In the 1990’s, the world economy started experiencing a global increase in trading, altering the nature of traditional value chains. There was a massive migration of manufacturing industries from advanced countries to developing economies, transforming some Asian countries into industrial giants. The chain of events that followed resulted in the concentration and redistribution of industrial activities in China and India – the two most populous and fastest-growing economies in Asia – and stirred industrial changes in Singapore, Malaysia, Thailand, Indonesia, Philippines and Vietnam to gather momentum. Many analysts had predicted a boom for the Asian manufacturing industry and were proven right. The Economist points out that in 1990, Asia accounted for 26.5 percent of global manufacturing output, which by 2013, reached 46.5 percent. Today, China accounts for half of Asia’s output.
The growth of Asia’s market share from a global manufacturing standpoint is shifting the balance of economic power in its favour. The continued increase in this market share has a significant implication on the rest of the world; it has already generated ripples, and radically altered the parameters governing development pace and composition. But what does this mean for the average manufacturer at the heart of this industrial revolution? How are the shop floors in Asia responding to this tremendous appetite for growth and the challenges that it brings today?
The age of Automation
In the past, manufacturing in Asia signified a large production volume, low-level technology and cheap labour – a fact that is no longer true. The increase in domestic demand, evolving consumption patterns, the advent of emerging technologies and fast changing infrastructure development levels in different countries have transformed the playing field. Today’s consumers are more interested in personalized products of higher quality with better safety features at a competitive price. The marketplace has no room for flaws in quality, especially at a time when massive recalls are rattling even the biggest brands.
The only way for manufacturers in Asia to manage growing product complexity, maintain quality assurance and competitive costs is to take advantage of the boom in global and technological advancements. Recent statistics suggest that this fact is not lost on manufacturers in Asia. In 2013, 98,807 industrial robots were shipped to Asia, 17 percent higher than in 2012 – the highest level ever recorded. Statistics from the same source also highlight that China became the largest producer of robotics in 2013, selling 36,560 units. Between 2008 and 2013, the compound annual growth rate (CAGR) of robot supplies to Asia (including Japan) was about 8 percent on average and total supply of industrial robots in China increased by 36 percent per year on average in the five consecutive years. With the industry’s increased awareness of the business benefits of automation, installation of industrial robotics is expected to increase across Asia from 689,349 units in 2013, to 1,107,600 units at the end of 2017.
Today, shop floor tasks commonly performed by industrial robots include welding, painting, polishing, deburring, assembling components, transporting items and machining. The new generation of robots is increasingly able to understand their surroundings better through sight and sound systems and can distinguish between different components, even work alongside human beings. To sustain successful robotic applications, shop floors need well-trained and highly skilled engineers to operate robotic simulation processes, offline programing and robot maintenance. The successful implementation of robots can help in visualizing and predicting operational results with a heightened degree of certainty. Not to mention increased job satisfaction for employees due to smart, efficient and accurate results.
In addition to robotic installations on the shop floor, factories are implementing several other automation models by employing programmable logic controllers (PLC). PLCs help in controlling robots, machinery, equipment, switches and alarms – they manage data communications among these elements to minimize human intervention, hence reducing human errors. The virtual commissioning model, in which factories replicate the behavior of a physical manufacturing environment with a software system, has numerous benefits for manufacturers including savings in labour, energy costs and improved product quality, accuracy and precision.
At the Cusp of a Societal Shift
In recent years, China has had to increase its purchases of robots because of the growing use across the developing nations owing to the fact that lower labor costs constitute much less of a competitive advantage than they did in the past. Industry research shows that the gap in manufacturing costs between China and the US has been narrowing from an average of 18 percent cheaper in 2003 to only 7 percent today. The reasons for this include rising labour costs in China, cheaper US energy costs and increased automation of factories.
As the trend towards automation continues to increase, so will the volume of robotic installations. Industrie 4.0 – the vision for the future of manufacturing that is becoming an increasingly stronger theme in global manufacturing – links the real-life factory with virtual reality. Robots are currently assigned multiple and dynamic tasks by human operators, however the robots of tomorrow will be able to solve problems together. Robots will have the ability to interact with each other, share information about pending operations, and assign tasks together. Nevertheless, robots have to be linked to a flexible conveyor and automation system to improve product quality, lower costs, and increase efficiency. The key for a successful industrial production under an Industrie 4.0 environment is strong product customization under flexible production conditions. This will ensure reduced error margins thanks to the availability of real-time data throughout the production cycle.
To realize this vision, digital manufacturing plays an important role, and it is expected to reshape the shop floor due to the following factors:
- Global competition will require modernization of production facilities
- It is energy-efficient and uses new materials, e.g. carbon-composites which require retooling
- Human-machine collaboration will open up new applications and attract new customers
- Growing consumer markets will require expansion of production capacities
- Decline in productlife-cycle and increase in the variety of products will require flexible automation
- Technical improvements of industrial robots will increase the use of robots in the general industry and in small and medium sized companies, e.g. user-friendly robots, uncomplicated, and low priced robots for simple applications
- Improved quality will require sophisticated high tech robot systems
- Robots will improve the quality of work by taking over dangerous, tedious and unpleasant jobs that are not possible or safe for humans to perform
Growing technological advancements and rapidly decreasing costs are leading to a vast increase in the number of jobs which robots can perform in an efficient manner. This will lead to a major increase in productivity, and also to the replacement of human workers in many sectors of the economy. The growing use of robots will reduce the competitive advantage which cheap labour historically provided by many developing countries. Robots will make vital contributions in helping aging societies like Singapore and China obtain better control of their healthcare costs.
The combined impact of all these technological advancements and industry trends puts a sharp focus on the potential of robotics and automation to transform the future of workplace efficiency, improve profit margins for companies and enhance the quality of life of the end users. How Asian manufacturers employ this evolving technology to realize its full potential, will determine the future of shop-floors and consumers alike.
About Author
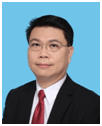
John Louie – Marketing Manager of Siemens Industry Software Limited, Asia Pacific region.