Modern Automotive Industry is seeing various drastic trends like intelligent cars and driver assistance and so requires a completely changed portfolio of relays & switches to fit in the applications. Here we present to you some of the latest innovations in relays & switches in automotive segment.
Relay is a kind of component by which when the input is reached a certain value, one or more outputs will produce the schedule changes. Automotive relays are designed for automotive application usage. It could be categorized by many different ways, basing on terminal arrangement and different functions, automotive relays could be divided as, PCB automotive relay, Plug-in automotive relays and combined automotive relays. Automotive relays of different sizes are found in every type of land or sea vehicle. They are often used to enable a low amperage circuit to switch a higher amperage circuit on or off. An example would be turning headlights on. Automotive relays also allow items to switch at the same time by using a single output, therefore allowing one to simultaneously open and/or close continuity on multiple items. With the increase of electronic circuits and safety requirements in cars, more and more switching contacts are monitored by diagnostic routines. Similar routines are used by the system suppliers before, during and after the assembly processes (In-Circuit and End-Of-Line tests) as well. Automotive relays are originally designed to switch real automotive applications (e.g. motors, lights, heating, etc.) with a load voltage of 12VDC (or 24VDC or 42VDC) and load currents above 1A. Lower diagnostic current and voltage levels can result in wrong interpretations of the state of the relay contact. Automotive Relay termination style is usually plug-in or quick-connect.
Selection for right automotive relays
Most PC board mounted relays are driven by microprocessors or other sensitive electronic devices. A successful coil drive circuit requires isolation between the relay and the microprocessor circuitry. Effective drive circuits must account for drive current and voltage requirements as well as effective suppression of L di/dt transients which can destroy microprocessor circuits. While it is easy to over-design an effective drive circuit, today’s designs must be cost competitive. Integrating a monolithic IC driver device into the relay will provide significant value to the system designer. Although the advances in the electronics industry are increasing day by day, mechanical relays are still extensively used in industrial and automotive applications to control high current loads. Their low cost and excellent fault tolerance makes relays to be an useful and reliable solution in industrial and automotive applications environments. The device requirements for industrial and automotive applications are different and must be addressed in different manner. While the requirements for automotive applications are the most difficult to comply with, industrial requirements traditionally allow more latitudes. Relay coil currents vary considerably depending on the applications.
The largest classes of industrial and automotive relays have coils with current consumption between 50 and 150 mA. Selection of a suitable relay driver requires many constraints to be evaluated. For automotive applications, it is necessary to put special attention in the following requirements:
- Load Dump (80 V, 300 ms)
- Dual Voltage Jump Start (24 V or More)
- Reverse Battery (−14 V, 1 Minute or More)
- ESD Immunity (according AEC−Q100 Specification)
- Operating Ambient Temperature (−40°C to 85°C)
Meeting these automotive requirements usually results in specifying an oversized and non-cost effective relay driver, or one requiring many protection components. Industrial applications on the other hand do not have many requirements different than the standard ones such as ESD immunity (usually 2.0 kV HBM), and a given range of operating ambient temperature (usually between 0°C to 85°C). However, some applications also call for protection devices against transient voltage conditions, which create the need for extra protection components too.
With the automotive market in India expected to continue registering strong growth over the long term, many global companies are looking forward to expand and strengthen automotive operations in India. Now a day manufacturers provides a wide range of automotive solutions and technologies for the evolution of next-generation automobiles. Current range of automotive products in India includes parts & materials, Alternators, Regulators, Rectifiers, Relays, Air flow sensors, Ignition products (coils, modules, cables) & fuel pumps.
Pulse Width Modulation (PWM) and Relays
Efficient energy management is one of the main goals in automotive industry Regulating actuators by Pulse Width Modulation (PWM) is a widespread means of improving efficiency. There has been an increasing penetration of PWM controlled applications like heater blowers, lamps, EPAS. Once a PWM controller is available in the car it could be used for several applications. Heat dissipation of monostable relay coils is one source of high temperatures in relay boxes, distribution and switching modules. That limits not only the relay performance, but the performance of the whole unit, too. These heat sources could be removed by using latching relays or at least be reduced by use of high resistive coils and / or by applying PWM controlled driver circuits. There could be many key aspects, which have to be taken into account when using PWM strategy for the relay coil driver.
