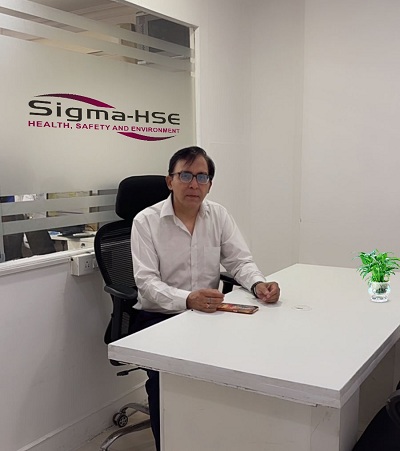
Mr. Naresh Kumar, Director of Sigma-HSE (India) Pvt. Ltd., discusses the company’s decade-long expertise in health, safety, and environmental solutions across industries like pharmaceuticals, chemicals, and electronics. Highlighting over 1,000 completed projects, he addresses key manufacturing safety challenges, occupational risks, and the need for advanced safety technologies, regulations, and training to promote safer industrial practices and align with global standards.
Tell us about your brief background and your experience in the Indian Market?
Sigma-HSE is a Technical Consulting company providing Comprehensive Solutions in the field of Health, Safety and Environment. We have our Head Office in New Delhi and our Powder Testing Lab at IIT Hyderabad with over 10+ years of experience in Pharma, Chemical, Paints, Electronics and Food Sector. We are a multidisciplinary consulting firm with 1000+ successfully executed projects PAN India & globally.
Number of various Safety Studies projects Undertaken:
- PHA Studies (HAZOP, SIL, QRA & LOPA etc) 100+ Hazop studies
- HAC, ATEX Assessment, DHA,EHA 200+ HAC studies
- Third Party Safety Audit, Electrical audit, 100+ Audits
- Fire audit, EHS Studies, Gap Analysis
- Dust Testing
Key Projects:
Projects | Key Client |
Quantitative Risk Assessment | Aker Solutions, Axalta, Dorf Ketal, Aarti Industries, Galaxy, Cipla, Mottmac |
Hazop study of Amonia plant | Chambal Fertilisers |
Hazop Study of Pharma/Chemical sector | Asian Paints, SRF, Givaudan, Anthem Biosciences, UPL, Johnson Matthey, Vasudha, Aarti, Pidilite |
PSM/Safety- Gap assessment audit/EHA | Pidilite, Cipla, TEVA, Atul Ltd, Galaxy |
Safety Trainings ( PSM/Electrical Safety/ Fire & Explosion Hazard Training/ Hazop/HAC/QRA/FMEA/Chemical Reaction Hazard Training/HIRA/ SIL-LOPA/Atex/CRH) | Anupam Rasayan (Training provided for 2 years in Surat and Vapi plant) for senior management, Mid level management and operator level. |
Hazardous Area Classification | Johnson Matthey, P&G, Henkel Adhesive, Cipla Ltd, Heuber |
Atex Assessment | Nestle, Perfetti, L&T, Insee Ecocycle, Cipla Ltd, |
Dust Testing | Pfizer, Croda, Unilever, P&G, GSK,Cargil, Dorf Ketal, SRF, Vesuvius, P I Industry, Global Aluminium, Ami Lifesciences, Glenmark, Metlok, Luminous, Jabil, Hikal, Aques Pharma, Jindal Steel, Tata Electronics, Salcomp |
How Sigma HSE India leverages advanced technology and methodologies to deliver accurate risk assessments and cutting-edge safety solutions?
Sigma HSE India leverages advanced technologies and methodologies to deliver precise risk assessments and innovative safety solutions tailored to meet diverse industrial needs. Utilizing cutting-edge software tools such as PHAST and PHA-Pro, the company excels in conducting Quantitative Risk Assessments (QRA), HAZOP studies, and other detailed hazard analyses. These tools provide accurate risk modelling, ensuring data-driven and actionable insights.
The consultancy adheres to international standards, including ATEX, IEC, and OSHA, to perform specialized assessments such as Hazardous Area Classification (HAC), ATEX compliance, and dispersion analysis. This ensures a comprehensive understanding of even the most complex scenarios.
Sigma HSE adopts a systematic approach to process safety by implementing advanced methodologies like Layer of Protection Analysis (LOPA) and Safety Integrity Level (SIL) assessments, ensuring the reliability and integrity of safety systems. By integrating traditional safety practices with modern techniques, Sigma HSE effectively mitigates risks and enhances operational safety.
With a client-focused approach, Sigma HSE customizes safety measures to align with specific operational challenges, ensuring practical and scalable outcomes. The company’s emphasis on leveraging technology and global best practices positions us as a leader in delivering comprehensive and forward-thinking safety consultancy services.
What are manufacturing safety challenges in India?
