Discussing the power supply requirements for commercial, military and network access devises.
Power supplies are considered among the simplest instruments because they tend to be single-function DC devices that output a controlled voltage, so most engineers believe they understand them very well.
However, there is much more to them than that, such as the multiple design topologies developed to serve a wide range of power requirements and the variety of functions developed to address an expanding range of applications.
The primary trends present in almost all power supply market segments are: increased efficiency; higher power density. There are several methods to improving efficiency and these include: developing new topologies; improved power devices, control ICs and magnetic component designs entering the market; the availability of new materials; and the application of digital control loops. Depending on the type of power supply and its end use, some or all of these methods will be used.
As power supplies are the very heart of every electronic equipment, special attention must be paid to their reliability. For other electronics a certain failure mode, at least for a part of the total system, can often be tolerated without serious (critical) aftereffects. However, for the power supply no such condition can be accepted, since very high demands on the reliability must be achieved.
Military Power Supplies vs. Commercial Power Supplies
Most commercial power supplies have a shorter mean time between failure (MTBF) rating than military power supplies.
In both military and commercial applications, every electronic system needs a power supply. As is the case with commercial power supplies, the three configurations of military power supplies are AC to DC, DC to DC and DC to AC; consequently, some may be inclined to believe that commercial and military power supplies are one and the same, however, they are not. What is the difference between military power supplies and their commercial off the shelf (COTS) counterparts? In a word, reliability.
While commercial power supplies may be adequate for some commercial applications, they are not appropriate for aircraft, sea craft or other military transportation equipment. That is because in these applications, a more robust power source is needed. Most commercial power supplies have a shorter mean time between failure (MTBF) rating than military power supplies. That means they are more likely to experience interruptions, often without warning. In a commercial or military transportation application, a loss of power can be cataclysmic – often, life threatening. These applications require a more robust power supply with a long MTBF, which military power supplies are designed to provide.
Another advantage that military power supplies offer is the ability to recognize any impending failures in the system. As the demand for predictability increases, new power conversion products are equipped to make the user aware of specific glitches that may be around the corner. Finally, military power supplies are subject to greater scrutiny than commercial power supplies. The military power supply industry is strongly regulated, with specific requirements involving the selection of parts, the design process and specifications for use in varying environments.
There are many fine commercial power supply products, but most are not suitable for military applications. When the defense market builds systems using COTS power supplies, it must understand the risks involved – obsolescence, process changes, environmental vulnerability, faulty electrical performance or EMI issues – and modify the system to compensate for said risks. The cost and manpower spent on those modifications can be avoided by bypassing COTS power supplies in the first place, and opting for power supplies that are engineered and designed for military applications.
With the coming proliferation of network access devices, driven by 4G/5G, security, “smart homes,” and a host of other applications, there’s a strong need for robust, off the shelf systems to combine power and communications into single cables. Speed of deployment, cost, safety, security, and other challenges must be taken into account by solution developers to remove these headaches for network designers.
Power Supply for Network Access Devices
The challenge of how to get power to devices mounted on lamp posts, tops and sides of buildings, security fences, and many other unusual places can often be the very last thing on an engineer’s mind. Take the case of small cells. What’s the first thing any good 4G-network planning engineer should ask? Probably, “What does my 4G coverage map need to look like?”
One way to solve the challenge of delivering power to odd locations is to use the same cable that connects the optical fiber, eliminating the reliance on local power availability near the device. So-called hybrid optical/copper cables are not new – several designs have been on the market for 20 years or longer. If that’s the case, then why haven’t such hybrid cables been sold in large volumes until now?It seems logical that combining power and optical communications delivery into one cable should provide time and cost savings to network providers. Isn’t that, after all, what power-over-Ethernet (PoE) technology is really all about – combining power and communications under one sheath? There are two reasons that until recently these cables haven’t taken the market by storm.
First, the industry’s hybrid cables up to now have proven very expensive, large in size, and time-consuming to terminate due to very complex cable designs. Second, getting power through these cables and accessing it from the other end of the device required significant engineering expertise. These systems have been difficult to deploy, and there are no “off the shelf” options generally available.
