Fabrizio DI FRANCO, Technical Marketing Manager, STMicroelectronics Pvt Ltd.
Akshat Jain, Technical Leader, STMicroelectronics Pvt Ltd.
Over the last decade, high brightness LEDs have rapidly improved in terms of energy efficiency (lumens/W), durability, reliability, and cost-effectiveness, completely transforming the lighting industry. Now the challenge for engineers is to develop an LED driver capable of delivering the necessary lumens of light output from the lowest possible level of power without compromising on circuit performance and protection.
The 75W, fully digitally controlled HB LED driver evaluation board shown in Figure 1 is capable of dimming LEDs up to 0.5% of their maximum brightness. The LED driver has two stages of power conversion. The front end stage is a power factor correction (PFC) converter to provide a regulated DC output, and the downstream stage constitutes a buck converter and modified buck converter connected in parallel as shown in Figure 2. The 32-bit microcontroller (MCU) takes care of the digital control for the PFC stage and two DC-DC buck converters. The digital control of the PFC stage and two DC-DC conversion give high advantages in terms of cost and flexibility. The on-board fast protection circuits guarantee all essential protection features with high reliability. The performance of the LED driver developed has been evaluated under universal AC mains (85-265V) over the entire range of brightness (0.5-100%). The power quality parameters are within the acceptable limits of harmonic standard IEC 61000-3-2 for universal AC mains.

Figure 1: STEVAL-LLL004V1 75W Digital Lighting evaluation board
The proposed solution adopts a digital conversion control approach rather than the standard design based on analog ICs.
The main advantage of the digital control is programming flexibility to tune the parameters and the operating points on the fly, for any given condition, without any HW modification, whereas the analog control can only be tuned for a specific range. Advanced features such as two dimming methods (analog or digital), dimming controls (0-10V, Wireless communication), dimming resolution, temperature monitoring, various protections and communication functions tend to be significantly more cost-effective since they can be implemented by a single IC and are easier to implement using digital techniques compared to an analog control. Additionally, the digital control guarantees more stability than analog in noisy conditions: a solution digitally controlled is less sensitive to component tolerance, temperature variations, and voltage drift.
System Overview
The newly developed LED driver consists of three different power stages controlled by the STM32F071CB microcontroller as shown in Figure 2. The PFC stage and the two DC-DC converters are designed to work in transition mode (TM) to have optimized efficiency. Both first DC-DC converters based on buck topology and second DC-DC converter based on inverse buck topology work in constant current mode. In inverse buck topology, the power switch is connected to ground rather than to the high side switch as in a standard buck topology. The MCU and the gate drive section including the PM8841D, the PM8834, and the L6395D are supplied from the VIPer013LS, the 60 kHz high voltage off-line converter, managing the auxiliary SMPS in flyback topology. The overall efficiency of the LED driver system at 100% load is ~91%, thanks to the STD11N60M2-EP, the N-Channel 600 V MDmesh™ M2 EP power MOSFET.
The MCU is configured to sense zero crossing detection (ZCD) of inductor current and other relevant signals for all power converters, and accordingly, the MCU controls the MOSFET gate drive signals. The board is equipped with comprehensive safety features like short circuit, open circuit, input under voltage, and input over voltage.
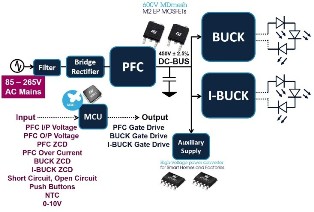
On board there is a provision of 0-10V input and push buttons to control the brightness of the LEDs. Thanks to the MCU’s advanced timers, the LEDs can be dimmed up to 0.5% level of the maximum brightness. Moreover, there is a provision to select the dimming approach, either analog dimming or digital dimming.
Table 1: Comparison – Digital (PWM) vs Analog Dimming
|
|
|||
No color shift as LED current remains the same | Color shift as LED current changes | |||
Possible current inrush problems | No inrush current | |||
Very linear change in brightness | Brightness linearity not as good | |||
Lower optical to electrical efficiency | Higher optical to electrical efficiency | |||
Frequency limitations and concerns | No frequency concern |
In Digital (PWM) dimming, the LEDs’ current turn ON and OFF at a fixed frequency (typically over 100Hz). The LEDs always turn ON at nominal current level. The average current to the LEDs is the product of the total nominal current and the duty cycle of the dimming function. The brightness level can be adjusted by adjusting the duty cycle. While in case of analog dimming, the LEDs’ current remain continuous, but there is a change in current level itself. Choosing the right dimming technique depends on the performance metrics of that application. Both dimming approaches have their own pros and cons, and some of them have been listed in Table 1.
Control Algorithm
The control algorithm of the LED driver is proven on the 32-bit STM32F071CB MCU from the STM32 family. The MCU controls all three power stages in transition mode, turning ON MOSFET gate just after the inductor current reaches zero. A proportional-integral (PI) control loop has been implemented for the PFC stage, improving control loop stability, line transition and dimming steps behavior, and reducing current and voltage overshoot at start-up. Buck and inverse buck converters work in hysteretic mode. The dimming technique and control can be selected from the toggle switches on the board. In either of the dimming techniques selected, the brightness can go down as far as 0.5% of the maximum brightness.
Digital dimming has been implemented using an MCU timer peripheral running at 500Hz. As per dimming level, the duty cycle is adjusted for buck and inverse buck converter.
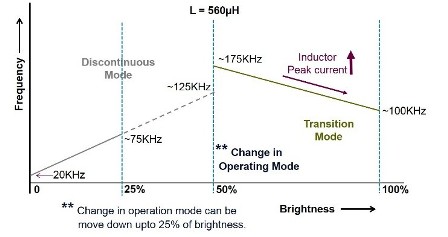
Analog dimming has been implemented using an MCU internal comparator and a digital to analog converter (DAC) peripheral. As per dimming level, the current threshold (inductor peak current) at the non-inverting end of internal comparator is adjusted by help of the DAC. While working in transition mode and controlling inductor peak current level, the LEDs can only be dimmed to a certain brightness level. To take care of low brightness levels, both DC-DC converters are made to operate in discontinuous mode as shown in Figure 3.
Experimental Results
Figure 4: Input voltage (AC) vs Efficiency @ Different Loads
Figure 5: Input voltage (AC) vs Power Factor @ Different LoadsFigure
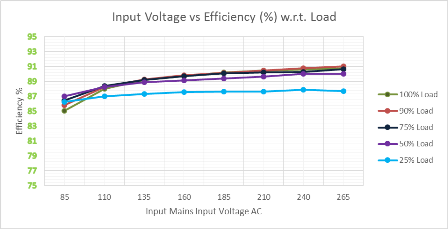
The overall efficiency, power factor, and Total Harmonic Distortion (THD) of the STEVAL-LLL004V1 has been calculated at different loads. With 100% load at 230V AC, the efficiency is above 91%. Figures 4, 5, and 6 show the LED driver performance in terms of efficiency, power factor, and THD.
Conclusion
The digitally controlled LED driver presented in the current work can deliver the power output of 75W. It can dim the LEDs up to 0.5% of the maximum brightness level by both analog and digital approaches. The operation is flicker free right up to 0.5% dimming levels using either of the dimming techniques, making the LED driver a unique solution. The experimental results show high efficiency, power factor near unity, and low THD% under wide input voltage and load conditions due to the performance of the ST power products as well as the control strategies implemented using the 32-bit STM32F0 MCU.