Searching for Sustainability in the Semiconductor Industry
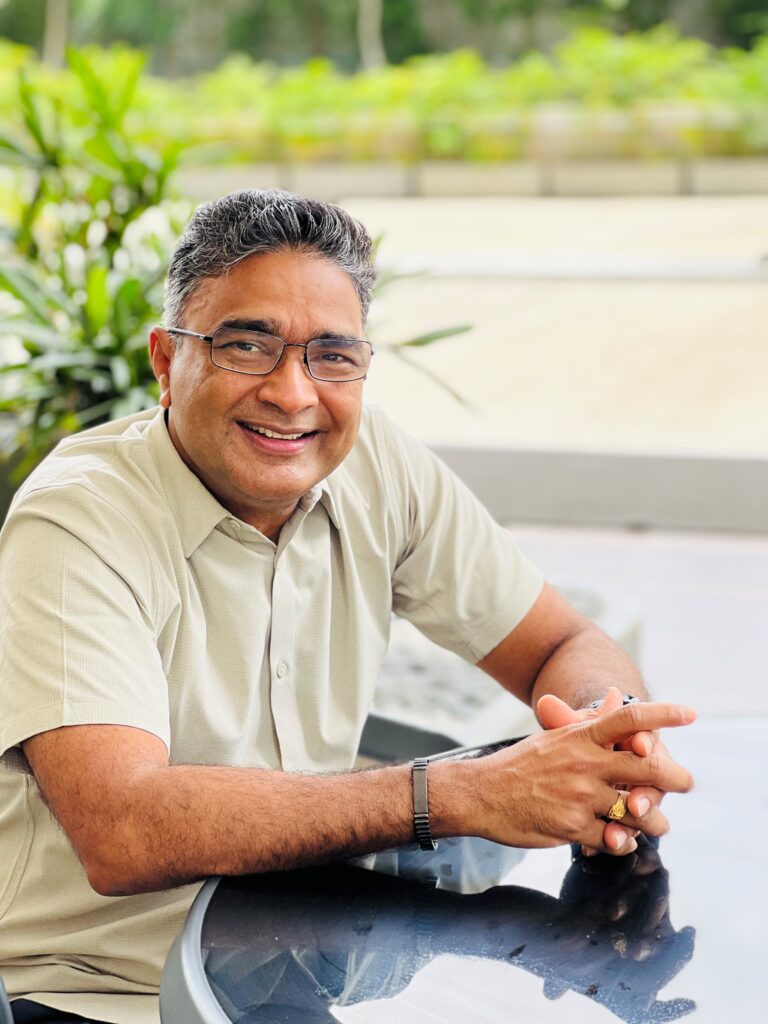
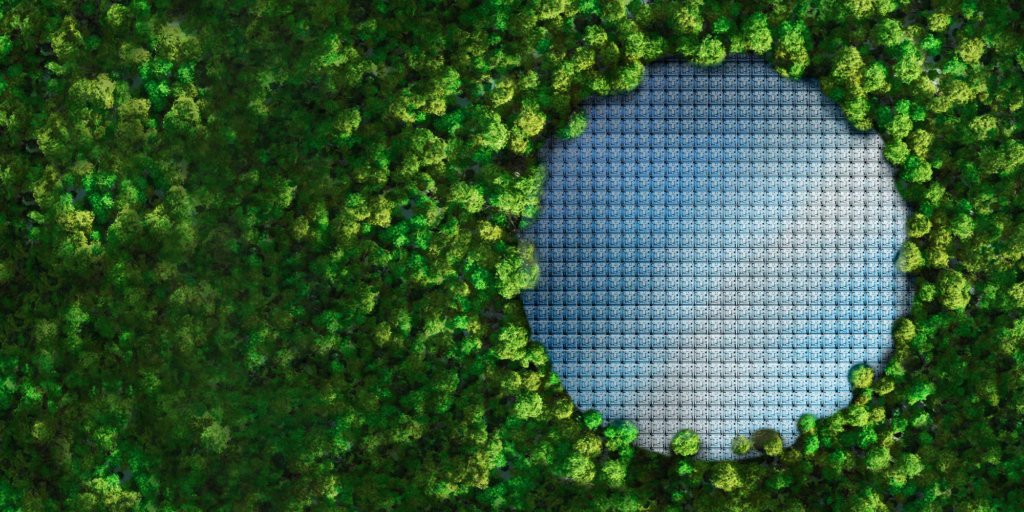
Amid an oxymoronic phase, the semiconductor industry has been working tirelessly to match high demand—with the industry in 2022 having been expected to ship the most semiconductors historically. This is despite the gloomy overall market and economic outlook set against a raging geopolitical storm. However, the need for silicon chips is ubiquitous and will only rise as we innovate to bring out the next smartphone or put the latest aircraft in the sky.
