New 3D AOI/SPI Combo, 3D AXI system for PCBAs, and M2M Software
Tokyo, Japan – January 29, 2020 – Saki Corporation, an innovator in the field of automated optical and X-ray inspection and measurement equipment, will demonstrate new automated inspection products, software, and capabilities and announce new personnel, offices, and collaborations at IPC APEX, San Diego, CA. On display will be a new combination 3D automated optical inspection (AOI) with 3D solder paste inspection (SPI) system, an automated X-ray inspection (AXI) system for printed circuit board assemblies (PCBAs), new self-programming software with self-tuning, and advanced M2M capabilities.
Saki’s combination AOI/SPI system fits NPI, high-mix/low-volume, and high-volume applications, enabling all companies to use both SPI and AOI inspection to ensure the quality of their manufacturing process and products, even when using 01005 and 0201 metric components and board sizes up to 27″ x 34″. Multiple sensors of 7μm, 12μm, and 18μm accommodate the inspection needs of almost all manufacturing operations. Common software and a common user interface enable Saki’s SPI, AOI, and AXI results to be viewed together, and programming is easy and intuitive, taking minutes instead of hours and providing automated data analytics and line performance dashboards.
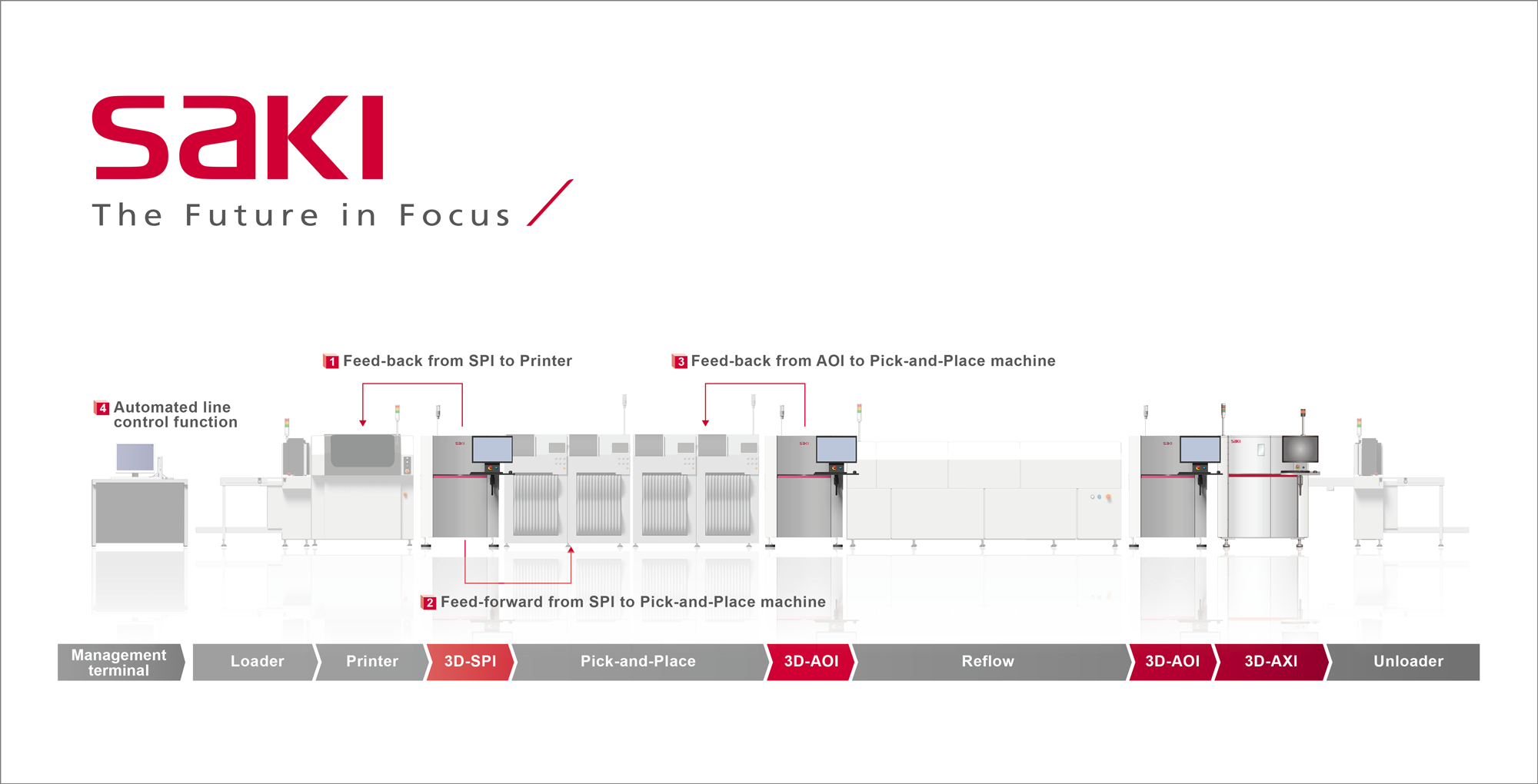
Saki’s new software solutions include its QD Analyzer which it co-developed with Cogiscan. This advanced software for manufacturing production quality and control presents actionable KPI data to accurately identify the cause of defects based on inspection results, while simultaneously monitoring machine performance and collecting traceability data. The software includes a defect-analysis dashboard detailing line performance, including drilling down to the exact pin of a reference designator to discover exactly what’s hindering productivity.
“IPC APEX will be a chance to introduce Saki America’s new personnel and offices,” said Norihiro Koike, president of Saki Corporation. “Saki technical experts from Mexico, Brazil, and Japan, as well as the United States, will be available to assist with your inspection needs. Please visit our booth #2025 at IPC APEX 2020, being held at the San Diego Convention Center in San Diego, CA from February 4-6.”
For more information contact Saki at pr@sakicorp.com, or visit www.sakicorp.com or www.sakiglobal.com.