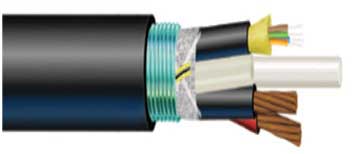
Let’s take a look at the cable designs for hybrid optical/copper cables. Until recently, common hybrid cables typically used some type of loose tube optical-cable design in which one or more buffer tubes were replaced with conductors (see Figure 1). A less common design, referred to as a composite design, involved taking individual optical and copper cables and bonding them together in a “figure eight” arrangement (see Figure 2) – more specifically, two side-by-side cables possibly bonded together by a third plastic sheath.
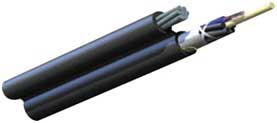
Hybrid-cable challenges
These cable designs are complicated in how the cables are manufactured and how they’re accessed for fiber splicing and copper termination. Also, making these kinds of cables requires three to six separate manufacturing steps, depending on the cable design, increasing the cost of the cable.
Accessing a typical loose tube style of hybrid cable requires several steps as well as specific optical- and copper-cable access tools. A survey of several customers with experience in deploying such cables reveals that it typically takes a minimum of two or three minutes to terminate them. In some cases, the amount of time could be as long as five minutes or more to prepare one cable end.
That amount of time may have been acceptable in the past for unique projects where only a few cables were deployed. But considering the current massive deployments of small cells, Wi-Fi access points, HD security cameras, and other access devices, the high cost and time constraints of the past are totally unacceptable.
For hybrid cables to become viable options for these markets, the cable must have characteristics resembling fiber to the home (FTTH) optical drop cable. The cable must be cost-effective and fast to deploy. It’s most desirable for such a cable design to be simple, ideally produced in a single manufacturing step, and able to be terminated in well under a minute.
But having a great hybrid cable is not necessarily enough. The majority of providers seeking to deploy hybrid cable don’t understand the challenges involved. For instance, there are voltage drop penalties over distance; electrical protection may be needed, such as surge protection or protection against lightning strikes or cable cuts.
Providers must also know how to convert from an optical signal to an electrical or PoE input at distances greater than a kilometer. Typically, most access devices such as small cells, Wi-Fi access points, and security cameras are not designed for direct fiber input. Therefore, media conversion is often necessary. Additionally, what type of power supply should be used?
There are lots of considerations beyond the cable itself. In short, every hybrid optical/electrical deployment of the past has required a unique electrical engineering design because no off the shelf options were available.
Backing it up
Another consideration is battery backup or uninterruptible power supply (UPS). It’s highly desirable to have emergency battery backup for small cells to handle emergency phone service. But backup power for security cameras, critical Wi-Fi applications, and other access devices may be equally important.
But if we truly envision millions of these access devices deployed globally in the coming years, then deploying and supporting millions of individual batteries probably isn’t the most effective strategy. Cost, environmental concerns, maintenance, and other such issues would seem to discount that approach as a viable alternative.
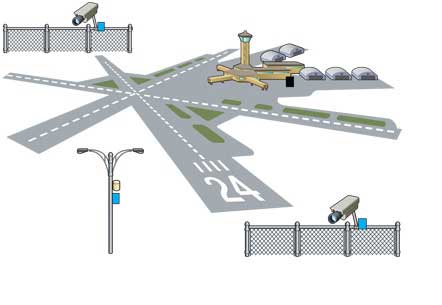
A centralized battery backup system is a much better alternative. Delivering power via hybrid cabling to many devices from a central location (perhaps in a star network arrangement) as a UPS service could support this approach (see Figure 3). Such a central location could be an outdoor distribution cabinet, a telecom closet, a macro base-station location, etc. Any location that has access to power and the optical network could be a potentially viable alternative for such a network architecture (see Figure 4).
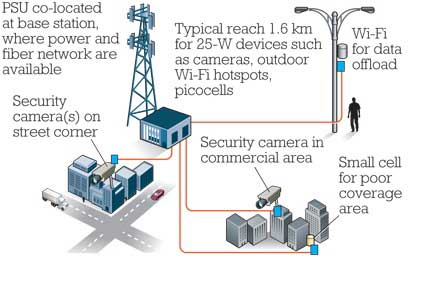
Another consideration is the type of power supply to use for powering the cable and how to safely and properly disseminate power off the other end to ensure delivery of the right energy levels to the network access devices. For the power supply, there are three basic choices to consider: -48-V DC NEC Class 2- or SELV-compliant power supplies, 120-/240-V AC systems, and 380-/400-V DC Microgrid systems.
