Can Be Used with Input Voltages Above or Below the Level of the LED String
By Victor Khasiev, Analog Devices
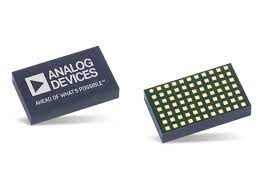
The LTM8042 can be easily configured in three topologies—boost, buck, and buck-boost—to meet a wide variety of specific application requirements. For low input voltages and high string voltages, a boost topology is appropriate, whereas a buck is more suitable for high input voltages and low string voltages. A buck-boost topology is used for a wide range of inputs where voltage can be below or above the LED string. This article covers the process of selecting the suitable topology and its corresponding connections.
Boost LED Driver
The most common topology for an LED driver is a boost application, as might be used for an LED array powered from a 12 V input rail, where VIN < VF. An LTM8042 boost solution is shown in Figure 1 with a block diagram shown in Figure 2. The input voltage is connected to the BSTIN/BKLED– terminal and the LED string cathode is connected to GND. When transistor Q is on, the current builds up in the inductor L. Once Q turns off, the voltage across L changes polarity and the inductor current begins flowing to output filter capacitor C2. LED dimming is implemented in the PWM section, which regulates the duty cycle, and by extension the average LED current (set by resistor RCLR). Capacitor C1 is an input voltage filter.
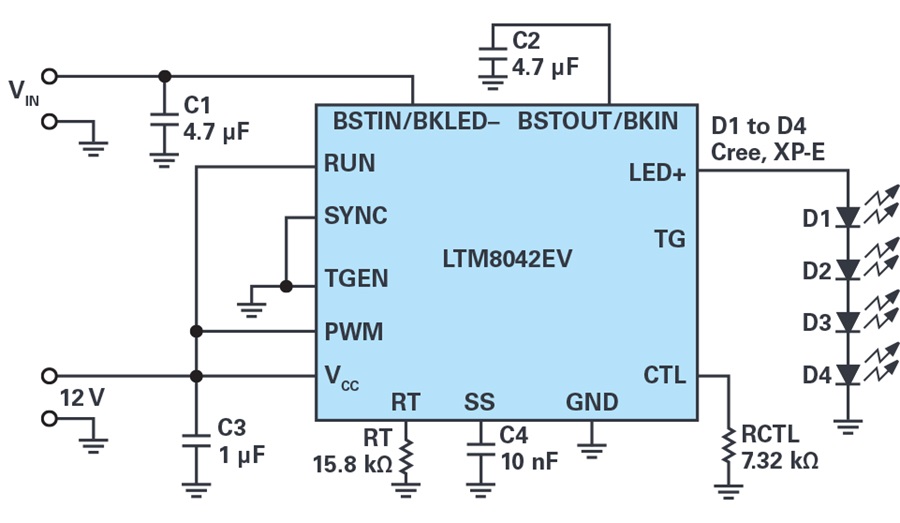
Figure 1. The LTM8042 driving four LEDs where VIN = 5.75 V to 10.25 V and IOUT = 0.5 A.
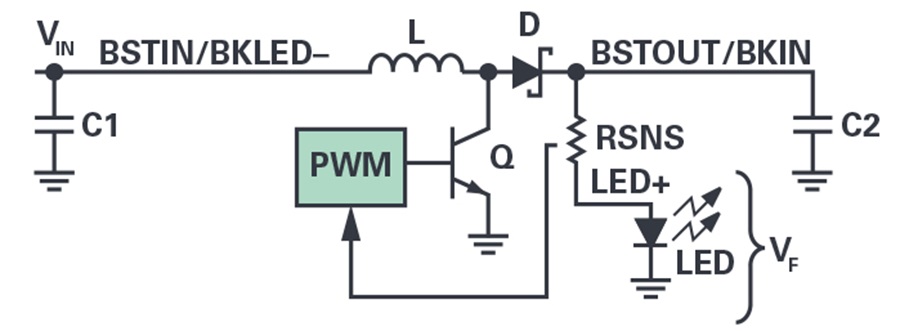
Figure 2. LTM8042 block diagram connections in boost configuration.
