Very low power consumption and high magnetic accuracy
The new 3D magnetic sensor TLV493D-A1B6 offers accurate three-dimensional sensing with extremely low power consumption in a small 6-pin package. With its magnetic field detection in x, y, and z-direction the sensor reliably measures three-dimensional, linear and rotation movements. Applications include joysticks, control elements (white goods, multifunction knops), or electric meters (anti tampering) and any other application that requires accurate angular measurements or low power consumption.
While conventional linear Hall sensors, Hall switches and angle sensors only detect magnetic field components, which are oriented perpendicularly to the surface of the chip (GMR angle sensors detect only the planar oriented field component), the TLV493D-A1B6 sensor enables the simultaneous detection of the x-, y- and z-coordinate of the magnetic field (figure 1). By providing the magnetic field components of all three axes, customers get a holistic, three dimensional picture of the magnetic field at the sensor. Any movement by the magnet will change at least one magnetic field component which will be detected by the 3D sensor.
The three dimensional sensing is possible by integrating both vertical and horizontal Hall plates on the sensor chip. Vertical Hall plates are sensitive to the planar oriented field components from x- and y- direction. The horizontal Hall plate is sensitive to the perpendicular oriented field component (z-direction).
One of the main development targets was low power consumption. Using innovative design technologies like the low power oscillator pushed the power consumption of the sensor to a record low in the range of some Nano Ampere. Concentrating the development on the core requirements, accurate 3D magnetic sensing and low power consumption resulted in a small piece of silicon which fits in a small package. The used TSOP-6 package is only 2.9mm x 1.6mm in size, smaller than any 3D magnetic sensor on the market today.
Due to small package and low power consumption, TLV493D-A1B6 can be used in applications which have not been penetrated by magnetic sensors so far, replacing potentiometer and optical solution. With contactless position sensing and high temperature stability of magnetic threshold, system concepts get smaller, more accurate and robust.
The sensor provides a digital output via 2-wire standard I²C interface, which enables a high communication speed, bus modus and bidirectional communication between sensor and microcontroller.
TLV493D-A1B6 is RoHs compliant and JESD47 qualified to enable customers’ systems to fulfill the highest quality standards and various environmental regulations.
Architecture and key features
The sensor architecture is designed and engineered with three main function units (figure 2): power mode control unit, sensing unit and communication unit.
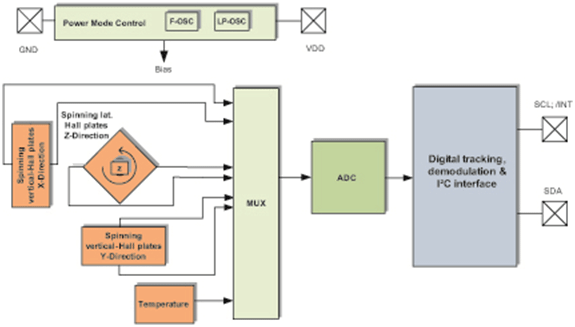
The power mode control unit is responsible for the power distribution in the IC(integrated circuit).It is also handling the start-up of the sensor.
The sensing unit contains the vertical and horizontal Hall plates and a temperature sensor. The sensing unit performs the measurement of the magnetic field in x, y and z direction. Each x, y and z Hall plate is connected sequentially to a multiplexer, which is connected to the Analog Digital Converter (ADC). The temperature sensor is also connected to the multiplexer and can be determined as option. The overall current consumption decreases by about 25 percent when temperature measurement is deactivated.
The communication unit, containing the I2C interface and register files, can be accessed by the microcontroller in any power mode, in order to read out register values. The values for the three axis and the temperature are stored in separate registers. The interface confirms to the I2C fast mode specification (400 kBit/s), but with a specific electrical setup data rates of 1 Mbit/s and more are possible. Following the guidelines of I²C protocol, the sensor is able to operate in an I²C bus with other devices. To operate a communication bus system reduces number of wires and enables controlling mechanism by the microcontroller (the bus master). The standard bus address of TLV493D-A1B6 sensor is a factory setting. During power up, this address can be changed via the address pin. The new address is valid during operation and only set back to factory setting by removing power supply.
For 3D magnetic sensing the TLV493D-A1B6 provides 12-bit data resolution for each measurement direction. This allows a high data resolution of 0.098mT per bit (LSB). So even smallest magnet movements can be measured.
Linear magnetic field (B) measurements of the Bx, By and Bz are possible for the wide linear field range of +/-150mT. This allows the customer to measure and cover a long magnet movement. The large operation scale also makes the magnet circuit design easy, robust and flexible.
By using vertical Hall plates for both planar magnetic field components (x and y direction), the sensor achieves an excellent magnetic matching of +/- 2%. This enables an accurate angle measurement.
Targeting industrial and consumer applications, TLV493D-A1B6 can be operated on supply voltage between 2.3Volt and 3.5Volt and in a temperature range from -40°C to +125°C. The product is qualified according Industry norm JESD47.
Flexible power modes enable lowest current consumption
The sensor provides an interrupt signal to the connected microcontroller after each measurement cycle. The microcontroller can now read out the magnetic and temperature values from the registers. The sensor interrupt signal can be used to wake-up a microcontroller system in sleep mode. Because the system is in sleep mode and only active during reading phase, the overall system power consumption can be reduced dramatically.