Power-supply comparison
The -48-V systems that remain within low power levels to meet electrical codes (such as NEC Class 2 and SLV) are desirable since they’re designed to keep energy levels low and as safe as possible. These systems can effectively handle power levels below 100 W, so electricians are not required for the installation. Readily available from multiple vendors, -48-V DC power supplies are a proven technology.
Because these systems keep power levels low, the drawback is that the inherent distances and power levels they can support are limited. Also, since the voltage level is so low, a higher electrical current is needed in the cable to drive power to devices. Higher current in the cable means more energy loss from heat caused by the electrical resistance in the copper. Still, these lower-voltage DC systems are typically the best.
The 120-/240-V AC systems are also a proven technology, with standards in place for many years. These systems can support higher power and longer distances than -48-V DC systems; however, they require qualified electricians for installation. Other drawbacks include the inherently less efficient power transmission of AC systems due to capacitive and inductive effects, added difficulties in integrating UPS battery backup (requiring more equipment), and the requirement for AC transformers and additional AC-to-DC rectification circuits. Therefore, in most cases AC systems are more expensive to deploy than -48-V DC systems.
The 380-/400-V DC Microgrid approach promises a new, more effective way to handle higher power needs without the inherent inefficiencies of 120-/240-V AC systems. Several systems were recently deployed by major institutions around the world. Standards development is underway through the efforts of the EMerge Alliance (www.emergealliance.org/).
While the expectation is that this method will be overall less expensive, easier to connect, easier to maintain, and more energy efficient than AC systems, it will still require qualified electricians to install. For high power and long-distance applications where low-voltage NEC Class electrical systems will not work, this method may be a good future alternative.
How much and how far?
Another important question to address is how much power can be delivered and at what distance to the network access device (small cells, Wi-Fi access points, HD security cameras, etc.)? With all power systems (AC or DC), the fundamental problem of voltage drop over distance must be addressed. Until now, an electrical engineering calculation was typically performed for every cable run to ensure the voltage range delivered to the device was within the acceptable range. With modern DC/DC conversion technology, devices are now emerging that eliminate the need for this engineering.
Properly designed DC/DC conversion devices can take in a wide range of voltage and deliver exactly what’s required to power the device, whether it be a 12-V HD security camera or 48-V picocell. Such new devices also incorporate the necessary types of carrier grade electrical protection to protect against lightning strikes, EMI surges, cable cutting, etc. These new devices promise to reduce engineering and make the systems install like “a long extension cord.”
Hi-tech DC power supply from GW Instek
Stemming from the design and manufacture demands of electronic industries, GW Instek offers diverse power supply product lines to meet user’s demand for a variety of applications. Based on different needs, the product lines can be divided into several categories including DC Power Supply, AC Power Source and DC Electronic Load. For DC Power Supply, the products can be briefly categorized by the following types, Linear, Switching, Programmable or Non-programmable, Single or Multiple Outputs, High Precision or Affordable Price, Dual Range and Wide Combinations of Voltage and Current, which can be selected to meet the application requirements.
GW Instek offers more than 100 power supply products are suitable for the requirements of Electronic Assembly Testing, Education, Component Testing, Wireless Product Testing, Burn-in, Battery-Power Product Testing Automotive, Aerospace industries and so on.
PSU-Series Programmable Switching D.C. Power Supply
GW Instek rolls out the brand new PSU series single channel programmable switching D.C. power supply featuring C.V/C.C Priority, adjustable Slew Rate, and series/parallel operation. The PSU series D.C. power supply, with high power density design, provides 1520W output power produced by 1U height. Additionally, features include rear panel output and multiple remote control interface make the PSU series most suitable for LED module, automotive component (low-powered D.C. brushless motor), DC-DC Converter, and hybrid-powered battery module production tests.
PSW-Series Multi-Range DC Power Supply
The PSW-Series is a single-output multi-range programmable switching DC Power Supply covering a power range up to 1080W. This series of products include fifteen models with the combination of 30V, 80V, 160V, 250V, and 800V rated voltages and 360W, 720W and 1080W maximum output powers. The multi-range feature allows the flexible and efficient configuration of voltage and current within the rated power range. As the PSW-Series can be connected in series for maximum 2 units or in parallel for maximum 3 units, the capability of connecting multiple PSW units for higher voltage or higher current output provides a broad coverage of applications. With the flexibility of multi-range power utilization and series/parallel connection, the PSW Series significantly reduces the user’s investment for various power supply products to accommodate the projects with different power requirements.
Website: www.gwinstek.com