By Yigit Yoleri , Applications Engineer and Guixue (Glen) Bu , Applications Engineer
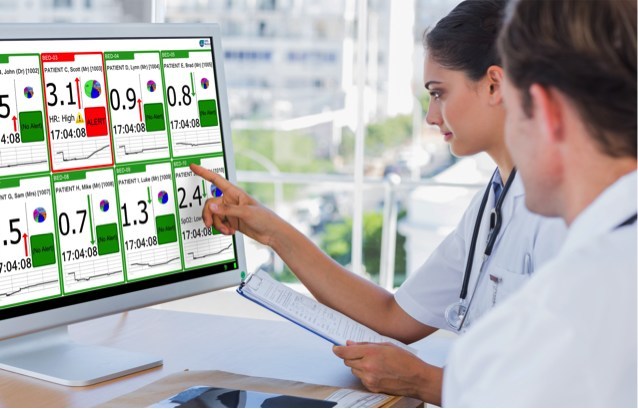
The last decade has witnessed drastic improvements in mobile, wearable, and digital health fields. In particular, there is rapid expansion and adoption of digital healthcare fueled by the continuous advancement in electronics and recent breakthroughs in cloud computing, artificial intelligence (AI), and communication technologies such as the Internet of Things (IoT) and 5G. Some of the vital signs monitoring (VSM) capabilities have been built into phones, watches, and other smart wearable devices, and thus have become accessible to a much broader population. Increased awareness about health has given rise to the demand for small but high accuracy devices that can measure various vital signs and health markers such as body temperature, heart rate, respiration rate, blood oxygen saturation level (SpO2), blood pressure, and body composition. In particular, the COVID-19 pandemic has caused a surge in demand for devices capable of monitoring multiple vital signs, including temperature, SpO2, and heart rate both in hospitals and at homes. The need for small and convenient health tracking devices, preferably smart wearables, has reached historically high levels.
Adding multiple sensing capabilities to such small devices has its challenges, calling for a smaller form factor, lower power consumption, and multiparameter capabilities with significantly improved performance. However, this can now be achieved through a single analog front-end solution. This new AFE functions as a multiparameter vital signs monitoring hub for synchronous measurements.
It offers low noise, high signal-to-noise ratio (SNR), small form factor, and low power consumption, enabling significant improvements to medical devices, especially wearable technology. For doctors, patients, and consumers, this makes vital signs monitoring easier than before with higher performance, longer battery life, and greater accuracy without the intrusive discomfort of multiple devices. This article discusses some of the breakthrough capabilities and features of this single analog front-end solution.
An Overview of the New Analog Front End
The ADPD4100/ADPD4101 is a multimodal sensor AFE that has eight analog inputs and supports up to 12 programmable time slots. The 12 time slots can enable 12 separate measurements in a sampling period. The eight analog inputs are multiplexed into a single channel or two independent channels, enabling simultaneous sampling of two sensors, either in a single-ended or differential configuration. There are eight LED drivers that can drive up to four LEDs simultaneously.
These LED drivers are current sinks and are independent of the LED supply voltage and LED type. There are two pulsed voltage sources for voltage excitation. The new AFE’s signal path consists of transimpedance amplifier (TIA), band-pass filter (BPF), integrator (INT), and analog-to-digital converter (ADC) stages. The digital block provides multiple operating modes, programmable timing, general-purpose input/output (GPIO) controls, block averaging, and a selectable second- to fourth-order cascaded integrator comb (CIC) filter. Data is read directly from the data register or through first-in, first-out (FIFO) method.
