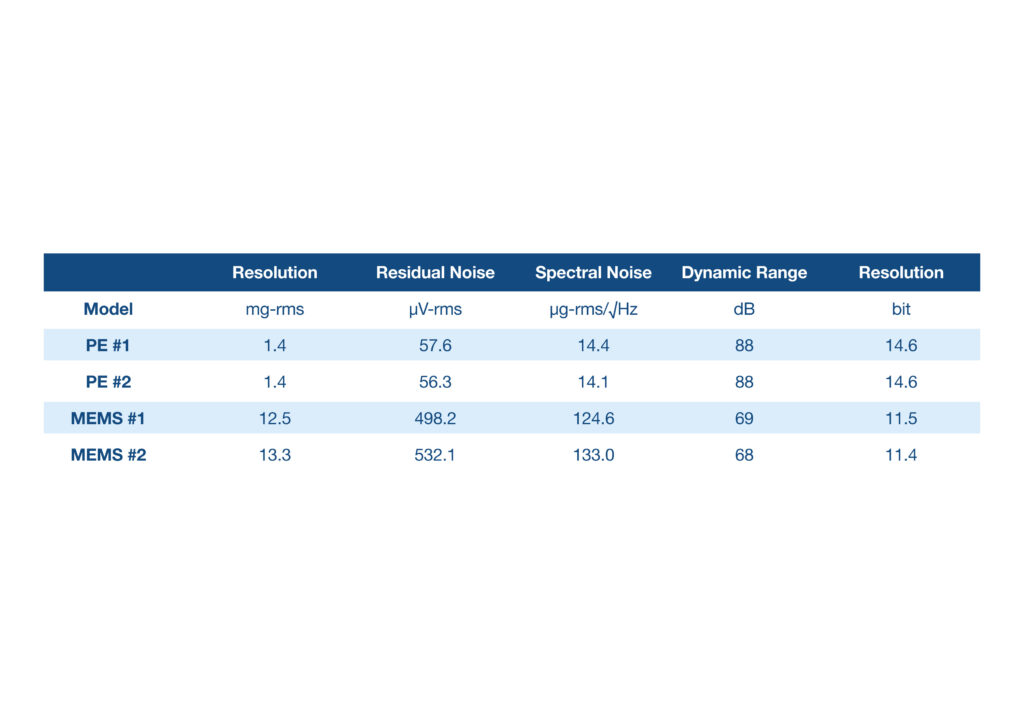
Other key figures to consider are drift and stability. The crystals used in PE sensors have demonstrated great resilience overtime in industrial applications. While it is difficult to ascertain the actual long-term drift of a PE crystal structure, the study did point to the fact that PZT crystals are the most common type used in PE accelerometers and are popular with engineers developing systems for use in an industrial setting.
The MEMS structure of VC-based accelerometer sensors is subject to drift and the manufacturers do provide that information. This varies from one sensor to another and is largely based on the MEMS structure used. In general, MEMS sensors manufactured using bulk micromachining demonstrate the best long-term drift but this can be reflected in the price. This can restrict their use in condition monitoring applications, where it is more common to see sensors constructed from a surface micromachined process. While this is a cheaper manufacturing process, it does not return the same performance in terms of resolution and stability.
Both types of sensors are suitable for use across the extended temperature range associated with industrial applications, from -40° C to +125° C. However, for applications that require operation beyond these limits, charge mode PE sensors are often the suggested solution.
Sensors enabling predictive maintenance
The type of signal required for predictive maintenance will depend on the parameter being measured. But at a system level, the sensors may connect directly to a programmable logic controller (PLC), they may also feed into an intermediary stage for data acquisition. In both cases, an analogue signal is the most common. Sensors may also be located in more remote areas and connected through relatively long cabling. In this case, it is common to use a 4-20 mA powered loop.
In the Industry 4.0 domain, the use of ‘smart sensors’ is more common. These will typically include some onboard processing, in the form of a microcontroller or microprocessor. These types of smart sensors can make decisions locally based on the information they are monitoring. In these applications, both PE and VC sensors offer valuable data and are therefore becoming popular with developers.
The TE study demonstrated that both types of sensors offer comparable performance. They can also compete well in terms of operating temperature, packaging options, output flexibility, and ease of use. But the study also showed that accelerometers based on PE technology offer better long-term stability, often deliver higher resolution, and wider operating bandwidth.
Condition monitoring and predictive maintenance are exciting new application areas, where advanced technologies will enable new insights and greater productivity. While all types of sensors are applicable, the TE study indicates that PE accelerometers might be the better option