In Long-Distance Industrial Automation Deployments
Rich Miron, Digi-Key
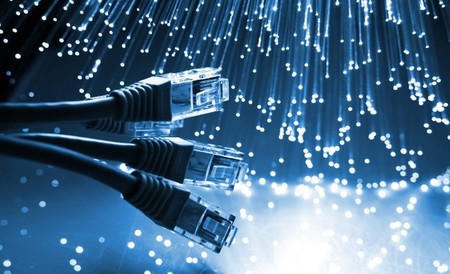
Twisted-pair Ethernet cabling is considered a mature and reliable technology that has been trusted with 10Base-T and 100Base-T data rates for many years. However, as high-speed Ethernet traffic reaches 1 gigabit per second (Gbit/s) and higher, designers have to deal with the reality that signals are less forgiving of cable inconsistencies and become more susceptible to interference, crosstalk, impedance loss, return loss due to reflected signals, and attenuation.
The issues are exacerbated as cable lengths increase, such as in industrial automation facilities. These have the added complication of twisting and bending of Ethernet cables during layout, as well as in applications such as robotics and other machinery. This repeated flexing can separate the twisted pairs, compromising the cable’s electrical performance. The resulting signal attenuation can introduce intermittent data losses that worsen over time. These types of errors are notoriously difficult to identify and troubleshoot, causing lengthy and expensive system downtime.
This article discusses the challenges of sending high-speed digital Ethernet data over twisted pair conductors. It explains how bonded-pair Ethernet cables can be used to provide consistent performance for high-speed Ethernet data over long distances, including reduced signal loss and resistance to physical abuse. It will then introduce two examples of bonded-pair Ethernet cables from Beldenand show how they can be used to ensure Ethernet signal integrity in industrial environments.
Reliably sending gigabit Ethernet data
Standard Ethernet cables send data over twisted-pair copper conductors. In the past, less expensive cables might only use two twisted pairs, but modern conventional Ethernet cables have four twisted pairs for high-speed data transfer and Power over Ethernet (PoE) delivery. All Ethernet cables suffer signal degradation to some degree due to cable construction, cable length, interference, and data rate. If high-speed data is sent over 10meters (m) or more of cable, it is the cable construction that is responsible for preventing excess signal degradation.
Most commercial and low-speed industrial Ethernet cables use twisted pairs of stranded copper conductors. Stranded copper is very flexible and easy to work with, resulting in a cable that can be bent around corners and that stays in place when taped down on floors and mounting points. However, stranded copper wires have greater resistance to current flow than solid copper wires, especially over long distances. This makes solid copper wires more appropriate for high-speed data, which typically uses lower signaling voltages, making high-speed data more susceptible to signal attenuation and data loss due to wire resistance. For PoE, solid copper can also carry more current and generates less heat compared to stranded copper, making it a more appropriate option. The drawback of solid copper is that it does not flex well and resists bending more than stranded copper, and so may require some additional effort when laying out the cable.
Twisted-pair Ethernet cables present a characteristic impedance to the receivers and transmitters at the RJ45 plugs. Typically, this impedance is 100 ohms (Ω) and needs to be consistent along the length of the cable. Impedance is affected by the center-to-center distance between the two conductors in the twisted pair. Impact with a heavy object or the stresses associated with stretching or squeezing a cable can separate the twisted pairs, changing the center-to-center distance in some sections. This results in a cable impedance change that degrades the signal. This may not be noticeable at rates of10 megabits per second (Mbits/s) (10Base-T) or 100 Mbits/s (100Base-T)speeds but can cause data loss at gigabit speeds (1000Base-T).
Crosstalk is another cause of signal degradation. Running two high-speed wires in parallel will result in each conductor inducing a current in the other wire, which is the worst-case situation for crosstalk. To minimize the risk of crosstalk and signal losses, wires are run in self-shielded twisted pairs. However, as with impedance loss, if the two wires in the twisted pair are shoved or moved out of place by external forces on the cable, it increases crosstalk between the pairs, reducing signal reliability.