Buck LED Driver
A buck topology is used for relatively high input voltages, such as automotive and industrial 24 V rails. Figure 3 shows a block diagram for a configuration for VIN > VF. The input voltage connected to the BSTOUT/BKIN terminal and LED cathode connected to the BSTIN/BKLED– terminal. When transistor Q is on, current flows from the input through the LED string and inductor L to GND. Once Q turns off, the voltage across L changes polarity and diode D becomes forward biased, pulling the LED cathode below the input voltage level, providing the set value of the current in the LED string. C5 creates an output filter for this topology.
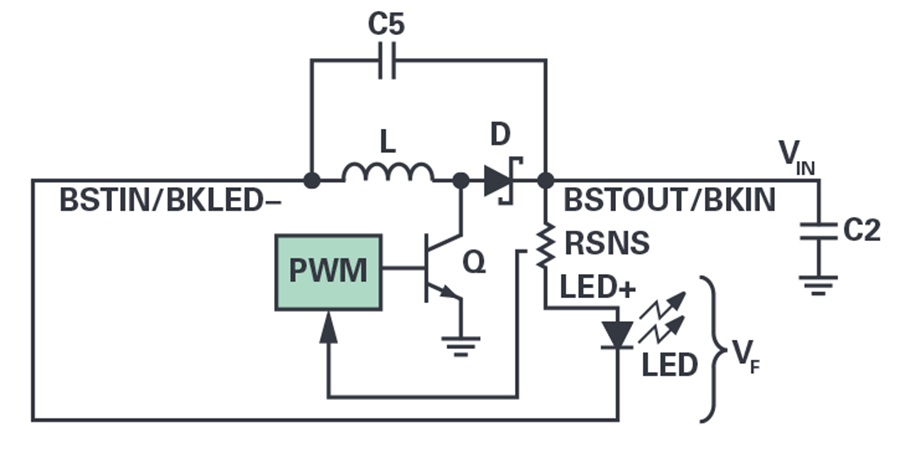
Figure 3. LTM8042 block diagram connections in buck configuration.
Buck-Boost LED Driver
In many commercial, battery, and solar-powered applications, the input voltage varies over a wide range. In these situations, the buck-boost topology shown in Figure 4 is best. The input voltage and LED cathode are connected to the BSTIN/BKLED– terminal. When transistor Q is on, the current builds in inductor L. Once Q turns off, the voltage across L changes polarity, forward biasing diode D while the voltage climbs above the input level. The PWM maintains the set value of current through the LED and C5, and the C2 functions as an output filter. The LED string voltage VF can be below or above VIN.
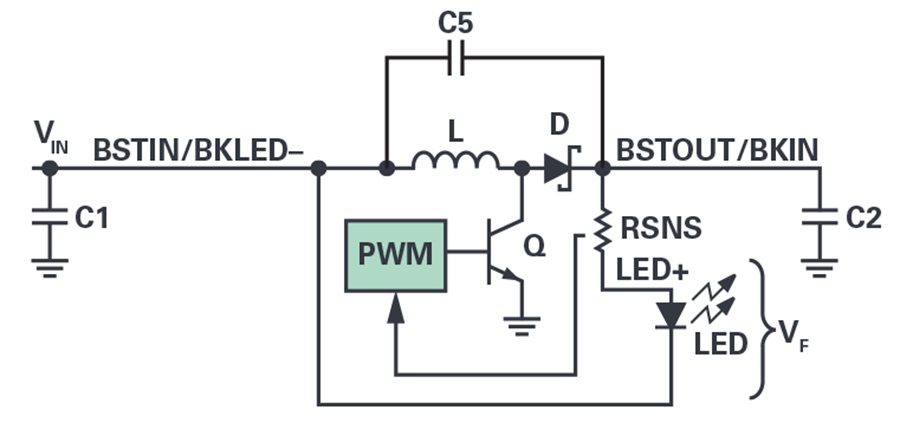
Figure 4. LTM8042 block diagram connections in buck-boost configuration.
