It could be said that ever since the Waste Electrical and Electronic Equipment (WEEE) and the Restriction of Hazardous Substances (RoHS) directives were adopted by European Union (EU) member states years ago, the electronics industry has transformed itself. Once primarily focused on manufacturing quality electronics products at low prices, the industry today has elevated its environmental concerns and is much more closely aligned with the cares of the environmental movement.
Obviously, environmental legislation in Europe and other parts of the world (China, India, and Vietnam, for example, all have similar RoHS legislation) has forced the electronics industry to wring out hazardous substances and adhere to environmental guidelines.
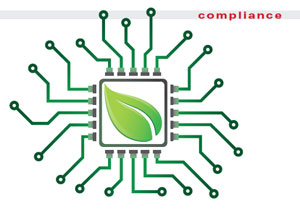
To avoid fines and major disruptions to their supply chains, electronics companies are vigilantly policing parts that make up their mobile devices, laptops, and personal computers, as well as TVs, dishwashers, and refrigerators, looking for RoHS banned substances that include lead, mercury, cadmium, hexavalent chromium, and some polybrominated flame retardants.
Companies have also had to follow the guidelines set out in WEEE, which calls for the collection and recycling of waste from a broad range of end-of-life electrical and electronic equipment products. One example of the impact this legislation is having on electronics companies can be found in a document issued by Lenovo this year, which outlines the approach the company will take to meet the WEEE requirements.
Among other commitments, Lenovo said it will design equipment with consideration to future dismantling, recovery, and recycling requirements. The company also intends to mark its products with the required symbols and inform users of their obligation to separate WEEE from general waste and dispose of it through the provided recycling systems. Additionally, Lenovo said it will facilitate the collection, recycling, and disposal of WEEE from private households and businesses as defined by the applicable member-state regulation.
Then there’s another EU regulation — Registration, Evaluation, Authorization and Restriction of Chemicals (REACH) — which governs the placement of chemical substances on the market. Under the REACH regulations, companies are required to register chemical substances manufactured or imported into the EU in quantities exceeding one metric ton per year.
These regulations as well as non-environmental legislation — such as the Dodd-Frank Wall Street Reform and Consumer Protection Act, which forces the electronics industry to disclose its use of conflict minerals, including gold, columbite-tantalite, cassiterite, and wolframite that originate in the Democratic Republic of the Congo — have prompted original equipment manufacturers, semiconductor manufacturers, component suppliers, and electronics distributors to strengthen their compliance mechanisms across their supply networks. This situation has caused companies to hire more staff, test more components, and closely collaborate with their partners as they add new business processes to comply with environmental legislation and other restrictions.
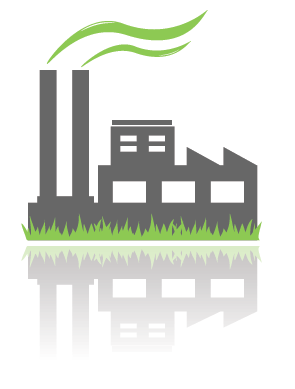
“It all starts with the manufacturers of electronics components and computer products,” said Harvey Woodford, vice president and chief compliance officer at Avnet Inc. He noted that manufacturers must invest in the due diligence, tracking, labeling, disclosure, and record-keeping processes needed to provide their customers and distributors with assurances and information on sourcing.
Furthermore, OEMs, their contract manufacturers, and component suppliers across the supply chain are required to answer several questions as they move their products along the supply network in preparation for export. According to Woodford, supply chain managers must ask themselves if their products contain certain hazardous substances that exceed RoHS limits; was forced labor or human trafficking used or supported in the manufacture of the products; and do the products contain conflict minerals?
“Ultimately, the end customer should have confidence in their upstream partners with respect to product compliance,” Woodford said. “Distributors like Avnet can support those manufacturers by passing on that information to their customers, but only if manufacturers provide the information to begin with.”
Providing information on whether electronics components are made up of hazardous substances can be an expensive task. According to Scott Wilson, solution strategist at IHS Technology Consulting, sending electronic products to a lab to be screened for hazardous substances that are banned under the RoHS directive can cost $600.
“Testing is expensive. It’s much easier to collect information than it is to take a physical device, prepare it, and perform the testing,” Wilson said.
Eric Austermann, vice president of social and environmental responsibility at Jabil Circuit Inc., said testing for restricted substances in the design phase of a product at OEMs should reduce or even eliminate the need for testing at other points in the supply chain.
Austermann noted that most of Jabil’s OEM customers design their own products and conduct testing during the design phase to collect baseline data for a particular part number.
It doesn’t really make sense to institute a lab testing process in the production phase because you are talking about different lots from different factories, all with the same part number, Austermann said. In fact, too much testing can hurt a company’s bottom line.
“When is enough enough,” Austermann asked, “in terms of being comfortable that my suppliers are telling me that the product does not have RoHS substances? There is a law of diminishing returns. You could spend thousands and thousands, maybe tens of thousands of dollars every month on testing, and what does that really provide you?”
While testing is part of the regulatory challenge, Wilson said the process of tracking products and the substances within them will provide a direct and immediate business benefit for supply chain leaders. In some cases, it can give you a competitive advantage if you become compliant or go greener before a competing company, he said.
Wilson also noted that, while compliance to environmental regulations has added paperwork and changed business process workflows, the electronics industry understands its supply chain better because of the work companies have had to do to comply with environmental regulations.
“As we understand these very complicated networks back to the material levels and understand the quantities that are represented in our finished products, we are collecting a lot more valuable information,” Wilson said. “The electronics supply chain is getting smarter.”