The combination of impedance loss and crosstalk, combined with the electrical resistance of the cable over distance, causes return loss due to the reflection of the signal back to its source. While return loss is expected and is compensated for using echo cancellation at the terminations, excess return loss can be a serious problem resulting in intermittent data loss. This problem can be notoriously difficult to diagnose and can result in excessive downtime. The problem can be exacerbated in high-vibration industrial environments where the Ethernet cable’s position is shifting and causing changing electrical characteristics, resulting in data signal problems that mysteriously disappear when the vibration or movement ceases.
Bonded-pair Ethernet cables
As discussed, impedance loss, crosstalk, and return loss are all heavily influenced by inconsistent center-to-center distance between the twisted pair along the length of the cable. For designers routing high-speed Ethernet connections in harsh environments, Belden has addressed the problem with its 10GXCAT6 and CAT5E bonded-pair modular Ethernet cords for gigabit Ethernet.
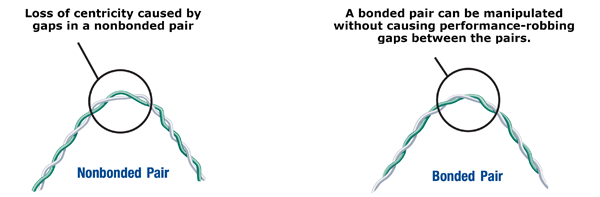
Bonded-pair cables maintain a fixed conductor-to-conductor centricity between the twisted pair conductors by physically bonding them together, preventing even temporary separation (Figure 1). This greatly reduces the risk of impedance loss and crosstalk.
Belden bonded-pair Ethernet cables also use solid copper conductors for the twisted pairs, reducing electrical resistance. In addition, solid copper conductors allow more power with less loss compared to stranded copper wires for PoE applications. This also improves safety by reducing heat caused by cable resistance.
Taken together, reducing the electrical resistance of the cable, reducing impedance loss, andminimizing crosstalk, results in significantly improved data integrity for gigabit Ethernet, even in harsh environments.
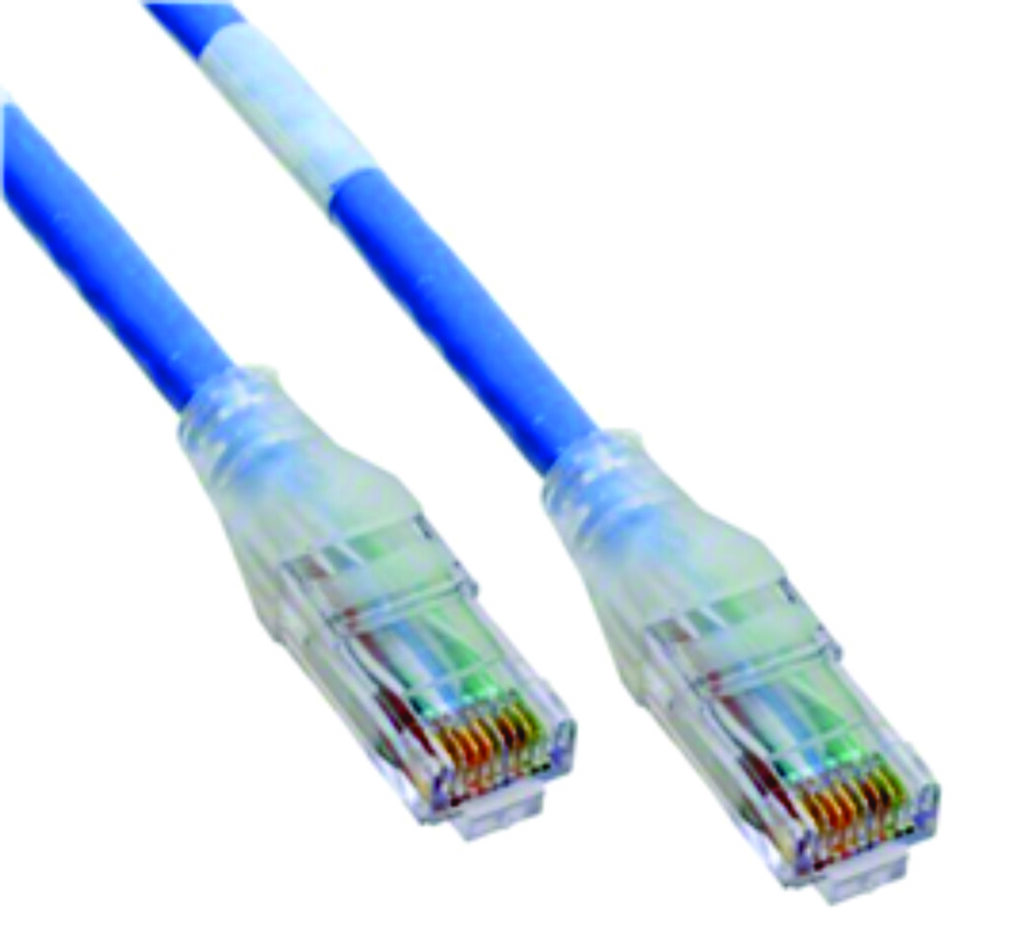
For gigabit Ethernet patch cords, Belden provides the C601106010 10 foot(ft.) bonded-pair Ethernet cable assembly (Figure 2). It is a CAT6+ cable assembly with four bonded twisted pairs of 24 AWG solid copper wire. The ends are terminated withRJ45 plugs with an elastomer boot molded to the polyvinyl chloride (PVC) outer jacket, forming a strong strain relief that resists separation. It also prevents twisting or separation of the twisted pairs at the RJ45 termination, as well as providing protection against water and dust.
