Requirements, challenges and SIPLACE product advantages to customers
The world of technology continues to advance, and there’s no stopping it. As electronics are used in an ever wider range of applications, more and more functions have to be combined in increasingly smaller modules. To manage this challenge, it is no longer sufficient to make the components themselves smaller and smaller. The dependencies and interactions between materials and production processes must be analyzed and taken into account already in the product planning phase.
The outlook is clear: The trend towards ever smaller passive components will continue, and because of their small dimensions and the resulting limitations with regard to their manufacture and their electrical values, 01005 components are predominantly found everywhere, where you need a maximum of functionalities on a minimum amount of space (smartphones, hearing aids, submodules etc.)
Challenges
One of the huge challenges would be the extreme demand of the production process. There are many factors to be considered starting from the 01005 dimensions and packaging to the PCB Topography and process characteristics. From the solder paste properties and printing to the delicate placement process. Even the reflow process and the production environment needs to be carefully executed
The smaller the components are, the more accurate the placement process must be, and the more precisely the vision system must recognize the components and align them with each other. One basic pre-requisite: The placement systems must operate reliably and within the specified tolerances especially in the area of 01005 mounting.
SIPLACE Product Advantages
If 01005 components are involved, the following parts of the placement process must be executed more accurately than with standard components:
- The feeder positioning and repeat accuracy
- The nozzle concentricity tolerance
- The control that the nozzle picks up and deposits the component reliably
- The vision recognition for component centering
To fufill the above requirements, the following placement process and technologies are used in the SIPLACE Placement system
Touchless pickup
It is important to pick up a component from a tape pocket with a vacuum nozzle without physically touching the components. Touchless pickup also has the advantage that the component cannot get damaged or jammed in the tape pocket.
Feeder modules
The feeder modules for these smallest of components should have an adjustable or appropriately preset travel profile to make sure that the tape accelerates and decelerates smoothly. Also, the feeder module must
still supply the components at the pickup position at a rate of speed that does not slow down the placement process. Here the SIPLACE X-feeders are well equipped with these features.
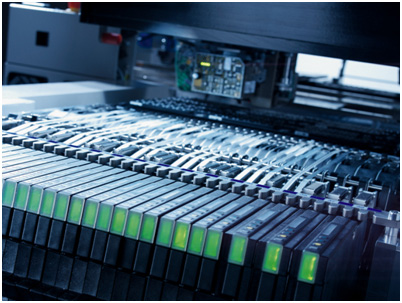
Nozzles
As far as the nozzles for 01005 components are concerned, the smaller the nozzle’s concentricity tolerance, the better the pickup. If possible, the nozzles for 01005 components should not exceed the component’s dimensions. This also avoids the problem of “placement shadows” when equally high components or mixes of resistors, capacitors and inductivities are being placed.
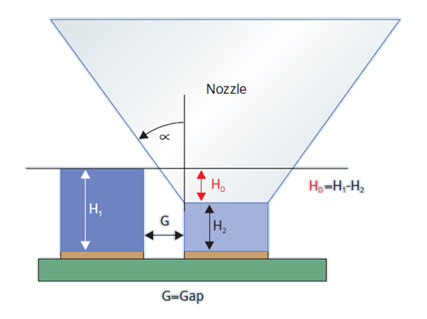
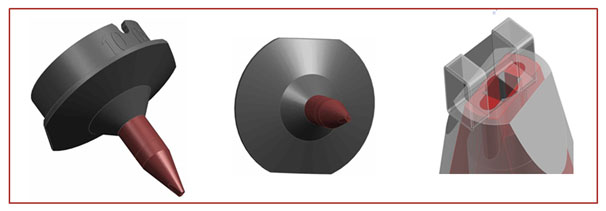
Placement force
For extremely small components, the placement force must be adjustable to lower values than as compared to other regular components. Here the SIPLACE SpeedStar head is capable of setting the Programmable set-down force in a range of 1.5N to 4.5N.
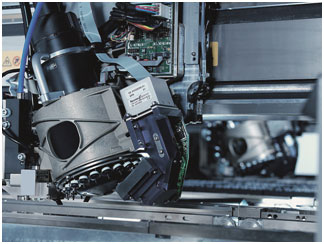
Vision system
When describing the vision data for 01005 components, you must be able to set the parameters in such a way that the components can be reliably recognized. In addition to having flexible lighting, the camera’s resolution must be sufficiently high, and the system’s algorithms must be able to recognize bill boarding and face-down components. The SIPLACE digital vision system is capable of meeting these requirements. Especially for 01005 components, a vision system with robust algorithms and good fiducial recognition is necessary.
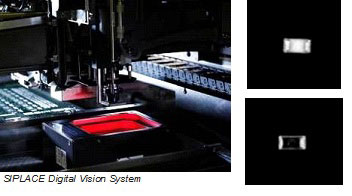
Summary
As product miniaturization advances, it is becoming more and more important to pay attention not to individual process steps but to the system as a whole and to make it as efficient as possible.
The relationships and interactions between materials and manufacturing processes must be taken into account already in the product planning phase. If
these requirements are implemented consistently, the result will be a product that is “designed for manufacturability” and provides high quality and a high yield within the user’s process window.
Author Profile
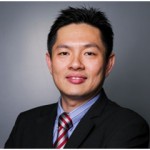
Simon Tan,
Product Marketing Manager,
ASM Assembly Systems Singapore
Simon is a Product Marketing Manager at ASM Assembly System, Singapore. His primary role is to lead the Product Marketing and Sales support for the SIPLACE Placement systems. He has about 15 years of experience in Surface Mount Technology covering pick & place machines as well as automatic optical inspection systems. He earned his BSc (Hons.) degree in University of London.