While many consider the autonomous vehicle to be a relatively recent idea, the concept was first postulated at the New York World’s Fair way back in 1939 and there have been many landmark developments along the way. In fact, it has been possible to build a 90% autonomous car from standard components for several decades, but making it 99% autonomous is 10 times harder, and 99.9% would be 10 times harder again. In other words, to create a totally autonomous vehicle with an acceptable level of safety and security for use on our crowded highways is very, very much harder than that creating a vehicle that has some Advanced Driver Assistance Systems (ADAS) but essentially still has a human in charge. While hardware developments, particularly improvements in semiconductor processing power and sensor technologies, have been central to making ADAS viable, the real ‘secret sauce’ is in system software where advances in Artificial Intelligence (AI) determine how vehicles process and act upon the signals they receive from their own electronic systems, from other vehicles and from the environment that surrounds them.
ADAS – from aircraft to automobiles
We’ve been flying aircrafts autonomously for a long time, which just goes to show how much safer it is in the skies than on our roads, mainly because there’s a lot more space between things. And it’s in the air where much of the technology that underpins today’s vehicle ADAS originated. Consider these examples. Electronic fly-by-wire technology was introduced in a production aircraft in 1958 (the Avro Canada CF-105 Arrow), its stabilisation system depending on gyroscopes, miniature versions of which are used in ADAS systems today. Aircraft head-up displays were derived from a parallax-free optical sight technology called ‘reflector sight’, first developed in 1937. The first head-up displays in cars were found in General Motors’ Oldsmobile Cutlass Supreme in 1988, closely followed by Nissan’s 240SX, introduced in 1989.
Vehicle ADAS development is focused on adaptive and predictive technologies that make driving a better, safer experience. With these systems installed and activated, driving is really a collaborative activity between ADAS and the driver. The systems provide warnings and initiate actions but the driver still has overall responsibility for the vehicle. In future, the systems will advance to the point that they will make faster and better decisions than human beings – which raises some interesting ethical questions about where the responsibility for decision-making lies.
Examples of components used in today’s ADAS
It’s clear that the number of of electronic circuits found in vehicles is now vast, and growing by the day. A key aspect of ADAS involves processing data from cameras, radar and ultrasonic, or other sensors, to alert drivers to potential problems or assist them, perhaps in maintaining lane discipline, avoiding getting to close to the vehicle in front or automating the parking process. These systems typically incorporate power management, a variety of communication interfaces, display drivers and power supplies, and microcontrollers (MCUs) – both general purpose and safety types.
Here are just few examples of components currently used in ADAS that will underpin autonomous vehicle development into the future.
Ultrasonic sensors are used in calculating parking distances and detecting objects. TI makes an AEC Q-100 qualified, signal-conditioning interface for ultrasonic signals, the PGA450-Q1. The device processes echo signals to calculate the distance between an ultrasonic transducer and an object, transmitting the resulting data over a LIN 2.1 network. Used in pairs, as shown in the diagram, the devices can measure distances from under 1 metre up to 7 metres, with 1 cm accuracy, depending on the chosen transducer-transformer pair. Each device integrates voltage regulators, an ADC, 8-bit (8051-based) microcontroller, oscillator and LIN 2.1 physical interface and communication protocol. The MCU and program memory allows the PGA450-Q1 to be configured for the end applications.
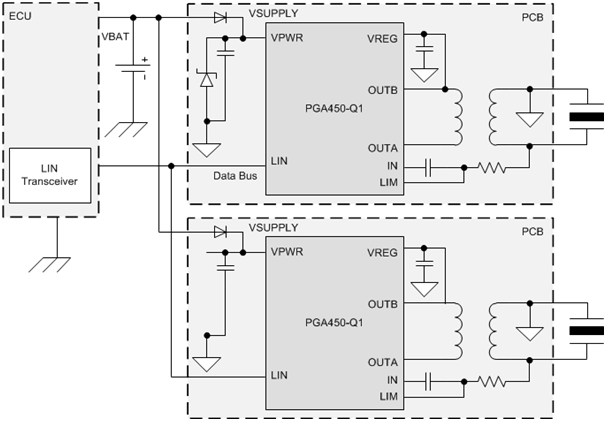
There’s innovation in vehicle lighting too. ON Semiconductor’s NCV78763 Power Ballast and Dual LED Driver. It’s a dual-output, boost-buck DC-DC converter that will drive two strings of LEDs at up to 60 V. Used for automotive front headlight applications including high and low beam, daytime running lights, turn indicators and fog lights, is has on-chip diagnostics for safety monitoring, which frees up system resources by relieving a microcontroller of that responsibility. Furthermore, the device has built in current-mode voltage booster controller that simplifies input filter design and cuts the bill of materials. Several of the AEC-qualified chips can be combined then configured through an SPI interface to provide a flexible platform for a variety of LED lighting set-ups.