The TLV493D-A1B6 provides five power modes which can be selected by the user: “Power down mode”, “Fast mode”, “Low Power mode”, “Ultra Low Power mode” and “Master Controlled mode”(Table 1).The power modes can be configured during operations via I²C interface,
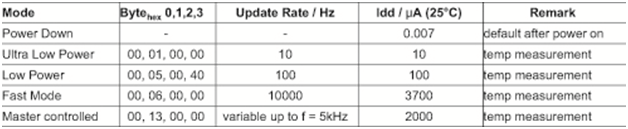
At power-up the sensor starts with the factory configuration. For a short period of time all function blocks are active. After this the sensor enters the “Power down mode” and all functional blocks are off. No magnetic measurement takes place during that period. Power consumption reduces to 7nA. Powered by two standard AA batteries (2,400mAh each), the sensor could operate over 39,000 years in this mode.
In “Fast mode”, readout is optimized on speed. Measurement sample from last conversion can be read while already the next conversion is performed. This mode is ideal for applications where fast magnet movements need to be detected like joysticks. Power consumption of the sensor peaks at 3.7mA, operating on maximum sample rate of 10kHz, corresponding to 10,000 measurement cycles per second.
In “Low Power Mode”, the sensor wakes up periodically every 10ms from “Power down mode” to perform magnetic measurements. Power consumption in “Low Power mode” is 100µA. This mode is ideal for applications like control elements (e.g. multifunction knobs), requiring regular magnetic measurements with low power consumption.
It is possible to get 10 times lower power consumption in the “Ultra Low power mode”. Wake up cycles are extended to 100ms, power consumption reduced to 10µA. Especially battery powered applications like tampering protection in e-meters will profit from this mode, as power consumption is very low.
In the “Master Controlled mode”, the sensor can be read-out flexible and depended on the applications need. After each measurement, the sensor waits for the microcontroller (master) to read the registers. Depending on the application situation, the read-out can be done immediately or with some time delay. As soon as the microcontroller collected the magnetic values, a new measurement cycle is triggered. This mode is especially useful when several TLV493D-A1B6 sensors are connected via I²C bus to detect large linear movements. So the microcontroller (master) decides which sensor data is more relevant to him and triggers the respective sensor.
Figure 3 shows the current consumption for the different power modes versus the temperature.
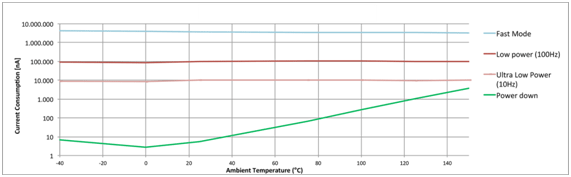
Application: tampering protection of e-meters
Traditional electricity meters have no ability to detect or deal with tampering because they only measure energy based on the voltage and current flowing between the in and out terminals. In such meters, tampering has become very easy and detection hard. However, electronic meters deployed today have the capability to detect tampering and take appropriate action.
Magnetic interference is probably the most common and easiest way to tamper a meter. Magnetic current sensors such as a current transformer (CT) are most susceptible to this interference. A powerful permanent magnet, when placed on the case close to the CT, produces a strong magnetic field that quickly saturates the core, thereby rendering the current sensor useless. In the event of the CT being useless, the current reading would be zero and would also make the energy reading zero.
The conventional approach to implement the magnetic sensing for tampering protection is based on two Hall sensors (one soldered on the related PCB and another one vertical to it on a separate small PCB, figure 4). This approach comes with some disadvantages like difficult mechanical construction, calibration and tuning. In addition, power consumption and costs are high.
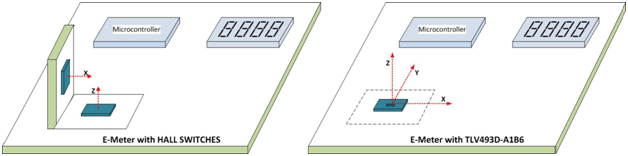
With the new 3D sensor there is no extra PCB necessary while the system complexity is reduced which leads to higher reliability. In addition, the TLV493D-A1B6 fulfills all the other demands for this kind of application like large field range, high resolution, temperature measurement, very low power consumption, digital output, no additional components, small package and low costs.
Joysticks and control elements
The accurate 12-bit resolution and the fast communication speed put TLV493D-A1B6 in top position for joystick applications. Non contacting magnetic sensing, high temperature stability and basically no aging effects allow the design of a novel generation of joysticks for industrial applications (e.g. man-machine interface).
Furthermore, the new 3D sensors enable cost effective and energy efficient control elements in white goods or home appliances, like user-friendly turn-push buttons. Accurate angle measurements and small system architecture allow to design new haptic end-user experience.
Evaluation board and free software
To enable a fast design and to reduce engineering time, customers can order a cheap evaluation board online (www.ehitex.com). The “3D Magnetic Sensor 2Go” Evaluation Board uses a TLV493D-A1B6 sensor and the Infineon 32-bit microcontroller XMC1100. Together with the attached magnet and the provided sensor software, first measurements can be done within minutes. Using the XMC1100 as microcontroller also offers the possibility to use the free development platform DAVE™ to develop a sensor system.
Summary and outlook on Automotive
The TLV493D-A1B6 sensor provides precise and energy efficient 3D magnetic sensing for various applications. Flexible operation modes enable dedicated and scalable system designs with a wide measurement range for accurate position sensing, while the current consumption is kept on lowest level.
Engineering samples of the TLV493D-A1B6 are available as of July 2015. Volume production is expected to start in January 2016. To serve customers in automotive market, Infineon will deduct a full AEC-Q100 qualification on the sensor. Volume production for automotive qualified TLE493D-A1B6 is expected for mid of 2016.
This first 3D sensor from Infineon marks the starting point for a 3D magnetic sensor portfolio. More 3D sensor versions will be introduced in the upcoming months.
www.infineon.com/3Dmagnetic
About the author
Hannes Birk is Marketing Manager for 3D magnetic sensors at Infineon Technologies AG of Neubiberg near Munich.
Phone: +49 89 234 26320
Email: hannes.birk@infineon.com