Digital power is one of the most important technologies for reducing power consumption and managing the growing power complexity in modern electronic systems.
It’s imperative that designers better understand the complex nature of digital power. Over the past several decades, one by one, analog electronic gadgets such as cassette tapes/players, VHS tapes/players, film cameras, CRT televisions/monitors, etc., have been dumped by the truckload in electronic recycling graveyards. Though not yet in the same category as a dinosaur, they’re all surely to wind up under the same roof—namely, a museum.
So far, analog power supplies have miraculously, and unexpectedly, been able to escape the misery. However, the inevitable will come, as attested to by the appearance of drones and driverless vehicles—all products of digital technologies.
In light of this trend, what should professionals well-trained in conventional analog circuits do to avoid being placed in the analog museum?
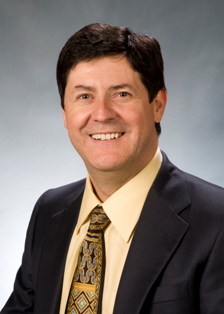
Tumble to Digital
Early on, what had happened to those antiquated apparatus certainly caught the attention of many corporate CEOs and business planners. Quite a few, including TI, Motorola, and, in particular, those who have stakes in power conversion, actually took steps to initiate the transition to digital techniques. Several companies thought, banking on their success on digital motor-control products, it should be easy to rein in the analog power converters with their existing devices and capabilities. However, the expectation failed to materialize.
It turns out that the know-how derived from motor control focuses on different areas that contrast from digital power conversion. In essence, the techniques (e.g., d-q decomposition, space-vector-modulation, etc.) developed via digital motor control can be viewed as versions of a more sophisticated sequential pulse-width modulation (PWM) intended to generate perfect motor (shaft) rotation. Digital power conversion, on the other hand, sets its priority on feedback error processing via digital means instead of analog amplifiers. Generation of PWM is less of a concern.
The power needs of many of today’s electronic systems can no longer be satisfied by even leading-edge analog supplies, but instead require a new form of power-supply architecture for control. The fully digital power-supply implementation has significant and tangible benefits with its flexibility, performance and adaptability. While it is radically different in concept and execution from the traditional analog-based supply, the digital design is mature and is rapidly expanding to other applications.
“I’m sure a book could be written on the trend of Digital Power Supplies and Digital Modules because of it being such a broad topic, but it is very evident that this technology is having a major impact on the Power industry by reducing the footprint, lowering part count, increasing thermal performance and reliability, along with higher efficiencies that has resulted with more convection-cooled product releases. End product time to market has been able to be shortened with the Design Engineer having more tools available at their disposal to tailor design solutions on the fly and tweak these changes without multiple board spins, as was the case in the past”, said Jim Reynolds, Senior Product Manager at Digi-Key Electronics.
He adds, “I believe it would be easier to say what markets won’t benefit! I see Digital Power fitting into all power markets – from Telecom that need special sequencing functionality and intelligent power control, through PMBus, to Industrial applications that need the communication interface with Intelligent Control Panels. I see the limiting factor being the cost of digital power; but as the price drops, it will be phased into most power markets over time”.
Lokesh Duraiappah, Director, Industrial Power Products, Renesas Electronics Corporation says, “Digital power management offers several unique advantages over traditional analog power. The inclusion of a PMBus interface on digital power products enables end users to have detailed knowledge about the health and status of their power supply. It also allows for easy changing of key regulator parameters, such as switching frequency, control loop settings, output voltage setpoint and margin levels, and fault response behavior. Historically, digital power has been seen as either hard to use or lower performing when compared to analog power. Today’s digital power products address these concerns, often exceeding the performance of analog-based solutions while offering all the flexibility that PMBus brings — programmability, control and real-time monitoring”.
He adds, “The proliferation of cloud computing applications is dominating digital power penetration into the data center server and telecom markets, as well as the industrial and consumer markets. While system manufacturers have functional experts, they typically do not have in-house power design expertise. With applications adding more intelligence while complying with green energy standards, IC suppliers have to deliver solutions that meet equipment makers’ power needs, are straightforward to use, and accelerate design time.
Digital power modules provide an alternative to the lengthy and arduous process of discrete power supply design by integrating all of the key components inside an encapsulated package. A digital power module includes the high-side and low-side MOSFETs, inductor, controller, and the compensation network. The engineer typically only needs to select the input and output capacitors, along with a few resistors to complete the power supply design.
Digital processing in data center servers, telecom and networking equipment is accomplished with advanced processors and FPGAs that require higher output currents ranging anywhere from 100A to 400A or more, depending on their complexity. These are the applications where digital multiphase controllers and smart power stages excel. They are able to maintain the power delivered from light-load to peak-load at close to peak efficiency. They achieve their high efficiency by parallelizing multiple power delivery phases, which the controller modulates based on the power draw requirement.