Relay Status
The best way to regulate the relay coil power consumption would be a DC current driver, since the main electrical parameters of a relay (pull-in, pull-through and holding currents) are to a certain extent temperature independent. But relay coils are usually voltage driven. Thus those characteristics translate into the temperature dependent voltages for pull-in, pull-through and holding. The reason is the temperature depending resistance of the coil wire material, i.e. copper. Once the relay has pulled through, it keeps its status (armature keeps to its position on the core) unless the coil current falls below the holding current. For shock and vibration resistance there is an additional excess current required, which depends on the relay type, further relay parameters and shock and vibration requirements. PWM controlled drivers regulate the effective applied voltage by changing the duty ratio of DC voltage normally at a given frequency. Inductive systems like relay coils respond in presence of parallel components to a negative going edge with a current decrease. This ripple around the effective current depends on the coil inductance, coil suppression, PWM frequency, and voltage level and duty ratio. It is always recommended to start with 100% PWM duty ratio until the relay pulls-through and settles. The necessary time depends on excess voltage, relay type, etc., but 500ms should be sufficient. Otherwise it will take some time for the relay current to settle around the effective current. In order to warrant a good relay performance with PWM it has to be made sure, that under all circumstances the coil current does not undercut the level of holding current plus the excess current for shock and vibration. Otherwise the armature and the contacts might open. Then the relay has to pull-in and pull-through again to settle. Repeated opening and closing the armature might cause humming noise. Unintended opening and closing the armature and contacts under load might cause contact welding.
Inductance
Relay coil inductances are in general relatively high, which result in comparatively small current ripples. But these values are not constant and vary strongly within one relay family or one type. The relay coil inductance depends among others on quite a few parameters, which are not under focus in a standard relay manufacturing process. Furthermore it heavily depends on the coil current (saturation) and status of the relay (armature open or closed).
Coil Suppression
In DC coil drivers coil suppression is done for protecting the relay driver from high coil switch-off voltage peaks. For PWM coil drivers suppression is even more crucial, since the coil switch off occurs at PWM frequencies, i.e. up to several thousand times per second. Furthermore coil suppression reduces the ripple coil current, and thus the potential for dropping out since the coil current takes longer to decrease. Therefore from this perspective the stronger the suppression the better, i.e. best with parallel diode. On the other hand this case is exactly the worst for relay switching capability. For single drivers the best compromise is probably an anti parallel low voltage (3…9VDC) Z-diode. A Zener diode in parallel to the driver would cause a varying voltage clamp across the relay coil during switch-off due to varying supply voltage.
Duty Ratio
The effective coil voltage is the product of PWM duty ratio and supply voltage. However the supply voltage varies due to changes in system load (e.g. cranking) and alternator and battery status. Therefore the PWM duty ratio should be regulated according to the supply voltage. A tight regulation would be optimal for efficiency. But slight variation on the supply side would cause a continuous regulation of the PWM duty ratio. Furthermore regulation response time would need to be faster than 1ms to ensure, that the effective coil voltage does not undercut the required voltage limit.
Disturbing Noises
The application of PWM voltage across the relay coil causes magnet-ostriction of the iron within the relay magnetic system (core/frame/armature). The result is a slight audible noise if the relay was freely suspended. However when the relay soldered or welded onto a rigid lead frame that noise might be amplified. This depends on the lead frame (suspension, dimension, etc.) and the sound propagation and damping within the car. Choosing 20kHz PWM avoids disturbing noises for human beings but might cause problems to animals.
EMC (Electromagnetic Compatibility)
Due to the steep voltage and current edges EMC problems are possible. Therefore electromagnetic compatibility tests of the whole unit are necessary.
Role of Relays
The range of applications of relays in automotives can be classified into resistive loads, capacitive loads and inductive loads. The current curve of resistive loads is specified by the load voltage and load resistance. Capacitive loads have a high inrush current and a low steady current. Therefore lamps are counted to the capacitive loads, because the cold filament has a significantly lower resistance, than the hot filament. Inductive loads are characterized by an exponential current increase and a remarkable switch off arc, induced by the demagnetization of the magnetic circuit of the load. Power supply relays (clamp relays) can switch or feed a mixture of different loads. The circuit design of resistive and capacitive loads is usually a simple switch on and switch off. Motor load circuits are often more complex.
Wiper Circuits
To stop the wiper in the correct position, a short-circuit brake is used. This can be done either by an internal slipring (usually used for rear wiper) or with the normally closed contact of the relay (usually used for front wiper). This requires a high switching capability of the N/C-contact, especially in combination with intermittent wipe function or rain sensor control. Dual speed wipers have two windings, which are commuted by a second relay. There are also wiper systems without mechanical gear, which are electrically reversed with a H-bridge circuit.
Cooling Fan Circuits
Depending on the size of the engine, either one or two fans are used to cool the engine. There are different possibilities to control the speed of the fans. Single fan systems are usually controlled by one or more serial resistors. The disadvantage is the electrical power loss of the resistors. Double fan systems are normally controlled by switching them either in series (low speed) or in parallel (high speed). If more speed steps are needed, additional serial resistors are used. A more sophisticated method is a PWM-controlled brushless motor. In commercial vehicles the cooling fan is mostly driven directly by the motor shaft.