Manufacturing safety in India faces challenges such as inadequate enforcement of safety regulations and limited awareness among workers about safety practices. Many industries still prioritize production over safety, leading to insufficient investment in safety training, equipment, and audits. Hazardous processes and outdated technologies in small and medium enterprises (SMEs) further exacerbate risks. Poor maintenance of machinery and lack of regular inspections increase the likelihood of accidents. Non-compliance with safety standards like IS 14489 and inadequate Emergency Response and Disaster Management Planning (ERDMP) are common issues.
Another challenge is the shortage of skilled safety professionals who can implement and monitor robust safety protocols. Cultural barriers, such as reluctance to report near-misses, hinder proactive risk management. Additionally, rapid industrialization without adequate infrastructure or regulatory oversight contributes to unsafe working environments.
Addressing these challenges requires stricter regulatory enforcement, worker training, and adoption of advanced safety technologies.
What is your take on health and safety governance in the electronics production network in India & Globally?
Health and safety governance in the electronics production network in India and globally is a critical concern due to the rapid growth of the sector and associated risks. Globally, major electronics manufacturers are increasingly adopting stringent safety frameworks like ISO 45001 to ensure worker protection. Companies are focusing on mitigating chemical hazards, improving ergonomics, and ensuring compliance with international standards such as REACH and RoHS to safeguard both health and the environment.
In India, while larger electronics manufacturers often align with global best practices, smaller players in the supply chain may lag due to cost constraints and lack of awareness. Common issues include exposure to hazardous substances like lead and solvents, inadequate personal protective equipment (PPE), and insufficient safety training.
Governance can be improved by enforcing stricter compliance with local and global regulations, fostering collaboration between industry stakeholders, and promoting technology-driven safety solutions, such as real-time monitoring systems and automation, to reduce risks effectively.
What are the health hazards and occupational risks in the electronic industry in India?
• Chemical Exposure: Contact with hazardous chemicals like solvents, acids, and heavy metals (lead, cadmium, mercury) can lead to respiratory issues, skin disorders, and neurological problems.
• Ergonomic Risks: Repetitive tasks, poor workstation design, and prolonged sitting or standing contribute to musculoskeletal disorders.
• Dust and Particulate Matter: Soldering, cutting, and polishing processes generate fine particulate matter, leading to respiratory issues and allergic reactions.
• Radiation: Prolonged exposure to electromagnetic radiation from electronic equipment can cause eye strain and fatigue.
• Noise Pollution: High noise levels from machinery can lead to hearing loss over time.
• Thermal Hazards: Exposure to high temperatures during soldering and component assembly may cause burns or heat stress.
• Electrical Hazards: Risk of electric shocks or burns from faulty wiring or equipment.
• Toxic Waste: Handling or disposal of e-waste without protective measures can lead to toxic contamination and long-term health impacts.
What are the common challenges they face and how to overcome those challenges?
Workers in the electronic industry in India face various health hazards and occupational risks due to the nature of the work, inadequate safety measures, and limited enforcement of labor laws. Key challenges include:
• Worker Health Issues: Increased absenteeism and reduced productivity due to illnesses from chemical exposure, poor ergonomics, or respiratory problems.
• Regulatory Non-Compliance: Failure to meet health and safety standards can result in fines, penalties, and reputational damage.
• E-waste Management: Improper handling of toxic waste creates environmental liabilities and health risks for workers.
• Workplace Accidents: Electrical hazards, burns, and injuries increase operational downtime and compensation costs.
Overcoming the Challenges- Addressing health hazards and occupational risks in the electronics industry in India requires a combination of stringent regulations, proactive industry practices, and worker empowerment. Implementing these solutions can foster a safer, healthier, and more equitable working environment for all employees in the sector.
• Implement Safety Protocols: Enforce proper use of PPE, ventilation systems, and ergonomic tools.
• Regular Training: Provide ongoing health, safety, and e-waste management training for employees.
• Routine Health Monitoring: Conduct periodic medical check-ups and exposure assessments.
• Compliance Audits: Regularly audit facilities to ensure adherence to safety regulations.
What is your view on health and safety policies for electronics workers in India?
• Insufficient Enforcement: While regulations like the Factories Act and e-waste rules exist, enforcement remains inconsistent across small and medium enterprises.
• Need for Comprehensive Policies: Existing policies often focus on compliance but lack emphasis on preventive health measures and worker well-being.
• Limited Awareness: Many workers lack awareness of workplace hazards, safety protocols, and their rights under health and safety laws.
• PPE Availability: Personal protective equipment is either insufficient or not provided in many facilities, especially in smaller units.
• Inadequate E-Waste Management: Many facilities fail to implement proper e-waste handling practices, exposing workers to toxic materials.
• Occupational Health Monitoring: Regular health monitoring is rarely mandated, leading to delayed identification of occupational illnesses.
• Focus on Training: Policies should emphasize regular safety training and education on emerging risks like nanomaterials and radiation.
• Worker Participation: Involvement of workers in safety committees and decision-making is often overlooked but crucial for effective implementation.
• Global Best Practices: Policies should integrate international standards, such as those set by ISO 45001, to improve safety outcomes.