There are two variations of this new AFE. One features an I2C communication interface, and the other has an SPI port. One of the advantages of the ADPD4100/ADPD4101 relates to optical measurements. Its superior, automatic ambient light rejection capability uses pulses as short as 1 μs in a synchronous modulation scheme combined with the BPF, eliminating the need for external control loops, dc current subtraction, or digital algorithms. A decimation factor higher than 1 can be used to increase the output SNR. There is a subsampling feature that allows selected time slots to run at slower sampling rates than the programmed sampling rate to save power, where power is proportional to the sampling rate. There is also a TIA ceiling detection feature, which uses voltage comparators at the output terminals of the TIA to set the interrupt bit when the TIA input exceeds typical operation limits.
The ADPD4100/ADPD4101 is an ideal hub for various electrical and optical sensors in wearable health and fitness devices for heart rate and heart rate variability (HRV) monitoring, blood pressure estimation, stress and sleep tracking, and SpO2 measurement. This new multiparameter VSM AFE’s multiple modes of operation can accommodate various sensor measurements, including but not limited to photoplethysmography (PPG), electrocardiogram (ECG), electrodermal activity (EDA), body composition, respiration, temperature, and ambient light measurements in healthcare applications.
PPG Measurement
PPG measurement detects the blood volume change in the microvascular bed of the tissue associated with each cardiac cycle. The total absorption of light correlates with changing blood volume due to systole and diastole events, producing a PPG signal. PPG measurement is performed by pulsing an LED light into human tissue, and collecting the resultant reflected/transmitted light with a photodiode, which converts light to photocurrent. The ADPD4100/ADPD4101 processes and measures the photocurrent and produces the digital PPG signal.
Without any change to the hardware connection, the AFE can be flexibly configured to operate in four different modes for different PPG measurement use cases: continuous connect mode, multiple integration mode, float mode, and digital integration mode.
Continuous Connect Mode
Continuous connect mode is the typical mode for PPG measurements. It provides the best ambient light rejection and provides high SNR. It works well with a charge transfer ratio (CTR, photocurrent over LED current) level as low as 5 nA/mA to 10 nA/mA and can pr ovide 95 dB to 100 dB dc S NR. These levels can be increased with increasing decimation factor. It uses the full analog signal path, TIA + BPF + INT + ADC. Incoming charge is integrated once per ADC conversion.
In a single stimulus event like PPG, most of the dynamic range of the integrator is used when the charge from the sensor response is integrated. The TIA is connected continuously to the inputs after the preconditioning period; therefore, the input signal is not modulated. To reduce the noise, the anode of the photodiode is preconditioned to the reference voltage of the TIA (TIA_VREF). TIA_VREF is typically set to 1.27 V to get the largest dynamic range of the TIA. The cathode of the photodiode is connected to a cathode voltage source (VCx) pin, and the device is typically set to provide TIA_VREF + 215 mV to the cathode of the photodiode to create 215 mV reverse bias across the photodiode. This reduces the noise of the signal path and the photodiode capacitance. In this mode, typical LED pulse width is 2 μs. Short LED pulses provide the best ambient light rejection performance. The use of multiple LED pulses increases the SNR by 3 dB for every doubling of the pulse number. Integrator chopping is typically enabled to get the highest SNR, since chopping eliminates the low frequency noise content from the integrator. Higher TIA gain selection results in lower input referred noise, but reduces the dynamic range of the TIA. The dynamic range of the TIA is calculated by dynamic range = (TIA_VREF)/(TIA gain). In order to increase the ADC saturation level, TIA gain can be reduced, or integrator resistor can be increased. Higher integrator resistor selection results in lower noise, but lower integrator resistor selection increases the ambient light headroom.
Multiple Integration Mode
Multiple integration mode is the same as continuous connec t mode, except the incoming charge is integrated multiple times per ADC conversion. This mode is useful in getting high SNR in low light cases because it uses a small amount, sometimes less than 50% of dynamic r ange per stimulus e vent.
Therefore, it allows for the utilization of a larger amount of the integrator dynamic range due to multiple integration prior to ADC conversion. Every doubling of the number of integrations per ADC conversion results in a 3 dB increase
in SNR, which is the same effect as doubling the number of pulses. Since this mode is typical for small inputs, the highest TIA gain is selected. This mode is used in the cases where CTR is lower than 5 nA/mA and good ambient light rejection is needed.