A typical multiphase system has the regulator modulating each inductor to provide a variable amount of current. Multiphase operation improves on a key shortcoming of single-phase converters, where the efficiency peaks at a nominal load, but drops at very high loads. Instead, multiphase systems can intelligently select the number of phases depending on the load. Flattening the efficiency curve across a much larger portion of the operating range frees data center planners from choosing between optimizing for typical and maximum workloads”.
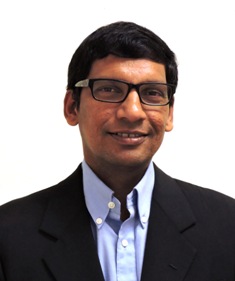
Analog works fine: Why go digital?
Analog techniques have long dominated the design of switching DC/DC converters (voltage regulators) because they were relatively simple and inexpensive to implement. However, analog design has its downsides, notably the tricky business of control-loop compensation.
Digital design offers an alternative, particularly as the components required to support a digital power supply have dropped in price, dimensions and power consumption. Digital components allow designers to finely tune the control of their circuit such that transient response is enhanced and efficiency maximized.
In practice things can be a little more complex, particularly as one silicon vendor can have a different definition of “digital power” from another. Some suppliers define the technique as a power supply solution with a digital interface that takes advantage of the functionality offered by the Power Management Bus (PMBus) protocol coupled with an analog control loop in a “digital wrapper” solution. Other firms insist that digital power is a fully digital control loop powered by a microprocessor or digital signal processor (DSP).
Each technique brings its challenges: the digital wrapper still leaves you with the control-loop compensation challenge you were perhaps trying to eliminate in the first place, while a full digital solution carries the inherent implication that a designer might need to do a significant amount of coding to get the digital power system up and running. However, a new generation of digital power controllers and modules promises to address the challenges of both digital wrappers and full digital solutions.
Tony Armstrong, Marketing Director – Power Products, Analog Devices Inc, “Our micromodule regulators resembles a surface mount IC; however, they include all the necessary support components that would normally be used to construct a power conversion circuit. This includes a DC/DC controller, MOSFET dice, magnetics, capacitors and resistors and so on, all mounted on a thermally efficient laminate substrate. They are then encapsulated using a plastic mold cap. The result was a complete power supply that can be simply adhered to a printed circuit board.
Built to the industry’s highest quality standards, this product family dramatically reduces risk, time and effort to successfully design high performance, high power density solutions. It is as if we have taken all our power supply expertise & know-how and put it into an IC like form factor. Many of our micromodule regulators, as well as our ICs also incorporate a PMBus I2C interface, also known as Power System Management. We refer to it as PSM for short.
Consider our 100A micromodule regulator, the LTM4700, that is expected to be in mass production in the July 2018 timeframe, as an example of a PSM device. Not only can it deliver 100A of continuous output current but its built-in Power System Management for enhanced functionality.
The major driving forces for the continued adoption of PSM devices is the flexibility they offer within the end system. In general, these include the following:
- Configure voltages, define complex on/off sequencing arrangements, define fault conditions such as OV and UV limits and set important power supply parameters such as switching frequency, current limit, etc. over a digital communication bus.
- Over the same communication bus, you can Readback important operating parameters such as input voltage and output voltage, input and output current, input and output power, internal and external temperature and in some of our products measure energy consumed.
- Customers can implement very precise closed-loop margin testing of their designs as well as trim power supply voltages to very precise levels.
- We have designed these devices to be autonomous. Once they are configured and input power is applied, they sequence up the power supplies, regulate very accurate voltages at the point of load, continuously supervise voltage and current while implementing the user configurable fault management scheme and arm a non-volatile fault recorder that stores information about the power system at the time of a detected fault.
- Our PSM devices can be cascaded to build large power supply systems that are coherent. We achieve this with an inter-chip coordination bus that operates at wireline speeds. We include internal NVM for device configuration and fault log.
- Most importantly our PSM devices are all supported by a common GUI called LTpowerPlay. LTpowerplay is an engineering level GUI that was developed with power system design and debug in mind as well as remote customer support.
In summary, the LTM4700’s key specifications are:
- It is a single 100A output capable micromodule. Or, it can be used as two 50A outputs.
- It is very close to 90% conversion efficiency when stepping down from 12V to 1V at 100A with only 200 LTM air flow. And has +/- 0.5% maximum DC error over temperature.
- It incorporates Digital Power System Management capabilities.
- Its x, y, z footprint is only 15mm x 22mm x 7.82mm
- Expected release is July 2018, with samples in June.
In addition to having a dual 50A, or single 100A output, the LTM4700 also incorporates a PMBus I2C interface or Power System Management.
This enables many different capabilities:
- A) Configure voltages, define complex on/off sequencing arrangements, define fault conditions such as OV and UV limits and set important power supply parameters such as switching frequency, current limit, etc. over a digital communication bus.
- B) Over the same communication bus, you can Readback important operating parameters such as input voltage and output voltage, input and output current, input and output power, internal and external temperature and in some of our products measure energy consumed.