Test Results for the Three Topologies
All three topologies were tested using the DC1511 demonstration circuit featuring the LTM8042—using the same LED string, output current, and switching frequency in all cases. To make sure that bias power dissipation is the same for all three settings, the same VCC (shown in Figure 1) was supplied as well. The VCC pin can be tied to VIN in most cases. Figure 5 shows the resulting efficiency curves. All three topologies were also modeled in LTspice® environments and simulation files related to LTM8042 can be found in its data sheet.
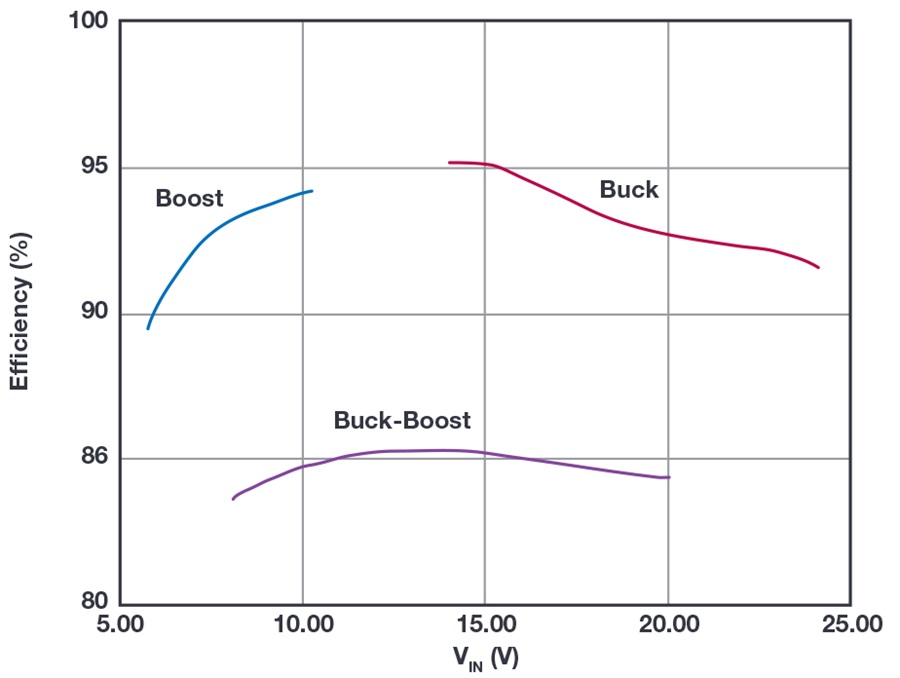
Figure 5. LTM8042 efficiency for boost, buck, and buck-boost configurations.
Conclusion
LTM8042 is a versatile and efficient LED driver capable of operating over a wide input voltage range, while providing up to 1 A LED string current. The LTM8042 is easily applied as a boost, buck, or buck-boost driver to satisfy the needs of a wide variety of applications.
Author
Victor Khasiev was a senior applications engineer at ADI with extensive experience in power electronics both in ac-to-dc and dc-to-dc conversion. He holds two patents and has written multiple articles. These articles are related to using ADI semiconductors in automotive and industrial applications. Topics cover step-up, step-down, SEPIC, positive-to-negative, negative-to-negative, flyback, forward converters, and bidirectional backup supplies. His patents include efficient power factor correction solutions and advanced gate drivers. Victor enjoys supporting ADI customers by answering questions about ADI products, designing and verifying power supply schematics, laying out printed circuit boards, and troubleshooting and participating in testing final systems.