Float Mode
Float mode is also used in low light cases to get high SNR. Float mode allows for noise-free charge accumulation on the photodiode. The photodiode is disconnected from the AFE—and therefore floats—and accumulates charge, due to light, in a noise-free manner. Then, the AFE is connected back to the photodiode, the charge on the photodiode rushes into the AFE, and the integration is done in a way that allows the maximum amount of charge to be processed per pulse with the minimum amount of noise added by the signal path. The dumping of the charge occurs quickly with short modulation pulses; therefore, the noise addition due to the signal path is smaller. Also, the float time can be increased to achieve higher signal levels, but there is a limit to the amount of charge that the photodiode’s capacitance can accumulate. In this mode, the band-pass filter (BPF) is bypassed because the shape of the signal produced, when transferring the charge from the photodiode by modulating the connection to the TIA, can differ across devices and conditions. To reliably align the signal with the integration sequence, the BPF must be bypassed.
This mode does not provide good ambient light rejection performance, and it is limited by photodiode capacitance, but it provides a power-efficient and less noisy measurement in very low light conditions.
Float Mode vs. Multiple Integration Mode Selection for Low Light Conditions
In low light conditions with CTR <5 nA/mA, the typical mode of operation is float mode. It offers lower noise than multiple integration mode, because multiple integration mode requires more integration cycles, leading to higher TIA and integrator noise contributions. Float mode is also more power-efficient than multiple integration mode as the BPF is powered down and the measurement time is smaller. Therefore, SNR per watt efficiency is significantly higher in float mode. When the photodiode is leaky or there is a significant amount of ambient light present in the PPG measurement, multiple integration mode is preferred. Leaky photodiodes can’t be used with float mode because the charge leaks off instead of being accumulated before the fast charge dump occurs. If the ambient light is significant, float mode is unfavorable, because ambient light dominates the amount of charge that can be stored on the photodiode. Multiple integration inherently offers excellent ambient light rejection due to the use of BPF and short LED pulses.
Digital Integration Mode
All the modes that have been mentioned so far use the integrator to integrate the incoming charge. Digital integration of the ADC samples is also possible through the digital integration mode. To achieve digital integration, the integrator is converted into a buffer. Digital integration mode works in two regions. In the lit region, the LED is pulsed and in the dark region the LED is off. ADC samples are taken at 1 μs intervals within the lit and dark regions and are integrated digitally. The signal is calculated by the subtraction of the integration of the dark samples from the lit samples. This mode can support longer LED pulses; therefore, it is the typical mode of operation where the photodiode has a slower response time and requires longer pulses. The BPF is bypassed and powered down. Digital integration mode provides the best power efficiency and results in the highest achievable SNR levels. However, ambient light rejection is subpar to that of continuous connect mode, due to longer LED pulses and bypassing of the BPF. Digital integration mode cannot support simultaneous sampling of tw o channels during the same time slot. Digital integration mode can support 100+ dB dc SNR.
The Advantages and Disadvantages of Digital Integration Mode
As mentioned previously, the typical mode of operation for PPG measurements is continuous connect mode as it provides high SNR and excellent ambient light rejection under conditions where CTR is greater than 5 nA/mA. However, digital integration mode results in the highest SNR levels and provides optimized SNR per watt efficiency. Therefore, if the ambient light is not an issue for the application and the target dc SNR is above 85 dB, digital integration mode can be selected to achieve high SNR efficiently. If the target dc SNR is below 85 dB, the power savings from digital integration is not significant when compared to continuous connect mode.
To summarize, digital integration mode can be selected if the photodiode requires longer pulses due to slower photodiode response time, or when there is no need for simultaneous sampling of tw o channels within a time slot.
Additionally, when ambient light is not an issue and when the target dc SNR is above 85 dB, selecting digital integration mode will achieve power efficiency.