The blue Ethernet cable is 5.715 millimeters (mm) in diameter, typical for an Ethernet cable. Since the bonded pairs and solid conductors do not add any additional bulk to the cable assembly, the C601106010 is appropriate for any application where commercial cables would be routed.
The cable assembly has a current rating of 1.500 amperes(A) per contact. Combined with the gigabit speed rating, the C601106010 is appropriate for industrial PoE applications such as robotics and Industrial Internet of Things (IIoT) endpoints. The maximum contact resistance is 0.020 Ω, which at 1.500 A generates a mere 0.300 watts of heat, an acceptable amount for industrial applications.
This CAT6+ cable assembly is rated for 1000Base-T applications and has a -10°C to +60°C operating temperature, making it appropriate for high-speed industrial automation applications with wide temperature extremes.
For longer distances, Belden makes the CA21106025 25 ft. bonded-pair Ethernet cable assembly. It is a CAT6a cable assembly with the same basic electrical specifications as the Belden C601106010, and the same termination seen in Figure 2. However, because the CA21106025cable is longer, it is more susceptible to external interference: gigabit speeds over a 25 ft cable act as an antenna that can pick up electromagnetic radiation from surrounding electronics. To ensure signal integrity, the CA21106025has an aluminum foil outer shield. This results in a diameter of 6.731 mm which is slightly larger than commercial cables, but well within tolerances for cable guides and common routing methods.
With this shielding, the Belden CA21106025 cable assembly is rated for10GBase-T (10 Gbits/s) rates, making it suitable for very high-end industrial automation applications, as well as for streaming high-definition video throughout a facility.
Conclusion
Gigabit Ethernet is bringing higher data rates to industrial automation facilities. With these data rates comes the increased risk of interference, crosstalk, and return loss which can result in intermittent data connections. This is particularly true in industrial applications where the cable may be subject to repeated bending, causing loss of cable electrical performance. Using bonded twisted-pair Ethernet cables that ensure a fixed center-to-center centricity, designers can comfortably use higher speeds over greater distances, while meeting PoE requirements for network upgrades and new deployments.