In the automotive industry, there is a growing trend toward an increasing number of product launches on a global scale. Original equipment manufacturers (OEMs) are trying to increase their market share in new regions, and they are looking toward regional production to support this goal. That means that often times the same vehicles are being built in multiple production facilities. But that’s just the beginning of the challenges.
In Asia, automakers are under pressure to provide a greater variety of personalized options than ever before. They have to reduce costs to compete in global markets, while accommodating an increasing number of process variations to meet the demands from more consumers. As a result, automotive OEMs face continual pressure to squeeze more time out of schedules that have contracted significantly during the past decade.
To meet these challenges, automakers in Asia need to adopt new manufacturing strategies that will allow them to quickly plan and design new processes; accurately assess the impact of changes; rapidly deploy best practices across global operations and better predict the timing, cost and quality of every program launch. Additionally, they must deliver more environmentally-friendly vehicles and build them with more energy-efficient processes.
To facilitate these strategies, many leading automakers are implementing a collaborative approach that integrates engineering and manufacturing in the development of the launch process. This approach allows for early access to product engineering data so that manufacturing operations work in parallel and processes can be planned, optimized and validated concurrently with design. An integrated approach increases the efficiency of deploying a modular platform that allows for a more predictable launch operation, and provides management with clear visibility into program performance. This predictive launch approach gives automakers greater confidence that their powertrain, body-in-white (BIW), stamping and final assembly processes will meet delivery expectations, first-time quality goals and program profitability targets.
As Asia continues to be the growth engine for the automotive industry with China leaping to number one back in 2009, McKinsey & Company projected that the next 7 years will be profitable for the industry in Asia with emerging markets driving the majority of gains. For these predictions to come true, local automakers need to build a higher impression in both “Brand” and “Quality” to market.
Japan and Korea automakers have long been seen on the same pedestal as industry leaders US and Europe. With globalization, new technology and local market requirements are now their key challenges to keep up with the quality expected of them. Examples like the Takata recall hurting Toyota raised a question mark on quality control that is often perceived to have fallen short while meeting international standards of safety and technological advancement. A framework to predict and eliminate these errors before production and full visibility to teams sitting across different geographical locations to access and edit the design data can help avoid such recalls.
Predictive Launches to Manage Growing Complexity
A successful launch is measured not only by the execution excellence of the entire manufacturing process, but also the cost and time it took to develop and build it. To be competitive, automakers must master the transition from mass production to mass customization, while fulfilling a variety of local regulations and consistently meeting consumer demand. New materials and coating technologies create design changes that can have a significant impact on manufacturability, but can be easily missed without an integrated platform for collaboration.
In 2010, Swedish-based Volvo Car Corporation (Volvo Cars) was acquired by Zhejiang Geely Holdings Group of China with the aim to establish China as the company’s second biggest market, after the US. As a result, Volvo Cars planned for new plants in China and major investments to contribute to the development of new global car models. To achieve that, the company needed to increase its production line flexibility to support multiple car models and change its engineering processes to support operations as a wholly independent organization. Through the adoption of mixed-model production scenarios and the utilization of manufacturing process management to manage and utilize process variants and changes, Volvo was able to enhance collaboration with manufacturing system suppliers, increase engineering productivity, and significantly reduced time needed to generate shop floor documentation.
Automakers need to achieve first-time quality requirements, reduce the time to ramp up and eliminate cost overruns in order to rapidly design, re-use and validate manufacturing processes. Getting all the parameters to the precise required point through trial and error on a virtual platform before implementation has proven critical to the success of automotive OEMs. With the help of integrated manufacturing, companies can optimize the product launch. The predictive launch platform is the catalyst in aiding today’s digitalized world of process management for automakers to compete successfully in the marketplace. Automotive OEMs must operate effectively and efficiently in this manufacturing and production environment while managing the increase in product complexity across the globe.
Enhanced Connectedness for Optimized Launch Frameworks
Integrated manufacturing helps automakers execute global car programs across the world with maximum efficiency and achieve first-time quality goals. To ensure automakers realize more predictive launches on a global basis, they must establish acollaborative development of manufacturing systems. This includes having a managed environment for early access to product engineering data during manufacturing system development, an integrated validation of manufacturing to optimize process productivity and efficiency, a fast and efficient process development and predictable program performance and profitability. Leading carmakers like BMW are already executing practices that employ various cutting edge industrial connectivity tools to achieve better results. They are using predictive analytics for production as well as repair processes.
Predictive modelling and analytics have the potential to turn traditional manufacturing frameworks on their heads. Employing technologies like Big Data to mine crucial and timely data to preempt and adjust the design parameters accordingly to swiftly changing specifications and leveraging the Industrial Internet of Things (IIoT) to make sure that each part of the process can talk to the other parts is set to usher in a new phase of launch practices for a number of verticals. The automotive industry stands to gain the most from predictive analytics and companies engaging these easily customizable robust solutions for their launch programs will steer ahead of the competition by achieving unprecedented control and speed for design and production processes while staying highly energy-efficient.
About Author
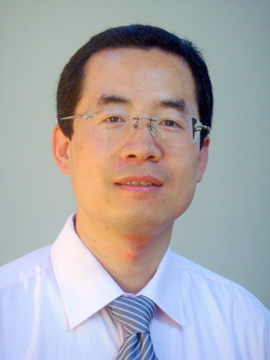