PPG Applications
In light of the COVID-19 pandemic, PPG applications have become even more important in vital signs monitoring and health diagnostics. Additionally, multiple metrics are critical to detection. For example, some key vital signs measurements include heart rate monitoring (HRM), HRV, and oxygen saturation (SpO2), which can be measured through pulse oximetry and blood pressure.
Optical and noninvasive SpO2 monitoring, which is also known as pulse oximetry, has become very valuable in the detection of hypoxia in patients with COVID-19. Hypoxia, one of the main symptoms of COVID-19, is the deprivation of oxygen supply to the body tissues. Hypoxia may also cause increased heart rate; therefore, optical and noninvasive heart rate monitoring is also critical to detection.
The integration of multiple measurement capabilities is optimal, if not necessary to future wearable devices, making the ADPD4100/ADPD4101 extremely advantageous.
This AFE measures any type of sensor inputs (including temperature, ECG, and respiration measurements). Therefore, a complete multiparameter VSM platform can be established with just a single sensor AFE.
Pulse Oximetry—SpO2 Measurement
Pulse oximetry is done through red (typically 660 nm wavelength) and infrared (IR) LEDs (typically 940 nm wavelength). Deoxygenated hemoglobin absorbs more of the 660 nm wavelength light, and oxygenated hemoglobin absorbs more
of the 940 nm wavelength. The photodiode perceives the non-absorbed light.
The perceived signals are then divided into dc and ac components. The dc component represents the absorption of light due to the tissue, venous blood, and non pulsatile arterial blood. The ac component represents the pulsatile arterial blood. The SpO2 percentage is then calculated by:
%SpO2 = (ACred/DCred)/(ACIR/DCIR)
Any two time slots of the AD PD4100/ADPD4101 can be configured to measure the response to the r ed and IR LEDs to measure SpO2. The remaining time slots can be configured to measure PPG from different wavelength LEDs, and can also support ECG measurement, lead-off detection, respiration measurement, and any other sensor measurements.
Figure 2 shows synchronous red, green, and IR PPG signals, as well as ac and dc parts of the IR signal as an example.
Heart Rate Monitoring
Heart rate monitoring is also critical in the detection of COVID-19. As the oxygen supply drops due to hypoxia, the heart starts to beat faster in order to supply enough oxygen to the tissues. Monitoring heart rate is also valuable in detecting cardiac problems or tracking fitness behavior.
A green LED with wavelength around 540 nm is generally preferred in heart rate monitoring. It yields the best PPG signal as it has a higher modulation index than red or IR LEDs. It also provides a decent CTR level; therefore, power consumption would not be too high.
AC SNR is a parameter of signal quality and can be calculated by dc SNR times modulation index. For example, with 1% modulation index, 95 dB dc SNR translates into 55 dB ac SNR.
ECG Measurement
ECG measurement has been added to wearable devices, such as watches for spot checking and chest patches for continuous monitoring. Electrodes made of metals and other conductive materials, which are polarized and called dry electrodes, are typically found in such devices. The primary challenges for ECG measurement with dry electrodes are high electrode-skin contact impedance and relatively high overpotential.
Conventional instrumentation amplifier-based ECG solutions use buffers to mitigate the high electrode-skin contact impedance associated with signal attenuation. The right-leg drive (RLD) technique, which requires a third electrode and drives a reference voltage back to the body, is implemented to reject the common-mode voltages the human body, electrodes, and cables are exposed to in ECG systems that measure the voltage.
When applied to ECG measurement, the ADPD4100/ADPD4101 takes a novel approach by using a pas sive resistor-capacitor (RC) circuit to follow the differential voltage across a pair of electrodes. The passive RC circuit can be as simple as three components, two resistors RS and a capacitor CS, as shown in Figure 3a. It is a two-step process for each sample of the ECG data.
