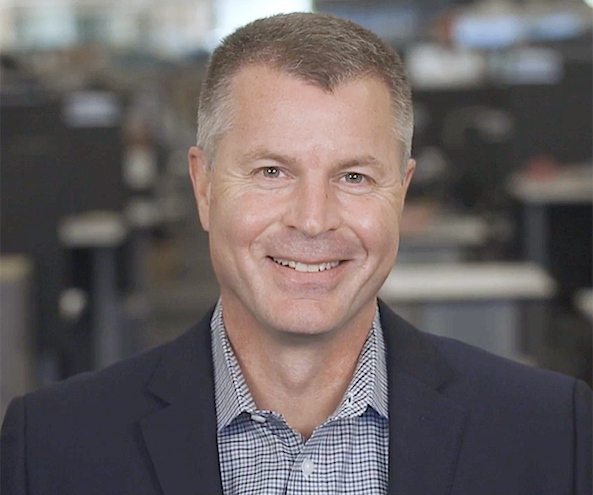
There is a new space race underway. Private companies and governments alike have set daring goals – from returning to the moon and space tourism to colonizing Mars and exploration beyond our solar system. Emerging technologies are propelling established players and start-ups to disrupt the industry through an ever quickening design cycle for space-based products such as satellites, more sophisticated payloads, and upgradeable communications systems.
With this accelerating pace of innovation, the space industry is looking to software-based automation and emulation tools to enable mission success. According to a recent Coleman Parkes Research survey commissioned by Keysight Technologies, 76% of space professionals see software test automation as one of the industry’s top challenges. Keysight’s General Manager of Aerospace, Defense, and Government Solutions Greg Patschke talks about the findings of the survey, the challenges facing engineers, and the industry’s future opportunities.
Why did Keysight commission the Defying Gravity survey?
We wanted to understand the opinions of senior leaders about where electronic system design, test, and measurement could provide value in the satellite and space industry based on current market dynamics. We’ve seen a steady ramp in innovation and non-government, private commercial investment in the satellite industry during the last five years and wanted to confirm the industry’s transition from large, geosynchronous earth orbit (GEO)to smaller low earth orbit (LEO)satellites enabled by the drastic reduction in launch costs.
Software test automation was identified as the top technical challenge. What makes this so challenging?
The complexity of a satellite, along with its nature as a “system of systems” that is part of a larger system, makes testing and evaluation a critical aspect of ensuring mission success. Even lower cost satellites must be thoroughly validated on the ground before launch, from early design through manufacturing and operation. Plus, with the higher number of satellites being constructed, we are transitioning away from single satellite production model into a volume production situation where satellite factories are producing one or more satellites per day. This means it is impractical, if not impossible, to produce a satellite and verify its functionality manually. Human error, along with the need for consistency during multiple rounds of satellite system testing, make it critical to have strong process automation to eliminate possible defects.
How can automation be implemented into the product lifecycle?
There are two major areas. One is in the design-to-manufacturing test lifecycle, as we have discussed, where high volume manufacturing necessitates a large volume of tests. This can be addressed with automation using modern, scalable, and open software platforms running both built-in self-tests and outboard test equipment with cloud-enabled software services to run the factory floor. The second area is using a software platform to automate the testing of a space vehicle operation and its control system software. This can include emulating real world conditions to test the satellite’s flight software, the software that enables the human-machine interface to the satellite, or the space vehicle’s operations control systems.
What other technical challenges are engineers facing?
As you can imagine, doing anything in space in not easy and when it comes to human-capable space vehicles, failure is simply not an option. Designing for high reliability, while optimizing for power efficiency and longer than a five-year lifetime is extremely challenging and must be thoroughly tested before a mission. Another challenge is the use of radio frequency(RF) spectrum in communication satellites to ensure sufficient RF power and bandwidth as well as steering RF signals to precisely where they are needed. Low-cost phased array antennas are enabling improvements in this area as are developments in free space optical transmission that enable satellites to connect with each other over high capacity laser links and route data based on the best connectivity to an earth ground station.
What is driving the industry’s focus on shortened development cycles?
With the new space industry, there is a “gold rush” mentality that is driving areas such as SATCOM as well as earth imaging and sensing. There are hundreds of new startups chasing new business models with tremendous time-to-market pressures to win business. Additionally, the US Government and other nations are looking to take advantage of commercial innovation by simplifying their acquisition rules to make it easier for smaller, non-traditional commercial companies to compete for contracts.
What other trends are you seeing?
In addition to faster development cycles, we’re seeing the increased use of modeling and other “digital twin” tools to predict performance with an emphasis on failing fast and early–ideally in simulation. The industry is also making use of lower cost commercial electronics, often automotive-grade in design and certainly with less stringent testing. We are also starting to see some interesting partnerships and collaborations being announced between early-to-market LEO satellite communications providers with terrestrial wireless network operators – such as SpaceX with T-Mobile and Amazon Kuiper with Verizon – to provide extended mobile coverage. Also interesting is that the US Government is seeking to procure more of their SATCOM services from the commercial sector to potentially augment their military Satcom capabilities at a much lower cost.
What major opportunities do space companies have over the next five years?
We are already seeing the commercial viability of high-resolution satellite imaging – more often in the public domain than with US government assets – for applications such as capturing and reporting on natural disasters and intelligence gathering in warzones. Global satellite-based communications for broadband and narrowband applications now appears to be coming at us very quickly. While some business models have yet to be proven, firms like OneWeb and SpaceX Starlink are leading the way with global connectivity for pretty much anywhere on the planet.
In the non-satellite realm, commercial launch has already been proven by SpaceX and commercial crew programs like Dragon and Boeing Starliner are pointing to more commercial development and deployment of space assets. Multiple companies are now working on a commercial space station, which is expected in the 2030s and possibly even a commercially-funded venture on the moon or to asteroids. It’s a very exciting time to be in the space industry!
How is Keysight helping address these challenges?
Keysight’s goal is to enable customer success along their project and program life cycles – from early design and development through design validation, prototyping, manufacturing, and operations – we want to be an indispensable mission partner. Our network simulation and electronic system-level design tools like EXatascalable network technologies and PathWave Design can interoperate with industry leading Systems Toolkit Software from Ansys Government Initiatives (AGI), allowing system engineers to develop high fidelity digital twins early in the concept of operations (CONOPS) development phase. From there engineers can take their designs to the operations lifecycle with links to our RF and network test and emulation equipment to mimic real-world conditions in the lab. And with the recent acquisition of Eggplant, Keysight can also test operational system control software using automated processes. Our frequency and signal monitoring tools along with our key solution partners, which include Kratos, Integrasys, and Calian, can provide ground support and monitoring equipment for the commissioning and operational phases of the satellite and space vehicle lifecycle.