Coil Suppression Circuits
The disconnection of the relay coil generates a transient voltage peak, which is only limited by the parasitic inductivity and capacity of the electrical system. In most of the cases it is necessary to suppress the transient voltage peak to typically 60VDC – 100VDC for the protection of the relay driver or the vehicle electrical system. Any voltage suppression of the relay coil influences the dynamics of the electromechanical system and can reduce the lifetime. The best protection method for the driver is a diode in parallel to the relay coil. But this method has the worst influence on lifetime of the relay. Typical suppression methods are a resistor in parallel to the coil (preferably as internal component in plug-in relays) or a Zener diode in parallel to the relay driver (preferably for PCB relays).
Short-Circuit Brake
The short-circuit brake is used, wherever an electric motor must be braked (e.g. wiper). The short-circuit brake transforms the rotational energy of the motor into electrical energy. The short-circuit brake can be critical at higher load voltages. If the switch off arc does not extinguish during the transition time of the movable contact, the arc creates a direct shortage of the power source. Particularly in 24VDC systems, the resulting extremely high arc current could cause almost instantly severe damage to the contacts and could destroy the entire relay.
Motor-Reverse Circuit (H-Bridge)
The H-bridge is used to operate a motor in two directions (e.g. door lock, steering lock, power window, seat adjustment, etc.). The operation time is typically very short compared to the thermal time constant of the relay (e.g. door lock <1s, power window <10s). This means, H-bridge relays must be designed for high current-switching-capability, but not for high current-carrying-capability. Higher load voltages can be critical, due to possible short-circuit-arcs.
OMRON Automation
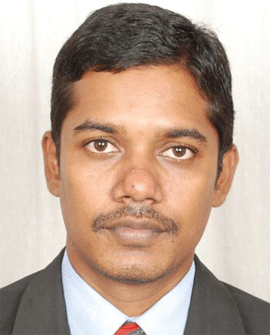
Mr. HR Thendral – Automotive Specialist, OMRON Electronics and Mechanical Components Business Division, India
Speaking on key features and specifications that differentiate a general purpose relay from automotive relays, Mr. Thendral said, there are many notable features which differentiate an automotive relay from a general purpose relay. Here is the low-down: a) Vast range of features and applications: Automotive relays of different sizes are found in every type of land or sea vehicle. They are often used to enable a low amperage circuit to switch a higher amperage circuit on or off; fully sealed with IP 67 standard, which can normally operate from – 40 degree Celsius to 80 degree Celsius. They also have High current carrying capacity in small packages. b) The technology: Automotive relays are comparatively more reliable and score high on quality. They are also sturdier – can withstand high temperature, humidity and vibrations. This all is being rendered through stringent test conditions and approval standards. As per Mr. Thendral, Some of the recent key innovative developments for For advanced automotives like, intelligent cars are, Compact relays: making really miniature versions that have high current carrying capacity. Arc proof DC power relays: especially designed for electric cars to ensure high voltage DC switching without producing any arc. And Better reliability: by making contact less relays and switches Globally, Omron generated a turnover of around 50 million USD through automotive switches in FY 2014-15. In the current FY, the growth target is 8 %. Omron has the right prowess backed by string R & D capabilities to provide meaningful value for Indian customers. Further Mr. Thendral said, we strive to keep in sync with the ever-dynamic world of technology by bringing flexibility in our product range effectively to meet the customer requirements. For example, we are developing non-contact technology which is being added to our range of conventional mechanical switches to enhance our product variations. We are also gradually spreading our application arena. The usage of our customized mechanical sealed micro switches to door closures, AT shifters, HVAC panels and other applications as detection & manual switches and our advanced electronic control technologies applied to the intelligent cars are some of the instances in this regard. In the Relays segment, Omron offers four types of relays: – Automotive – plug-in (mounted in engine compartment) – PCB relay which is mounted in the car- interior of ECU, and – High-voltage switchgear DC power relay for battery control in the case of electric vehicles. This wide variety not only suits most of the applications for the automotive sector but also satisfies several application needs from varied customers. We have a proven track record spanned across more than 30 years in the development, production and sales of automotive relays helping us meet customer’s expectations in terms of technology and high quality. Omron continues to track the next generation vehicle developments which requires lighter materials, infotainment (information and entertainment for the driver) and greater electronic functionality for driver’s comfort and safety .These trends require smaller, more high efficient relays for greater power switching and smaller size. Omron is already progressing well with new PCB power relays to satisfy these kinds of futuristic requirements.
Conclusion
Automotive electronics industry of India is upgrading to smart cars than provides much more than just comfort and millage. So is the relays part of the automobile electronics. Today’s relays have extended their applications to a very diversified role in the automobiles and hence different specifications and topologies are being used to meet specific requirements. TECH FOCUS