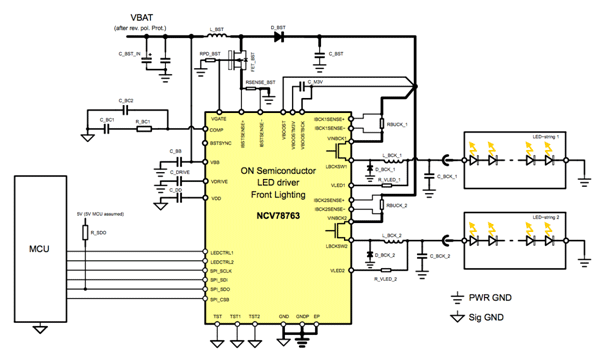
Tyre-pressure monitoring is now an important safety feature found in many vehicles. NXP offers a low power wired or wireless sensor device, the FXTH8715 (originally a Freescale part before the company’s acquisition by NXP), designed specifically for this application. In a 7 x 7 x 2.2mm QFN package, it combines pressure and temperature sensors, dual-axis XZ-axis or Z-axis accelerometer, 125 kHz LF receiver and 315/434 MHz RF transmitter with an 8-bit microcontroller (MCU). The device produces accurate pressure measurements from 100-1500 kPa, so it can even be used in heavy-duty trucks, buses and construction vehicles.
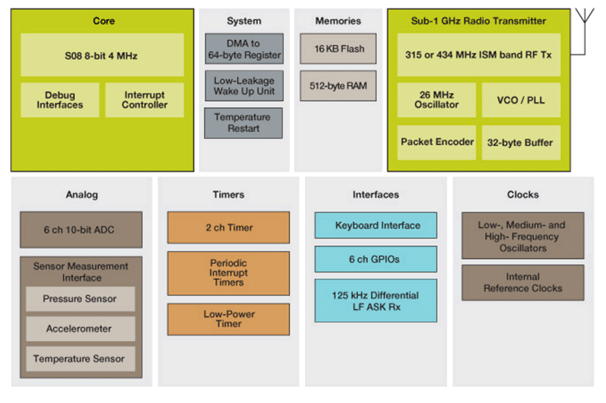
Even passive component makers are developing products with automotive applications in mind. Metal oxide varistors – or voltage dependent resistors – are important devices used to protect against transient and surge voltages that could otherwise damage electronic circuits. Two of AVX’s families of varistors are particularly suitable for automotive applications, both in high-reliability engine control units and the more benign environment of in-cabin electronics. VC and VG series TransGuard multilayer varistors (MLVs) are AEC-Q200 qualified, zinc oxide parts that provide bi-directional protection. They come in voltage ratings from 5.8 to 85 volts DC, with surge energy ratings from 0.05 to 7.3 Joules and peak surge current ratings up to 2000 amps. They respond to voltage transients in less than a nanosecond, providing the vital protection that’s needed in today’s ADAS systems and that will be perhaps even more critical in autonomous vehicles of the future.
Of course, in any electronic system connectors are a potential weak point when it comes to reliability. Delphi Connection Systems has been around for more than 100 years and has become one of the best-known suppliers of connectors for vehicle electric and electronic distribution systems. Going back to the headlamp application discussed earlier, Delphi APEX HIR2 connectors mate with halogen infrared bulbs, which are popular for main beam and dipped beam lighting due to their high-intensity output. But high output means high operating power and significant heat generation, so these connectors are designed for bulb terminal operating temperatures up to 190 °C and the connectors and terminals are tested to 150 °C. Silver plating is used to maximize heat energy conductivity on the terminals and the perimeter seal of the connectors is positively retained to prevent the ingress of moisture or other contaminants.
This article has only touched on a few of the component technologies that will help make the autonomous vehicle a reality. Wireless communication between vehicles (V2V), from vehicles to their surrounding infrastructure (V2I), and into the cloud will also be fundamental enablers of this new breed of vehicles, but that’s a topic for a later article.
Mouser Electronics
Authorised Distributor