- C) Users can implement very precise closed-loop margin testing of their designs as well as trim power supply voltages to very precise levels
- D) A system benefit of using our PSM devices is higher reliability and quality
- E) Our built-in servo loops will maintain higher power supply accuracy over the life of the product improving reliability
- F) The readback features of our PSM devices can be used to improve test coverage at In-Circuit-Test and screen out possible defective devices before they get into the field.
- G) During the life of the customers product our PSM devices continue to monitor important parameters. Trends in voltage, current and temperature can be used to profile the power system. Once a good system signature can be found, a bad system or one that is about to fail can be identified.
Furthermore, most of our step-down micromodule devices automatically current share since they are current mode control-based. Therefore, to generate a 250 Amp output from a 12V input to a 1V output for example, one can simply use 5 of our 50A step-down micromodules configured in parallel – as show on the left-hand side of this slide. Also, on the right of this slide is an example of a 386A output configuration for power a well know VLSI FPGA. In this case, the solution would consist of 7 x the LTM4650 and a single LTM4677 (36A).
The advantages of this solution are clear:
- Precise sharing of total output current among each micromodule.
- Uniform distribution of heat
- Hight reliability operation since there is no thermal stress on a single device.
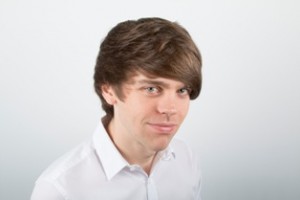
Dr. Michael Hallworth, XP Power
The Benefits of Utilizing Digital Power Modules
Digital power is an important technology to reduce power consumption and manage increasing complexity of upcoming electronic systems. Digital power modules have the best features of power modules and digital power. Already we are seeing a trend towards high efficiency power conversion modules because of their high reliability, high integration and flexibility.
Digital power management is used in data servers, smart hand held devices and wireless base stations. They give real time intelligence and enable developers to design power systems that optimize efficiency and adapt to their environment.
Embedded engineers working on digital power modules have a lot to gain in terms of experience and performance. Moreover, digital power modules can make the design of a high power custom power supply simpler. Intelligent digital power systems can automatically compensate for changes in system temperature and load.
The good news is, there are many new digital control schemes that can help you achieve enhanced transient performance with reduced output caps. Features like adaptive dead time control, dynamic voltage scaling and robust protection under fault conditions enable high energy savings and optimum system performance.
With just a few output and input caps, you can build a complete custom power supply. Basically, power module integrated circuits can make the job of designing power supplies easy and simple.
Dr. Michael Hallworth, XP Power, Senior Design Engineer, “Digital power has experienced rapid growth over the last five years taking advantage of the many benefits that digital control can bring to a traditionally analog domain. The increasing adoption of digital control has been supported by the many new products from microcontroller vendors which specifically target the digital power market”.
Renesas’ digital power modules offer best-in-class power density and thermal performance
Renesas offers a wide range of single- and dual-channel DC-DC step-down digital power modules for telecom/datacom, industrial, and consumer applications. These modules are capable of providing from 6A to 80A of continuous output current, and up to 320A in a multi-module current sharing configuration. They are configurable to support output voltages as low as 0.6V, and they are optimized to operate from industry standard 3.3V, 5V and 12V input power rails.
Renesas’ digital power modules offer best-in-class power density and thermal performance. The ISL8272M 50A and ISL8273M 80A digital power module occupy a mere 18 mm by 23 mm footprint and are the highest power density encapsulated solutions in the market today. Their performance is made possible by using a unique architecture where all power-dissipating components such as FETs and inductor are directly mounted on a copper lead-frame as opposed to a traditional PCB approach. Using a full copper lead frame, that is very similar to a traditional integrated circuit, allows for direct heat transfer to the mounting PCB; hence, the thermal management is more efficient and allows these devices to run cooler and more efficiently. Renesas’ power modules operate at the full rated output current over a wider temperature range without requiring any heat sink or cooling airflow.
Renesas also provides a family of digital multiphase controllers and a companion smart-power stage. The ISL68137, the first digital solution with PMBus and an adaptive voltage scaling bus (AVSBus), provides up to seven phases assignable in any combination across two outputs and combines with smart-power stages to provide a scalable power solution that delivers up to a 450A load to any processor, ASIC or FPGA. The result is enhanced power optimization and more energy-efficient equipment to make the cloud infrastructure and Internet of Things (IoT) greener.
The Renesas digital multiphase solution is tunable on the fly, changing quickly as the need arises. Designers can develop a complete power solution with the PowerNavigator tool in 30 minutes compared to spending days managing RC tables with other solutions. PowerNavigator connects to development boards communicating across PMBus and AVSBus, allowing engineers to set up and control all parameters, optimize efficiency via precise current thresholds for adding or dropping phases, and adjust the loop tuning. The final configuration is simply stored to non-volatile memory.