The two input pins (IN7 and IN8) float during the charging step. The charge on the capacitor CS is proportional to the differential voltage across the two electrodes if the charging time is >3τ where τ is the time constant defined by the RS and CS, τ=2RSCS. During the charge transferring step, the capacitor is connected to the TIA and the charge is transferred to the AFE for measurement. This charge measurement-based ECG solution offers several advantages, including eliminating the buffers and the third electrode for RLD, shrinking the system size through fewer external components, and saving power.
It is convenient to add lead-off detection to this ECG solution with the design flexibility of the ADPD4100/ADPD4101 using a bioimpedance-based approach.
Figure 3a shows the lead-off detection circuit with driving pulses to one electrode and receiving current at another electrode. If one or both electrodes are detached from the skin, the path is broken and no current is received. Figure 4 shows traces of ECG and received electric current for lead-off detection, where ECG is measured in time slot A and lead-off detection in time slot B.
When compared to the pull-up resistor circuit for lead-off detection in conventional ECG solutions, which impact the input impedance of the ECG circuit, this bioimpedance-based lead-off detection in a separated time slot has no impact on the ECG measurement. With this dc-coupled circuit, ECG is captured once the electrode-skin contacts are re-established.
Impedance-Based Respiration Measurement
Respiration measurement using the ADPD4100/ADPD4101 detects the bioimpedance change of the lung during the inhalation and exhalation cycles. Respiration measurement for patient monitoring in the intensive care unit (ICU) and during sleep allows patient management and timely alarms to save lives. It is critical for patients with respiratory problems and sleep apnea. Sleep apnea alone is a public health and safety threat, with more than 25 million adults afflicted in the U.S.1 When the patient breathes, the volume of the lung expands and contracts, leading to changes in the impedance of the chest. The impedance change can be measured by injecting a current to a path across the chest and measuring the voltage drop. Figure 5a shows a reference design that employs two electrodes for ECG measurement and respiration monitoring. Figure 5b shows synchronously recorded ECG, respiration associated impedance wave, and PPG. ECG and respiration were measured using stainless steel dry electrodes on the left and right wrists and PPG using a green LED.
Summary
Vital signs monitoring has extended its presence in the consumer market in the form of smart wearable devices. The health information generated by the wearable devices can play an essential role in health and disease management.
To meet demand and make these devices accessible to a much broader population, designers must consider common r equirements such as cost, size , and power. This groundbreaking AFE from Analog Devices, the ADPD4100/ADPD4101, demonstrates its great advantage as a multiparameter vital signs monitoring hub. A single AFE design reduces the number of ICs for multiparameter VSM systems, and hence significantly lowers the cost and size. In addition, multiparameter systems designed with ADPD4100/ADPD4101 generate synchronous data and eliminate the burden of data synchronization.
References
1 “Rising Prevalence of Sleep Apnea in U.S. Threatens Public Health.” American Academy of Sleep Medicine (AASM). September 2014.
About the Author
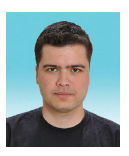
Yigit Yoleri is an applications engineer in the Molecular Sensing Group at Analog Devices in Wilmington, MA. He works closely on healthcare, consumer, and industrial applications of optical sensors. He started working at Analog Devices in February 2019. He holds an M.S. degree in electrical and computer engineering with a specialization in medical devices and systems from University of California San Diego (UCSD), and he has a B.Sc. degree in electrical and electronics engineering from Bogazici University in Turkey. He can be reached at yigit.yoleri@analog.com.
About the Author
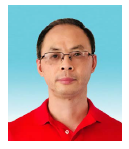
Guixue (Glen) Bu is an applications engineer in the Molecular Sensing Group with R&D focus on biomedical measurement technologies and applications. He joined Analog Devices in September 2018. He received his B.Eng. from Tsinghua University and MS and Ph.D from Purdue University, all in biomedical engineering. He can be reached at guixue.bu@analog.com.