Semiconductor manufacturing activity, aided by several ongoing and proposed projects, will inevitably meet the high demand—but this could come at a cost. A response of such a massive scale brings up the conundrum of staying sustainable and being energy efficient in the face of increased production. Energy is a critical component of semiconductor manufacturing, which—in turn—is equally integral in impacting the climate crisis. The combined carbon footprint of all semiconductor manufacturing-related activity can be astonishingly large, and companies that were once passive are already looking to create more sustainable working environments with determined carbon goals.
Companies can no longer wait and watch, with the conversations around climate reaching a fevered pitch. Businesses are carefully watching energy usage across entire supply chains; in many cases, fabs will account for a hefty portion of these emissions as they incessantly mine millions of gallons of water, energy, and greenhouse gases (GHG). Companies have slowly begun to react to this fact and are actively pushing for change in reform and setting climate goals. There is a skew across companies approaching sustainability. Some have wholly committed to net-zero goals, while others are still deliberating on going beyond merely offsetting emissions and setting their own emission goals. These include individual GHG emissions targets, investing in energy savings, carbon-neutral goals, and more in ambitious timeframes.
These individual goals can seem ill-conceived when viewed against countries’ long-term production-based targets. While we will have to wait and watch how companies’ plans pan out, what is evident is the need closely involve stakeholders across the research, innovation, and production lines to consider best practices, identify gaps, and answer them. A little illustration of innovative thinking: Various manufacturers are already employing technologies to help recycle water, contributing to reduced scope 1 and 2 emissions. And more will have to be done to limit the emissions from energy-intensive subsystems, gas abatement systems, and massive artificially controlled clean rooms.
But the quest for reduced carbon emissions in fabs is rarely straightforward. While desiring to reduce emissions, companies are unsure where to apply their efforts. It becomes essential to understand where efficiency probabilities lie and to target those areas of production or revamp utility buildings. Besides the manufacturing process and design-related energy expenditure, scope 2 electricity consumption from working the tools and powering the facilities are also responsible for high energy requirements, and companies must assess where they can rein in these losses based on their operations. Another area for companies to ponder is the outright cost associated with energy goals: Sustainable roadmap executions can vary depending on the capital available to companies. While some fabs might be content with solar power fittings, others might have the financial pull to overhaul entire plants. In this regard, industry-wide collaborations are aiding companies with investments towards energy efficiency. Accounting for cost and efficiency will primarily shape the industry’s future when it comes to reducing its carbon footprint.
Concern remains over the effects of essential process gases on the environment. Moving to less-polluting alternatives like fluorine and cleaner tool cleaning gases is a step forward. Further, central abatement systems and various other methods can increase gas abatement in fabs while companies must figure out the most efficient ways to keep harmful by-products low. Successful research into gas recycling could signal a landmark moment wherein process gases can be reused in a system, reducing harmful emissions.
In the quest for a green future, merging efforts across allied industries will be imperative for long-term viability. More cohesive partnerships spanning the entire length of the supply chain can have a knock-on effect in helping reduce carbon emissions at individual points in the link. Energy-efficient practices in the semiconductor industry can possibly give rise to other green outcomes in end-stage customer operations further down.
Broader sustainability and net-zero strategies will enter the picture as fabs expand worldwide: Addressing scope 3 emissions upstream and down stream of supply chains will become more pertinent under these circumstances. As they grow their footprint, expect companies to consider making fabs more efficient in design, intelligently segregating segments based on energy requirements. Computing power could also be exploited to use data to understand when systems/tools are idle and automatically shut them down. All of this will contribute to tremendous energy savings.
Now, we move to semiconductor products and how they impact the carbon-print. Higher performance in computing and associated sub-systems will consume huge amounts of power to meet the future AI model training and data centre computing. Energy efficient computing the name of the game in the next few decades and it is a green field for many companies to innovate and impact the industry going forward.
The future depends on a vision that assimilates the best in engineering and innovation and uses it to accompany sustainable climate policies within companies and the regions they’re located in. Manufacturers can always lean into their healthy margins and funnel resources into adapting green measures, mixing traditional collaborations with data-based practices to create intuitive factory floors that are inherently green. Companies must remember to not only turn to renewable energy but understand how to use it and reduce power consumption if they’re to meet their climate goals.