The team of technology leader ASM Assembly Systems can look back on an extraordinarily successful Productronica 2015. In the impressive booth, which was largest yet covering 650 square meters, visitors had to fight for space to view “live” the progress the company has made on the path to the Smart #1 SMT Factory. Equally popular were the workshops and product presentations ASM Assembly System’s offered during the technology inhouse show at its Munich headquarters. Highlights at both locations included the SIPLACE BulkFeeder for tape-free component feeding, the new DEK NeoHorizon printers in interaction with the ASM ProcessExpert as the first self-learning inline expert system for SMT production, and integrated SIPLACE solutions for material logistics. The new ultra-compact SIPLACE TX high-volume placement modules received Global SMT & Packaging’s innovation award in the “High-Volume Placement” category.
Also popular was a study which ASM developers presented in cooperation with robotics manufacturer KUKA. It demonstrated how intelligent, self-propelled robots can help line operators refill components or pick up component reels from the automatic SIPLACE Material Tower storage system.
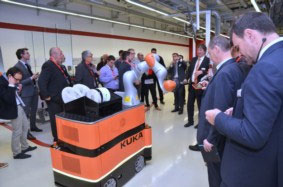
“The Productronica has always been a successful forum for us, but this year it broke all kinds of records for us. Our sales team received many project inquiries, with most of them being very concrete and specific. Our visitors repeatedly confirmed to us that our activities in the Smart #1 SMT Factory segment provide the right answers to the challenges facing electronics manufacturers today and tomorrow,” said Gabriela Reckewerth, ASM’s Director of Global Marketing. She added: “Particularly popular was the fact that we showed tangible solutions for all four innovation drivers in the Smart #1 SMT Factory: highly flexible printing and placement platforms, the SIPLACE BulkFeeder for automation, the self-learning ASM ProcessExpert system as a technological milestone in process integration, and our integrated material logistics solutions on the basis of the SIPLACE Material Manager. The tailwind generated by this year’s Productronica will help us to further solidify our position as the leading equipment supplier and partner of the electronics manufacturing industry.”
Innovation award for SIPLACE TX placement modules
In addition to attracting lots of interest among visitors, the new SIPLACE TX high-volume placement modules were honored with Global SMT & Packaging’s Innovation Award in the ‘High-Volume Placement’ category. Judges and spectators alike were impressed by the extremely compact modules, which set new industry records in speed, accuracy and floorspace performance (they are only 1 meter wide and take up only 2.3 square meters).
New product category: The self-learning ASM ProcessExpert
The ASM ProcessExpert is the world’s first self-learning inline expert system for electronics production. The interaction between the integrated and extremely precise 5D SPI system in the ASM ProcessLens, the ASM ProcessEngine real-time software and their knowledge databases enables SMT lines for the first time to control themselves completely automatically. In live demonstrations, ASM Assembly Systems showed how the ASM ProcessExpert can perform a valid DFM HealthCheck based on virtual prints and Gerber data – long before the first board enters the line. During the production run, the system controls the networked DEK printers and monitors the paste printing quality.
No tapes, no splicing
With the SIPLACE BulkFeeder, ASM demonstrated a tool for the tapeless feeding of 01005, 0201 and 0401 components. Using vibration, the system makes the components available on a pickup glass. The integrated camera identifies them, and the ultra-fast SIPLACE heads pick them up at full speed. Each cartridge for this innovative feeder holds up to 1.5 million components. The SIPLACE BulkFeeder relieves lines operators from the time-wasting and error-prone splicing process and the many steps involved in handling and disposing of tapes and tape fragments. At the same time, it increases the placement accuracy in high-density applications like the smartphone production, because – unlike traditional tape-based pickup processes – the camera-supported pickup process ensures perfect component centering.
Robotics study in cooperation with KUKA
Experts believe that collaboration between robots and human operators (“collaborative robotics”) is one of the largest efficiency boosters in the Smart #1 SMT Factory – and one of the toughest challenges for developers. Accordingly, a robotics study developed jointly by ASM and KUKA generated lots of interest during the show. Visitors could observe a self-propelled robot that supports humans during setup and resupply operations. The KUKA robot received its commands for providing component reels to the line when and where needed from the SIPLACE Material Manager software.